
颗粒机配件新闻动态
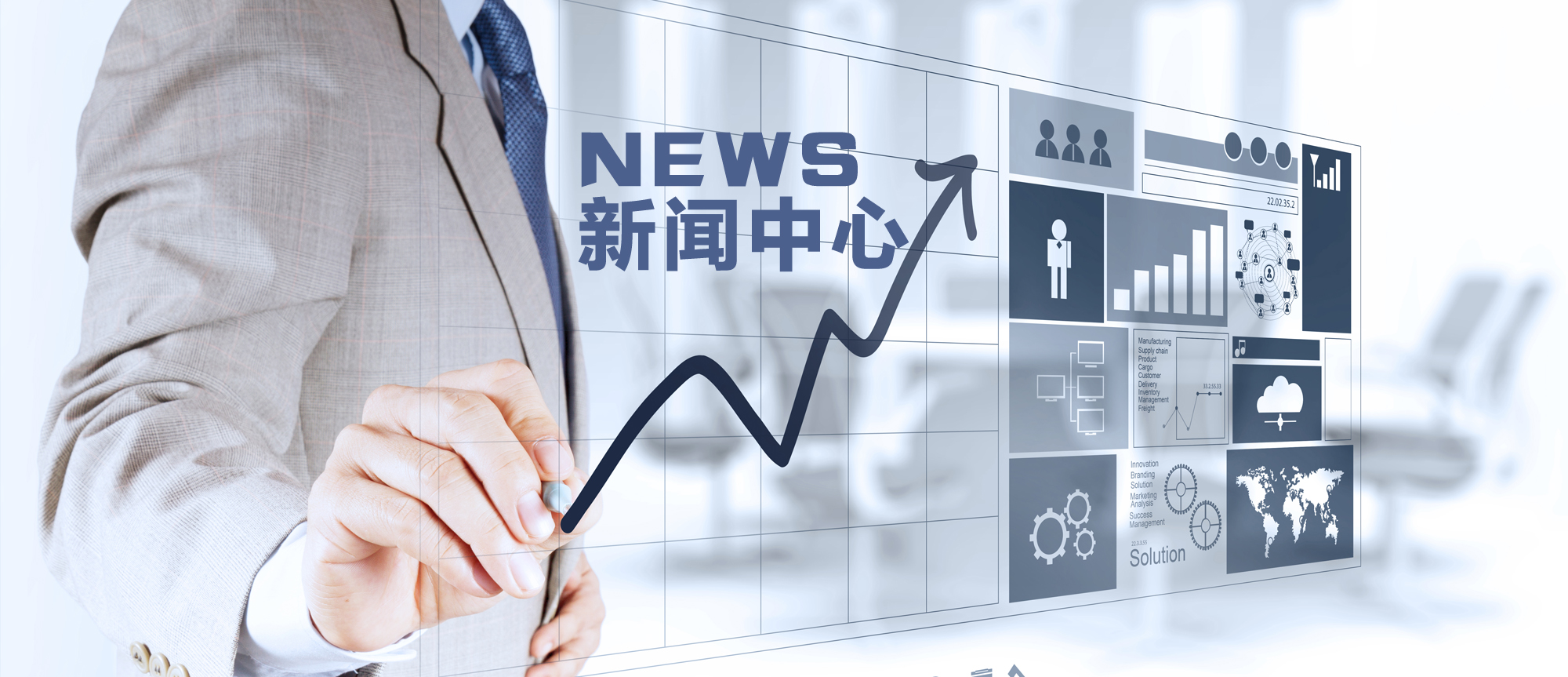
富通新能源 > 动态 > 颗粒机配件新闻动态 > > 详细
Ø1830mm×6400mm球磨机的故障分析与技改措施
发布时间:2013-05-18 08:43 来源:未知
本公司60 kt/a磷酸二铵生产装置采用湿法磷酸生产工艺,萃取磷酸所用矿浆由2台∮l830 mm×6 400 mm球磨机提供。该机于1990年初投入使用。2台球磨机均采用橡胶衬里,湿法磨矿,故具有噪音小,粉尘少(或无粉尘),节能并能长周期连续运转,较好地满足了磷酸生产的需要。
但该机在长期运行过程中,仍发生过许多设备问题,如大齿固密封漏油,隔仓板断裂等,严重影响了球磨机的安全经济运行。从1990年10月至今,笔者根据球磨机多年运行的情况并结合实践经验,认真分析球磨机的故障后采用“四新技术”进行处理,收到了良好的效果。
1、主要故障原因分析殛处理措施
1.1大齿圈密封漏油
大齿圈靠齿轮自身带油润滑,在大齿圈罩底槽内盛有齿轮油并保持一定高度。大齿圈端面与齿圈罩之间用厚10mm的羊毛毡密封,防止了较大颗粒异物或灰尘进入润滑油中,但无法避免润滑油飞溅而发生的漏油现象。当大齿圈将齿轮油带到顶部,润滑油就会顺着犬齿圈流下,由于齿轮罩本身制作得较小,无法收集到从简体上,大齿圈表面落下的润滑油,致使大量润滑油流到了地面上。
齿轮油不断流失,造成了很多不良后果:一是污柒环境;二是地面油腻光滑,危胁操作工的人身安全;三是设备润滑不良或缺油,造成齿轮千磨;四是需不断补充新油,导致球磨机的运行费用升高;五是阻碍了企业设备管理的升级,增加了设备现场管理的难度。
富通新能源销售球磨机、雷蒙磨分级等磨机设备。
处理措施:
1 992年10月,大齿圈改用二硫化钼脂润滑,解决了齿轮的润滑问题,消除了泄漏现象。具体实施办法是:拆掉大齿圈罩上半部分,将齿轮表面清理后全部涂上二硫化钼脂,安装好齿圈罩,设备运转后,每隔0.5~1h从加油孔加入二硫化钼1~2 kg,一段时间后,润滑月旨就会充满齿轮罩。以后,加油的频率逐步下降,最后达到数月加油1次。
采用二硫化钼脂润滑有如下特点:
(1) 因采用闭式传动,飞溅到罩顶和壁部的润滑脂积累到一定程度,又重新滴落在齿轮表面上,可进行二次润滑,这样周而复始,保证了齿轮副一直处于良好的润滑状态。
(2)增大了齿轮表面润滑膜的厚度,提高了润滑效果,且齿轮的传动噪音和振动有明显降低。
(3)密封容易,无泄漏,润滑脂不受污染,不易变质,使用周期长。
1.2筒体端盖螺拴断裂
球磨机中空轴与端盖的连接是保证球磨机两轴同心度的重要环节。原设计的筒体端盖不仅有包容中空轴法兰并使其定位的止U,而且24条端盖连接螺栓(规格:M 36×1 60,材质35 CrMo)均采用铰孔螺栓。从1 999年10月起,该连接螺栓经常发生断裂现象,更换新螺栓后,每年至少仍有5条螺栓断裂。
简体端盖螺栓断裂对设备安全运行危害极大,轻者引起磨体振动,法兰处漏浆,重者可导致筒体变形脱落,轴承座等破裂的严重设备事故。
