1、概述
由于高锰钢( Mn13)耐磨,冲击韧性高而广泛用于选矿球磨机衬板易损件。目前,国内外研究应用表明,在高锰钢件中添加强碳化物形成元素,使高锰钢合金化及采用弥散硬化热处理新工艺,是提高其耐磨性的有效途径。但是加入合金元素,势必增加生产成本,复杂的弥散硬化热处理工艺在大生产中也难以控制,为此,采用了在高锰钢中添加成本相对较低的铬、稀土元素,产根据生产实际情况,制定了较为简便的弥散硬化热处理新工艺,从而研制出“GML”新材料。实现了提高4#球磨机衬板的耐磨性,降低选矿成本的目标。
2、衬板新材料的研制
研制新材料确定的化学元素成分见表1。

化学成分中碳与合金元素的配比为:
(1)影响高锰钢耐磨性的主要因素是碳元素与锰元素的合理配比。碳含量低,钢经热处理后,冲击硬度低,耐磨性较差,碳量过高,热处理后晶界极易形成粗大网状碳化物,致使钢的脆性增大,耐磨性也差。如果锰元素含量高,热处理后硬度高,成本也高。如果适当降低锰含量和碳含量,使锰碳比达到8~9的最佳配比,热处理后不仅硬度提高,耐磨性也可提高。
(3)合金元素钒、钛、铬、钼、稀土等,都是强碳化物形成元素,这些元素在高锰钢中形成的特殊碳化韧是提高钢耐磨性的关键,尤其是形成弥散状的碳化物显著提高钢的耐磨性,但由于钒、钛、钼都比较贵重,所以选择了又经济又能提高耐磨性的强碳化物元素,铬和稀土首选元素。如果当钢中的合金元素含量较低时,只能形成Fe
3C普通渗碳体,所以只有在锰铬元素与碳达到一定比值(约为1.8)时才能产生弥散状的特殊碳化物(Cr
7C
2或Cr
23 C
8等),从而可显著提高钢的耐磨性。
弥散硬化热处理工艺的确定。试制的4种弥散硬化热处理工艺模拟方案见表2。
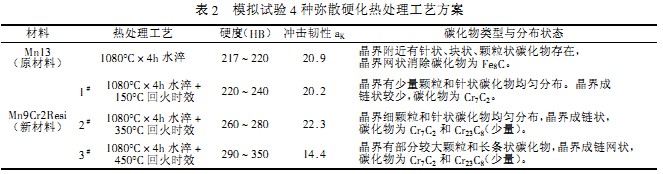
模拟试验4种处理工艺方案后,机械性能和金相组织显示:2#型热处理弥散工艺:1080℃×4h水淬后,在350℃回火时效后,其碳化物在晶界以细颗粒和细针状均匀分布,界面成链状其碳化物达到弥散分布,从机械性能方面看,硬度也较高,冲击韧性也较高,比150℃回火时效工艺有较好的强度、硬度和韧性。450℃回火量效工艺其碳化物尽管也达到弥散分布,但晶界附近出现大块链网状碳化物,这样钢的脆性变大,对耐磨性是不利的。
3、新材料衬板的试用效果
1999年7月10日前试制出83件约重16t4#球磨机通体部新材料(Mn9Cr2Resi)衬板,并于1999年7月22日安装于选矿4#球磨机,易磨损的通体进粒端,历时10.5个月生产试用,于2000年6月9日磨损失效卸机,共处理磨选原矿75.9万t,与原型衬板(Mn13)处理磨选原矿49.8万t相比,其耐磨性提高34%,每付衬板可降低选矿衬板消耗费和节约设备维简费共8.58万元,全年可创效益92.3万元。
三门峡富通新能源科技有限公司除了销售球磨机外还销售破碎机、颚式破碎机、圆锥破碎机、颗粒机等机械设备。