
生物质锅炉新闻动态
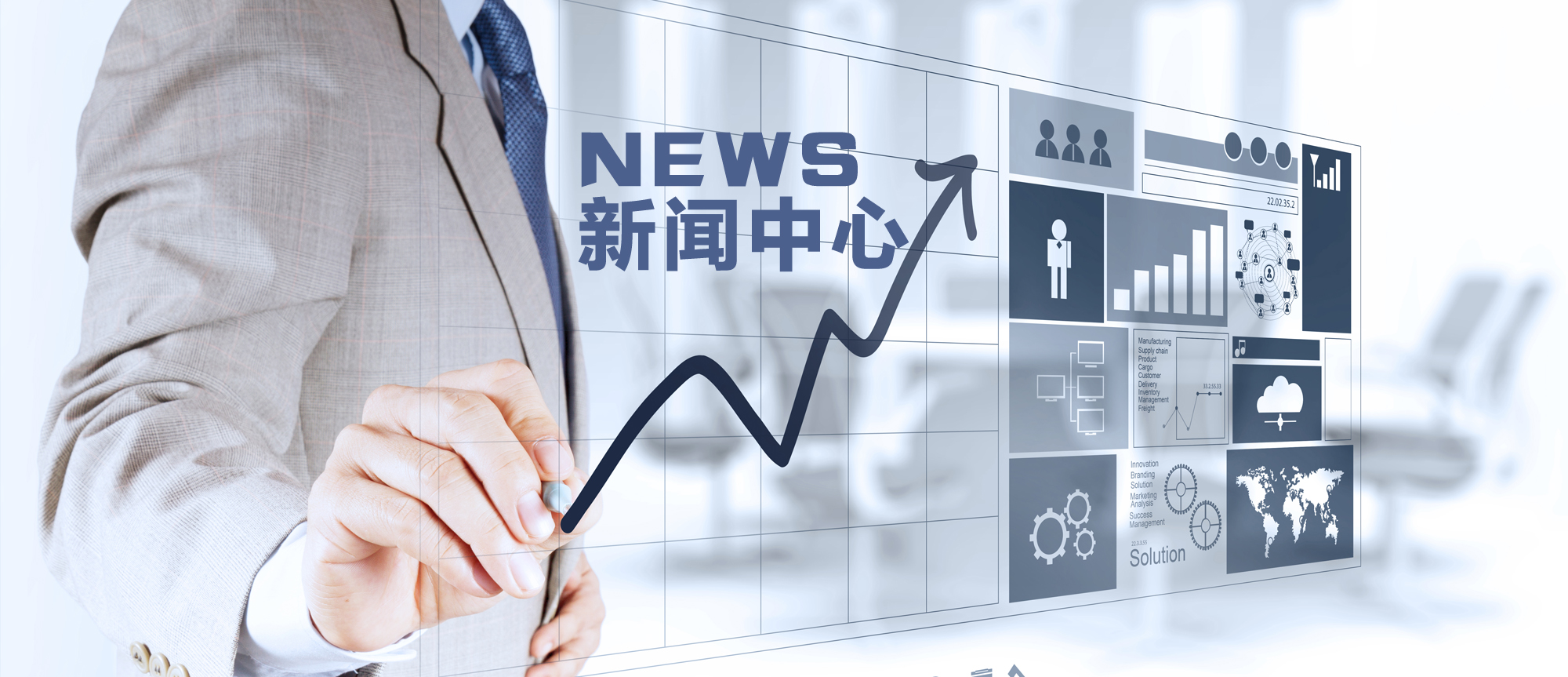
富通新能源 > 动态 > 生物质锅炉新闻动态 > > 详细
75t/h煤粉与高炉煤气混烧锅炉存在问题及改造
发布时间:2013-06-21 10:45 来源:未知
1、前言
贵州某钢厂动力分厂的75 t/h煤粉与高炉煤气混烧锅炉,存在飞灰可燃物及排烟温度较高、排粉机磨损严重等问题。为改善锅炉运行状况,提高锅炉运行的安全性和经济性,决定对锅炉进行技术改造。
高炉煤气(BFG)是炼铁的付产品,主要可燃成分是CO,不可燃成分是惰性气体、C02及N2。CO的体积成分一般在30%左右,发热量不高,一般低位发热量为3 000~4 000 kj/m3。由于高炉煤气内含有大量氮气和二氧化碳,燃烧温度低、速度慢,燃用困难。而生产生活中需要的蒸汽负荷与炼铁中产出的高炉煤气随时间变化的规律不一致,为满足生产经营的要求,最经济的方式是实现掺烧高炉煤气。然而,高炉煤气和煤粉是两种性质完全不同的燃料,要想让两者都能得到充分的燃烧,需要考虑炉膛热力参数、燃烧器的结构与炉内空气动力工况、锅炉运行参数等诸多因素。
2、燃料及设备简介
该锅炉为B&WB-75/3. 82-MQ型锅炉,主要设计参数如下:额定蒸发量75t/h,过热蒸汽压力3. 82 MPa,锅炉工作压力4.22 MPa,过热蒸汽温度450℃,给水温度104℃,排烟温度180℃.锅炉设计热效率87.35%,燃料种类为煤、高炉煤气混烧;燃消耗量9604 kg/h。锅炉制粉系统为中间储仓,乏气送粉,燃烧器四角布置切向燃烧,分为煤粉燃烧器和高炉煤气燃烧器,煤粉燃烧器一次风分散布置,高炉煤气燃烧器为半预混式。
炉膛断面尺寸为:5450 mm x5450 mm。假想切圆直径∮550mm。
表1和表2分别为该锅炉设计的煤粉和高炉煤气的成分及有关参数。
富通新能源生产销售生物质锅炉,生物质锅炉主要燃烧木屑颗粒机压制的生物质颗粒燃料。
3、存在问题及原因分析
该锅炉长期存在飞灰可燃物较高、排烟温度较高、排粉风机磨损严重等问题。通过改造前的冷态试验以及长期的运行经验表明,其主要原因在于高炉煤气的掺烧量较设计值高了很多,具体原因分析如下:
3.1 高炉煤气的掺烧量对燃烧的影响
