4Cr13
颗粒机环模的淬火后回火温度对硬度的影响见下表。
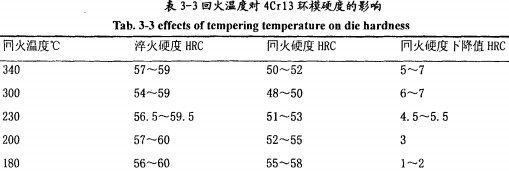
从结果来看,180℃回火,环模硬度很高,脆性很大,极易使环模产生裂纹。300℃是回火曲线中的低谷,不宜采用。340℃回火,环模的硬度偏低,会影响其寿命。合适的回火温度应控制在200℃左右,环模的最终使用硬度在52~55HRC,左右,这样,既可以保证环模不丌裂,又可保证模孔和工作面的磨损很小,使环模的使用寿命大大提高。
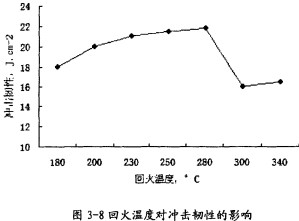
(2)回火温度对环模硬度的影响
4Cr13的第一类回火脆性区的温度范围为300℃~370℃,第二类回火脆性区的温度范围为450℃~600℃。为保证环模在回火后仍能保持较高的硬度,同时又要避开回火发生脆性的温度区,环模采用200℃低温回火较合适。
3.4.4不同回填气体压强对环模冷却速度、硬度及尺寸变化的影响
(1)不同回填气体压强下,冷却温度对时间的变化曲线
由上图可以看出,在相同的装载量情况下,增加回填气体压强能明显提高环模的冷却速度。充填1.6bar压强的气体,与充填1.3bar压强的气体相比,快速冷却时间可缩短23%。
(2)不同回填气体压强对环模硬度的影响
由上图可以看出,在相同的装载量情况下,增加回填气体压强能明显提高环模的硬度。充填1.6bar压强的气体,与充填1.3bar压强的气体相比,硬度提高2~3HRC。
(3)回填气体压强对尺寸变化的影响
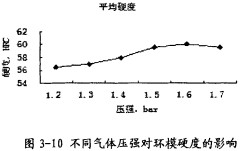
回填气体压力越大,冷却速度越快,环模的变形率越大。
3.4.5真空淬火对环模组织的影响
淬火前环模的金相组织为完全退火处理状态,其组织为:铁索体基体上分布着碳化物及晶界上网状分布着碳化物颗粒。
淬火后的环模金相组织为马氏体+碳化物+残余奥氏体。
(1)环模锻坯材料中的碳化物颗粒分不较均匀
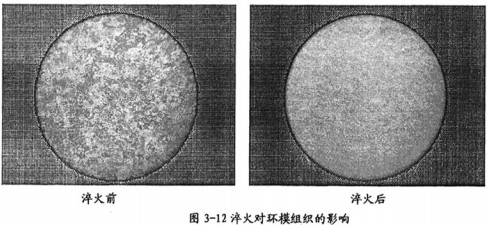
(2)环模锻坯材料中的碳化物颗粒分布不均
淬火可以消除锻坯材质的部分缺陷,但对环模材料的均质性影响不大。锻坯晶粒粗大、均质性差,在淬火工艺中难以消除这种缺陷。
3.4.6热处理对环模尺寸的影响
环模热处理的变形对环模的使用影响较大。如果变形大,椭圆度增加,一方面会使环模不完全出料,影响产量;另一方面会使压辊在环模内摩擦转到时,产生不连续的跳动,对环模工作面产生冲击。环模本身具有较大的裂纹敏感性,经压辊的不断冲击、跳动,有可能产生微裂纹,并使微裂纹扩展,导致环模丌裂。用真空淬火,环模在热处理后具有微小的变形。
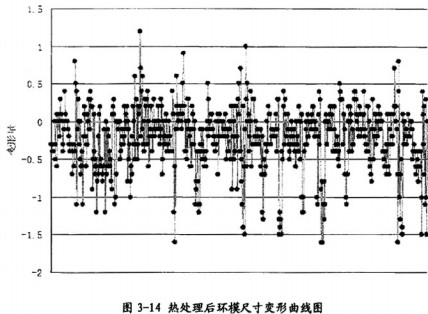
MUZL600颗粒机环模经多次试验结果分析:环模热处理后尺寸变化多数回缩,在回填气体压力不大、冷却速度较慢的情况下,尺寸变化也有可能是涨式。
3.5环模有限元分析
在颗粒机环模的设计工作中,传统的计算和分析方法很难精确地计算颗粒机环模各个部分的应力和变形情况,因此缺乏设计的理论依掘,只是用一些经验公式进行粗略计算。目前国内外应用有限元分析技术在机械方面进行了一些研究,取得了很好的效果,但对于环模颗粒机这类饲料机械还应用较少。本课题采用有限元分析方法对颗粒机环模进行系统的仿真试验,用有限元分析方法计算颗粒机环模的应力和变形,为颗粒机环模设计提供依据。
