
烘干搅拌输送新闻动态
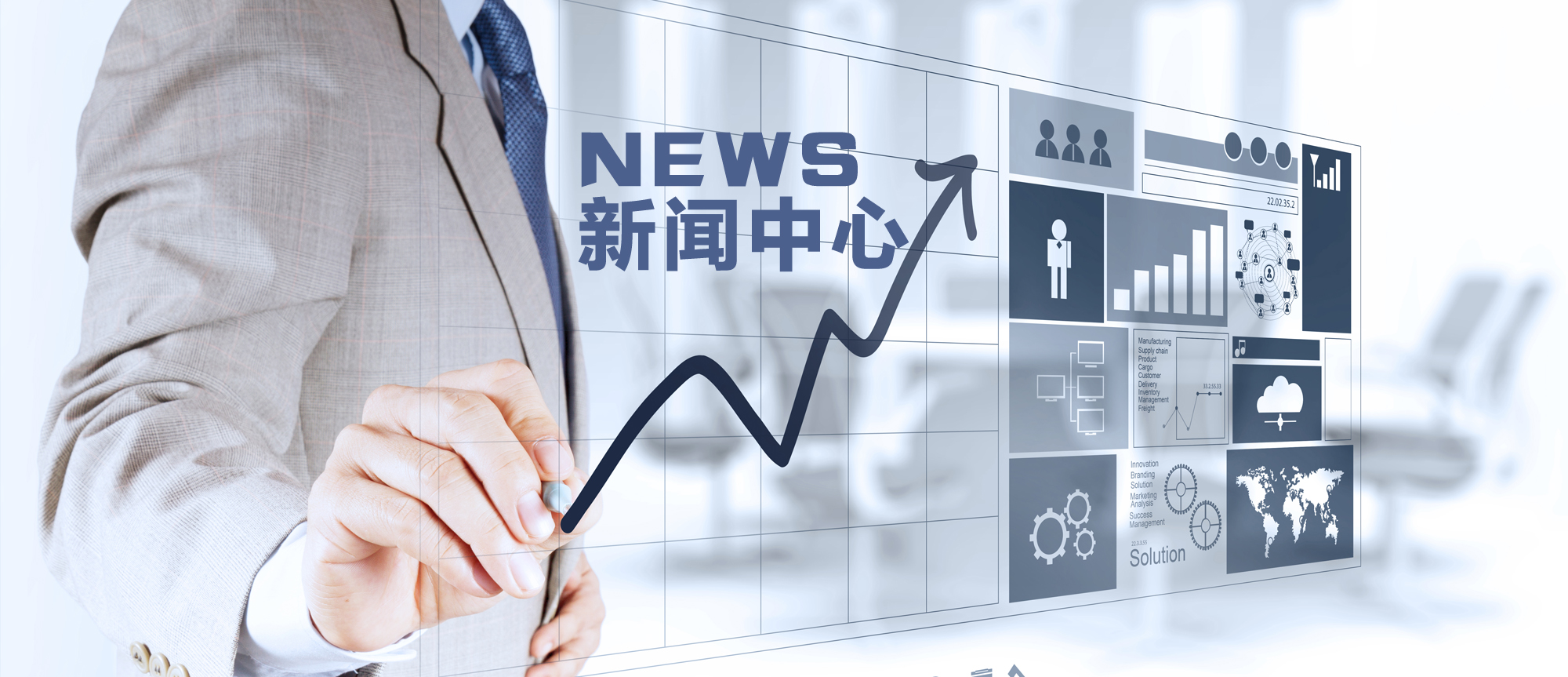
富通新能源 > 动态 > 烘干搅拌输送新闻动态 > > 详细
AUMUND链斗式提升机一次故障的分析处理
发布时间:2013-05-04 07:42 来源:未知
0、前言
江苏某公司(以下简称我公司)使用100%无烟煤的5 000 t/d熟料生产线于2004年10月28日正式点火投产,其生料制备系统采用日本UBE公司制造的分体式立磨,型号为UM50.4N,主机功率为3 600 kW.产能为磨损后390t/h (R0.0912%)。与磨机系统配套的外循环斗式提升机是由德国AUMUND公司提供,型号为BW-2900/285/5,最大输送能力为1300t/h。该提升机头部为整体式双驱动,功率2x200 kW,驱动轴上装有分嵌式无齿型链轮:内部输送系统为双链轮,双锻造输送链条,双料斗,尾轮张紧各自独立。该设备为目前国内输送能力最大和输送高度最高的链斗式提升机,本文就该设备在2005年出现大故障的原因分析和处理措施作一介绍。
1、生料粉磨系统工艺流程及AUMUND链斗式提升机主要参数
生料粉磨系统工艺流程见图1;AUMUND链斗式提升机主要参数见表1。从图1可知.UBE公司的UM50.4N立磨系统,其动态选粉机9为外置,与机分体,立磨与动态选粉机9之间通过风管相连。经立磨粉磨的半成品生料进入动态选粉机9进行筛选,合格品进入电收尘,不合格品再进入磨机进行粉磨。
2、故障现象及原因分析
2.1故障现象
2005年7月6日,因系统工艺优化不够和中控操作员经验不足等原因,发生了提升机头部链轮牙盘和输送链条严重打滑,功率波动在270—400 kW之间,最高达到435 kW且持续10 s,造成输送链条一侧被磨断,另一侧有8节被严重磨损的重大事故,直接经济损失达8万多元人民币。
2.2原因分析
2,2.1 磨机系统漏风点多,喷口环风速低,未能形成风扫立磨良好的内、外部循环效果
公司当时生产为美标Ⅲ型熟料,使用的铁质校正原料为南京钢铁联合有限公司的冶炼废渣(以下称“南钢钢渣”),化学成分见表2。生料配料中,南钢钢渣的配入比例约为4%。
经中材国际南京水泥工业设计研究院技术中心检测,南钢钢渣的铁相组分以纯铁和铁的氧化物两种形态存在,其中磨盘混合料中的纯Fe组分含量(质量分数)在4.68%左右,Fe203含量(质量分数)在7.180/0左右,即磨盘物料中含有大量的富集纯Fe。由于铁组分的体积质量为7.9 kg/m3(为一般生料的2倍以上),密实难磨,因此半成品生料中含有大量铁质小颗粒,它不断被选粉机选下,又被气体提升到选粉机,反复冲磨着磨机出口风管,使风管弯头多处磨穿漏风。
