
烘干搅拌输送新闻动态
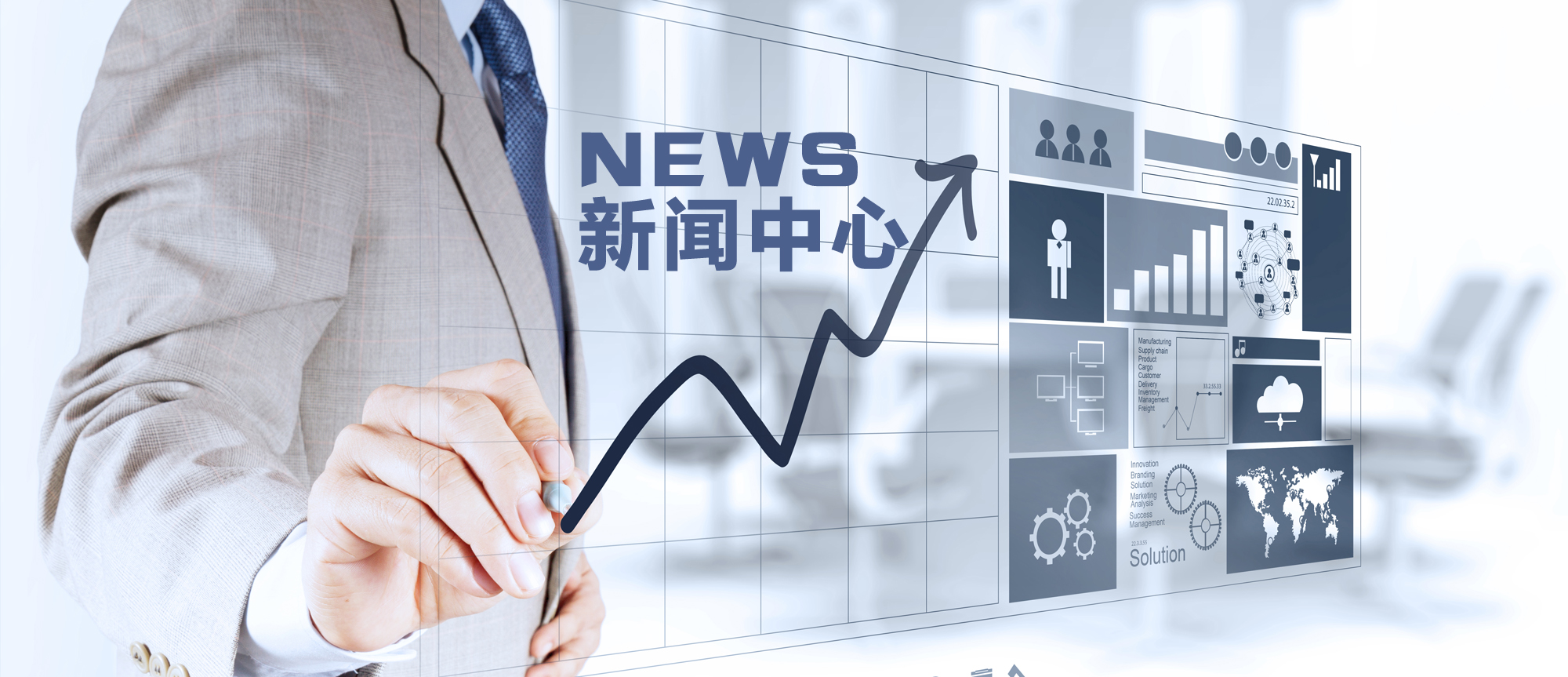
富通新能源 > 动态 > 烘干搅拌输送新闻动态 > > 详细
国内外带式输送机的现状及技术前瞻(下篇)
发布时间:2013-03-24 08:55 来源:未知
3、矿用带式输送机发展的技术前瞻
矿用带式输送机大型化与高可靠性要求,对设计者和制造者提出了更高的要求,只有解决了带式输送机发展的关键技术,才能制造出高性能、高可靠性的大型带式输送机。其关键技术如下。
3.1动态分析技术
建立带式输送机的输送带在起动和停机过程中的动力学方程,求解输送带上不同点随时间推移所发生所的变化,找出变化剧烈的张力波可能造成的破坏,这就是带式输送机的动态分析。 动态分析技术是一门综合性学科,不仅要对整机运行全过程的动态特性进行分析,更重要的是对其涉及到的基础理论,运用现代先进技术进行系统研究,是当今世界的高新技术。采用动态分析技术进行设计,不仅可实现优化设计,降低设备的投资费用,而且还可预防运行事故的发生,提高设备运行的可靠性。在国外,德国、前苏联、澳大利亚、美国、波兰、南非、日本等,都对动态分析技术进行了深入的研究,取得了可喜的成果,有的己在实际工程中得到应用。在国内起步较晚,动态设计的方法、概念还处于刚体力学阶段,还没有真正应用到设计中去。应用动态分析技术来对大型带式输送机进行优化设计,最直接、最明显的经济效益——较大幅度地降低了输送带的安全系数,安全系数最小可达4.8,这对国内常规标准设计来说是不可想象的,目前国内即使己使用了可控启动装置,其安全系数也只能取到8左右。在满足安全运行的条件下有效地降低输送带的强度等级与各元部件的重量,输送带费用约占大型带式输送机费用的35:-45%,大大地节省了设备费用。澳大利亚GREGORY煤矿使用的一条大型带式输送机,其主参数为:L-lOOOm、B-0.9m、Q=1400T/h、V-4.2m/s、H(提升高度)-30m、N-3×355+840kW。这条带式输送机专门请美国诺丹尔教授进行动态优化设计,安全系数为4.8,仅选用ST1600钢丝绳芯强力输送带。国内官地矿即将使用的一条大型带式输送机的主参数为:L-5400m、B- 1.2m、Q=1200T/h、V=3.5m/s、H-90m、N-4×500kW。由于是按照国内常规标准设计,即使己使用可控启动装置,安全系数也只能取为8.02,再不敢往下取,只能选用ST3500的钢丝绳芯强力输送带。如果官地矿的带式输送机也是采用动态设计,光输送带这一项就可节省费用600多万元,经济效益相当可观。带式输送机动态分析技术的研究,在国内刚起步,还没有真正应用到设计中去。掌握动态分析技术,不仅可使我国带式输送机技术水平有一个质的飞跃,还可带来巨大的经济效益,应尽快开展这方面的研究工作。
3.2可控启动技术
大型带式输送机的启动,一定要有一个足够的时间,使启动加速度保持在允许范围内。运距越长、带速越高、输送量越大,启动时间就需越长。假如没有足够的启动时间,输送带初张力会下降,最大可下降50%左右,就会丧失输送带与传动滚筒保持正常传动所需的张力比,造成输送带在传动滚筒上打滑而不能启动。启动是一个加速过程,加速度值由零增到最大又下降至零,输送带发生粘弹性变形,处于不稳定状态而产生动张力。当带速越高、启动时间越短时,启动加速度与输送带变形就越大,因而动张力也就越大,造成巨大的瞬时冲击,就会损坏输送带与其它元部件。