
烘干搅拌输送新闻动态
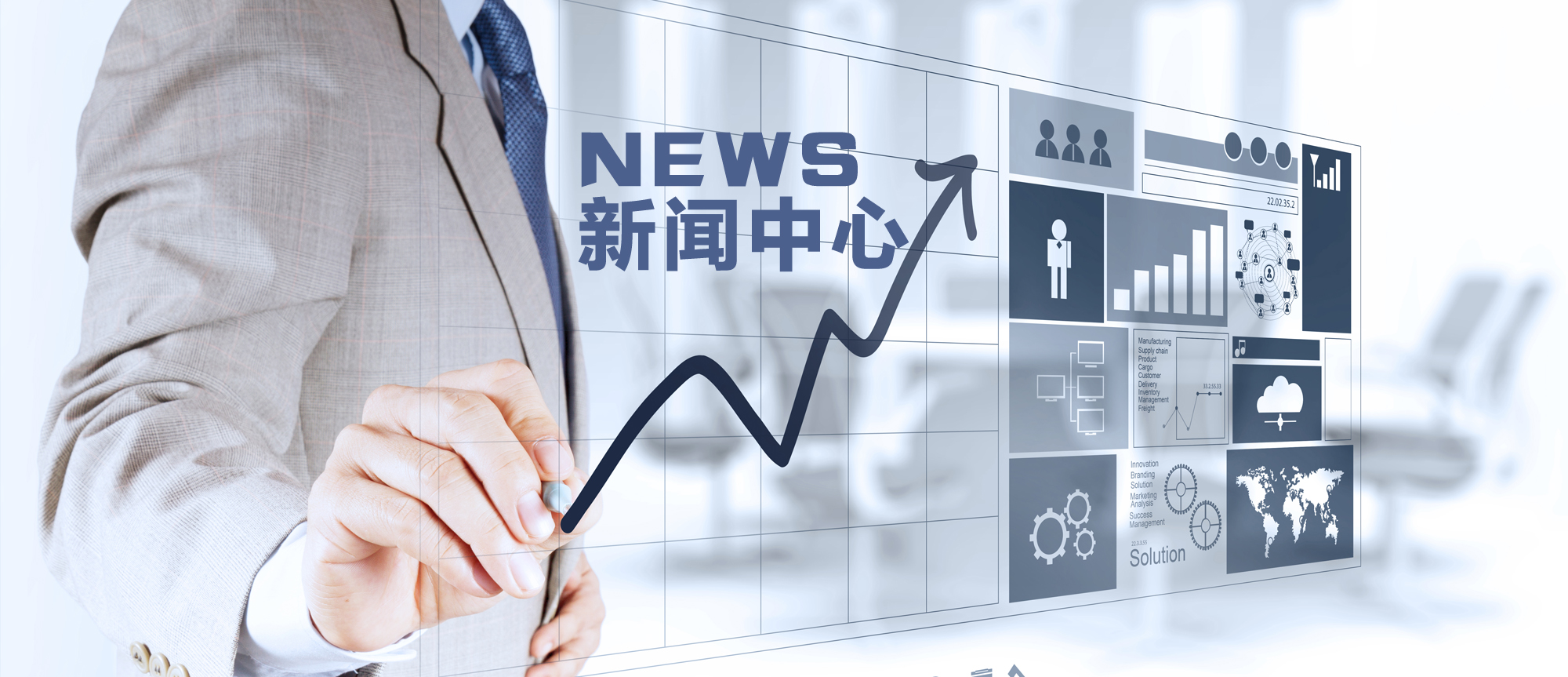
富通新能源 > 动态 > 烘干搅拌输送新闻动态 > > 详细
2000t/d回转窑生产线节能技术改造
发布时间:2012-10-21 15:27 来源:未知
某公司2条2 000t/d生产线是我国自行开发设计的,主机设备全部国内制造,采用四级预热器带RSP分解炉,回转窑规格为4mx60m,于1992年4月通过验收,产量稳定在2x2 056t/d。1995年10月配套建成了12MW带中低温补燃炉的余热发电系统,年发电量为8400万kWh。随着时代进步,水泥生产装备飞速发展,这2条生产线的经济技术指标已经严重落后。因此,我公司于2009年9月对2号生产线进行了技术改造,取得了很好的效果。
1技改前情况
1)粉尘排放浓度高
原环保设施设计标准要求标态下粉尘排放浓度<150mg/m3,而GB4915-2004《水泥工业大气污染物排放标准》要求2010年1月1日起,现有生产线各生产设备标态下粉尘排放浓度<50mg/m³。
2)熟料热耗高
预热器出口气体温度高于400摄氏度,熟料热耗高达3966KJ/kg,折合标准煤耗135kg/t。比山东省地方标准DB37/836-2007《水泥单位产品综合能源消耗限额》中规定的2008年可比熟料标准煤耗限额值123kg/t高9.8%,比2010年可比熟料标准煤耗限额值114kg/t高18.40/0,
3)预热器系统阻力高
由于预热器采用的是老式高阻力旋风预热器,出口阻力高达5 800Pa,导致熟料烧成电耗高达38kWh/t,综合电耗达81kWh/t。比DB37/836-2007中规定的2008年可比熟料综合电耗限额值72kWh/t高12.5%,
比2010年可比熟料综合电耗限额值64kWh/t高26.6%。
4)熟料成本高
由于熟料的热耗和电耗高,设备的产能利用率低,产品的制造成本高,随着原材料及能源资源价格的提升,产品市场竞争力不强。
5)运转率低
部分设备老化及功能缺失造成运转率低下,不能满足企业稳定高产低消耗的技术要求。
2 技改措施
2.1窑尾废气系统
原有电除尘器粉尘排放已远远超过现有标准;原有的增湿塔规格为中9m x22m,处理风量为458 000m3/h,喷水系统已经落后和老化,经常出现湿底现象,不能正常运行;废气排风机的排风量为446000m3/h,全压1186Pa。
将电除尘器更换为KDM280-2x6的袋式除尘器,处理风量5O0000m³h,进口风温200℃,标态下出口含尘浓度≤30mg/ m³,过滤面积10080²,压力损失≤1700Pa,采用西门子脉冲控制技术,进口脉冲阀,玻纤後膜复合针刺毡滤袋。由于电除尘器改成袋式除尘器后阻力将增加1 200Pa左右,原有排风机不能满足要求,改造后将原有风机全压提高到2500Pa,相应将原有的功率280kW、转速480dmin的12极电动机更换为功率500kW、转速580r/min的10极电动机。
