1、增加减速器箱体基座
原设计减速器没有安装基座,减速器在地脚螺栓浇筑后,固定在基础上,当减速器出现质量问题需拆卸时,必须割断地脚螺栓,安装也费时费力。因此,我们在减速器下面增设了底座,以方便减速器的安装及维修。
在减速器与混凝土基础之间加一个结构件基座,基座连接尺寸保证安装要求,强度满足设备使用要求。将原来混凝土基础打开一个1.6m宽、0.4m深安装基座的基槽;对原来的8条地脚螺栓进行缩短处理,形成地脚螺栓与基座连接,基座与减速器连接的结构形式。在拆卸减速器时只需把减速器与基座间的连接螺栓拆除即可方便地拉出减速器。
2、减速器结构及性能
该减速器是单边单传动,即只有一个输出齿轮与磨机筒体上的大齿轮相啮合,减速器结构见图1。
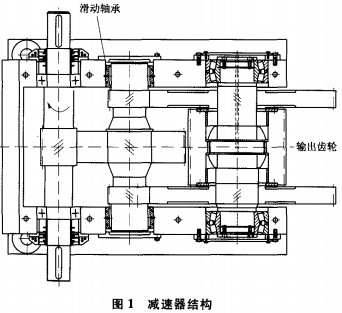
高速轴是采用双列调心滚子轴承支撑的模数为10的斜齿轮轴;中间轴采用滑动轴取支撑;输出轴采用双列调心轴承支撑,除与中间轴相啮合的一组斜齿轮之外,输出齿轮为模数20的直齿轮,直齿轮与输出轴采用鼓形花键齿连接,齿轮内腔与轴之间安装2套关节轴承,这一结构保证输出齿轮有10的自由调心能力,增大直齿轮与磨机大齿圈(齿数为232个,模数为20,直径为4 640.786mm)的啮合精度。
所有装在轴上的齿轮全部采用大过盈配合传递动力,减速器配一润滑油站对所有润滑油点强制润滑,润滑油用N320号极压齿轮油,油站配有列管式水冷却器冷却润滑油。
3、减速器传动构件出现的故障及解决措施
3.1 中间轴滑动轴承发热
在空载及半负荷试车时中间轴滑动轴承频繁发热,最高温度超过70℃,致使滑动轴承合金面出现烧损,减速器无法连续运行。
3 .1.1原因分析
经过检查发现,润滑油冷却能力不足,滑动轴承间隙过大、接触角位置不合适,是滑动轴承发热的主要原因。
1)运行过程中产生大量热量,虽经强制供油润滑冷却,但由于冷却能力不足,导致滑动轴承温度超高。
2)滑动轴承间隙过大,致使中间轴在滑动轴承内跳动度大,很难在轴承腔内稳定定心运行,不仅容易产生震动导致设备运行不平稳,而且不利于均匀承载润滑油膜的形成,极易引起滑动轴承发热。同时,由于间隙过大,会出现传动轴理论中心距与实际中心距偏差过大,不利于设备稳定运行。
3)滑动轴承巴氏合金面接触角应该是最大受力位置,在刮研时是主要精修面,而其它位置不进行刮研精度要求。原设计两片滑动轴承接触角开在正下方,而实际情况或按受力位置分析,中间轴在运行过程中主要受力位置不在正下方,而是在水平侧面偏上部,所以,接触角位置也应该调整到受力位置才合适。
3.1.2解决办法
1)调整滑动轴承接触角位置,减小轴与滑动轴承间的间隙。按轴径、减速器运行最高温度、润滑油膜的合理厚度等进行理论计算,同时结合多年处理滑动轴承问题积累的经验,直径为中260mm的滑动轴承间隙量为0.25~0.30mm合适,原设计的0.35~0.46mm间隙量偏大。所以,在更换滑动轴承时,把实际间隙量调整到0.25mm。接触角位置按理论调整到最大受力区即可。但为增大滑动轴承的承载能力,减少单位面积上的载荷,降低摩擦面产生的温度,最后决定对整个滑瓦表面进行全部精确刮研。经运行使用,设备运行平稳,噪声降低,效果非常理想。
2)对滑动轴承进行强制冷却。解决滑动轴承发热最直接的方法就是强制冷却。通过对滑动轴承瓦结构及装配空间的认真研究,最后确定采用在滑动轴承瓦上钻孔通水的方式。改造方法见图2。
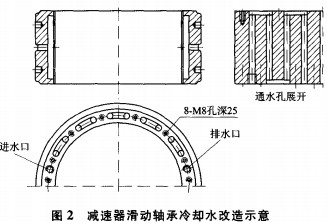
具体步骤如下:
①在滑动轴承瓦上均匀钻12个通孔,水从一侧孔进入,然后在瓦内12个圆孔通道内循环冷却后排出。