因而必须对启动时间加以控制。可控启动时输送带张力波动极小,启动平稳。可控启动就是我们平时所说的软启动,即在设定的启动时间内,通过控制输送带启动加速度值,来确保输送机按所要求的启动速度曲线平稳启动,并达到额定速度:同时使启动电流与启动动张力控制在允许范围内。因而必须对启动时间、启动加速度进行控制,启动时间与启动加速度应根据带速、运距、输送量等参数来确定,根据我国有关标准规定,启动加速度不得大于0.3m/s2。采用可控启动,可使输送带初张力下降大为减少,仅下降不到10%,可以保证输送带不打滑。可控启动技术是大型带式输送机的关键技术,己成为带式输送机是否达到技术先进的标志之一。通过电控与可控启动装置组成的闭环调节系统来完成带式输送机的可控启动,选择哪一种可控启动装置,除了考虑技术性能外,还必须考虑其经济合理性。
近几年来,国内外相继开发成功了多种形式的软起动装置:①液粘性软起动装置,如澳大利亚的BOSS系统、美国的CST等。②液力型软起动装置,如调速型液力偶合器、加长后辅腔液力偶合器等。③电气型软起动装置,如变频调速、可控硅控制开关磁阻起动等。④机械式软起动装置,如BEST、德国力士乐公司的辅助液压马达周转齿轮系统(原理与BEST相同)等。
需要特别指出的是:带式输送机对驱动装置的调速要求不是输送机运行所要求的,其目的是:①降低起动电流对电网的冲击。②减少起动过程中各承载部件的动载荷。所以对输送机不必进行高精度的调速和控制。通过前面分析我们可知:国产软起动装置完全能满足带式输送机软起动的要求。由于调速型液力偶合器比电软起动具有更优良的性能,所以国内现有带式输送机软起动装置90%以上是采用调速型液力偶合器,不仅技术可行,而且经济合理,操作维护又简单。调速精度太高的软起动(如BOSS、CST等)对带式输送机来说,技术上没有必要,经济上也是一种浪费。只有经常需要变速运行的设备(如潜水艇、军舰等),采用液粘调速装置才是合适的,才能最大限度地发挥它们的优势。
国外带式输送机的软起动大多数也是采用液力调速装置。即使在美国,在带式输送机上使用差动轮系液粘调速装置也是少数。97年11月上海分院与西山矿务局联合组团赴澳大利亚技术考察,在所考察的六个煤矿的八条大型带式输送机的软起动,全部是采用液力调速装置,其中GTEGORY煤矿长度为10公里带式输送机、澳大利亚PROK公司为马来西亚设计的6.5km、SEDGMAN公司为印度尼西亚设计的37km超特大型带式输送机软起动也是采用液力调速装置。目前国内生产的调速型液力偶合器还存在漏油和效率损失等问题,需要进一步完善。
3.3 下运制动技术
下运输送机的三个技术关键为:
(1)制动能量大
制动器吸收的能量有机械能转化为热能,如仅使用闸块式制动器,闸轮表面热量集中,由于制动时间短,热量不能及时散发出,温度急剧升高,如超过150℃就有引起煤尘爆炸的危险。而且温度高则闸衬易于磨损,摩擦系数下降,制动时间增加,导致制动能量增大,温度又进一步升高。超温和闸衬互为因果,会使闸块式制动器的制动力矩急剧下降,以致造成飞车事故。
(2)制动平稳性要求高
制动减速度要求限制在0.1 --0.3m/S2范围之内,制动时间约l0: -20s。如果用恒力矩制动装置,就存在这样一个问题:一方面为确保制动的可靠性,制动器的额定力矩应力输送机满载力矩的1.5: -2倍;另一方面当输送机上的物料很少时(此时最容易发生滚料现象)也以同样的力矩来制动,其减速度必将超出允许范围。因此,为保持稳定的制动减速度,就要求制动力矩能随外来负载的大小而自动调节。
