
生物质锅炉新闻动态
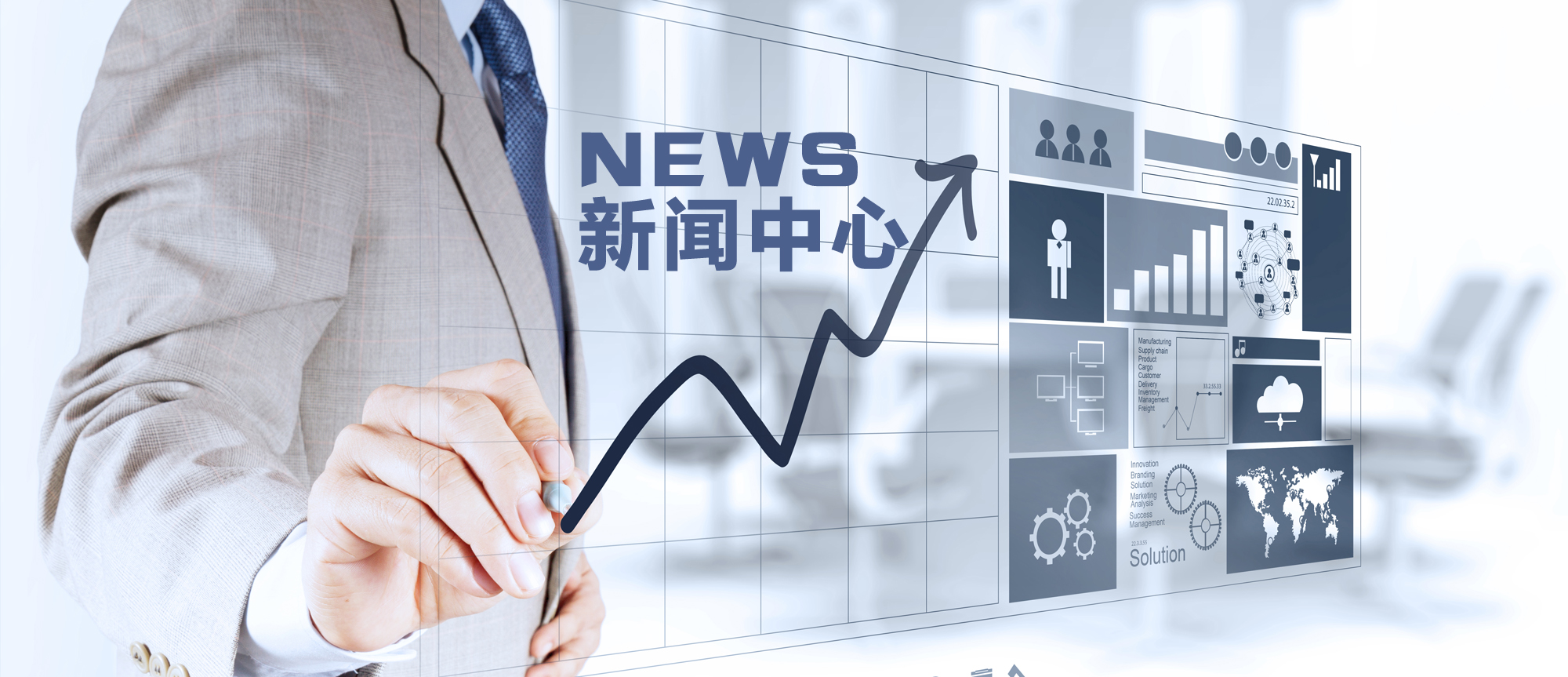
富通新能源 > 动态 > 生物质锅炉新闻动态 > > 详细
75t/h洗煤泥流化床锅炉设计与点火运行
发布时间:2013-05-25 08:03 来源:未知
煤炭洗选加工过程中排放出大量煤泥,煤泥的水分和灰分含量高,很难再利用。但堆积起来不仅浪费大量土地资源,而且对环境造成污染。
浙江大学热能工程研究所从80年代初开始致力于煤泥的流化床燃烧技术的研究与开发,从实验室研究入手,先后在永荣矿务局发电厂10t/h流化床锅炉和兖州矿务局兴隆庄煤泥热电厂的35t/h煤泥流化床锅炉上燃用洗煤泥取得成功。浙江大学和杭州锅炉厂设计的燃用煤泥的35t/h流化床锅炉己运行了近45000 h。浙江大学与无锡锅炉厂完成了75 t/h煤泥流化床锅炉的方案设计和施工设计,由无锡锅炉厂制造,该炉安装于兖州矿务局东滩矿煤泥热电厂,1997年12月18日点火成功,并运行至今。
1、75 t/h洗煤泥流化床锅炉的设计及结构
锅炉的结构见图1。
1.1锅炉参数
额定蒸发量 75t/h
饱和蒸汽压力 3. 82 MPa
过热蒸汽温度 450℃
给水温度 150℃
1.2燃 料
兖州矿务局东滩矿洗煤泥分析数据见表1。
1.3计算参数
热力计算涉及参数很多,有些参数在计算前根据具体情况选取或计算。部分预先取定的参数值见表2。
锅炉热力计算采用浙江大学热能工程研究所自行开发的流化床锅炉热力计算专用软件包。
2、锅炉结构
采用浙江大学提出的洗煤泥大粒度给料异比重床料的流化床新技术,在高温过热器前进行一次分离,低温过热器后设下出气旋风分离器,进行二次分离,并将灰回送炉内继续燃烧,具有燃烧效率高、结构紧凑、操作检修方便等优点。
富通新能源销售生物质锅炉,生物质锅炉主要燃烧木屑颗粒机压制的生物质颗粒燃料。
锅炉运行通过放底渣调节料层高度,加旋风分离器将飞灰分离并回燃,以进一步提高燃烧效率。80%热风经水冷布风板进入床层,其余20%热风由布置在床层上部的二次风口送入炉膛形成二段燃烧,以降低NO,排放。
锅炉系单锅筒自然循环,室内布置,由床层、炉膛、
撞击分离装置、锅筒及其内部装置、下出气旋风分离器、流化床回料室、过热器、省煤器、空气预热器、床下点火及辅助燃烧系统、平台扶梯、炉墙钢架等主要部件组成。
