1、前言
球团车间担负着高炉熟料供给丁作。随着高炉的产能增加,球团矿在高炉炉料的比例对于提高高炉产量,降低生产成本,提高经济效益起着巨大作用,球团矿TFe的提高对高炉减少渣量,降低焦比有很大的作用,并在生产实际中的地位越来越高,因此高炉对球团矿产、质量提出更高的要求,尤其是对TFe指标,球团生产所用原料的结构上差异较大,而烘十机、润磨机的有效使用是改善原料结构上缺陷的主要手段。烘干机将原料水分脱至工艺需求;润磨机通过挤、碰、压、磨作用,使原料进一步均匀、细化,降低粘结剂配比,提高生球强度,对于优化焙烧制度,提高产、质量有很大的促进作用。我厂现阶段烘干机、润磨机运行后,由于设备本身缺陷和设计中的不合理,造成润磨机、烘十机作业率低,使用效果差等原因,使粘结剂消耗较大,针对这种情况,我车间经过认真分析总结对烘于机、润磨机进行了改进和维修,进一步降低粘结剂配比,提高球团矿TFe指标,满足高炉需求。
2、原因分析
由于南北竖炉烘干机粘料严重,进料不足且形不成料幕,而且烘干效果不好,导致南北竖炉烘干机作业率不高,原料混合不均匀,粘结剂用料偏多。由于润磨机篦板裂、蓖板螺栓断.严重制约润磨机的运转,造成润磨机停机频繁,设备作业率低,烘干机和润磨机配合使用效果不好,原料混合不均匀,再磨再选精矿水分大的问题解决不好,导致粘结剂配比较大。
3、确定目标
原料条件的改善,以及设备的完善,烘干机润磨机作业率提高,使粘结剂配比逐步降下来,根据实际情况,保证产、质量的基础上,具体制定了以下目标:烘干机与润磨机未运转,皂土粘结剂混合物单耗26.00公斤/吨,烘干机与润磨机运转,皂土粘结剂混合物单耗24.0公斤/吨,从而降低粘结剂消耗,提高球团矿TFe含量。
4、改善原料质量
球闭用铁精矿的粒度、品位、S含量对其质量影响很大。竖炉在2005年10月之前,主要使用南料场精矿及精矿仓混合精矿。之后改为再磨再选精矿配加南料场精矿,配比为70:30左右,今年,再磨再选料的整体粒度善和全再磨再选料配比,注重过程控制,科学量化管理,严细执行,分解实施,责任到人,并对计量秤进行校正,准确记录,来降低粘结剂配比。各种精矿的性能列于表1。

从表2中数据可以看出,三种铁精矿各有优势:南料场精矿的水分适中.S含量较低,但粒度较粗,品位低.S102含量较高;再磨再选精况“粒度细.S含量较低,品位高,Si02含量较低,而水分高;混合精矿粒度细.SiO2含量较低,但S含量高,且水分高。综合考虑再磨再选精矿用于球团矿生产最佳。增加再磨再选精矿配比,则TFe可以提高,相对粒度(-200目)细料比例提高,有利于生球质量提高,有利于Si02相对降低,有利于成品球冶金性能的提高。
4.1 生产过程中稳定原料成分.降低皂土配比
现阶段球团生产用料,主要是选矿厂,经管道皮带直接输送至南料场7跨,再磨再选精矿粒度细,小于200月达到85%以上,水分高达到10.0%以上。整于这种情况,要求7跨精1皮带必须穿梭布料,使之成分稳定均匀,保证半跨穿料、半跨出料。又针对配料圆盘由于料潮,圆盘盘底打滑,出料不稳定,及时跟没备组联系,利用小修时分别对精矿园盘采取改造,盘底改为料磨料,从而稳定精矿圆盘出料量,同时加大对配料岗位考核力度使配料稳定,使过盘制度得到有效实施,达到全再磨再选精矿配比,使粘结剂配比降低。
5、提高烘干机、润磨机的作业率
5.1提高烘干机效率
由于南北竖炉烘干机扬料板粘料严重,烘F机进料量只有50t/小时且形不成料幕、烘干效果不好只能脱掉1.5%的水分,鉴于这种情况7月中旬对南南炉烘干机扬料板整体更换、同时对南北竖炉煤气管道进行清洗,压力有所提高,达到5Kpa左右,热值明显提高,温度达到1080℃,烘干效果有所好转,为降低粘结剂配比提供保汪.针对南竖炉烘十机扬料板改造为复合升举式扬料板,改造后扬料板存在粘料的问题。7月24日一10月27日针对南竖炉烘干机扬料板改造后粘料的问题,又对北竖炉烘干机扬料板整体进行更换改造,从而解决了因长时间腐蚀造成扬料板掉和粘料多形不成料幕影响烘干效果的问题,北竖炉烘干机改造后,废气烟囱抽力不够导致烘十产生的废气在烘十机内不能及时抽走,烘干机内饱和蒸汽压力高,彤成水蒸气部分重新冷凝成水进入料中,使烘十后出料水分大,影响润磨机的进料量,不能满足生产需求,针对烘十机烟囱抽力不足、人料口蒸汽大的问题,对烘千进料烟罩进行改造、改造后烘十效果明显好转、使烘干机过料量90吨/时,脱水达到1.8%的较好水平,使润磨机的进料量明显增加,烘干机作业率的提高,解决r粘结剂配用因料潮混合不均匀,生球粒度不稳定的问题;运转后粘结剂明显降低、同时解决了料潮堵润磨机篦板的问题。(如表2)。

