0、引言
输煤系统是火力发电厂辅机系统的一个重要组成部分,是保证火力发电厂稳定运行的重要因素之一。黑龙江某公司3台循环流化床
锅炉机组输煤制煤系统在实际运行过程中,由于系统设计方面原因,存在实际出力低、达不到原设计值、制煤颗粒曲线不合理、设备维护费用和运行费用高等问题。该输煤制煤系统设计为双路四段皮带,出力为182 t/h,按规划容量6x75 t/h循环流化床锅炉机组设计,锅炉入炉煤设计热值为12 665 U/kg,颗粒>10 mm。贮煤场设有4个地下受煤斗,主设备为2台跨度31.5 m、起重量St、终合出力200 t/h的桥式抓斗起重机,用于煤场作业;另外有2台轮式装载机和推煤机作为辅助设备。筛碎系统采用二级破碎一级筛分。在一级碎煤室内设有2台出力200 t/h的HSZ - 200型环
锤式破碎机及2台BS - 250型波动筛,还设有2台ZHT -1型电动缓冲滚筒。在二级碎煤室内设有2台出力200 t/h的PCHX80×180型环锤式破碎机。
1、输煤制煤工艺过程
输煤制煤系统是将原料煤矸石加工成符合锅炉燃烧要求的颗粒并输送至炉前仓的全过程。系统的刨面展开简图见图1。
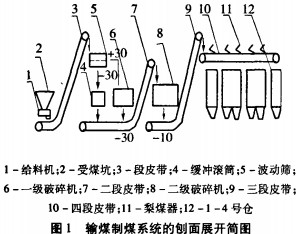
输煤制煤工艺过程:由桥式抓斗起重机(轮式装载机或推煤机)将煤矸石送入地下受煤斗,经其下方设置的电机振动给料机将煤矸石送入一段带式输送机,由一段带式输送机将煤矸石运至一级碎煤室的波动筛进行分级,筛上<30 mm颗粒的煤矸石进入一级破碎机进行破碎,破碎至≯30 mm颗粒;筛下≯30 mm颗粒的煤矸石经缓冲滚筒缓冲与一级破破碎后的煤一起进入二段皮带,由二段皮带输送机运至二级破碎室,进入二级破碎机进行二次破碎,破碎至≯10 mm颗粒后落人三段带式输送机上,由三段带式输送机运至主厂房煤仓间的四段带式输送机上,经四段带式输送机上的梨式卸料器依次送入1-3号锅炉前仓。整个输煤制煤过程由PLC程序控制。
2输煤制煤系统及设备存在的问题
该循环流化床锅炉机组于2003年10月投入运行。该机组投入商业运行初期,燃烧平均热值为12540~16720 U/kg,随着对机组运行参数调整,机组燃煤热值逐渐降低;到2008年,机组平均燃煤热值只有9 614 ~10 450 kj/kg。经现场勘察和分析,发现输煤制煤系统工艺和设备存在若干缺陷。
2.1制煤颗粒曲线不合理
输煤制煤工艺过程因两级破碎机之间无分级筛,造成~级破碎机破碎后≯10 mm颗粒煤和波动筛筛下≯10 mm颗粒煤进入二级破碎机再次进行破碎,这是一种浪费加工,产生如下弊病:
a.加大了二级破碎机的电耗和锤头的磨损,影响系统出力。系统设计出力为182 t/h,实际最大出力仅能达到120t/h,平均出力为90 t/h左右,加速了二级破碎机锤头磨损。
b.制煤颗粒曲线不合理。一方面,造成制煤颗粒过粉碎,制成的成品煤颗粒非常细小的粉状煤含量较多(主要指≯0,1 mm颗粒的煤),这部分煤进入循环流化床锅炉,因循环流化床锅炉燃烧室内温度较低,细小颗粒煤在炉内停留时间短,一次难以燃尽,而且分离器又不易捕捉,致使飞灰可燃物增大,燃烧效率降低。细小颗粒煤不参加物料循环,影响炉内动力、传热特性。另一方面,由于二级破碎机除铁室腔无底板,破碎后达不到粒径的大颗粒煤矸石、石头等含量较多(燃煤热值低,硬度较高,不易破碎),这部分大颗粒煤矸石、石头等从除铁室落人到成品煤中,进入循环流化床锅炉,不能全部循环流化,燃烧不彻底就排出炉外,降低了锅炉的热效率;密相区燃烧份额过大,炉床超温结焦。运行中为避免结焦,减少给煤,导致出力降低。
2.2煤湿时极易堵塞二级破碎机
鸡东热电有限公司所用燃煤多数为洗煤厂洗中煤,含水率高;部分燃料煤露天存放,雨季湿度加大;从煤矿采购的相当部分原煤本身的水分较高。煤湿时二级破碎机堵塞严重、频繁,疏通清理二级破碎机极费力、费时。当煤含水分9%~16%时,其上煤量不能超过70 t/h,严重制约了系统制煤能力,影响机组负荷。
2.3二级破碎机锤头磨损不均
由于二级破碎机中心线与上部二段皮带输送机中心线相差658 mm,二段皮带下料槽与二级破碎机人料槽一侧相对应,造成进入二级破碎机的煤流集中在破碎机转子轴向一侧,使破碎机锤头磨损严重不均。靠近煤流侧的锤头磨损到更换程度时,另一侧锤头磨损轻微,被迫与煤流侧的锤头同时更换,更换频繁,维护量大;二级破碎机转子上只有1/3、部分的锤头能满负荷工作,破碎机达不到满负荷出力。
