某电厂有2台220 t/h锅炉,1997年投产使用,型号为DG220/9. 8-8单汽包自然循环、倒U型布置锅炉,设计燃料以煤粉为主,点火方式为三级点火,点火器液化气渣油煤粉,炉膛四角切向布置燃烧器,气流在炉膛中心形成直径为D= 561mm的假想切圆(某年曾对燃烧器改造,目前假想切圆直径D- 600 mm)。2010年某月,该炉连续两次发生水冷壁管泄漏和爆管事故,发生部位均为燃烧器上方,停炉后,检查发现炉膛水冷壁四周有不同程度的腐蚀现象。为确保锅炉长周期安全运行,对爆管和腐蚀产生的原因进行了分析。
1、水冷壁爆管的原因分析
从拆除下来的水冷壁管宏观观察,管肇内部有深浅不一的坑,初步判断这些坑可能是由酸碱腐蚀或是电化学腐蚀等原因造成的,将爆管处水冷壁外垢样及锅炉给水水样送往专业机构分析化验,分析结果见表1。
从表1中可以看出,其腐蚀垢样的主要成分是Fe2 03、S03等,具有高铁、高硫特点,属于水冷壁管发生高温腐蚀的基本特征,在电厂(包括自备电站)中最常见的腐蚀方式为:硫化物( FeS2、H2S)型腐蚀、焦硫酸盐型腐蚀和氯化物型腐蚀,通常水冷壁管发生高温腐蚀的区域多在燃烧高温区,即局部热负荷较高,管壁温度也较高的区域,如燃烧器区附近,其余区域的高温腐蚀明显减弱或根本不发生高温腐蚀;发生高温腐蚀的管子向火侧正面的腐蚀速度加快,造成管壁减薄,背火侧则不易发生高温腐蚀。
三门峡富通新能源销售生物质锅炉主要燃烧木屑颗粒机压制的生物质颗粒燃料,如下图所示:
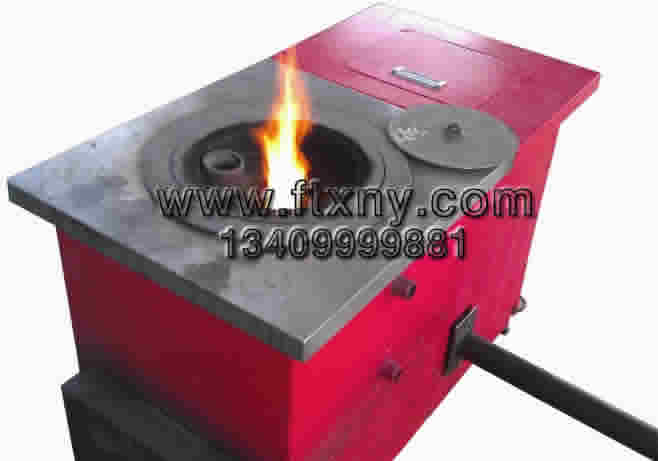
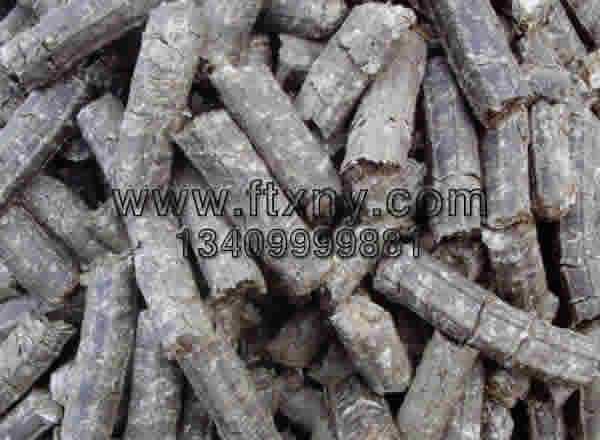
1.1燃烧煤种含硫量较高的分析
该电厂2010年某季度原煤煤样中含硫化验平均统计与锅炉设计煤种w(S)=0.36%相比较,燃用煤种的实际含硫量偏高,个别来煤中硫质量分数大于1%,根据含硫量测定及锅炉实际运行情况的实验研究可以判断,实际燃煤含硫量高,是锅炉受热面产牛高温腐蚀的一个因素。
1.2燃烧器动力场实验的分析
某电力科学研究院对1*炉进行空气动力场实验,测量过程中发现入炉最近的2#、3#角的两个一次风管风速高,最远的两个1#、4#角的一次风管风速低,风速不均也促成局部偏烧现象。另外该锅炉使用的一次风门调节手段较落后,该电力科学研究院建议将一次风门的固定齿由原来的12齿粗调变为24齿细调,尽量使风门实现微调,以免影响一次风压。
通过测量发现,二次风风速较小,二次风率下降,对煤粉的辅助燃烧能力变差,造成火焰中心卜移,后部烟道有积灰,飞灰可燃物含量变大,效率下降,使得煤粉在缺氧状态下燃烧,再射流下游形成局部还原性气氛。当未完全燃烧的煤粉气流冲刷高温区水冷壁管时,会导致水冷壁管高温腐蚀,并最终发生爆管。
1.3锅炉水源水质分析
该电厂锅炉补给水主要来自化学水处理二级脱盐水、汽轮机凝结水、化工装置来的凝结水等混合后送往锅炉。这些水首先经热力除氧器除氧,再通过汽机加热器加热送入锅炉。该电厂锅炉给水化验与监督是采用手工定时不连续方式进行,因此,存在一定的盲区,可能有一部分杂质不可避免地被带入给水,然后进入锅炉。爆管后,该电厂将该水质送往专业机构分析,水质分析结果见表2。
从表2可以看出:化学水处理脱盐水指标能控制在国家标准的规定范围内,但化上装置凝液中存在的杂质进入锅炉,造成炉水品质恶化。水中溶解的杂质(盐类)形成水垢,造成管壁热阻增大,传热效果不好,管材长期超温运行导致爆管。再加上干净的锅炉蒸发面金属容易离子化,即Fe- 2e—Fez+,使锅炉表面带负电荷,而一些结垢物质常常带正电荷,这样由于静电吸引作用,使结垢物质沉积在金属表面而生成水垢,致使局部管壁过热,导致发生爆管事故。
