流化床是一种洁净高效煤燃烧技术,近十几年来在世界主要工业发达国家和我国得到迅速发展。用流化床燃烧技术改造电厂煤粉锅炉,减少污染、延长服役期己形成流化床燃烧技术发展方向之一。原有小型煤粉锅炉均没有配烟气脱硫脱硝装置,S02、NOx排放严重超标。对这些旧锅炉增加烟气处理装置不如将其改造为循环流化床锅炉经济。用流化床技术改造现有电厂的煤粉炉,能使电厂服务期延长25年,与新建带有烟气脱硫装置的煤粉锅炉和循环流化床锅炉相比其改造费用只有它们的1/4左右。
煤粉炉改造为循环流化床锅炉,整体布置上的差异是技术难点之一。煤粉炉多采用“兀”形布置,结构紧凑,钢架之间空间小。循环流化床锅炉运行特性决定其必须配备高效的气固分离装置,气固分离装置的结构决定着循环流化床锅炉的整体布置。圆形旋风分离循环流化床由于其分离器的圆形结构无法实现锅炉整体的紧凑布置,在应用于“n”型布置的煤粉炉改造时,原有钢支架及尾部烟道都要改变,改造投资大。水冷异型分离循环流化床锅炉采用方形分离器,锅炉结构紧凑,占地面积小,能够实现锅炉的“兀”型布置。因此在对煤粉炉改造时,对原有的钢结构改变较小,分离器与炉膛之间不需要膨胀节及密封,改造投资比采用圆形旋风分离循环流化床锅炉减少30%左右。
河曲二电厂使用原北京锅炉厂65 t/h煤粉炉3台,拟先将其中一台改造为循环流化床锅炉,改造后要求锅炉蒸发量达到70 t/h,蒸汽压力及蒸汽温度维持3.82 MPa、450℃不变。太原锅炉集团有限公司根据河曲二电厂锅炉房及锅炉本体状况,并结合当地燃料情况,在满足用户对锅炉改造要求的前提下,综合考虑各种经济、技术因素,采用清华大学水冷异型分离型式的循环流化床锅炉(CFBB)方案对65 t/h煤粉炉进行了改造。
1、65 t/h煤粉锅炉改造方案
1.1改造的总体构思
保持原锅炉厂房不动,充分利用原锅炉顶部至房项横梁之间的空间,将炉膛加高3m,以保证循环流化床锅炉物料循环的需要。炉膛加高后的结构型式及受热面布置及水冷分离器带来的受热面的增加,可使锅炉出力达到D=70 t/h,蒸汽压力P=3.82 MPa,蒸汽温度t=450℃。改造后锅炉采用单锅筒横置式自然循环、异型水冷分离器、膜式壁炉膛、前吊后支、全钢架“兀”形结构型式。保持原前部4根立柱位置不动,拆除尾部的4根立柱及全部横梁,在与22柱距离3m处重新构筑两根立柱,立柱截面尺寸与原立柱相同。接长原立柱,将顶部框架整体上移3m,同时将锅筒亦相应抬高3m。将原过热器系统中的集汽集箱、自制冷凝器、喷水减温器、部分管道、仪表、阀门及平台扶梯重新利用。设置全新炉膛、分离器、过热器、省煤器、空预器、燃烧设备、护板、炉墙、密封装置等。重新配置相应的辅机;如一次风机、二次风机、引风机、给煤机等。见图1。
1.2改造后锅炉的结构特点
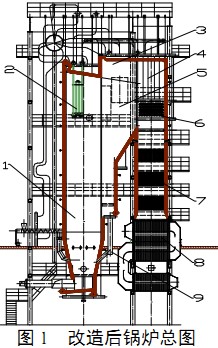
