目前国际上球磨机的发展趋势是向大型化发展,其筒体两端的端盖尺寸也越来越大。端盖材质一般采用铸造低合金钢,其凝固特性决定了铸件易形成显微疏松,磁粉探伤后出现超标磁痕显示,特别是精加工后不易进行返修焊补和回火处理。传统铸件工艺的设计方法根据经验确定铸造工艺,试浇铸,检验试样是否存在浇铸缺陷,如有则修改工艺方案,然后重复上述过程,直至获得合格铸件。由于这种方法必须在浇铸件后才能对铸件工艺是否合理进行评价,因而其设计周期长,生产成本高,效率低,而且最终得到的往往不是最终工艺方案,尤其对于大型或复杂形状的铸件更是如此,球磨机端盖由于自身结构特点,铸件壁厚变化较大,在轴径和R出上述问题不易控制,成为制约生产和保证外商交货期的最主要问题。
本文模拟美国SVEDALA公司的球磨机端盖,铸件最大直径∮9000m,高897mm,铸件毛重69.2t,端盖净重40.4t。如果通过计算机对铸造过程进行仿真模拟,将以上过程在计算机中可以不经实际浇铸即可确定铸件中可能出现的缺陷位置,评价铸造工模拟的合理性。结合计算机辅助工艺设备,提高设计质量,缩短试制周期,降低生产成本,是先进制造技术改造传统工业的应用实例之一,富通新能源销售球磨机、雷蒙磨粉机等磨机机械设备。
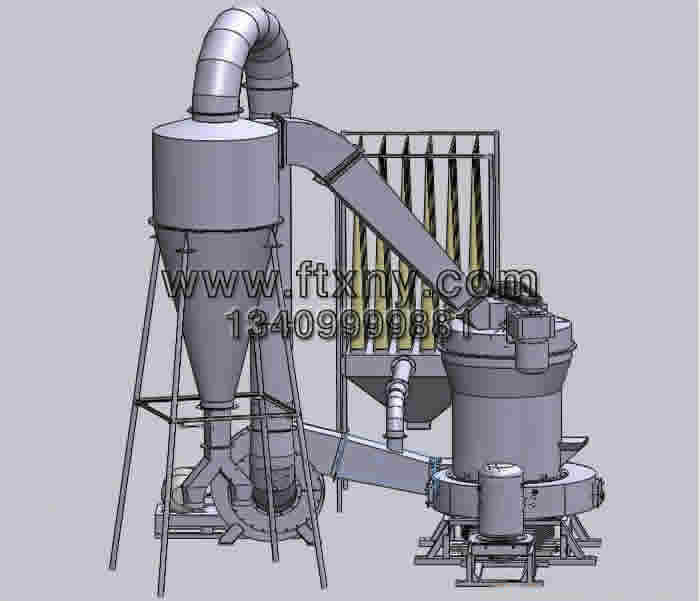
2.1模拟对象
模拟对象是中信重机公司生产的大型球磨机铸钢端盖。铸件根据METSO标准A06-000015铸造,材质为ASTM A216WCA,碳含量不高于0.25,硅含量不高于0.60,锰含量不高于0.70,磷硫含量分别不高于0.040和0.045。铸件最大直径∮9000,高897mm,毛重69. 2t k g,铸件净重40. 4t。由于铸件尺寸过大,设计为1/4方式生产,然后再用螺栓拼接成型。每次浇注两个1/4部分(即半个),目的是防止铸件变形。铸型材料为水玻璃石英砂,浇注温度1540~1560℃。技术要求:(1)铸件根据METSO标准A06-000015铸造,材料为ASTM A216 WCA,含碳量不高于0.25,(2)关键区域1,全部圆周部分100%超声波探伤,要求达到II级标准;关键区域2,全部圆周部分100%超声波探伤,要求达到III级标准。(3)经METSO书面授权,消除应力后不得进行挖割或补焊。
2.2实体造型及铸造工艺
(1)在铸件的内锥面外圈放置∮375mm冒口12个高560mm,其冒口套的尺寸为0515mm;两端放置∮450mm冒口各一个高560mm,冒口套的尺寸为∮580mm;中间放置450mm×650mm冒口高560mm,冒口套的尺寸为580mm×780mm。
(2)铸件的内锥面中圈放置325mm×500mm冒口7个高480mm,冒口套的尺寸为435mm×610mm;两端放置∮330mm冒口各一个高480mm,冒口套的尺寸为∮430mm。
(3)在铸件的内锥面内圈放置∮300mm冒口8个高460mm,冒口套的尺寸为∮420mm;中间放置300mm×450mm冒口高460mm,冒口套的尺寸为435mm×585mm。
(4)锥面下,在冒口间放冷铁两圈宽300mm厚150mm。目的是防止该处由于冒口难以补缩而产生缩孔、缩松缺陷,并划分冒口的补缩区域,提高冒口的补缩效率。
(5)铸件的底座处用厚150mm冷铁一周砌满。目的是加速此部位的凝固,以避免产生热裂纹。
(6)铁于铸件间用20mm的刮沙层隔离。
(7)其加工余量为外圆30mm,内圆30mm,内、外侧为35mm,上(含内锥面)35mm,下30mm,缩尺2.0%。铸造工艺如图2-1所示。
模拟计算之前,必须先生成铸件的三维实体模型。可以使用任意成STL格式文件的应用造型软件来完成这一工作。考虑到应用软件的普及程度和易操作性,选用Solidworks进行造型。完成后的三维铸件模型如图2-2。
