3000 Ua ADC发泡剂原有1 000 t/a和2 000 t/a两条干燥生产线,均为正压间歇箱式气流干燥工艺,生产能力小,自动化程度低,工人劳动强度大,干燥环境差(主要是粉尘污染严重),安全隐患大,劳动生产率低下,产品质量不稳定。2003年年初,根据市场需求和公司氯碱发展的需要,开封东大公司决定建6 000 Ua ADC发泡剂干燥装置,同时要求提高自动化水平,提高产品质量,为平衡公司氯碱做好准备。公司技术人员通过广泛的讨论、学习、研究,最终确定了采用负压连续气流干燥的新工艺。2003年8月开始设计,经过紧张施工、安装,2004年2月试生产一次投料开车成功。3年多的连续运行证明,干燥装置能力达到了6000t/a以上,产品质量明显提高,现场环境干净整洁,劳动生产率大幅度提高。
1、原有干燥工艺
原有干燥工艺为正压间歇箱式气流干燥工艺。其工艺流程:洗涤合格的湿ADC经三足离心机脱水,用行车吊出,间歇投入一级干燥箱,在搅拌情况下与热空气充分接触进行干燥,待水分基本合格之后,调整进空气量。风料通过旋风分离器,绝大部分ADC进入二级干燥箱,夹带部分ADC的气流经布袋除尘器除尘后排空,留在布袋上的ADC通过人工敲击也进入了二级干燥箱,进一步干燥合格后包装粗品,再搬运到振动筛分工序筛分,除去杂质包装成品ADC发泡剂。原干燥工艺流程见图1。
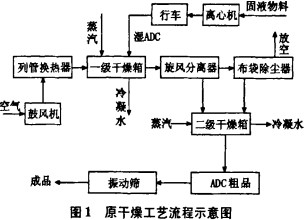
2、原干燥工艺存在的问题
(1)正压生产易造成干燥的ADC粉末外漏,浪费物料并污染环境;
(2)间歇进料干燥系统中的ADC物料较多,存在较大的安全隐患,开封东大公司曾在2000年、2001年出现了两次较严重的ADC分解事故,造成数十万元的经济损失,均是干燥箱搅拌器与金属机械杂质摩擦所致;
(3)从离心机中人工吊料及向一级干燥箱加料,体力劳动强度大,易吊坏滤布造成物料浪费;
(4)粗品搬运过筛不仅增加体力劳动,浪费包装及物料,而且干燥ADC容易吸潮而难以过筛,尤其是在阴雨天,更易造成ADC发泡剂成品水分超标,造成结块而影响质量;
(5)旋风分离器内的物料和布袋除尘器内的物料未分开,造成ADC粒径分布宽,使产品在使用时存在发泡周期长、不易控制以及有效发泡体积小等缺点;
(6)自动化程度低,劳动生产率低。
3、干燥工艺的改造
针对上述存在的问题,开封东大公司设计人员最终设计了负压连续气流干燥新工艺。其工艺流程见图2。
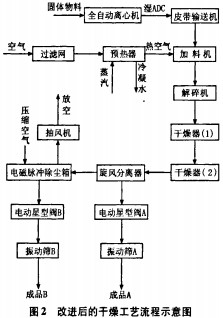
工艺过程:空气由引风机经空气过滤网吸入,经板翅式换热器与蒸汽间接换热升温后进入加料机风管,与经全自动离心机脱水由皮带机输送来的湿ADC混合,经解碎机破碎,在热空气的吹送下进入干燥器,在两级干燥器中不断除去水分,风料进入旋风分离器,95%的干ADC通过星形阀振动筛包装并称质量,得到成品A。细小的ADC被热风带入电磁脉冲除尘箱.干ADC吸附在除尘箱布袋上。水分由热空气夹带,经引风机抽出放空。用压缩空气将吸咐在除尘箱布袋上的ADC吹到除尘箱底部,由螺旋推进器经星形阀振动筛包装并称质量,得到成品B。
4、改造效果
(1)经过3年多的连续运行,干燥能力达到6000 Ua以上,物料消耗明显下降。
(2)通过旋风分离器的物料与通过布袋除尘箱的物料分别包装销售,用户反映良好。A成品平均粒径为14~15 pm,B成品平均粒径为8~9μm,粒径正态分布曲线明显改善,产品质量提升了一个档次。
(3)物料连续进出系统,系统中物料少,安全性大大提高。
(4)采用了先进工艺和设备,自动化水平高,操作方便,改善了工作环境和劳动条件,劳动生产率提高2倍多。
(5)整个系统内为负压,从根本上解决了ADC发泡剂粉尘外溢的难题,现场环境干净整洁,物料损耗降到最少。
5、结论
新建的6 000 t/a ADC发泡剂干燥装置消化吸收了国内外同行业的先进技术,提高了自动控制水平,劳动生产率大幅度提高。增强自主创新的能力和水平,是我们今后工作中应坚持和倡导的。