1、存在问题
(1)传动齿振动大且磨损快
球磨机额定载球量26 t,转速为19.4 r/min,工作环境差,冲击力大,属于低速重载机械。传动齿润滑脂(ZL-2型锂基润滑脂)利用率低、更新慢。齿轮啮合磨擦脱落的磨屑及进入齿轮密封罩的少量粉尘粘附在齿面上,破坏润滑油膜,加剧了齿轮磨损。传动齿运行噪音大、振动大,齿面磨损快。
(2)烧瓦事故频发
主轴承是对开式滑动轴承,轴瓦材质是巴式合金。为保证球磨机的可靠润滑,设有低油压定值保护装置,压力冲量取自润滑油泵出口总门前的油路上。根据设计,只有润滑油压大于等于0.1MPa的定值时,方可启动球磨机,否则,保护闭锁,从而避免损害主机。实际运行中,由于各种原因,润滑油压经常低于保护定值而无法启动主机,值班人员就关小出口阀门以节流提压,启动球磨机。这样,减少了主轴承和减速机的润滑油量,导致轴瓦烧损。据统计,机组运行7年间共发生烧瓦事故9起,影响发电量61.3 MW/h,减少收入2. 425万无。
(3)轴瓦温度测量不准且无超温保护
主轴承基体两侧设有测温孔。采用插入式热电阻监测主轴承温度并远传至中央集控室多点巡回数字显示仪。运行中,监控主轴承温度小于等于60 ℃,回油温度小于等于50℃。主轴承测温孔深216 mm,而热电阻插入深度仅为173 mm,尽管在测温孔内充盈润滑脂,但仍不能即时反映轴瓦钨金面的真实温度,多次出现表盘显示温度仅40摄氏度,而轴瓦已经烧损的现象。加大润滑油流量的结果却引起轴瓦漏油,污染环境。因无超温报警,轴瓦一旦异常升温,不能及时提醒值班人员采取调控措施,导致烧瓦事故扩大。
(4)减速机轴承漏油
减速机采用人字齿圆柱齿轮,轴承采用溅油润滑,轴承端盖采用毡囤接触式密封结构。减速箱顶部设有87 mm高的呼吸器。运行中,具有较高线速度的齿轮剧烈搅甩润滑油,减速机内温度升高,空气膨胀,大量油雾从呼吸器逸出。端盖密封毡圈弹性恢复力差极易失效漏油,更换频繁,且更换时必须拆除电动机、减速机主动轴和从动轴联轴器,检修时间长,工作量大。
2、改进措施
(1)传动齿采用全自动喷射润滑
全自动喷射润滑装置由空气压缩机、润滑油泵、自动控制系统等组成,如图1所示。喷射喷嘴安装在齿轮密封罩上,并以一定的角度吹扫齿轮工作面。工作时,高压气体(0.4~0.8MPa)先吹除齿轮工作面的尘粒和磨屑,然后和润滑油混合形成的高压雾化油喷向工作面,在齿面形成一定厚度的润滑油膜。停止供油后,压缩气体继续吹扫,用以吹进齿根,均匀油膜,如此循环。
(2)改进主轴承保护系统
以流量保护取代低油压定值保护,利用可调式热电阻接触测量钨金面温度,并增设轴瓦及其回油超温报警。改进后球磨机润滑油系统如图2所示。安装在大瓦淋油器上的流量传感器直接监测大瓦人口油流,将润滑油流量转变为脉宽不同的脉冲信号。同低油压定值保护相比,具有信号显示灵敏、直观,便于监控和调节;脉冲信号抗干扰能力强,准确、可靠;设有低流量、超温报警和低流量停磨保护等优点。一旦出现故障,自动停车、声光报警和输出闭锁信号,提示值班人员及时排除故障。
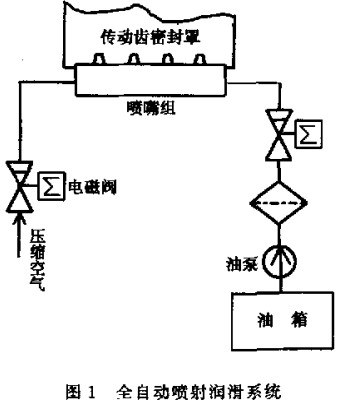
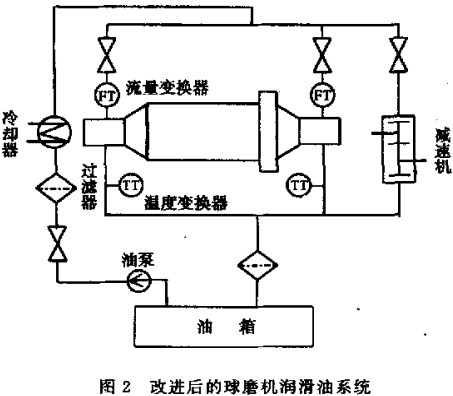
改进端盖密封函,采用剖分式对开函盖,并以J型骨架橡胶油封取代毛毡密封,如图3所示。在转轴上预装1~2只备用油封,仅用30 min即能更换完油封,极大缩短了检修时间,降低了工作量。
适当加长呼吸器,在管内布置迷宫式滤网,以吸附油雾并保护呼吸器畅通。
(4)加强润滑油质监测
随着运行时间的延长,润滑油中的杂质和水分含量逐渐增加,会降低润滑效果甚至损环设备。运行中,加强油质监督,及时滤除油中杂质和水分,保证润滑效果;利用机组大小修机会,根据油质理化指标,对润滑油进行再生处理循环利用,降低油耗。
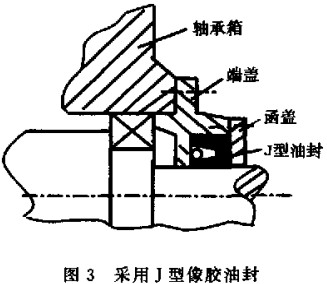
根据监测,夏季节球磨机润滑油温度相差18~23 C,考虑到润滑油的粘温特性,在冬春季节采用68号润滑油,而在夏秋季节适时改用100号润滑油,以增强润滑冷却效果。
3、改造效果
(1)降低传动齿磨损,延长使用寿命
全自动喷射润滑机能够洁净齿面。采用抗压性能极强的680号齿轮油,改善润滑提高齿面抗磨牲,降低机械振动和噪音,延长齿轮工作寿命40%以上,如表1所示。
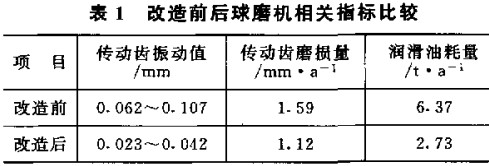
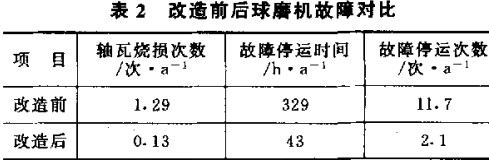
调整润滑油流量,使球磨机处于最佳润滑状态,消除主轴承漏油,杜绝因欠流和断流引起的烧瓦事故,降低设备事故率,如表2所示。
由表1和表2可见,改进后延长了传动齿使用寿命,消除了设备漏油,大幅度降低油耗和维修费,直接经济效益13. 47万元/a;此外,减轻检修人员的维护工作量,减少锅炉故障燃油,增加上网电量,还具有可观的间接效果。
三门峡富通新能源销售球磨机、雷蒙磨、雷蒙磨风机、雷蒙磨配件等。