
生物质锅炉新闻动态
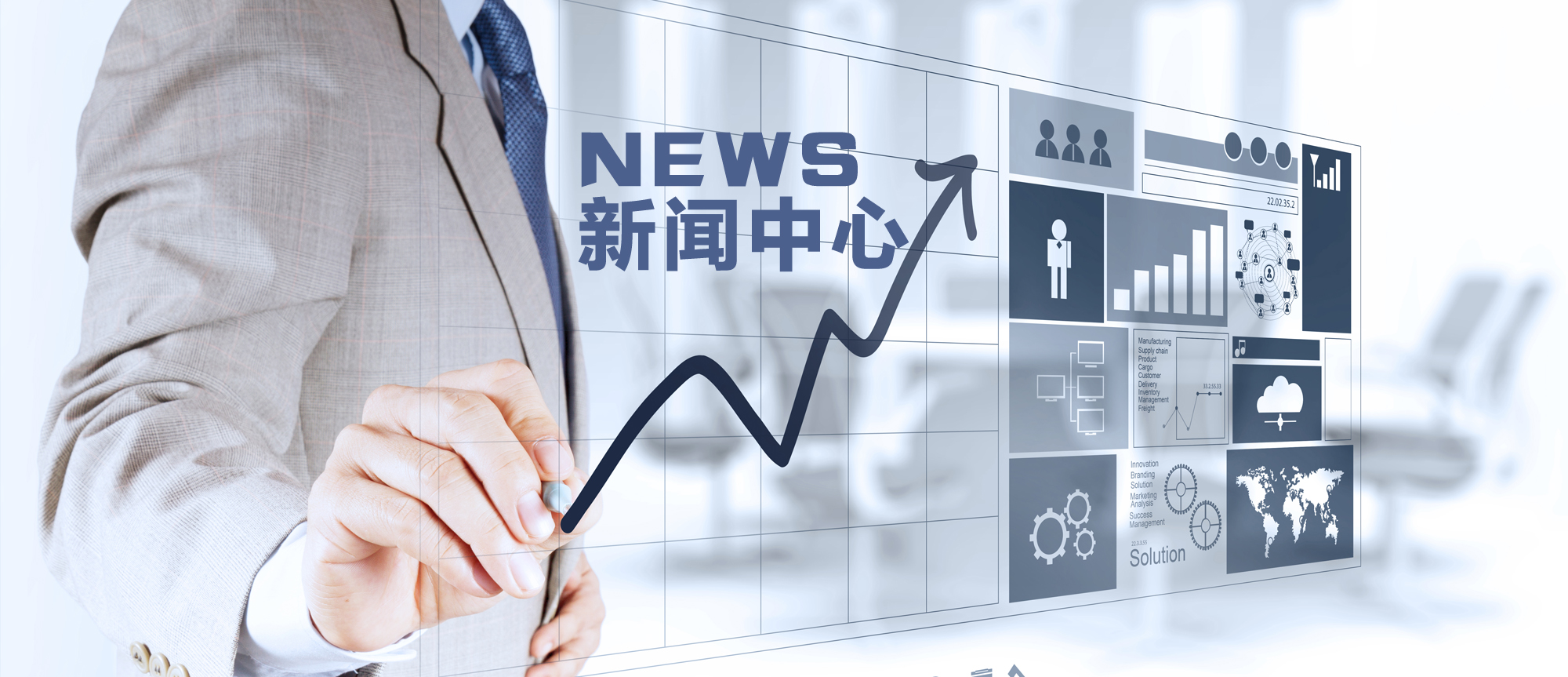
富通新能源 > 动态 > 生物质锅炉新闻动态 > > 详细
75t/h水煤浆锅炉顶棚过热器破裂分析
发布时间:2013-06-19 08:01 来源:未知
1、前言
某厂动力车间新建75t/h水煤浆锅炉(TG - 75/12 -J)点火试运行过程中,顶棚过热器曾先后多处发生破裂泄漏。
顶棚过热器由15CrMoG钢管及其鳍片组成。换热管规格为∮42mm×5mm,鳍片扁钢截面尺寸为48mm×6mm。钢管与鳍片之间通过埋弧自动焊相连,焊接坡口为K型;焊丝H08CrMoA ∮2mm,焊剂HJ501;焊接电流260~320A,焊接电压28~32V,焊接速度600 mm/min;焊接无预、后热及焊后消应力热处理。顶棚过热器运行参数:管内介质为饱和蒸汽,温度约为300℃,压力约为13.8MPa。
现将过热管破裂分析及采取的改进措施简述如下。
2、检测和试验
2.1试样
现场和试验室宏观、PT检查发现,过热器破裂均发生于弯管区,见图1。检测和试验在取自顶棚过热器弯管(发生破裂)和直管部位的两组过热器管段上进行。弯管试样:长560 mm,由鳍片连接的两根相邻弯管段;直管试样:长500 mm.由鳝片连接的两根相邻直管段。
2.2宏观检验
在弯管试样弯曲内侧(翅片以下部分)角焊缝边缘附近多处存在与焊缝走向一致的穿透性裂缝,较长的一处长约100 mm,另一处长约50 mm,而且上述相应管段两鳝侧片以下角焊缝区大约呈对称开裂。
解剖检查看出,裂纹起始于角焊缝下方过热器管内表面(焊缝热影响区),由内壁向外并向长度方向扩展,见图2。宏观断口显示,裂纹是多源的,较长的裂纹是由几处小裂纹扩展相聚而长,主裂纹两侧还有与之平行的若干条小裂纹,因此,断口上存在台阶和复合断面。过热管破裂区及其附近,壁厚减薄及变形不明显(见表1),属脆性开裂。破裂面上覆盖有黑色附着物(包括腐蚀产物)。此外,焊缝存在局部咬边、气孔、未焊透等缺陷,富通新能源销售生物质锅炉,生物质锅炉主要燃烧木屑颗粒机压制的木屑生物质颗粒燃料。
2.3过热器管破裂区化学成分分析
2.4过热器管材料室温力学性能试验
从直管试样上取拉伸试样,在Instron电拉上做抗拉试验,结果见表3。
2.5过热器管金相分析