更换了部分腐蚀的增湿塔本体,更换喷水系统,采用低压双流体喷雾系统,变频调速,便于中控操作人员随时根据气体温度调节水量,保证袋式除尘器入口温度。
2.2生料制备系统
原有生料粉磨系统为2套中3.5mxlOm中卸烘干闭路球磨系统,配套舛m旋风式选粉机。每套球磨系统的配料系统均由3个磨头仓组成。石灰石和砂岩顶配料后送入混合料磨头仓,粉煤灰和硫酸渣各占1个磨头仓,生料磨台时产量为71.6t/h,入库提升机为板链式,设计能力200t/h。
技改期间将原来的石灰石和砂岩混合料仓改为2个单独的纯石灰石仓和1个纯砂岩仓,保留硫酸渣仓以及粉煤灰仓共5个磨头仓。石灰石皮带秤的计量能力由85 t/h改为120t/h。生料终粉磨系统采用CLF180/100辊压机,配套VX9620G型V型选粉机和XR3400动态选粉机,出入V型选粉机提升机分别采用NSE500和NSE650提升机,现辊压机系统产量稳定在220—230t/h。同时更换原有入库提升机为N-TGD630x48500钢丝胶带提升机,提升能力250t/h。
2.3生料出库、计量及提升系统
原有生料库充气系统罗茨风机已严重老化,备件无法购买,且故障率高;原库底透气层损坏,均化效果差;原提升机因预热器能力和高度变化,无法满足改造后需要。改造期间更换了库底充气层及罗茨风机,入窑提升机利用原有部分壳体,改造为N-TGD630x90426钢丝胶带提升机,提升能力220t/h;生料计量系统为申克秤,最大计量能力300 t/h。
2.4预热预分解系统
原有的四级旋风预热器,生科与气流换热不充分,结构形式落后,换热效果不好,导致预热器出口废
气温度高,熟料热耗偏高。此外分解炉容积偏小,煤粉在炉内燃烧不完全,导致底部预热器温度与分解炉温度倒挂,也是引起热耗上升的原因。
老式高阻力旋风预热器的旋流角度仅1800,气流紊流阻力高,进风口及出风口风速设计偏高,烟室缩口风速也很高,导致系统整体阻力很高,另外三次风管为V形结构,也增加了气流阻力。这不仅影响煅烧系统的通风能力,还大大增加r高温风机的电耗。
分解炉容积小,煤粉在炉内燃烧不充分,没有完全燃烧的煤粉和生料粉混合后被喂入窑尾,在烟室和分解炉缩口处形成结皮,影响窑内通风,窑内工况恶化。对劣质煤的适应性更差,窑系统的产能难以发挥。分解炉容积仅220d,单位熟料产量容积比仅2.65m³·t/h
改造后采用的预热器系统为2-1-1-1-1组合带N-RSP分解炉,结构简单紧凑。各级预热器规格为Cl:2-Φ5000mm,C2: l-Φ6 700mm.C3:1-Φ6 950mm,C4:1-Φ6 950mm.Cj:l-Φ7250mm。预热器采用具有高分离效率的大蜗壳高效低阻型旋风预热器,有效降低了预热器系统阻力。改造后C.出口的阻力降至5600Pa左右,C1出口废气温度降到340℃左右。