锅炉正常给料采用三台立式煤泥给料机从炉顶三个给料口投入床层。煤泥在炉内燃烧烟气和飞灰在炉膛出口冲刷撞击式分离器,一部分飞灰分离后再落回炉膛继续燃烧。高温烟气再经高低温过热器进入下出气旋风分离器,分离下来的飞灰经流化床回料器送回炉内继续燃烧。烟气流经省煤器再次沉降部分烟尘后进入空气预热器,经除尘器、引风机、烟囟进入大气。
锅炉的前墙设二只给煤口,以备燃煤时采用,给料口下部喷入播煤风,以冷却给料口,布风板风道前装有床下自动点火装置,在点火时启用。点火升温时间可控制,一般约1~2 h,床下自动点火装置由浙江大学热能所设计和制造。
为保证锅炉受热面和分离器等关键部件的长期安全运行,采用系统化的防磨结构设计。在密相区,横埋管上焊接了环形鳍片,在给煤泥点和返料口处,埋管让开;炉膛顶部烟气转弯处、顶棚和水平烟道包墙都分区域加焊了密度不同的销钉。锅炉设计中,下排气旋风分离器内敷设了耐磨浇注料,烧结后具有良好的耐磨性能。中心筒上焊销钉防磨。高温过热器,所有弯头处加防磨盖板;过热器和省煤器管束特定管排靠墙处焊接了搭片以防出现烟气走廊;下排气的旋风分离器出口下方设置了均流板和假想管,采用膜式省煤器,并在省煤器的高温段前三排管子上另焊两片纵向鳍片,弯头处加防磨盖板;空预器管子入口加了套管。
3、锅炉技术特点
3.1 低循环倍率
本锅炉与普通的流化床锅炉相比,采用较低的循环倍率(1~2),在保证燃烧效率的前提下,较低的循环倍率避免了大量灰分无效地在炉内循环,降低了自用电耗。
3.2 特殊的分离器型式
分离器采用下出灰、下排气方式,与锅炉流程完全吻合,虽然分离效率略低,但烟气阻力可降低,也使结构简单合理。
3.3 中温分离
采用飞灰中温分离技术,分离器工作温度略低于600℃,布置在省煤器上方,这种布置方式可缩小几何尺寸,使整个锅炉结构紧凑。
3.4 系统化的严密防磨措施
在床层埋管及其它易磨处都采取诸如降低烟速、加防磨板等严密防磨措施,确保锅炉长时间正常运行。
3.5 埋管结构
由于燃用劣质燃料,低循环倍率,密相区燃烧份额较大,密相区设置埋管有利于床温控制。
3.6床下热烟气点火
锅炉采用流态化方式的床下热烟气点火,这种点火方法节省用油,启停时间少,根据点火过程能量微分方程求解,该锅炉可以在60 min左右点火成功。
4、点火启动
传统的床上点火技术,存在以下明显缺点:能耗高;操作工序多,劳动强度大;自动程度低,控制性能差;成功率较低,与运行操作人员的经验有很大关系。特别是较大型的流化床锅炉需分床逐一点火升温扩散,启动过程长,锅炉承受的热应力大。因此传统的上点火方式己难以与流化床锅炉发展形势相适应。特别是75 t/h洗煤泥流化床锅炉为目前国内乃至世界上最大的全部燃用洗煤泥的流化床发电锅炉,更应在锅炉点火启动技术上采用先进的床下热烟气点火技术。