(3)在事故停电时要求系统迅速而安全地制动。
所以一般的机械抱闸制动器是不能用作井下下运带式输送机的可控制动装置,用于煤矿井下的制动装置必须满足三个技术要求:①制动减速度必须限制在0.1~0.3m/s2范围内。②每小时制动十次,接触面除不能产生火花外,各元部件温度不得高于MT820 -1999“煤矿井下用带式输送机技术条件”中规定的温度。③整个采区停电也必须保证能够制动。完全满足上述三个技术要求的国产制动装置仅为液力制动装置,己在煤矿井下普遍使用。但此种制动装置存在着体积庞大、多种能源(电、液、气)操作复杂,易出事故等缺陷,需要加以改进提高。比较有发展前途的是盘式制动装置,它体积小、重量轻,省掉一套机械抱闸制动器,操作维护简便,更适合于煤矿井下使用。但目前国内井下用的下运带式输送机大多采用液力制动装置,原因是盘式制动装置的关键技术还没有很好地解决,下运阻尼输送机技术也还需要进一步完善和提高。
3.4 自动张紧技术
张紧装置是保证带式输送机正常工作的重要部件,在确保输送机中最小初拉力能满足挠度要求的条件下,驱动滚筒趋入点和奔离点的张力比应为定值,为此要求在起动时张紧力与额定工作时张紧力的比值k=1.4~1.5,允许波动±10%;在正常工作过程中k=0.9~1.1。当输送机的结构、起、制动方式及张紧装置的安装位置确定后,张紧装置的特性就取决于其自身的性能。没有张紧装置的密切配合,要想获得良好的可控启(制)动与自移机尾是不可能的,自动张紧技术也是带式输送机的一个关键技术,它可大大地提高输送机运转的可靠性。国产带式输送机运转事故多的因素之一,就是张紧装置性能差,工作不可靠所造成的,但目前张紧技术还不被人们所重视。大型带式输送机所用的张紧装置必须满足以下技术要求:①自动调整张紧力:能随着输送带张力变化而能自动地调节张力与张紧行程,始终保持输送带所规定的挠度,并使驱动滚筒趋入点和奔离点的张力比应为定值。②响应速度快,当输送带张力发生一个变化值时,张紧装置使输送带张力恢复到原值所花费的时间称为响应速度。要求响应速度越快越好,当响应速度小于输送带张力变化周期,就会使输送带获得一介稳定的张力,运行平稳;反之,输送带张力不稳定产生振动,严重时还会发生共振。③不能出现死区:即张紧滚筒作反向移动时,不至于产生张力的突然变化。尤其对机尾有低谷的高垂度输送机,制动时在低谷处会由于垂度过大而引起输送带的折叠和严重变形,从而导致煤的滚落。最简便而有效的自动张紧装置是重力张紧装置,此种装置由于受到煤矿井下空间的限制,使用受到一定的影响,仅用于倾斜运输的带式输送机上。国内煤矿井下使用较多的是绞车与油缸相结合的自动张紧装置,绞车用于输送带大行程张紧,油缸用于小行程张紧,两者的结合而达到自动张紧的目的。经煤矿实际使用证明,此种自动张紧装置能达到输送机的启制动和正常运转时对输送带张紧的要求。国外使用的是液压绞车自动张紧装置,由低速大扭矩马达根据输送带张力变化,通过改变流量来有效控制绞车转速的快、慢与开、停。此种自动张紧装置的响应速度与可靠性要比国内的高得多。在设计带式输送机张紧装置时,除了满足上述技术要求外,还必须确定张紧装置最佳的安装位置,以获得最小的张紧力与张紧行程以及最快的张紧响应速度。张紧装置在不同的安装位置上,其所需张紧力与张紧行程相差甚大。目前国内的张紧装置能做到自动调节张紧力,但响应速度不快、可靠性不高,比国外还有很大的差距,有待进一步研制开发。