端盖螺栓断裂的原因主要有以下几个方面:
(1)端衬与中空轴之间的环形空腔中流入矿浆,长期冲刷磨蚀端盖螺栓尾部,引起螺栓松动,中空轴歪斜,个别螺栓受到的冲击载荷增大而断裂。
(2)更换后的螺栓未采用铰孔螺栓,受力不均,强度不足。
(3) 更换螺栓时,未清理端盖止几与中空轴法兰间夹杂的异物,导致磨机前后轴不同心。
(4)未定期检查紧固螺栓。
处理方法:
(1)在简体端衬与中空轴间环形空腔中填充软质填料,如废旧橡胶块、石棉绳等,或浇灌水泥砂浆,但应注意事后检修拆卸的方便,螺栓孔的预留及衬板的牢固安装。
(2)更换螺栓时,应停机拆掉全部联接螺栓,彻底清理止口后,涂上1层铅丹或漆片,然后安装专用铰孔螺栓,并保证磨体不同心度小于o.5 mm。
(3) 为了确保中空轴与端盖的相对位置不变,且各个铰孔螺栓受力均匀,铰孑L螺栓的安装还应根据两零件螺孔的精度“对号入座”。并均匀拧紧螺栓。
(4)定期检查紧固螺栓,防止螺栓松动、漏浆。
1.3 筒体裂纹
球磨机筒体材料为16 Mn钢,厚度16mm.端盖厚度50 mm,镶嵌入筒体后二者焊接在一起。2002年元月22日,2#磨机简体前端50 mm处出现裂纹并漏浆。停车检查发现裂纹正处于端盖法兰焊缝处。内部裂纹长度接近2/3周长,外部裂纹长度近1/2周长,内部裂纹最宽约l mm。
裂纹产生的原因有如下几点:
(1) 筒体变形 因长期停车,致使简体在18.5 t(铭牌质量)研磨体及自身重量的作用下产生挠曲变形,受到的弯曲应力增大。
(2) 两轴不同心简体端盖与中空轴联接螺栓松动或断裂后,中空轴歪斜,造成前后两轴不同心。
(3) 负荷增大磨机生产能力提高,加入物料和研磨体质量增大,载荷增加后对简体冲击过大。
(4)疲劳破坏因结构原因,简体在端盖焊缝处受到的应力最大,且在长期运行中受交变载荷的反复作用而发生疲劳破坏。加之,焊缝热影响区发生脆化现象使简体材料的断面收缩率和延伸辜下降,加速了简体破坏的进程。
处理及预防措施:
(1)补焊筒体。清理、打磨简体内部裂纹,采用T 506或T 507焊条分段对称焊接。外部裂缝打坡rI后对称焊。磨平后,外包钢带,材料16 Mn,宽度100~120 mm,厚度16 mm。
(2) 为避免磨机筒因长时间停车受压变形,可采取以下任一方法加以预防:①洗磨后,倒空前、后仓研磨体;②停车后每8h盘动900或180。(点动);③将磨机简体用千斤顶支起;④降低设备负荷率,按规定质量要求加入研磨体,保证设备安全稳定运行;⑤经常检查、紧固端盖螺栓。
1.4隔仓板断裂
隔仓板将简体分为前后仓,前仓充填大球,主要是冲击粉碎;后仓充填小球,主要是研磨粉碎。隔仓板中部的固定环(两半部分)将24块隔仓板连成一个整体。同时,因固定环截面形状为“7”形,避免螺栓受研磨体冲击而磨损断裂。隔仓板中部的孔板与固定环联接。
磨机运行一段时间后,隔仓板断裂,孔板脱落的现象频繁发生。隔仓板断裂的主要原因是固定环凸缘磨损,研磨体冲断螺栓使该隔仓受到较大冲击所致。其次是孔板与固定环连接螺栓螺母裸露在固定环之外,易受研磨体冲击而断裂,致使孔板脱落,由此发生的窜球现象影响研磨效果。