5.2润磨机改造提高润磨机效率
润磨机篦板裂、蓖板螺栓断,严重制约润磨机的运转,造成润磨机停机频繁,设备作业率低,备件消耗极大。设备组对蓖板及蓖板螺丝进行改造,生产组对润磨机钢球粒度及组成,钢球加入量、进行摸索试验。将润磨机蓖板螺丝由M36改为M42,螺栓选用10.9级高强度螺栓。螺栓接触面由斜面改为平面,杜绝了螺拴受冲击产生位移的可能,避免螺丝松动,解决了蓖板螺丝断的问题。对润磨机蓖板结构进行改造,加强了易裂部位的强度。对南竖炉2#润磨机钢球量进行标定,加入直径lOOmm钢球65吨后运转,螺丝断、篦板裂严重。钢球直径由100mm降至80mm,且降低润磨机钢球数量,螺丝断、篦板寿命有所好转。从而确定出最佳钢球加入量为40吨,每日补充钢球直径为80mm,加入钢球量30个。此种操作制度对篦板、螺栓损伤小,生产效果较好。针对螺丝紧固不好、易断的情况,采用每日自班专人负责紧周,从过去连续运转12小时提高至24小时以上,篦板螺丝更换次数明显减少,篦板寿命有很大提高从而使润磨机作业率提高,又通过对润磨机入料皮带改造从550mm加宽至650mm,提高入料量降低粘结剂配比,提高TFe品位,提高生球质量起到关键作用。
5.3通过制定相应制度提高润磨机作业率:
5.3.1南北竖炉润磨机必须保证一台运转,一台备用。备用润磨机油温必须升到30~35℃,螺旋线必须清干净,螺丝紧同好,能随时启机,有故障及时找相关人员处理。两台机原则保证交替运转周期不超一天。
5.3.2润磨纳入正常生产工艺,不允许私自甩开任何一个工序环节,若由于工艺需要确须改变工艺,经车间向生产部同意备案后,方可实施,岗位人员必须随时掌握来料量和槽位情况。严禁空转润磨机或投料量过少导致篦板损坏,过料量不低于50吨,小时。
5.3.3润磨机点检、运转记录要认真填写。岗位每小时对岗位进行巡检。工长对烘干机、润磨机的运转要在下午4:00调度会上详细汇报,岗位对传动小齿、托轮、挡轮等接触部位不及时加油。
5.3.4来料潮,烘干机脱水后水分大于9%。润磨机可视情况运转或停机。烘干机若停机,润磨机禁止运转。
目前,随着原料条件的改善,铁精矿粒度变细,再选再磨料-200目达到85%以上,烘干机与润磨机配合使用,烘干机运转,解决再选再磨料水分大的束缚,保证全再选再磨料配比。润磨机运转,改善原料的特性,使物料更加的均匀,保证南北竖炉全再选再磨料配比。使得粘结剂配比降低。
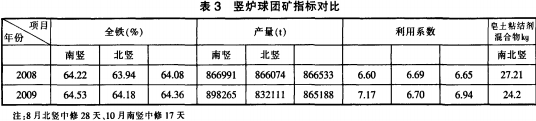
6、效果分析
6.1 产质量指标对比
烘干机润磨机作业率的提高,降低了原料水分,润磨挤、碰、压、磨作用,使原料进一步均匀、细化,降低粘结剂配比,有效调节生球粒度、提高生球强度从而提高球团矿的产质量,烘干机和润磨机的正常运转使降低粘结剂配比明显降低见表(3)。
2008年-2009年竖炉球团矿指标如下:
从表4中数据可以看出:通过提高烘干机和润磨机的作业率,竖炉球团全铁含量由2008年的64.08%,提高至2009年的64.36%;利用系数由2008年的6.65%,提高至2009年6.94%;皂土粘结剂混和物单耗降低3.01kg /t,2009年竖炉产量1730376吨、粘结剂价格为1960元/t皂土价格为270元/t,(粘结剂、皂土配比80:20)则年效益为:1730376x3.01+lOOOx (1960x80%+270x20%):844.81万元。
间接效益:
竖炉球团矿产质量的提高,创造了较高的经济效益,并为高炉进一步优化炉料结构和增产降耗奠定了良好基础。