3、球磨机端盖铸造工艺计算机模拟
3.1凝固模拟
由Solidworks进行造型后,用华铸软件进行凝固模拟。华铸软件有三个相对独立的模块组成,即前置处理部分、计算处理部分、后置处理部分。
(1)前置处理:STL选择一优先级别设定(铸件、特殊材料、冷铁、冒口套、铸型、绝热材料)一参数输入(网格大小:25mm,缩尺比例:1.02)一剖分结果一显示参数
(2)计算处理:
开始计算前,必须先确定铸件和铸型的物理性质。模拟计算时必须确定铸件和铸型的初始温度。实际浇注完成后的瞬间,铸件和铸型的温度应该是不均匀的。因而假设铸件和铸型的初始温度分布是均匀的计算。计算涉及的物理性质参数如表3-1。
计算初始温度为:铸件温度1540℃, 环境温度20℃。
模拟计算根据编制程序进行计算,计算过程中,每隔一定时间(本例取60s)对铸件各单元的温度
分布进行存储。计算循环直至每一单元温度均降低至固相温度止。结晶过程中产生的凝固潜热用温度
补偿法和等价比热法处理。过程为:计算选择一文件转换一物性参数设置一界面导热系数一设置温场
基础参数一温度场初始化一自动存盘一显示控制。
(3)后置处理
对计算过程中储存的温度场分布和缺陷位置,应用图像处理技术生成虚拟的铸件图,进行BMP处理,BMP集成AVI动画等。从而直观地观察到铸件的凝固过程(图3-la,b)与凝固结束后内部的缺陷分布状况(图3-lc,d)。由图中可看出,铸件中除冒口中存在补缩形成的缩孔外,只在冒口中间处有少量缩孔存在。说明此铸造工艺基本上是合理的。模拟结果与工厂实际浇铸的结果吻合。
图中的红色部分为液相区,绿色部分为固相区。图3-1 (a)、(b)中的冒口中间两部分可以看出出现的独立液相区,于图3-lb中可以清楚的看出,有两圈间断的红色区域(即独立液相区)这就意味着,在凝固的过程中这部分将不会被补缩,就很容易出现缩松、缩孔现象,使铸件产生缺陷。图3-1 (c)、(d)中也可以看到在铸件的底座处也出现了独立液相区,同样也出现了缺陷。
冒口中间即放冷铁处有少量缩孔存在,以至于出现孤立液相区,所以增厚,增加冷铁,以改进其激冷效果。工艺修改后,再进行模拟。具体改进工艺如下:(1)在外锥面下的两圈冷铁加厚到250mm,并把刮沙层的尺寸由20mm减少到15mm。(2)在铸件的内圆中加10块弧长200mm,厚150mm,高与内圆弧面高相等的冷铁,冷铁间的间隙230mm。冷铁与铸件间的刮沙层厚度为15mm。(3)其他部位的工艺不作改动。
改进后用华铸软件进行工艺模拟,结果如图3-2所示,图中的蓝色部位为冷铁。
然后应用图像处理技术生成虚拟的铸件图,进行BMP处理,BMP集成AVI动画。模拟铸件凝固过程如图3-3。从图3-3 (a)、(b)可以看出,铸件凝固过程可以看出此次铸件的凝固模拟结果比改进工艺前有很大的改观。铸件的凝固过程中孤立的液相区已经明显减少到几乎没有。说明此次的铸造工艺比较合理,已经避免了铸件的缩松和缩孔缺陷的产生,达到了铸件的技术要求。
从上述模拟的过程中可以看到铸造过程模拟仿真在铸造工艺设计过程中的优越性。这一技术结合计算机辅助工艺技术的应用,可以彻底改变传统设计方法的落后状况,提高铸件生产的质量和效率。
4、结论
(1)利用华铸CAE软件,通过对球磨机端盖铸造工艺计算机模拟,预测了球磨机端盖在两圈冒口中间部分及轴径处出现了显微疏松,原因是冷铁激冷度不够,再优化铸造工艺参数,保证铸件的顺序凝固及冒口金属的有效补缩,获得高质量的铸件。
(2)利用计算机对铸造凝固过程进行数值模拟,为优化铸造工艺提供了有力的分析依据,提高了设计质量,缩短了生产周期,同时节约了大量的试验费用,降低生产成本,是辅助定制铸造工艺的强有力手段。