由于锅炉炉水水质超标(尤其以甲酸、乙酸为主),对锅炉内表面进行腐蚀。锅炉水质Cl-超标,导致水冷壁部发生氯化物腐蚀,水冷壁管变薄,如果长时间Cl-超标极易发生爆漏导致水冷壁爆管。为此需要对现有水冷壁进行全面、认真检查,凡是管壁胀粗超标的或表面有裂纹的,应全部给予更换。
1.4静态场的问题分析
该锅炉设计的煤种是二类烟煤,实际燃烧煤种介于一类与二类之间,不易着火,改造之后的燃烧器炉内假想切圆变大,运行时制粉系统风速很高,38、48角还有点偏,导致形成的切圆变形更大,喷燃器出口边缘靠近水冷壁处燃烧程度变强,并且灰份冲刷水冷壁能力增强,使得水冷壁管外表面出现很多小麻点。测试结果:喷燃器背火侧风速高,向火侧风速低,而向火侧煤粉浓度高,引起偏烧,从而对水冷壁的烤灼能力增强,尤以48角为重。对切圆燃烧锅炉,当燃烧切圆直径过大、火焰中心未形成切圆或燃烧切圆偏移时,致使炉内空气动力场倾斜,燃烧器区域出现火焰冲墙和还原性气氛,从而发生高温腐蚀,最终导致爆管事故发生。
1.5高压加热器停运问题分析
不使用高压加热器,给水温度低,省煤器温度低,相同负荷下需要锅炉增加部分燃煤量,弥补省煤器、水冷壁热量不足,受热面的吸热量要增大,相当于锅炉出力增加。
1.6操作人员未按规范进行操作分析
锅炉水中呈悬浮物状态的盐类有些具有很强的黏性,如Mg3 (P04)2和Mg(()H)2等。由于锅炉运行时化学监督人员对炉水是人工间接性分析与加药,没有在线分析自动加药仪表设备,存在分析和加药盲区;锅炉运行人员定期排污不规范,为了节能节水,连排阀门开度过小、致使炉水悬浮状态的盐类增多,浓度增大,从而很容易粘附在锅炉热负荷较高的受热面上,经过高温烘熔后,进行局部反应,使沉淀物形态发生变化,转变为水垢(即从泥垢转化为水垢),堵塞水冷壁排污管和部分水冷壁下部管段,导致循环不好。
由以上原因分析可知,造成锅炉水冷壁管高温腐蚀和壁管变薄的原因,主要是水质不合格、煤中含硫量较高、燃烧切圆偏大、一二次风配比不合理,致使燃烧器周围的水冷壁管处于高温、水质恶化、水循环差、存在一定还原性气氛中运行,从而造成了严重的高温腐蚀和管壁变薄。
2、改进和预防措施
该电厂建市了一套完善的水质管理、汽水监督管理办法及实施细责。设备管理方面则要求根据实际情况,定期对水冷壁管进行割管检查,为了保证锅炉长周期安稳运行,需要从以下几方面进行调节和处理。
(1)为了有效防止喷口背火侧冲刷水冷壁的现象,建议在双通道一次风喷口内背火侧贴一块档风帖板,3*、4*角喷口背火侧壁帖板,角度与壁面夹角不超过6°,1#、2#角喷口背火侧壁也对应帖板,夹角不超过4。,这样可以保证各喷口背火侧的水冷壁的冲刷磨损现象,减小炉内该区域爆管的概率。
(2)加强对燃料的控制,可通过燃烧前和燃烧中除硫的方法,降低燃料的含硫量;同时控制适当的煤粉细度,尽可能均匀各燃烧器之间的煤粉浓度分布;
(3)加强对给水的控制,适当提高高温腐蚀区域水冷壁管内水流速度,降低管壁温度,严格控制给水品质,避免因水冷壁管内结垢而影响换热,从而导致水冷壁管壁温度增加;
(4)提高金属抗腐蚀能力,可采用在管外金属(镍、铝)热喷涂工艺,用于表面防护,降低腐蚀速度;
(5)加强燃烧凋整、合理配风,以达到降低水冷壁附近还原性气氛和避免烟气直接冲刷水冷壁两个目的;
(6)加强排污管理,严格考核,保证锅炉给水品质合格,建议每年做一次空气动力场实验。
(7)建议在高压加热器允许投运的情况下尽可能长周期投运,以保证锅炉在经济工况下安稳运行。
3、结论
水冷壁管爆管后,技术人员对锅炉实施了以上改进和预防措施,经过半年多的实际运行,目前水冷壁管无异常现象发生,各项工艺指标受控,能够为锅炉长周期安稳运行提供有力保障,对同行业电厂锅炉安稳运行具有一定的借鉴作用。