LB13A薄片生产线属辊压法制烟草薄片设备,产量200 kg/h。生产线中的粉碎机与旋风落料器、除尘器及风机等设备组成粉碎系统。粉碎系统将烟末、梗签、辅料CMC粉碎成一定粒度的粉料,通过旋风落料器、滤尘器等,将符合要求的粉料收集并集中供到粉料储料罐。
粉碎机在高速运行过程中,叶轮轴轴承工作环境不平稳,易产生震动,发出很大噪音,进而加剧磨损而损坏设备。粉碎机传动总成在两班制生产中,平均维修周期少于3个月,维修频率较高,对持续高效的生产造成不利影响。为了解决以上问题,需要对粉碎机传动总成进行改进。
1、薄片粉碎机的概述
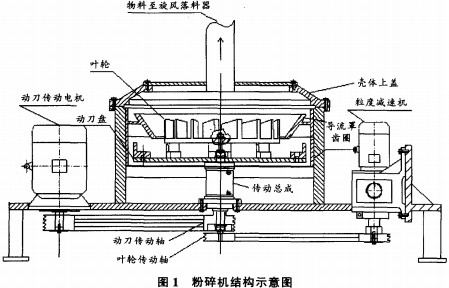
该公司薄片粉碎机为气流蜗旋粉碎机,主要由壳体、传动总成、动刀、动刀盘、齿圈、粒度减速机、动刀传动电机等组成(图1)。进入粉碎机的物料在旋转风力的作用下,在高速旋转的动刀和齿圈之间进行碰撞,从而使物料产生碎裂,形成更加细小的颗粒。由于离心力的作用,碎裂不完全颗粒在壳体内外圈部分继续碰撞粉碎,而细小的颗粒则通过旋转的叶轮,进入到风管到达旋风落料器,成为下道工序的原料。叶轮旋转的主要作用就是产生旋转风,分选物料颗粒。通过调节粒度减速机控制叶轮的转速,控制旋转风力,从而达到分选物料颗粒的效果。
2、粉碎机传动总成存在的问题
LB13A薄片粉碎机传动总成在运转过程中,叶轮轴轴承易磨损,进而产生较大震动和噪音,直至损坏。粉碎机传动总成由于叶轮轴轴承的损坏而无法运转,故障周期难以控制,维修更换传动总成过程费时费力,备件需求数量大,最主要的是对生产造成不利影响。
2.1粉碎机传动总成的结构与原理
LB13A薄片粉碎机传动总成主要由动刀传动轴、叶轮传动轴、壳体、轴承等组成(图2)。动刀传动轴为空心套结构,叶轮轴通过轴承固定在动刀轴的内壁上,两者的旋向相同(图3)。动刀电机和粒度减速机分别安装在粉碎机机架两侧,但水平位置不相同,通过三角带传输给同轴心安装的2个皮带轮。动刀电机带动动刀轴和动刀盘高速旋转;粒度减速机(无极调速减速机)通过叶轮轴带动叶轮旋转。
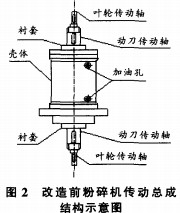
2.2故障原因分析
由于叶轮传动轴轴承安装在动刀传动轴的空心内壁上,动刀传动轴转速和叶轮传动轴之间有很大的转速差,叶轮轴的相对转速高于2 000 r/min;而且动刀轴在运转时的震动会直接传导在叶轮轴轴承上,使叶轮轴轴承工作环境恶劣。另外,叶轮轴轴承为6003,叶轮轴直径较细,对载荷、震动和转速承受的承受能力相对较弱。
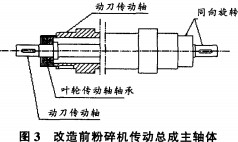
3、改进方案和措施
由于粉碎机的叶轮轴承使用寿命较短,工作性能不稳定,易造成叶轮传动轴损坏,最终容易导致总成整体出现故障,需要频繁地更换、维修,故确定改进方案,制订具体的实施措施。
3.1传动总成的改进
由于分析粉碎机传动总成的主要问题出现在叶轮传动轴上,所以从2个传动轴的结构人手加以改造。首先分离2个传动轴,把叶轮轴从动刀轴中分离出来,动刀轴改为实心轴,外型尺寸、安装位置和传动方式不变。
3.2粉碎机壳体上盖的改进
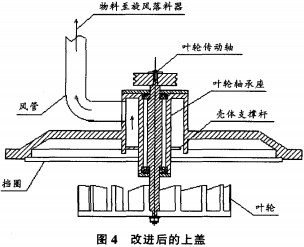
把剥离出来的叶轮轴更换安装位置,将叶轮轴安装在壳体的上盖上面(图4)。原来的上盖中心开口处与风管相连,因为改进后要把叶轮轴安装在上盖中心,所以上盖的结构也要进行相应地改造。在上盖中心圆孔处加装叶轮轴承壳体,外部加装导流罩,导流罩侧面开孔与风管相连,使物料从粉碎机内通过叶轮叶片、上盖开孔辐射壳体支撑杆空隙、导流罩、风管进入到旋风落料器。
3.3叶轮轴的改进
经过上述改造,叶轮轴安装在上盖上部,重新设计叶轮传动轴尺寸。在设计过程中为了提高轴承的有效载荷和使用寿命,适量增大了叶轮传动轴尺寸,改变了原轴承型号。在不影响物料顺利通过上盖腔体的情况下,叶轮传动轴直径40~50 mm,轴承采用6209。另外,传动轴上皮带轮孔的尺寸和叶轮轴孔的尺寸相应地进行了改变。
3.4粒度减速机安装位置的改变
由于叶轮传动轴的位置发生了改变,传动皮带轮移动到上盖的顶端,所以粒度减速机的安装位置也随之旋转180°,并根据叶轮轴皮带轮的位置做出相应调整,两者水平相等。
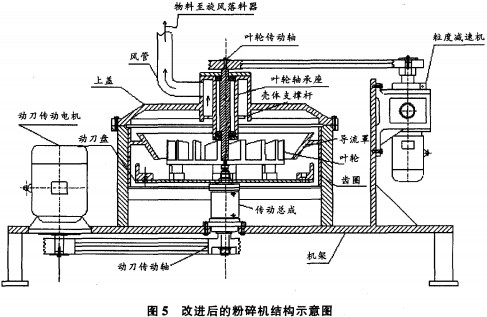
4、改进效果
改进后的粉碎机结构比较科学、合理(图5)。通过对动刀轴和叶轮轴的分离,简化了LB13A薄片粉碎机传动总成的结构,提高了部件使用的可靠性能。在故障出现的时候,没有必要同时更换所有轴承,可以根据具体情况分别更换动刀轴轴承或者叶轮轴轴承,从而减轻维修的工作量,方便维修工作,减少维修时间,降低维修成本,起到良好的经济效益(表1)。
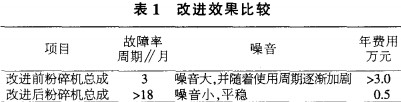
5、小结
通过对粉碎机传动部分的综合改进,提高了设备的质保能力和经济效益。在实际生产过程中,改进后的粉碎机使用效果良好,有效延长了粉碎机总成使用周期,明显减少了设备故障影响生产的因素:降低了噪音的污染,改善了工作环境。