流化床锅炉由于运行时需要维持相当厚度的料层,正常运行开始前,必须加热升温至正常运行的温度,通常在800 C以上,75 t/h洗煤泥流化床锅炉选用了浙江大学开发的ZU-75A型床下热烟气点火装置,该点火装置由油枪、高能点火器、旋流器、稳焰器、燃烧室等组成。本锅炉配两只点火装置。该点火装置采用旋流燃烧器、带回油的油枪,因而可根据锅炉启动的要求在较大范围内调节燃油量,从而改变进入锅炉风室的热烟气温度。
正常启动过程如下:启动引风机和送风机,并启动油泵备用,对点火燃烧室吹扫3~5 min后打燃高能点火装置,然后迅速开启油枪前的油路电磁阀点燃油雾。两只点火装置顺序启动。点火过程中通过改变进油压力和回油压力调节喷油量来调节热烟气温度,也可调节风门的开度,改变掺混风的流量进而调节热烟气温度。点火过程中一般控制点火燃烧室内温度不超过1100~1200℃,锅炉风室内温度不超过700℃,当床温达到500 ℃后,即可投入少量烟煤,待床温呈上升趋势后逐步加大投煤量,减少喷油量,当床温达到800~850℃时停油,锅炉点火启动过程完成。待稳定运行10min后,即可慢慢切换为投煤泥。图2为某次点火启动过程中床温、风室、温度随时间的变化。
白锅炉下点火装置投运以来,点火过程中从未发生结焦现象,点火成功率100%。该点火装置的成功应用,体现了安全、经济、可靠、文明,并实现了点火过程的程序化,具有工作可靠、操作简单、调节控制方便、节油省能、点火成功率高的特点。
5、运行情况
1997年12月18日,75 t/h洗煤泥流化床锅炉点火成功,并进入满负荷运行。由于煤泥系统未完成调试,先燃用洗中煤,锅炉运行良好,可带12 000 kW负荷。供热管网安装完成后,实现了75 t/h满负荷运行。
1998年4月30日,顺利完成煤泥系统调试后,即开始投煤泥运行,至今锅炉运行参数正常。
75 t/h洗煤泥锅炉是在35 t/h煤泥炉的成功运行基础上进行的改进设计,显示出较多的优点,如全膜式壁结构,水冷风室床下点火方式,不需分床点火。床料的补充采用定期加入洗中煤的方法,减轻了运行人员的工作负荷。该炉不仅可以单独燃用煤泥、洗中煤,而且适用于煤泥和洗中煤的混烧。对飞灰进行取样分析表明,采用二级分离与回送,锅效率也有较大提高。