3. 5.1系统环境
(1) UG系统环境
UG (Unigraphics)是Unigraphics Solutions公司推出的集CAD/CAE/CAM为一体的三维设计平台,广泛的应用于各制造领域,它是一个全三维、双精度的造型系统。它以世界上具有领先地位的Parasolid为内核,在产品的概念设计、机构分析、有限元分析、装配、工程制图、数据输出等领域均有相应的功能模块,尤其是在实体造型方面功能强大。
(2) ANSYS系统环境
ANSYS是一专用的有限元分析工具,其数值模拟和分析功能强大。在工程领域有许多力学问题和场的问题,都可以看作是一定边界条件下求解微分方程,但只有在少数的简单问题能求解。因此,在20世纪60年代,有限元法逐渐展并成熟起来。ANSYS的数值模拟技术是在建立模型(数学模型和过程模型)的础上,对所模拟的客观或理论系统进行定量的研究、试验和分析,它既不是实验方法,也不是理论方法,而是在大量的试验基础上,通过基本原理构建的一套数值计算模型。
ANSYS处于有限元界的领导地位,被全球工业界广泛接受,经过大量的实例验证,在众多的工程领域都有很好的可靠性。
(3)有限元法(Finite Element Method -FEM)
在上世纪60年代术至70年代初,有限元在非牛顿流体力学中的应用得以深入发展。它是解大型非牛顿流体力学问题的数值方法中使用最广,最具有代表性的方法。有限元法的核心是根据变分原理或方程余量与权函数正交化原理建立积分表达式。它将在整个积分区域中的求解函数离散为若干单元区域的连续函数,再通过单元积分,总体合成为代数方程形式的有限元方程。与有限差分法相比,有限元法适合于复杂区域和边界条件的离散,而且对每个区域的近似解是连续的。有限元法中又包含了混合有限元法、FAN方法(Flow Analysis Network)、罚有限元法、富有限元法、控制体积法、有限块法以及修正的Luo-Tanner流线有限元等。
3.5.2有限元分析模型建立及计算分析
环模和压辊之间的载荷分析对环模和压辊的结构设计具有很好的指导意义,同时通过对环模和压辊之间的载荷分析也有利于分析环模和压辊的磨损情况。首先,环模和压辊的强度和刚度计算需要知道两者之间的载荷,知道载荷后A+能确定环模的厚度、压辊的大小;再者,物料压入的多少有与载荷有关.物料压入多,环模和压辊之间的载荷大,环模和压辊的磨损也就越严重,反之,物料压入少,环模和压辊之间的载荷小,磨损少,因此环模和压辊之问的载荷与环模和压辊的磨损有关,磨损又与环模和压辊的寿命有关。
环模是比较昂贵的易损件,其使用寿命是评价环模制粒机性能的重要指标。怎样减少和改善环模的磨损,延长使用寿命,降低生产成本,是研究制粒机的核心内容。环模的寿命与环模和压辊间的载荷有密切关系;
制粒的过程是物料被卷入、压紧,最后从环模上的模孔被挤出,因此在环模圆周方向,环模与压辊的间距越大,物料压力程度越小,载荷也就越小。反之,环模与压辊的间距越小,物料压力程度越大,载荷也就越大。
(1)有限元分析模型建立
在Ansys作有限元分析过程中,建立几何环模是必不可少的一个过程,Ansys有强大的接口能力和对实体的力学分析功能。本文采取UG建立实体三维模型,通过中间软件数据转换的平台,利用Ansys的高级接口技术,实现几何模型的建立,完成数据的转换。
建立的三维模型通过IGES文件导入ANSYS软件分析界面中.
