在选矿生产中磨机的屯耗约占2/3,目前普遍存在磨矿效率低,其90%的能量为损耗。因此,控制磨机负荷使之在最佳工作状态下运转是提高磨机磨矿效率、提高产量降低电耗的重要途径。在我国大多数选矿厂,磨机的运行监测目前仍处于人为判断、手工操作的原始状态,对磨机负荷的监测普遍比较粗糙简单。在手动操作状态下,由于人为经验的限制,磨机往往不能运行在稳定、高效的状态,出力较低,而且人为调节的不确定性也使得出磨物料的粒度不均匀,影响了选矿厂中矿石的质量。
2、磨机负荷测量原理
磨机在运行时,研磨介质与衬板、研磨介质与研磨介质之问、研磨介质与物料、物料与衬板以及物料与物料之间都会因相互之问的碰撞和研磨面发声,且止常运转时这种噪声可高达120dB。在磨机运行时发出的噪声中,钢球之间的相互碰撞,以及钢球和衬板碰撞产生的噪声是磨机噪卢主要部分。
磨机长期的运行实践表明,磨机的负荷与嗓音信号之间存在着一定的对应关系。当磨机负荷较小时,噪音土要来自研磨介质之间以及研磨介质与衬板之间的摩擦和碰撞,噪音较大并且频率较高;当磨机负会逐渐增大时,随着磨内空间和研磨介质之问的空隙逐渐被物料所充填,磨机噪音主要来自物料和研磨介质以及物料和衬板之问摩擦和碰撞,磨音较小日,频率较低。因而通过对磨机噪音的检测,可以间接确定其负荷。
采用磨音法测监测磨机的负荷,其结构是一个集磨音检测和处理变送于一体的电耳。将变送器和电耳封装在一起,既可以减小测量仪的体积,减少一级信号传输,也便于在现场进行安装调试。考虑到生产现场环境恶劣,灰尘较大,磨音传感器由噪音检测元件和防尘壳体组成。
电耳可以准确地检测强度为120分贝以下,频率范围为20k~16k的声音信号。由电耳测得的磨音信号只是粗略地反映了磨机的负荷状态。要更精确地确定负荷的大小,还需要经过变送器对信号进行放大、带通滤波、信号处理和噪音特征潜识别,最终在显示器上显示出来。
电耳硬件外观设计如图1所示。
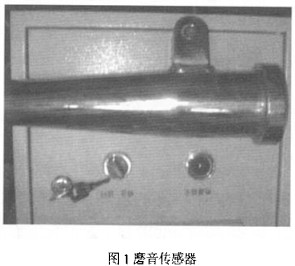
3、磨机控制系统中的硬件设计
负荷检测及监测系统由电耳、涡轮流量计、压力传感器等组成。在本套系统中由电耳来完成对磨音的检测,通过涡轮流量计来完成对水流量的监测,通过压力传感器来完成对浓度的监测,如图2所示。
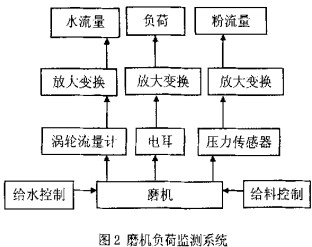
由电耳实时监测磨机的负荷,将声音信号送入16位单片机MSP,130F149,经过A/D转换与期望值相比较,通过控制算法(PID)调节后再经过D/A转换,最后将信号送入变频器调节给矿皮带机转速,实现给矿量的自动控制。给水量的实时监测由涡轮流量计测量,信号也送入l6位单片机MSP430F149,经过A/D转换与期望值相比较,通过控制算法(PID)调节后冉经过D/A转换,最后将信号送入变频器调节电机,实现给水量的自动控制。还必须考虑矿浆的浓度,综合上面的三个因素,我们才能使磨机出力最大并且功率较小,工作在最佳工作状态。单片机监测控制系统框图如图3所示。
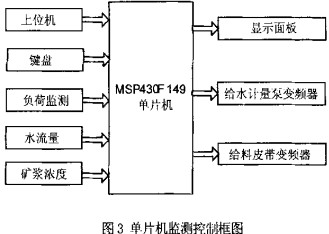
4、磨机控制系统中的软件构成
软件的控制策略采用模仿人j二智能控制方案。它依据智能控制的原理,模仿人的思维对磨机实现智能控制。以保证磨机安全、可靠运行,其软件的构成是由智能逻辑判断和智能控制算法组成。
智能逻辑判断的依据就是设计操作人员积累的经验。根据输入值与测量值之差和其变化率实现相应的控制策略。其控制原则就是:根据磨机的噪音信号也就是电耳信号和输入的期望信号,调整给料电机变频器,使料位达到稳定范圈;但是稳定匀速的给料控制,必须有与之相适应,符合磨机工作要求的水量才能达到比较理想的摔制效果。根据满轮流量汁的测量值与输入的期望值,调节给水电机的变频器,控制阿个回路达到平衡状态。智能控制算法是依据磨机的耦合情况,将控制器分为两个控制回路,每个回路采用模糊PID控制,取得了仿人控制的目的。磨机的给料控制不是一个孤立的系统,它要和给水量相对应,组成-个大的控制系统。
TI公司的单片机MSP430用C语言编程,充分利
用c语言编程结构化、程序简洁和运行速度快的优点。软件设计采用模块化设计,人机界面友好。各模块组成如下图4所示。
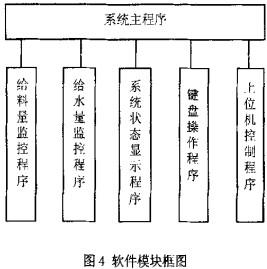
系统主程序主要是完成一些基本的设置工作,对系统进行初始化,如定时器、看门狗、中断设置。监测和判断系统运行的情况;上位机控制程序完成人工监测和控制;键盘操作程序主要是完成一些参数的设定与修改;系统状态显示实时的反应系统的状态;给水量监控程序完成给水量的监测与控制;给料量监测程序完成给料量的监测与控制;中断控制处理突发事件和定时器产生的中断,根据预定的算法进行相应的处理。
5、结语
本嵌入系系统采用新型的低功耗16位单片机MSP430F149作为整个系统的控制器。本芯片外围模块丰富,对丁-采集数据、转换处理、存储、显示等操作十分的方使。使得整个系统的硬件电路实现十分容易。本系统已经在唐山选矿厂投入使用,检测准确,运行可靠,能根据生产的需要自动进行调节。
三门峡富通新能源销售颗粒机、球磨机、雷蒙磨、木屑颗粒机等机械设备。