从发现破裂的弯曲管裂纹附近取样进行金相分析,观察显示:过热管母材组织为铁素体+珠光体,具有明显带状特征;焊缝金属组织为先共析铁素体+针状铁素体+少量贝氏体;过热区组织为粒状贝氏体;正火区组织为细块状铁素体+珠光体;不完全正火区组织为铁素体+细珠光体一铁素体一马氏体群聚区。
由于过热管壁较薄,鳍片与钢管之间焊缝下方管内壁处于焊接热影响区,且大多处于不完全正火区,少量处于正火区。
由于不完全正火区中含有马氏体组织,此区中的马氏体为高碳马氏体(比过热区中经常出现的低碳板条马氏体更脆、更硬),它与原来未转变的铁素体和部分未转变的珠光体等形成很复杂的混合组织,结果导致性能变得很脆。这己为测得的显微硬度数据(HV0.05 - 467:不完全正火区显微组织中马氏体或马氏体群聚区显微硬度)和宏观硬度数据(表4数据为焊接接头区宏观硬度分布,不完全正火区硬度为包括马氏体、马氏体群聚区及其它组织在内的较大范围硬度平均值,不完全正火区硬度在整个接头区中最高)所证实。
2.6过热器管裂纹金相分析
观察显示,裂纹起始于焊缝下方过热器管内表面,观察的四条裂纹中三条裂纹起裂点处于不完全正火区,一条裂纹起裂于正火区;其中三条裂纹终止于焊缝,一条裂纹止于正火区。裂纹在不完全正火区和正火区为穿晶扩展,在过热区和焊缝金属中基本沿晶扩展。
2.7过热管裂纹附近硬度测定(见表4)
2.8断口扫描电镜分析
低倍观察,裂纹扩展迹线由管内壁向外发散,从微观形貌上证明裂纹起始于管内壁,由于断口表面覆盖有黑色附着物,断口细节难以看清。
2.9 断口复盖物微区成分分析
对几处裂纹面(断口)复盖物成分进行分析表明,复盖物中含有一定量的Na(0.41%)、S(0.99%)、Al(0.31%)、Cu(2.42%)、Si(0.35%)、Mn
3、讨论
3.1过热器管破裂性质
根据裂纹位置、形态及过热器管经历看,裂纹属脆性开裂;裂纹在点火试运行过程中有扩展,属动态裂纹。从裂纹起始于焊接接头最脆区,且起始阶段为穿晶扩展,可认为至少部分宏观裂纹由焊接或弯管过程中形成的穿晶小裂纹扩展而成。从裂纹起始于管内壁,多源,裂纹起裂并扩展一段后即转变为沿晶扩展,裂纹多分枝,裂纹集中于弯管区,显示裂纹具有应力腐蚀开裂特征。从裂纹面上残留NaOH,证实裂纹属碱应力腐蚀开裂。
3.2过热器管破裂原因