处理措施:
(1)注意检查固定环凸缘的磨损情况,发现磨损及时更换。
(2)将孔板与固定环整合为一体(仍分为两半部分,因人孔限制),减小了连接螺栓的长度,消除了孔板脱落现象。
(3)连接螺栓用双螺母锁紧,然后点焊,防止螺母松动。
采取上述措施后,大大延长了隔仓板的使用寿命,一股使用周期可达6个月以上。
1.5轴瓦拉伤
轴瓦拉伤的原因一方面是缺油,因干磨擦所致;另一方面是润滑不良,油被污染。
1990年6月5日,带油环上刮油器松动脱落,致使磨机前轴瓦拉伤,轴瓦限位螺栓顶断。巡检发现油位正常。但操作工未观察到主轴表面是否有油。
主轴承座润滑油被污染的原因主要是矿浆从磨头迷宫密封漏入轴承座内,导致润滑不良。
操作中一是采用正确的观察方法,应在磨机旋转方向一侧从监视孔观察轴瓦的润滑情况,而不应只观察油位的变化;二是改进迷宫密封,在迷宫处安装滴环,防止油被污染;三是发现润滑油被污染,要及时换油。
2、技术改造
2.1橡胶衬板代替金属衬板
采用橡胶衬板代替金属衬板有以下优点:
(1)耐磨性好,使用寿命长
根据磨机多年运行情况统计,前仓橡胶衬扳可使用8—10个月,实际运行4 474—6 355 h,根据资料介绍,一套锰钢衬板使用寿命约为3600 h。按更换1次压条计+橡胶衬板的使用寿命为钢衬板的
1.8倍左右。若按更换衬板对比使用寿命,橡胶衬板约为锰钢衬板的3倍以上。
(2)提高球磨机的生产能力
球磨机采用橡胶衬里比金属衬里的产量提高10%—30%(因用矿不同而异)。∮l830 mm×6 400 mm球磨机改用橡胶衬板前后的产量对比见表2。
(3)减轻磨机负荷,节能效果显著
橡胶衬板质量轻,仅为锰钢衬板的1/2—1/4,使用橡胶衬板后,磨机转动部分质量减少约6吨,其运行电流从300 A下降到260 A,每年可节电14万千瓦时。
转动部分减轻后,磨机的启动力矩亦相应减小,即使在电压偏低的情况下,仍能一次启动。
(4) 减少备件费用,降低生产成本
每套橡胶衬板的价格与锰钢衬板相近,但寿命是锰钢的1. 8-3O倍,所以若按每吨原矿的衬板费用计,橡胶衬板为2元,而锰钢衬板为8元。
(5)节约钢材,提高矿浆质量
1台∮l830 mm×6 400 mm磨机,使用1套橡胶衬板可节约锰钢43吨左右。用钢衬板时,矿浆含Fe3031.90%,改为橡胶衬板后,同种矿的矿浆含Fe203降至1.22%。
(6) 延长设备的使用寿命
因质量减少,传动部件传动力矩减小,所以减轻了减速机,联轴器、轴承和齿轮的磨损,同时延长了传动部件的使用寿命。使用橡胶衬板后,每台球磨机年运转时间增加约500 h,仅此一项,1台∮1 830mm×6 400 mm磨机就可增产DAP约4 000吨。
(7)减轻劳动强度,减少修理工时
改用橡胶衬板后,没有因断螺栓而引起衬板脱落的现象,维修量大为减少,同时橡胶衬板轻而有弹性,安装时方便,减轻了劳动强度。
(8)工作环境得到改善
改用橡胶衬板,噪音大为降低。同时橡胶衬板隔热性能好,提高了矿浆温度,改善了矿浆的流动性能,大大改善了工作环境。