3.5中间驱动技术
随着我国高产高效矿井的出现,煤矿井下用的带式输送机已向大型化方向发展,但由于受到送带强度与驱动装置的限制,井下使用的带式输送机单机长度还不允许无限制地加长。中间驱动就是把驱动功率的一部分放在输送机的中间段,使驱动功率分散开来,这样可以降低输送带的最大张力,降低输送带强度,提高输送机的输送能力,降低整机成本。它可以在不提高输送带强度等级前提下,最大限度地增加单机长度:使单元驱动装置小型化,通用性强。单元驱动装置的功率保持在一个较为经济合理的范围内,最大限度地降低输送机的投资费用,据有关资料介绍:当采用两台中间驱动装置时,承载带最大张力可减少1/2左右,当采用十台中间驱动装置时大约减少3/4,约可降低费用15%左右。
中间驱动有二种方式:直线摩擦式与滚筒卸载式。直线摩擦式对带速同步要求比卸载滚筒式低,主要是子带与母带可以相互滑动。但投资费用要高,主要是增加了一条子带输送机的费用。一般来说,这二种中间驱动方式都可用于固定式带式输送机,可伸缩带式输送机机尾需随着工作面推进而要求机身延长或缩短,装拆子带输送机工作量大,影响工作面的推进速度,因而可伸缩带式输送机的中间驱动大多是采用滚筒卸载式。在煤矿井下采用中间驱动技术更能显示其优越性,由于单元驱动装置小型化,不仅搬运、安装方便、而且还可减少安装空间,使巷道的拓宽量大为减少,因此,在井下长距离带式输送机上应大力推广使用中间驱动技术。为了减少承载带的附加张力,所有驱动装置电动机的功率应该相等,机械特性应该相同。中间驱动的关键技术是驱动装置的负荷分配及各驱动装置的启动顺序和时间间隔,中间驱动点数量越多,这种要求就越高。目前国内外多数是采用液力调速装置来解决这个技术关键的。
3.6高速托辊技术
托辊是带式输送机的主要部件,量大面广,重量约占整机的1/3,价格约占整机的1/5,-1/3。据现场调查,煤矿井下托辊的使用寿命一般在180:-240天,在顺槽中使用的托辊,一般采完一个工作面后,托辊损坏数量约为60%:-80%,经济损失相当严重。另外托辊的旋转阻力及输送机运行阻力大,功率消耗也很大。煤带式输送机的停机事故,绝大多数是由托辊因素造成的。因此,提高托辊质量对降低能耗、节省费用、增加运行可靠性具有很大的意义。
托辊的使用寿命主要取决于轴承和密封的性能,如果托辊具有良好的密封性能(如采用组合密封),托辊使用寿命实际上就是轴承的使用寿命。轴承不仅对托辊使用寿命有重大影响,而且对托辊旋转阻力也有一定的影响。测试结果表明:轴承摩擦阻力约占托辊旋转阻力的1/4,-1/8,托辊常用轴承为204、205系列滚动轴承。通过对国内外轴承进行分析研究,认为国产轴承在尺寸精度和材料热处理等方面,与英国,西德等国基本相同,但英国道梯公司由于采用415705专用轴承,而使其寿命比普通204轴承提高10倍以上,旋转阻力降低1倍以上。
针对托辊轴承存在的问题,国内研制开发了KA系列托辊专用轴承,在结构上作了改进。试验结果表明:即使在非常恶劣的条件下运转,专用轴承的实验室寿命可以达到204轴承的10倍以上,而旋转阻力低一倍以上。但其运行阻力还是较大,使用寿命仅有20000小时左右,带速一般也不能超过4.5m/s。