为了定性分析压辊和环模的载荷,建立环模的模型,并施加非均匀载荷,如图3~15所示。所加载荷的函数是:
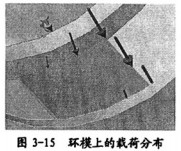
F= kx
通过施加约束,并进行网格划分,得到环模的有限元模型,如图3-16所示。
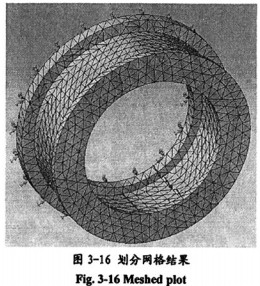
(2)力学模型的建立
单元模型共8个节点.单元材料为线弹性,并且各向同性.根据广义虎克定律:
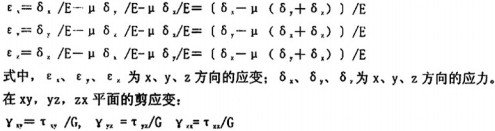
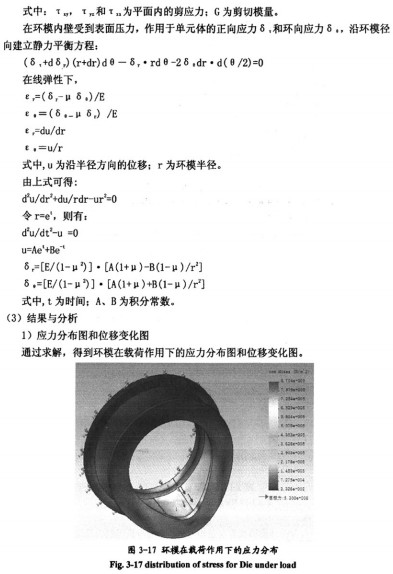
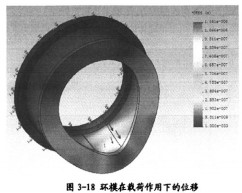
2)环模和压辊之间的载荷分析
可以看出,在这样的载荷作用下,环模外侧的位移变化比较大,这说明如果物料在环模轴线方向的均匀的话,环模里侧的磨损最大,环模外侧的磨损最小。
如果在环模轴线方向卷入的物料均匀,按理是磨损均匀,但是考虑到环模实际上是悬臂梁的结构形式,环模外侧的变形大,因此环模和压辊的间距会比没有工作时大一些,这样物料就没有里侧的物料紧一些,所以磨损小一些。按照这样的分析,环模的磨损曲线应该是如下图所示。因此物料在环模轴线方向均匀卷入的话,里侧反而磨损严重。
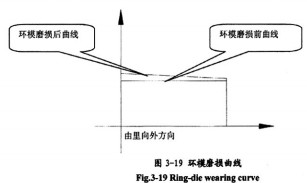
3.5.3环模实际磨损情况
上面的分析是基于载荷在环模轴线方向是均匀这一假设分析得到的结论,实际的载荷情况应该根据磨损的情况反过来分析。图3-20即为压辊的实际磨损照片,环模与压辊磨损曲线如图3-21。
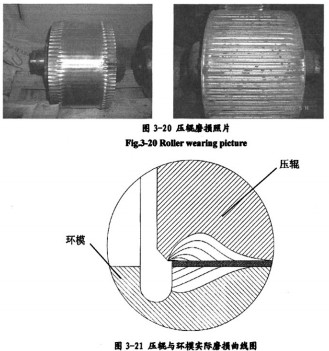
从实际磨损情况看,沿轴向方向,环模与压辊两端的磨损明显大于中间部位,且两端的磨损基本对称(后端更长、更平滑、角度更小)。
3.5.4结论
结合受力分析及实际磨损情况,得出如下结论:
(1)沿轴向方向,物料在压辊与环模之间分布不均匀:
(2)沿轴向方向,外侧分布的物料较内侧多:
(3)沿轴向方向,中间分布的物料较两侧少;
(4)为了使磨损更均匀,可以通过控制物料的分稚来实现:
(5)相关分析需要根据实验进一步验证。
料层的分布情况直接影响环模的使用寿命,所以解决环模的不均匀磨损问题,核心是使料层均匀分布在环模的内壁上,使环模受均匀的载荷作用。通过分析,可以说明选用更加昂贵的环模材料,仅从环模的优化角度出发,或者从饲料的配方、颗粒度等方面不能解决环模的不均匀磨损问题,因此,环模的不均匀磨损只能通过饲料的均匀分布得以解决,而进一步优化环模制粒机的结构是提高环模使用寿命的根本途径。