N-RSP分解炉规格为分解室:Φ4500mm,混合室:Φ5 750mmx23500mm.鹅颈管:Φ4300mm。预燃室规格为Φ4 500mm,采用单侧270°旋式进风口,燃烧室旋流人口风速为25m/s左右,大大降低了进风口阻力。圆形混合室有效容积达51 6 m³,在中部还设计有一个缩口,使煤料气混合更均匀,燃烧更充分。N-RSP比较重大的改进是增加了连接混合室与C,的鹅颈管,进一步增加了分解炉的有效容积,延长了煤粉和生料的停留时间。炉系统内气体停留时间Ss,物料停留时间22s以上,对于低品位燃煤也有很好的适应性,有效降低了燃煤成本,也使c5的布置高度合理降低,降低了窑尾框架的高度。混合室底部缩口采用圆形结构,没有边角效应,使物料不易在此黏挂,减轻结皮,还可以避免方形截面的直墙段上耐火材料脱落的问题,缩口处耐火材料的使用寿命能有较大的提高。
2.5回转窑
回转窑原传动电动机为2x125kW,窑最高转速为3.2r/敏,不能满足改造后的要求,为此更换减速器最高一级传动齿轮,将窑转速提高到4.5r/min,相应电动机更换成2台ZSN4-280-092B/160kW毫动机,同时更换存在裂纹的二档简体,加宽二档轮带、托轮,改善该处受力状况,对窑口简体、窑头密封、窑尾密封进行完善大修。正常运行后,窑转速为4,2r/rrun左右,满足3 000t/d要求。
2.6篦冷机
原有篦冷机是S609-819-809-1019富勒二代篦冷机,篦床有效面积仅46.8m2。2000年前后,曾进行过一次改造,将前5排改为固定篦板,一段改为高阻力、低漏料篦板,比改造前稍有改善,但是效果不理想,出库熟料温度达到150℃左右。改造后采用928S/1140H型篦冷机,设计能力2 800t/d,篦床有效面积68.4m2,全部采用充气篦板,每块篦板下带有自调节阀门,控制篦板通风量,有效地消除了“红河”现象,产量在3 000t/d时篦冷机出口<20mm未经破碎的熟料完全可以手拿。二次风温达到1110℃以上,三次风温达到860℃左右,窑头废气温度270℃以下,达到预期效果。
2.7窑头废气处理系统
原电除尘系统规格型号为F400/H4S/2 x35 -96110/P/2T/LZD.横截面积为105m2,处理能力315 000d/h,窑头排风机流最为384 000m3/h,全压为1422Pa.转速580r/min。改造期间增加极板和电晕线清灰能力,提高收尘效果,同时补齐极板和电晕线,取消运尘拉链机,改成料斗直接通过回转下料器人熟料拉链机。将原有排风机转速改为730dmin,全压提高到2 000Pa,相应电动机由10极更换为8极,功率由260kW提高到355kW。
2.8煤磨系统
原有煤磨系统为两套中2.8mx(5+3)m烘干风扫球磨系统,电动机功率480kW。配套有粗粉分离器、细粉分离器、电除尘器,系统台时产量约12~14t/h。煤粉计量系统由双管给料机、冲板流量计和气力喷射泵组成。存在以下问题:
1)煤磨产量太低,最大产量为14Uh。对比目前同等规格的煤磨,产量应在17t/h以上,效率太低,不仅浪费电能,产量也不能满足改造后窑系统的需要,另外大小齿轮磨损严重需要更换。