(9)利用磷酸系统排放的污水代替清水磨矿。
由于橡胶衬板耐腐蚀,所以将磷酸系统回收的污水再利用返回磨机,不仅节约了清水,减少-污水排放,而且在一定程度上降低了酸耗。
2.2进料装置的改造
某公司∮1830 mm×6400 mm球磨机进料装置由进料溜管、进料螺旋、密封装置和加水管4部分组成。
密封装置原设计采用填料密封,不仅磨损快,漏料严重,而且摩擦阻力大,磨机启动困难。1990年10月将填料密封改为迷宫密封并在两摩擦副间加润滑脂,解决了漏料问题,提高了密封效果和磨机的启动性能。但没有克服矿水比例失调,磨机“糊磨”时密封面泄漏矿浆的现象。为此.在密封环处增设1个橡皮垫,起到“滴环”的作用,将矿浆引流到地面,避免了矿浆进入轴承座内,使润滑油被污染。
磨机进料装置的作用是将矿和水按比例顺利送入磨机内部,然而由于磷矿经擦洗脱泥处理后,含水量大,细矿多,极易造成进料螺旋堵塞,每班停车清理螺旋次数达7~8次。1997年7月15日,将进料溜管由∮400mm缩小到∮325mm(进料螺旋法兰内孔随之缩小)插入进料螺旋。加水管由磨机内部移至溜管处。这样,利用水的冲力将矿送到进料螺旋上,然后由螺旋将物料旋入磨机体内,彻底解决了进料螺旋因料湿而频繁堵塞的问题。
为了更好地提高磨机运转率,减少停机检修时间。1995年4月,在进料溜管下部加装滑轮、轨道后,一拉一推就能完成进料装置的拆卸、安装,省力、省时又方便。
2.3减速机高速轴的密封改造
球磨机减速机轴封采用挡油环、毡垫密封结构。14球磨机高速轴密封长期漏油,1995年4月大修期间,将毡封改用油封(PG 160×130×14),彻底消除了漏油现象。但油封老化、磨损需更换时,必须拆卸联轴器后才能安装,检修时间长。在轴上安装2~3个备用油封,更换油封时将旧油封割断拿下即可,不需拆卸联轴器,大大延长了设备的检修周期。
2.4球磨机冷却水系统的改造
改造前,2台球磨机前后轴承座、轴瓦,减速机油温是分别冷却,进水口和出水口共有6个,操作控制分散,一次水浪费大。
改造后,将2台球磨机冷却水进出口合并集中,改为2进2出。保证了设备的安全运行,同时节约了大量水资源。
2.5滚筒筛的改造
改造前,滚筒筛安装钢丝筛网,筛网孔为5 mm×5 mm,磨损快,造成矿浆中大颗粒磷矿多,对萃取生产危害极大,对矿浆泵、磷酸料浆泵、稠浆污水泵、低闪轴流泵、搅拌桨、萃取槽防腐层等磨蚀严重,影响磷矿转化率,造成设备、管阀堵塞,降低开车率。
1995年4月,将钢丝筛网改由16 Mn,厚度3mm钢板卷制,网孔为∮3.86 mm。为了提高滚筒筛的开孔率,又将圆孔改为条形孔2.5×20 mm,并将滚筒筛制成圆锥形∮594/∮554mm,滚筒筛的锥度加快了矿浆中大颗粒矿的分离速度。
2.6安装直线振动筛
矿浆经滚筒筛一次分离后+仍难以满足生产需要。为此,在滚筒筛下部安装1台直线振动筛(规格600 mmXl 200 mm,筛网网孔1.2mm×7.2 mm,电机型号;YZD -8 -4,N=0.75kW,n=1 460 r/min),对矿浆进行二次筛分。矿浆经二次筛分后,提高了矿浆的细度。