结论
1、4Cr13是完全合适的环模材料,刚度和韧性都较好, 热处理硬度为HRC52~55,并具有良好的耐磨性和耐腐蚀性,使用寿命长。Cr的增加对环模的硬度没有影响,但可以显著增强环模的耐腐蚀性。实际使用中含Cr量12%左右的环模使用寿命比含Cr量14%的环模在其它处理相同的条件下,其使用寿命减小1/3以上;所以环模质量的源头是从刚锭开始,要确保Cr含量12.5%以上。
2、模孔冷加工时切削转速直接影响环模的表面粗糙度,切削转速越大,表面质量越好。加工的模孑L孔径越小,切削转速越高。采用枪钻加工环模模孑L,模孔直径为1. 6mm时,转速为9000r/min时,表面粗糙度为1.6“m:转速为13000r/min时,表面粗糙度可达到0.8 um。对于普通钻床,一般最高转速为3000~5000rlmin,加工出的表面质量较差,加工小孔径环模时,由于粗糙度不合格,在环模的带料试验中无法出料。
3、热处理淬火温度从1030℃上升到1050℃,硬度可提高1~1.5HRC; 1060℃淬火,硬度虽然较高,但冲击韧性下降明显,热应力太大,极易产生淬火微裂纹。所以,采用1040℃淬火最为合适。
4、真空淬火对环模模孔粗糙度的基本没有影响。
5、4Cr13环模具有高强度和高耐磨性,但也有很大的裂纹敏感性,淬火后的回火相当重要。为保证环模在回火后仍能保持较高的硬度,同时又要避开回火发生脆性的温度区,环模采用200℃低温回火较合适,环模的最终使用硬度在52~05HRC左右,这样,既可以保证环模不开裂,又可保证模孔和工作面的磨损很小,使环模的使用寿命大大提高。
6、在相同的装载量情况下,增加回填气体压强能明显提高环模的冷却速度和硬度。充填L 6bar压强的气体,与充填1.3bar压强的气体相比,快速冷却缩短23%。硬度提高2~3HRC。回填气体压力越大,冷却速度越快,环模的变形率越大。7、环模热处理后尺寸变化多数回缩,在回填气体压力不大、冷却速度较慢的情况下,尺寸变化也有可能是涨式。
8、在颗粒机环模的设计工作中,传统的计算和分析方法很难精确地计算颗粒机环模各个部分的应力和变形情况,因此缺乏设计的理论依据,只是用一些经验公式进行粗略计算。本文应用有限元分析方法针对环模寿命问题,分析环模在均匀载荷与非均匀载荷时的应力与应力强度分别情况,提出合理的方案以解决环模的不均匀磨损,对于环模的研究方法是一次突破和有意义的尝试。
三门峡富通新能源销售颗粒机、
秸秆颗粒机、
秸秆压块机、饲料颗粒机等生物质燃料饲料成型机械设备,同时我们还销售颗粒机环模等配套设备。