②在进出水方向上,把每两组孔中间铣出对应的通水槽。
③在瓦两侧用精加工的6mm厚的压圈把通水孔压牢,压圈与瓦间用小沉头螺钉加AB胶粘合剂压紧。
④进水口与出口用M16mm螺栓钻孔后与软管连接进出水管。
⑤在使用前要通水试验,试验压力不低于0.5MPa。
⑥两半瓦均采用这种形式制作,形成独立的冷却体。
改后效果非常好,滑动轴承温度比原来降低25~28%,中间滑动轴承温度没有超过41℃,再没有因为发热问题停产。
3)加强润滑油站的冷却能力。设备自备的润滑油站使用列管式冷却器,冷却面积为10m2,即使冬季气温在O℃以下时,供油温度仍然会超过45℃。为了进一步降低设备运行时的温度,保证设备安全运行,新增一台8m2板式冷却器串联在油路上,对润滑油进行冷却。这种冷却器占地小,冷却效果好,经过使用,即使在夏季气温超过30℃时,设备供油温度也超不过40℃,对稳定设备运行起到非常重要的作用。
经过以上的改造及技术处理,中间轴滑动轴承发热问题得到彻底解决。
3.2高速轴故障分析及改造方案
减速器驱动功率1600kW,高速轴转速1480r/min,轴承频繁出现高温,使用寿命偏低,轴承游隙由0.15mm增大到0.50mm,严重超标。
3.2.1 原因分析
减速器高速斜齿轮轴上安装2套双列调心滚子轴承,轴承外形尺寸为Ø170mmxØ310mmx110mm,轴承型号为23534,由瓦房店轴承厂生产。轴承内外圈均用定位环进行定位,外圈定位环被轴承端盖压紧,定位环与端盖间在安装时预留0.20~0.30mm间隙;内圈被高速轴肩及联轴器压紧。高速轴完全依靠这2套轴承承载径向力与斜齿轮传动的轴向力。
导致高速轴轴承频繁损坏的主要原因如下:
1)用双列调心滚子轴承承受带有轴向力的支撑布局不合理。双列调心滚子轴承一般安装在只有径向力支撑的布局中,或者小载荷的轴向布局中也有个别使用。如果在轴向力的传动中使用,必然会造成轴承偏离原来的球面运行轨道,虽然是双排滚子运行,但实际上只有一排滚子既受轴向力又承受径向力,另一排滚子只承受径向力,受力倾向理论上也较小,导致双排滚子磨损不均,极大降低了轴承的使用寿命。经过几套轴承使用后游隙检测,2排滚子游隙相差0.03~0.06mm,充分反映出这种布局结构的不合理。另外,由于2套轴承内外圈均进行定位(一般这种轴承是一侧定位,另一侧轴承外圈不定位处于自由状态),并且外圈被箱体壳体压紧,根本不会窜动,在装配高速轴时,根本不可能让2套轴承滚子均在球面轨道承载中心,必然使安装后的轴承受力不均,降低轴承的使用寿命。
2)轴承选型偏小、承载能力不够也造成轴承频繁损坏,有2套轴承是在润滑完全正常的情况下,仅仅开机几分钟就烧坏抱死。这些问题除由于轴承装配结构布局不合理,造成轴承安装时达不到轴承最佳受力状态外,轴承承载能力设计余量太小是最主要原因。经过计算,在1480r/min转速时,23534轴承最大承受径向载荷能力仅为1678~1762kW。而实际减速器输入功率为1600kW,已经接近轴承承载极限,尤其在启动过程中,在达到理论转速之前,轴承实际承载可能超过额定承载能力,导致轴承在启动过程中就烧损。同时高速轴是斜齿轮轴,在运行时会产生6 500~8 000N的轴向力,这也减少了轴承承受径向力的能力,增大了高速轴运行不稳定性的因素。
3.2.2改造方案
结合现有减速器箱体及高速轴的结构,在不动减速器箱体的情况下,把原来86mm宽的滚动轴承改造成150mm宽的滑动轴承,不仅增大了轴承的承载能力,而且有非常合适的布置空间,并且能对滑动轴承进行强制水冷却,从根本上解决高速轴承温度高、频繁损坏的问题。用固定在高速轴上的止推板,把轴向力传递给滑动轴承,实现高速轴轴向、径向受力布局。同时在滑动轴承瓦上设计有冷却水槽,可对滑动轴承强制冷却。改后结构见图3。