鉴于破裂均发生于过热器弯管段焊接区;均起(0.40%)、Cr(1.29%)等。始于过热器弯管段焊接区下侧管内壁,加之过热器管破裂的其它特征(多源,多分枝,脆性动态扩展等),因此,可认为过热器管的破裂与焊接过程、弯管过程、管内介质密切相关。
在过热器管相应材质(15CrMoG,淬硬性强)、结构和焊接工艺(钢管与翅片之间通过埋弧自动焊相连)条件下,不完全正火区中出现非常脆硬的高碳马氏体,或含有高碳马氏体的复杂混合组织,这为开裂提供了材质条件。过热器管的弯曲加工过程,导致焊接区管内壁(特别是弯管下侧焊接区管内壁)产生很大的拉应力,与焊接残余应力、工作应力迭加后成为过热器管开裂的力学条件。过热器弯管下侧焊接区管内壁某些脆性组织在弯曲过程中可能引发脆性开裂(脆性组织、弯曲冷作硬化、弯曲和焊接残余应力迭加作用的结果),形成一些微裂纹,为应力腐蚀开裂提供裂源并成为集聚的区域。
过热器碱洗过程中,上述存在脆硬组织、迭加残余应力、脆性微裂纹的弯管段下侧焊接区管内壁就可能产生碱应力腐蚀开裂或原脆性微裂纹以碱应力腐蚀开裂机制而扩展。过热器管裂纹沿晶扩展及断裂面上附着有NaOH痕迹,一定程度上支持了碱应力腐蚀开裂或扩展的提法。
离汽包最近的弯管区是碱洗过程中碱水或含碱蒸汽容易到达的地方,但因碱洗后的处理使断口上残存的碱大为减少。
4、处理措施
对已经严重开裂的过热器弯管部分应加以更换,重新制作的弯管部分应作消除应力热处理,以避免焊接裂纹、弯管开裂及应力腐蚀开裂。
厂方重新制作的弯管段完成鳝片焊接后,弯管前和弯管后都作了消应力热处理,弯管前热处理的目的在于消除焊接残余应力和改善接头区组织,避免焊后和弯管过程中开裂;弯管后热处理在于消除冷作产生的残余应力和材料硬化,以提高弯管部分抗碱应力腐蚀开裂的能力。经过改进后制作的顶棚过热器已安全运行半年以上。
5、结论
(1)顶棚过热器多处开裂均发生在离汽包最近的弯管区,且起始于过热器弯管段鳍片下侧焊接区管内壁,属碱洗过程中引发的碱应力腐蚀开裂;
(2)弯管段鳍片下侧焊接区管内壁存在高脆性高碳马氏体,焊接和弯管过程产生的残余应力,碱洗过程中高温碱水或碱蒸汽的侵入、弯管过程在内壁高碳马氏体区诱发微裂纹等为上述过热器管应力腐蚀开裂提供了必需的条件;
(3)重新制作时,弯管段完成焊接后,弯管前和弯管后都作了消应力热处理,由此解决了上述过热器管应力腐蚀开裂问题。