高速托辊在密封结构、加工质量、轴承、润滑脂等方面有更高的要求,而国外如美国、澳大利亚等均使用了新型注油托辊,其运行阻力小,轴承采用稀油润滑,托辊寿命可达10年以上,托辊速度高达6~8 m/s。我们应该通过改进密封结构与材质,采用非金属保持架的大游隙专用轴承与专用润滑脂来提高高速托辊的质量。目前,国内外托辊质量存在差距的另一个主要原因是加工质量,国内托辊生产厂家的加工工艺与设备精度保证不了设计要求,造成托辊旋转阻力增大、甚至不能转动,使用寿命短、甚至用不到1~2个月就损坏了。只有改进托辊的加工工艺和更新设备,才能制造出高质量的高速托辊,才能满足大型带式输送机高带速的要求。对托辊进行质量分析,在现有煤矿条件下,若把托辊的使用寿命从原来的一年左右提高到五年以上,则每年托辊损坏的数量可减少五分之四,其经济效益是非常显著的。
3.7电控与监测自动化技术
为了实现输送机可控启(制)动、中间驱动、功率平衡、带速同步、自动张紧与机尾自移以及各种保护装置、通信与信号联络等综合功能的要求,国外大型带式输送机都已采用高档PLC可编程序控制器,开发了先进的程序软件与综合电源继电器控制技术以及数据采集、处理、存储、传输,故障诊断与查寻等完整的自动监控系统。该系统除了自动监控输送机的可控启(制)动、带速同步与功率平衡等外,还对各种保护与安全装置、输送带张力、传动滚筒与托辊轴承温度、输送带接头强度、输送量计量等实行监测。在电控与自动监测技术方面,国内外的差距更大,国内煤矿用带式输送机仅采用了中档PLC可编程序控制器来控制输送机的启动、正常运行、停机等整个工作过程,虽能与可控启(制)动装置配合使用达到可控启(制)动、带速同步、功率平衡等功能,但没有自动监控装置、没有故障诊断与查寻。另外,安全保护装置性能不理想与品种少,也没有人员呼救的功能。由于这些差距造成了国产带式输送机运行性能与工作可靠性差,故障多,因此,电控与监测自动化技术是国产带式输送机技术水平提高的一个迫切需要解决的关键技术。
3.8 CST的国产化技术
在各种可控起动中,CST的性能无疑是最好的,但进口价格很贵,订货周期长,备品备件供应困难,迫切需要国产化。国内已大量应用调速型液力偶合器来实现单台电机功率在500kw以下的带式输送机的软起动和功率平衡,但单台电机功率超过500kw以上时,由于调速型偶合器的散热设备较大,无法在间狭窄的顺槽可伸缩输送机上使用,特别是随着煤矿5公里以上长距离、高带速输送机的出现,由于调速型偶合器的调速范围在0.30~0.97之间,所以无法解决验带问题。01年8月国家科技部将此课题下达给了上海分院,课题名称为:动态软起动装置,要求04年上半年完成该项目,主参数为:功率N-500kW,速比I=30~40,调速范围:0.1~1.0。
4、结论
国内外高产高效矿井的原煤运输系统,基本上都是采用带式输送机作连续运输,且输送机的主参数正在向大型化与自动化方向发展。以刚体动力学为基础的带式输送机的一套常规的标准设计,己不适用大型带式输送机的设计。大型带式输送机主参数要比一般带式输送机大得多以及煤矿井下运输的某些特殊工况要求,使得上述的关键技术显得尤为突出,但往往某些关键技术在国内还不被人们所重视。当今国内外带式输送机技术发展迅速,其中某些技术如带式输送机动态设计与分析技术己进入当今世界高新技术领域,但在国内刚起步,还没有真正应用到设计中去,因而国内外大型带式输送机技术水平存有一个不小的差距。只有采用新技术,大力开展输送机关键技术的研究,尽快攻克这些关键技术,才能使我国煤矿井下用大型带式输送机设计水平、运转性能与可靠性有一个质的飞跃,真正满足煤矿高产高效的要求。