从表1和表2煤粉和高炉煤气的成份分析可以看出,高炉煤气的热值比煤粉的低位发热量低得多,这样,当高炉煤气的掺烧量增大后,炉内混合燃料的发热量就会降低,经计算可以得出高炉煤气的不同掺烧量下,混合燃料的低位发热量见图1所示。随着高炉煤气的掺烧量不断增大,混合燃料的低位发热量下降很快,从而导致炉膛温度水平的显著下降,严重影响炉内煤粉的燃烧。从图1中可以看出,当煤气热量掺烧比从0%增加到30%时,混合燃料的发热量就从18.175 MJ/kg下降到7.36MJ/kg。
另外,高炉煤气燃烧时的理论燃烧温度比高热值的燃料低得多,一般烟煤、油和天然气的理论燃烧温度约1 800~2 200℃,而高炉煤气的理论燃烧温度为1 149℃。由于高炉煤气的理论燃烧温度低,因而炉内火焰的辐射能力较弱,与烟煤相比,相同条件下高炉煤气的炉内传热能力约低59%。因此炉膛的吸热能力减弱,更多的热量只能在锅炉的过热器和再热器等部分被吸收,从而容易造成炉尾的烟气超温以及排烟温度较高。
3.2 高炉煤气的掺烧量对炉膛烟气的影响
高炉煤气量增大以后,送入炉内的吸热性介质增多,烟气的热容量增大,火焰中心的温度水平下降,火焰中心的位置上移,导致煤粉在炉内的停留时间缩短,从而造成煤粉的不完全燃烧。掺烧比越高则烟气量越大,热焓越高流速也越高,但传热系数和烟速的0. 64~0.8次方成正比,所以锅炉排烟温度随高炉煤气的热量掺烧比的增大而升高,实际的排烟体积增量因为温度的修正而更大。
3.3高炉煤气的掺烧量对飞灰可燃物含量的影响
高炉煤气的掺烧量增大后,混合燃料的理论燃烧温度降低,严重影响了炉内煤粉的燃尽;高炉煤气在炉内的燃烧滞后,因此在炉内抢夺与煤粉燃烧的空气,也造成煤粉的不完全燃烧,从而增大了飞灰可燃物的含量;另外,炉膛烟气量的增加,导致烟气在炉膛内的流速增大,煤粉在炉内的停留时间缩短,也影响了煤粉的燃尽。特别是当高炉煤气的掺烧量较大时,存在的大量惰性气体阻碍可燃成分与空气的充分混合,减缓燃烧化学反应速度和火焰传播速度,使炉内的高炉煤气“抢风”,导致煤粉燃烧初期的氧量不足,从而增大了飞灰可燃物的含量,如图2所示。从图2中可以看出,当高炉煤气的掺烧量低于22000m3/h时,飞灰可燃物可以控制在10%以内,当高炉煤烧量大于35000m3/h时,飞灰可燃物含量一般都大于20%。
