
生物质锅炉新闻动态
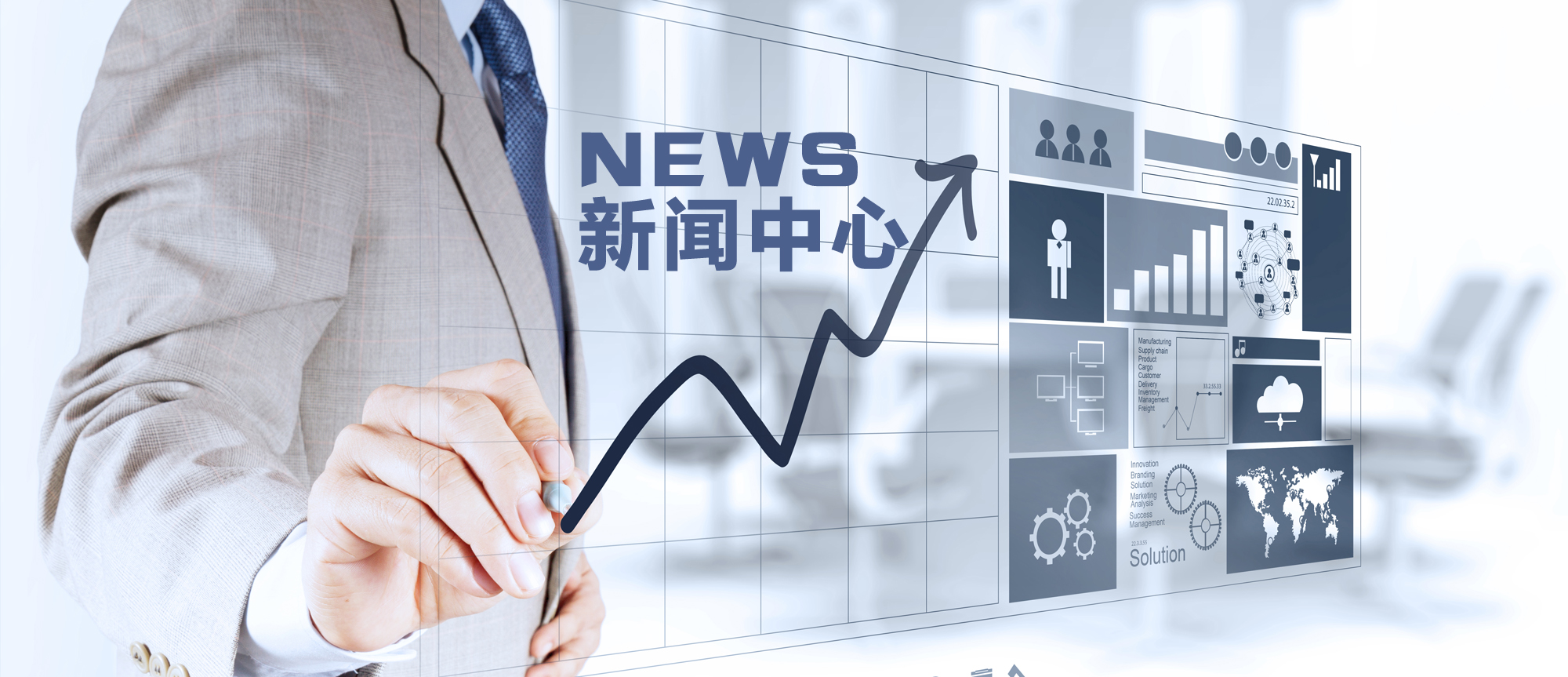
富通新能源 > 动态 > 生物质锅炉新闻动态 > > 详细
75t/h锅炉高炉煤气掺烧转炉煤气的实践
发布时间:2013-05-31 11:35 来源:未知
1、概况
宣钢动力厂8#、9#高炉鼓风机站5台中压锅炉是公司东区高炉煤气最大的调节用户,夏季高炉煤气富裕,锅炉全部燃用高炉煤气;而冬季高炉煤气紧张,锅炉煤气使用受限,是高炉煤气压减使用调节的第一用户。
本着减少转炉煤气放散、间接提高转炉煤气吨钢回收率、缓解冬季高炉煤气平衡紧张的目的,动力厂自2009年11月6日开始,陆续对2台75 t/h锅炉进行了掺烧转炉煤气的技术改造工作,其中1#炉改造于2009年12月3日完成,2#炉改造于2010年1月12日完成。
2、燃料燃烧计算
燃烧计算时,未考虑煤气含湿量,即假设转炉煤气和高炉煤气都是干煤气,标态下煤气的含湿量dq =0°
转炉煤气和高炉煤气热值计算结果如表l所示
燃转炉煤气和燃高炉煤气的理论烟气量计算结果如表2所示。75 t/h锅炉燃料由高炉煤气变为转炉煤气,锅炉的烟气温度和烟气量也会发生变化。转炉煤气热值相对于高炉煤气较高,故锅炉燃料由高炉煤气变为转炉煤气时,炉膛温度提高,炉膛辐射换热增强,炉膛水冷壁吸热量提高。
对于中压锅炉,过热器是以对流换热为主的受热面,计算烟温为500一700℃时,烟气侧辐射换热系数只是对流换热系数的1/5。因此,影响蒸汽温度的主要因素是烟气量。由以上计算可以看出,在标态下,转炉煤气完全燃烧所需空气量是高炉煤气完全燃烧所需空气量的2倍左右;但是产生的烟气量约为1.3倍。考虑两者热值的差异,假设在锅炉相同负荷、用两种煤气热效率相同的情况下,转炉煤气燃烧后每放出单位热量所产生的烟气量约为高炉煤气每放出单位热量所产生的烟气量的70%。由于高炉煤气、转炉煤气的成分是在一定范围内变化的,所以计算结果可能与实际有所出入。
因此,锅炉燃料由转炉煤气替换高炉煤气时,锅炉蒸发量应该有所增大,而过热蒸汽温度调节用减温水量将减小。
3、改造方案
3.1改造方式的确定
锅炉改烧转炉煤气后,锅炉燃料组成发生了根本变化,本应该对锅炉进行热力校核计算并对受热面进行相应调整,但是根据目前。高炉区域鼓风机站热力负荷及2台75 t/h锅炉设备的实际情况,本着节约改造费用、缩短工期的原则,确立了不改变锅炉本体受热面布置、仅改变锅炉燃烧器布置方式的总体改造思路。