2)选粉机为静态粗粉分离器,分离效率低,煤粉细度控制非常困难。
3)煤粉计量系统控制和计量精度均较低,给回转窑的操作造成困难。
改造后,磨机内部衬板重新设计,更换磨损的大小齿轮,增加研磨体到额定的32t,保证磨机的粉磨能力,采用MDS -850高效动态选粉机,处理风量50 000—55 000m3/h,产量达到18—20t/h,并能灵活控制煤粉细度,提高选粉效率,增加唐机产量。改用袋除尘器简化了工艺过程,将标态下粉尘排放浓度降至<30mg/m³。窑头和窑尾均采用MULTICOR K50称重流量计,窑头采用MULTICELL800-50水平星形给料机,给料量1.0~10t/h,精度±0.5%,窑尾采用MULTICELL800-70水平星形给料机,给料量1.5~15t/h,精度±0.5%,实现了煤粉准确的控制和计量。窑头采用四通道皮拉德燃烧器,有效保证煤粉燃烧,窑尾温度稳定在1200qC左右。
2.9原煤预均化系统及配料输送系统
原煤预均化堆场的取料机为桥式斗轮取料机,设备老化严重,备件供应困难,故障率较高,且供应3条熟料生产线,无大修时间,造成设备状况日益恶化,很难保证全厂燃煤的连续稳定供应,经常出现铲车直接喂煤,原煤得不到均化就粉磨入窑,给回转窑的稳定煅烧造成困难,也不能满足改造后所需输送量要求。
改造后采用QQG200/30抬头桥式刮板取料机,并对进出料输送系统进行改造,使得堆料能力达到150t/h,取料及输送能力保持150t/h,更换石灰石、砂岩和粉煤灰输送系统减速器,提高皮带速度,达到提高输送能力的目的。
2.10变频技术应用
原有高温风机采用液力偶合器写电动机连接,窑头排风机、窑尾排风机均采用对轮直连式,改造后上述3台风机均采用变频调速技术,新增的辊压机循环风机、选粉机等也采用变频调速技术,有效节约能源,降低电力消耗。
3技术改造效果
2号生产线于2010年8月技改完毕投入生产运行。截至10月初已安全运行40d,回转窑喂料量稳定在220dh,熟料电耗、煤耗达到并超过技改目标。
1)标态下生产线各生产设备排放浓度降低到<30mg/m³满足GB4915-2004的要求。
2)熟料28d抗压强度达到58MPa。
3)熟料热耗3260kl/kg,标准煤耗109kg/t,达到山东省2012年水泥企业可比熟料标准煤耗112kg/t的限额要求。
4)回转窑产量超过3 000t/d。
4 结束语
此次技改成功的经验首先是领导的重视,并组织大量人员进行了充分的改造前期准备工作。其次,本次改造设备采购均采用阳光招标方式,有效保证技改设备的技术参数先进性、性能町靠性及优异的性价比。最后,业主、设计方及监理、各安装单位精诚合作,合理安排时间,2号生产线在短短5个月内完成了设备安装、非标制作和浇注料等耐火材料施工,并且保证了安装期间的施工质量优异、安全无事故。
现1号线正在进衍设备拆除,预计2011年6月底投入生产。