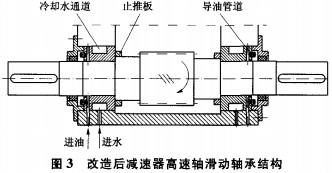
3.2.3 改造安装要点
1)充分利用减速器箱体孔的位置,在不改变箱体的情况下进行滑动轴承的结构设计,同时通过强度及承载能力的计算,内径为Ø170mm、宽度为150mm的双油楔液体动压滑动轴承许用载荷5.5~6.5kl\l,完全可以满足高速轴承载的需要。
2)水泠却结构设计。如图3所示,在滑动轴承瓦外表面中间开一条70mmx35mm环形冷却水通道,通过在箱体上加工连接的进出水管,对高速轴滑动轴承进行强制冷却。
3)润滑结构设计。如图3所示,滑动轴承的润滑是滑动轴承设计的重点之一。第一,油量要比滚动轴承大;第二,存油槽的数量、位置要合适;第三,要兼顾传递轴向力的止推板与滑动轴承端面的润滑;第四,要结合实际,在有限的空间位置完成润滑结构设计。兼顾以上因素后的方案为:在箱体上钻一个Ø16mm的进油孔向滑动轴承供油,油量比原滚动轴承大一倍多,润滑油可直接进入第一个存油槽中,在滑动轴承瓦上用一根1800过渡导油管把润滑油通人第二个存油槽中,形成双油槽配油润滑的结构形式。在油槽靠近止推板一侧,开Ø3mm小油孔通入端面,端面加工环形油沟,实现止推板与滑动轴承端面的润滑。
4)止推板的加工要求。止推板作为传递轴向力的主要部件,在加工时一定要做到:止推板内孔留出足够的加工余量,热装在高速轴上,过盈量不小于0.08mm;止推板的端面与高速轴滑动轴承位置轴径必须同时加工,以保证止推板的端面与轴的垂直度。最终保证滑动轴承端面与止推板端面的平行度,否则,滑动轴承端面因受力木均会发热。
5)滑动轴承瓦的加工工艺要求。滑动轴承瓦是由两半20号锻钢组成的整体,合口面由4条定位销钉将2片瓦把紧定位,合口面用0.03mm的塞尺检测不能有缝隙。由于滑动轴承端面与止推板摩擦,所以在加工时一定要保证瓦内孔、外圆的同轴度,同轴度的偏差不大于0.025mm;相对瓦外圆中心,端面跳动度不大于0.025mm。滑动轴承巴氏合金的浇灌按肯规工艺加工,采用锡基巴氏合金,保证合金层不脱落、无气孔等缺陷即可。
6)滑动轴承的刮研。滑动轴承内孔表面采用整面刮研方式,不刻意刮研接触角,对瓦面多方向研磨检查,以保证接触精度在各方向上均匀一致。滑动轴承与轴间的间隙为0.15~0.20mm,考虑箱体压紧时滑动轴承可能有微量变形,刮研滑动轴承时间隙可取公差上限。高速轴组装到减速箱体后,要用塞尺检测间隙量,不能低于0.15mm,否则要拆下重新刮研。刮研好瓦内孔后再刮研端面,把轴竖起研磨轴承端面,直至端面与止推板完全接触。
7)高速轴安装。滑动轴承刮研好后,2片滑动轴承抱在轴上打好定位销组装一体,把导油管安装好,进行0.5 MPa以上的压力试验无渗漏方可安装。滑动轴承瓦背面要涂密封胶,防止水套中的冷却水渗漏,在半面减速器箱体上调整止推板与滑动轴承端面的间隙量,保证两侧间隙之和在0.30~0.50mm,然后对减速器进行组装。检测猾动轴承径向游隙合适后,精确测量滑动轴承与轴向密封端盖的间隙值,磨定位隔环端面,压紧滑动轴承端面密封端盖,保证滑动轴承轴向无窜动。
8)检测试车。高速轴安装后要保证轴向窜动量在0.30~0.50mm,径向游隙为0.15~0.20mm。具体检测办法如下:在电动机端联轴器没有组装之前,用斜铁撑联轴器间的缝隙,用百分表在另一端测量轴的窜动值,取最大值为轴向游隙量,径向游隙用塞尺检测,检测合格后安装端盖。安装外部润滑油管道时一定要对
三门峡富通新能源销售球磨机、雷蒙磨、颗粒机、秸秆压块机等机械设备。