1炉膛2.高温过热器3.分离器出口烟道4.包墙管5水冷异型分离器6.低温过热器7.省煤器8.空气预热器9.回料阀
(1)米用全膜式壁结构
锅炉从水冷风室至尾部过热器烟道包墙采用了全膜式壁结构,因此锅炉的膨胀、密封得到了很好的解决。前墙水冷壁向后弯曲构成水冷布风板,与两侧墙组成水冷风室,为床下点火创造了必要的条件。
(2)米用“水冷异型分离器”
该炉布置了两个“水冷异型分离器”,该分离器由膜式水冷壁加高温防磨内衬构成。分离器与炉膛组成一个整体,既解决了膨胀密封问题,又保留了原锅炉“兀”型布置的优点,同时相应增大了锅炉的受热面积。弥补了由于锅炉房高度对炉膛高度的限制带来的炉内受热面较少的不足。
(3)过热器的布置
循环流化床锅炉负荷降低时,风量减小,炉膛上部空间风速降低,从密相区扬析和夹带的物料量也随之减少,炉膛上部空间物料浓度降低,放热份额也相应减小。风量减少同时也带来了锅炉尾部烟道烟速降低,尾部受热面对流换热系数减小。改造后将高温过热器布置在炉膛顶部,低温过热器布置在尾部烟道(见图1)。这一布置特点,使过热器吸热量随锅炉负荷变化有很强的自适应性,使得锅炉负荷大范围变动时蒸汽参数保持稳定。高温过热器布置在炉膛项部靠近前墙附近,由于烟气在炉膛后墙出口处转弯离开炉膛,因此高温过热器处烟速及固体物料浓度均较低,不会对高温过热器产生磨损。运行实践也充分证明了这一点。
(4)床下点火
由于采用了水冷风室及水冷布风板,为床下点火创造了条件,本次设计采用床下热烟气发生器点火,点火用油在热烟气发生器内筒燃烧,产生高温烟气,与夹套内的冷却风充分混合成850℃左右的热烟气。通过布风板使床料在沸腾状态下加热,因此该点火方式具有热量充分交换、油耗低、点火劳动强度低、成功率高等特点。
(5)可靠的回灰系统
该炉采用小风量、低压头、高流率的自平衡回灰系统。回灰松动风采用一次风,省去了专设的高压松动风机,系统简单,运行操作方便,安全可靠。
(6)固定膨胀中心,确保锅炉安全
该炉采用刚性平台分上、下两层固定膨胀中心,使锅炉按预定方向膨胀,利于密封,同时由于锅炉炉膛高、宽比很大,固定膨胀中心后,可以避免炉体晃动,产生安全事故。
(7)有效的防磨措施
循环流化床锅炉的磨损是影响锅炉连续经济运行的重要因素之一,在炉膛燃烧室,“水冷异型分离器”内以及分离器出口区等膜式壁部分采用焊密集销钉加特殊的高温耐磨可塑料进行防磨处理,对流受热面采用降低烟速、加防磨盖板等有效措施,对穿墙管等处和某些局部均采取特殊防磨措施。同时在炉膛燃烧室的耐磨可塑料与水冷壁交界处,焊有防磨鳍片,以破坏涡流。
2、改造后的运行情况
改造设计燃料与改造前相同,低位发热量为21.6704MJ/kg,燃料的干燥基成分见表1,入炉煤粒径分布见图2。入炉煤为0~20 mm的宽筛分燃料,细颗粒较多,质量平均粒径为342μm。