通过改造,期望锅炉可以实现在转炉煤气与高炉煤气混烧、全燃高炉煤气、全燃转炉煤气等3种工况下运行,且锅炉出力不低于50t/h。
3.2改造措施
(1)新架设1条Dn800mm转炉煤气管道,将其作为2台75 t/h锅炉共用煤气母管,最大流量为18000m3/h,保证煤气在锅炉喷嘴前压力不低于4.5 kPa。
(2)转炉煤气燃烧器和高炉煤气燃烧器均选用着火性能稳定、阻力水平较低,负荷调节性能良好的双旋流式煤气燃烧器,转炉煤气燃烧器单只设计出力为5000m3/h,高炉煤气燃烧器单只设计出力为8000m3/h,并对锅炉燃烧区域四角48根水冷壁管重新弯制。
(3)锅炉室外转炉煤气总管和原高炉煤气总管之间铺设联通管,并由电动阀控制切换,实现高炉煤气燃烧器和转炉煤气燃烧器的共用,即根据转炉煤气和高炉煤气压力情况,这8只煤气燃烧器既可以同时全燃转炉煤气或高炉煤气,又可以实现转炉煤气和高炉煤气分层燃烧。并增设氧化锆分析仪,根据炉膛出口含氧量进行燃烧调节。
(4)保留原四角高炉煤气燃烧器及室内高炉煤气支管,焦炉煤气作为锅炉点火及低负荷稳燃燃料。
(5)运行调节中,使下层煤气燃烧器负荷大于上层燃烧器负荷。
(6)对锅炉减温水系统进行改造,增加以锅炉给水为介质的备用调节管路,并针对管径小的情况,选用性能可靠、调节精度高的调节阀,确保改造后过热蒸汽温度在安全可控范围之内。
(7)拆除锅炉麻石水膜除尘器并降低引风机前烟道标高,以有效减小烟气阻力及锅炉烟道系统漏风。
(8)密封炉膛底部排渣槽.减少炉膛漏风对炉膛火焰中心高度的不利影响。
(9)送风机和引风机不变。
(10)修订并完善锅炉运行维护和操作规程以及煤气使用相关制度,以有效保证转炉煤气安全、稳定地掺烧。
(11)对锅炉热工、电气控制系统进行优化,利于岗位工操作、调节便利可靠。
3.3实施过程
首先铺设1条DN800mm的转炉煤气管道至原高炉煤气平台,然后在新转炉煤气总管和原高炉煤气总管之间铺设联通管并加装电动阀控制。同时重新对锅炉燃烧区域四角48根水冷壁管进行弯制,安装双旋流式煤气燃烧器。根据高炉煤气、转炉煤气火焰长,原有炉膛空间偏小这一状况,为保障锅炉过热器运行安全,降低排烟温度,在有限的燃烧器区域空间内,最大限度地降低四角燃烧器中心标高。