另原料进磨旋转锁风阀(图1中4)设计不合理。旋转阀板外压装橡胶板(图2中1)与壳体壁进行锁风,阀板与壳体壁间所装橡胶板宽为
127.5mm。由于橡胶板会产生塑性变形,此变形间隙极易使个别的块状物料卡在其间,长时间运行引起了阀板扭曲变形,使得进料系统漏风日益严重。
2.2.2 磨盘挡料圈高度调整不当和电机高报跳停量程设置偏高
(I)磨盘挡料圈高度调整不当。UBE公司调试人员为提高磨机产量,在2005年6月19日将挡料圈高度从122 mm调整到113 mm,想通过减少铁质原料在磨盘上的富集,降低磨盘磨辊磨损,加大循环量来提高磨机产量。中控操作员为稳定磨盘料层,将调速皮带速度从60%提高70%。该阶段提升机功率波动在300~320 kW,循环料量大于最大输送量1300 t/h,处于超负荷运行状态。
(2)电机高报跳停量程设置偏高。按AUMUND公司提供的说明书要求,当提升机达到最大输送量1300 t/h时,对应电机驱动功率为229.6 kW。而当时实际设置的高报跳停量程为435 kW,延时10 s跳停。显然,此高报跳停量程远大于设计的有效保护值。
2.2.3 其它原因
(1)试生产时期,设备连锁未能完善。提升机保护性连锁故障频繁,生料磨因提升机速度开关和料位开关等误动作经常跳停。性能测试时,将速度开关和料位开关等全部短接,未能及时恢复。链条打滑不能得到有效保护;底部料位如在高位时,料斗填充率将大于74%,循环斗提超负荷运行。
(2)原料的体积质量加大,循环负荷增加。配料中使用的铁质校正原料为南钢钢渣,这就大大提高了物料的体积质量。提升机料斗内原料设计体积质量为1.3 m3/t,而经现场测量料斗内原料体积质量高达1.9~2.0 t/m3,对应于料斗100%填充率(水平满斗),电机驱动功率增加到460.8 kW.是最大产量1300 t/h对应功率229.6 kW的2倍,循环负荷成倍增加。
(3)磨系统连锁设计不合理。图l中,磨系统外循环皮带机8和外循环提升机5是连锁启动,而调速皮带机4和磨机7之间未加连锁。当磨机振停后,循环系统有余留原料进入计料仓2,为防止计料仓2满仓(此前有过教训),在系统气路调整完成后,操作员再停调速皮带机。此间,部分原料通过调速皮带3喂人磨内,再次启动磨机时,磨内富集的原料通过外循环皮带8迅速喂入斗式提升机5内,斗式提升机负荷短时间内迅速增加。
3、故障处理
(1)更换磨损严重及断裂的链条共计16节,更换磨损严重的料斗30只。