改造后锅炉满负荷试运行,主蒸汽流量为71.4 t/h,主蒸汽压力为3.78 MPa,主蒸汽温度为448,达到了预期的目的。见表2。
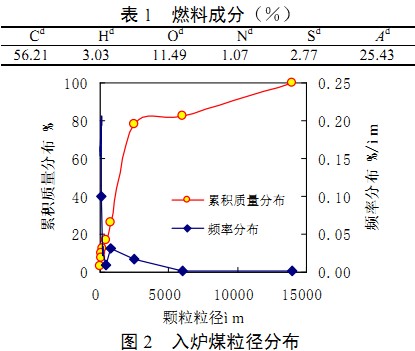
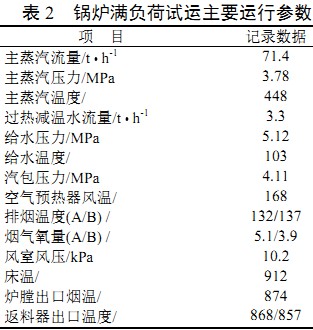
炉膛受热面布置合理,物料循环系统畅通。水冷分离器吸热使回料温度降低,温降为21℃,满足回料平衡床温的需要,使床层温度在满负荷下平衡在912℃,该床温比较合理。
锅炉在满足预期改造目的的同时,各项参数均在合理范围之内。排烟温度较低,为135℃。锅炉密封性能好,排烟含氧量为4%,体现了锅炉的高效运行。
为进一步了解改造后锅炉运行性能,对本改造后的循环流化床锅炉及燃用相同燃料同容量的圆形旋风分离循环流化床锅炉的飞灰、底渣进行取样分析。将样品进行筛分,筛分段内的平均直径为
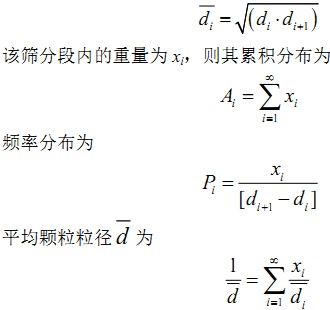
飞灰从除尘器下取样获得,飞灰颗粒频率分布及各筛分段的分级含碳量见图3。由于改造后锅炉与同容量圆形分离循环流化床锅炉燃用燃料相同,粒径分布相同,因此,正常运行情况下,飞灰的粒径分布反映分离器的分离效率,飞灰含碳量在某种程度上反映锅炉的燃烧效率。改造后锅炉飞灰的平均粒径为53μm,平均含碳量为5.5%;同容量圆形旋风分离锅炉飞灰平均粒径为68μm,平均含碳量为8.6%。表明水冷异型分离器分离效率较高,与同当量直径的圆形旋风分离器相当。改造后锅炉的燃烧效率比同容量圆形分离循环流化床锅炉的燃烧效率高。
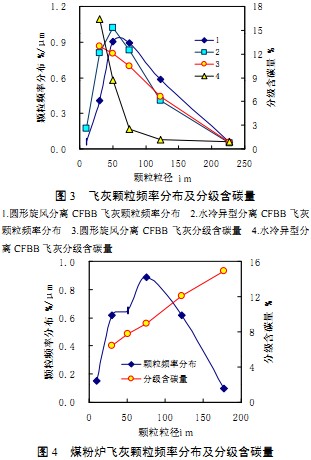
对原煤粉炉的飞灰进行取样分析,其颗粒频率分布见图4,飞灰平均粒径为59μm,平均含碳量为9.6%,比改造后锅炉的飞灰平均含碳量高。由于煤粉炉飞灰份额比循环流化床锅炉高,因此改造后锅炉燃烧效率比改造前有所提高。
正常运行情况下,循环流化床锅炉依靠排渣来维持合理的床料量,排渣口设在炉膛底部布风板处。正常流化情况下.床料分层,大颗粒在底部经排渣管排出炉外,称为底渣。改造后锅炉底渣平均粒径844μm,含碳量3.65%:相同容量的圆形旋风分离循环流化床锅炉底渣平均粒径739μm,含碳量3%,见图5。二者粒径分布相似,含碳量接近。
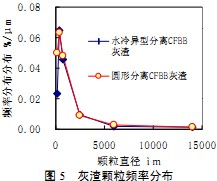
以上对比分析可知,改造后锅炉的物料循环系统工作正常,炉内气流组织合理,燃烧效率比原煤粉炉有所提高。
3、总结
保持原锅炉厂房不动,在原有钢架范围内,将65 t/h煤粉炉改造为“水冷异型分离”CFB锅炉。改造后锅炉布置紧凑,保持了原有的“兀”型布置,并将锅炉的出力提高到70 t/h。运行实践表明,各项参数均达到预期值,改造后锅炉运行性能优越,燃烧效率比改造前有所提高。该改造非常成功,其改造经验可为同类型锅炉改造借鉴。