2.4二级碎机破筛板和锤头强度不够
二级破碎机筛板是由4块长970 mm的弧形铸钢耐磨板铸成,每块筛板中间只有一条筋板。因燃煤热值低、煤中含有较多的不易破碎的矸石、石头等,这些不易破碎的矸石、石头还没有被破碎到合格颗粒时硬从筛板珊逢中往外挤,由于筛板强度不够,筛板筛逢就被挤大而无法保证制煤颗粒了。另外,1台二级破碎机共有锤头124件,分4排装在转子圆盘和摇臂上,由于锤头数量多,体积小,强度低,锤头频繁碎裂,严重时每班至少出现1次锤头碎裂现象。
3、输煤制煤系统工艺改进及设备完善
为了解决输煤制煤系统工艺缺陷造成制煤能力低、制煤曲线不合理以及二级破碎机结构问题,确定如下改造方案:把原来的输煤制煤两破一筛工艺流程改成两破两筛工艺流程,即在一、二级破碎机之间加分级筛,同时改进二级破碎机不合理的进料方式和二级破碎机内部结构。
3.1在二级破碎机前加分级筛
在二级破碎机前加设分级筛,筛机选型是改造的重点和难点,所需要的分级筛属于最终成品筛分,是细颗粒的分级。一般细颗粒物料的分级筛分级潮湿物料时,其出力都会明显降低,易堵筛孔;由于该公司储煤场干煤棚较小,雨季时煤的水分较高,所进燃料煤中含水分较高的煤矸石占进煤量的1/2左右,燃料煤不但潮湿,而且粘性大,用常规的筛分设备不能发挥正常的分级功能。潮湿细粒级粘性物料的干法筛分是国内外研究筛分技术的难点,因为潮湿细粒级粘性物料互相粘结成团,松散困难,黏附在筛面上堵塞筛孔,使筛面的有效筛分面积降低,导致筛分效率下降。目前国内研制的能适合潮湿细粒级粘性物料分级的筛机主要有琴旋筛、螺旋分级筛、弛张筛以及GS型煤用概率分级筛等,还有增大振动参数的大振幅强力振动筛。河南太行振动机械股份有限公司的GY21525型高振幅圆振动筛既能满足生产条件及出力要求,又基本上能满足现场尺寸安装要求,价格较其它型同等出力的筛机便宜近1/2,最后确定该型筛机为改造所用筛机。
GZY1525型高幅筛振动强度非常大,足以使颗粒间的液体架桥断裂,能达到较好的分级潮湿细颗粒物料的目的;双层筛面强制预先筛分,克服了大颗粒阻碍细颗粒物料的透筛,加速了筛分过程,增大了筛机的处理能力;弹性筛面,使筛孔变形,覆盖膜断裂,筛面共振,使粘性成团物料碎裂,使其透筛。该型筛机能满足潮湿细颗粒物料的筛分,还具有体积小、处理量大的优点,很适合空间尺寸小、筛分的物料又比较湿的情况下选用。
3.2完善二级破碎机
3. 2.1 加装二机破碎机除铁室底板
二级破碎机工作腔是由破碎板、筛板、拨料板等部件组成,拨料板与机壳构成除铁室腔,该腔下无底板,破碎不了的硬物如铁等从此排出。该机原设计除铁室腔无底板,目的是为排出破碎不了的极少量的大颗粒物料,以便保护破碎机的安全。由于所燃用的燃料煤属于低热值劣质煤,硬度高,不易破碎,除铁室腔无底板使制煤不合格大颗粒量较多。除铁室腔加设了底板时,制煤能力大大下降,远远满足不了锅炉燃煤的需要,并且过粉碎更加严重。在二级破前加设高幅筛以后,使进入二级破碎机的煤量减少50%,又改进了二级破碎机的进料槽结构,使二级破碎机能满负荷工作,在这种情况下将二级破碎机除铁室腔加设了底板,既保证了制煤颗粒,又保证制煤能力,同时还避免了过粉碎。
3.2.2完善二级破进料槽结构
在二级破碎机前加筛改造后,将破碎机进料槽加宽到和破碎机转子一样宽,并在进料糟腔内加设布料板,从而使破碎机沿转子轴向长度上都能均匀参于工作,破碎机出力达到了最大化。
3.2.3增加筛板强度
二级破碎机筛板是由4块长970 mm的弧形铸钢耐磨板组成,每块筛板中间只有l条筋板,筛板强度不够,使不易破碎的矸石、小石头等硬从筛板筛逢中往外挤,将筛板筛缝挤大,无法保证制煤颗粒。对此,将每块筛板再增加2条筋板,每块筛板有3道筋板,从而增加了筛板的强度。
3.2.4加大锤头体积
二级破碎机锤头由62个圆环和62个齿环组成,1个圆环和1个齿环为一组,1个圆环或齿环重量只有10kg,强度不够,经常碎裂。将1组圆齿环改成1个圆环或齿环,圆环或齿环加大l倍,增加强度,延长寿命,数量减半,但总重量没有变,因而负荷没有增加。
4、结论
输煤制煤系统工艺改进与设备完善后,其制煤能力明显提高,制煤颗粒大小合理,提高了
锅炉的热效率,缩短了系统设备的运行时间,节省了二级
破碎机锤头的消耗和系统维护费用,减轻了运行人员的劳动强度。