(2)检查链条节距。按AUMUND提供的数据(表3),对其余链条进行测量。测量结果为:链条套筒外侧长度为249 mm,仅比标准长度248 mm伸长1mm,未达到需更换时的长度257.8 mm。因此,链条节距均在正常范围,无需更换。
(3)逐一检查头轮链轮牙盘与轮毂联接螺栓M24,10.9级的扭矩,均达到AUMUND要求的扭矩数据1050N-m.性能正常。同时检查尾轮滑动轴承和头轮轴承性能正常:并恢复外循环提升机速度及料位开关与斗提驱动间的联锁。
(4)对锁风阀变型部分进行校正,去掉橡胶板,用焊接钢板方式让其延伸,使之与壳体间间隙控制在5 mm。出磨风管磨损部位定期补焊Hardox板。
4、改进措施
(1)更改计量仓量程。原计量仓50t时为仓满量程,改为仓满量程为40t。进料皮带l和计量仓2之间设置连锁控制。即当计量仓2满量程时,皮带机1高报跳停。这样保证生料磨抬辊时,外循环系统的余料进入计量仓时,仓不出现溢料。
(2)生料磨抬辊和调速皮带机3之间加连锁,抬辊时调速皮带机3即刻跳停,磨内不会有多余料量。二次启动磨机时,循环系统负荷将不会增大。
(3)重新设定循环斗式提升机5的功率报警量程。当功率高报250 kW时,磨机系统设备跳停;高报230 kW时,外循环皮带机8s延时跳停调整为10s,保证斗提内物料走空。磨机本体和外循环皮带机之间加连锁。
(4)对立磨喷口环进行改造。针对此阶段磨机系统运行状态,在外循环皮带机上截取2m物料,进行测量,线质量为225 kg/m,经计算,循环率3.78(循环料量/磨机产量),外循环量偏高,磨机喷口环风速偏低,较低的风速不能有效将部分物料反吹到磨盘上重新粉磨,结果为磨机产量低,循环量大。2005年8月,在喷口环外围用10 mm厚的A3板进行了部分封盖,l#和4#辊加封的宽度为65 mm,2#和3#辊加封的宽度为110 mm,如图2。这样喷口环面积由8.06mz降为6.31 m2,面积缩小21.7%.考虑到其他工况不变和改造后喷口环压损忽略不计,喷口环风速应按线性关系增加。
5、效果
采取上述应对措施后,外循环斗提功率能稳定在250 kW左右运行,磨机系统运行状况大有改善,再未发生斗提链条打滑磨断之事。同时,在三次大修中,使用某厂家的w(Al203>56%的耐磨陶瓷料在风管内作耐磨内衬防磨,重新设计制造更换原料进磨旋转锁风阀,调整挡料圈的高度等一系列优化改造后,磨机系统漏风得到有效根治,系统操作参数稳定合理,外循环斗提运行功率降至160 kW。这就有效减少了斗式提升机出现故障的概率,也减少了链条的磨损,提高了系统设备的运转率。