其中1#炉四角燃烧器中心标高较改造前降低约620mm;2#炉则根据1#炉投运后掺烧转炉煤气的实际情况进一步调整,高炉煤气燃烧器标高较1#炉降低了190mm,转炉煤气燃烧器降低了750mm。锅炉减温水系统增加一路备用管路并且选用高精度调节阀以保证改造后过热蒸汽温度在安全可控范围之内。拆除原锅炉麻石除尘器和炉膛底部排渣槽。经过两个半月的改造调试,75t/h锅炉重新投入运行。
4、运行效果
改造完成后,对75t/h锅炉进行了3种工况下的调试(调试情况见表3—表5)。
可以看出锅炉在3种全燃气工况下运行出力如下:
(1)在高、转混烧工况下,保证转炉煤气使用量的前提下,通过调节高炉煤气用量,2台75 t/h锅炉出力可以不低于110Uh。
(2)在全燃转炉煤气工况下,单台锅炉最佳煤气使用量为25000m3/h左右,锅炉出力可以达到55 t/h。
(3)与锅炉改造前在全燃高炉煤气工况下最大出力45t/h相比较,锅炉可以达到55 t/h,仍有上升空间,但受排烟温度影响,锅炉负荷在50Uh左右为宜。
(4)由于减少了锅炉漏风量,在全燃高炉煤气工况、锅炉最高负荷下引风机入口调节风门开度由改造前的100%减小至70%,降低了风机电耗。
从运行效果来看,2台锅炉掺烧转炉煤气的技术改造达到了预期目的。就目前煤气状况而言,2台75t/h锅炉以高、转煤气混烧为主,其中设定转炉煤气量为15000m3/h左右,即1#炉7000m3/h、2#炉8000m3/h。以高炉煤气作为调节锅炉负荷的手段,为热力发电满负荷运行创造条件,同时,为提高公司转炉煤气吨钢回收率做出了贡献。
5、结语
锅炉掺烧转炉煤气运行后,有以下问题值得考虑:
(1)锅炉改为全燃煤气后,过热器面积偏大,特别是在锅炉升压并炉阶段,锅炉过热器存在超温的安全隐患。确定减温水投用的时机与水量,杜绝过早投用出现“水塞”或延误投用而造成过热器管排过热疲劳损坏是运行中应该注意的问题。
(2) DN800mm转炉煤气管道除供75t/h锅炉使用外,富裕量将掺入高炉煤气管道,但在高炉煤气管网压力高时,掺混调节阀只能关闭,转炉煤气无法掺混,否则,高炉煤气进入转炉煤气管道,影响锅炉正常使用。故如何匹配高炉煤气压力与转炉煤气管网压力以提高转炉煤气回收率,是一个值得思索的问题。
(3)锅炉全燃煤气改造后,由于受热面面积未做相应调整,使锅炉排烟温度有所提高,故可利用以后锅炉大修机会,对炉膛水冷壁、省煤器面改造,从而达到进一步提高锅炉蒸发量、降低排烟温度的目的。