3.4该炉投入运行后,煤粉掺烧发生了较大的变化,导致制粉系统出力不足,以及排粉风机磨损严重的问题。
4、改造措施
通过以上的分析,可以看出,高炉煤气的掺烧对炉内燃烧产生了很大的影响,因此对该锅炉的改造应针对高炉煤气的特点进行。当大量混烧高炉煤气时,由于高炉煤气的热值低,在炉膛底部燃烧释热极少,当遇高温煤粉火焰时,大量高炉煤气才开始充分燃烧,燃烧放热集中在炉膛的中上部,造成炉尾烟气超温。对锅炉的安全运行造成威胁。针对这种情况,其改进方法可考虑强化高炉煤气在锅炉炉膛底部的燃烧,使锅炉高温带下移。措施是使燃烧器尽量下移,由于实际位置的限制,对于煤粉燃烧器部分,标高相比改前下移180mm,对于煤气燃烧器部分,标高未能下移,煤气燃烧器结构、尺寸等未作改动;另外,由于高炉煤气掺烧量的影响,导致炉膛燃烧温度下降,造成煤粉的不完全燃烧,飞灰可燃物增大,以及燃烧效率下降,采取的措施是,强化煤粉的燃烧,应用稳燃腔煤粉燃烧器。即在两个一次风前加装稳燃腔煤粉燃烧器以强化着火、稳定燃烧。稳燃腔燃烧器是将一个三棱柱钝体置于一腔体内,腔体与一次风管连接,如图3所示。稳燃腔燃烧器的原理及特点请参阅参考文献。
5、改造效果
对锅炉进行上述改造后,经运行证明,燃烧很稳定,无论高炉煤气的掺煤量是多大,都能保持锅炉的负压运行。另外,锅炉带负荷能力很强,在高炉煤气的掺烧量较高的情况下,飞灰可燃物及排烟温度比改造前大大降低。
(1)锅炉带负荷能力
试验发现,该炉运行时的带负荷能力很强,可大大超锅炉的额定出力,纯烧气时,54 000m3/h的气量可带50 t/h,配合4台给粉机运行可带80 t/h。从试验数据分析,每10 000m3/h的气量可带约8.5t/h的负荷。
(2)锅炉燃烧效率的明显改善
对锅炉改造前和改造后的试验数据取纯烧煤粉和高炉煤气的热量掺烧比为25%这两种工况进行对比分析,见表3示。
从表3可以看出,锅炉改造后的燃烧效率比改造前有了明显的提高。
(3)运行建议
当高炉煤气的掺烧量在10 000~ 20 000m3/h之间(即热量掺烧比在14%~28%之间)时,锅炉的飞灰含碳量可以控制在8%以内,燃烧效率最低降到88%。属于比较理想的混合燃烧。
当高炉煤气的掺烧量大于20 000m3/h时,飞灰可燃物明显增加,锅炉燃烧效率的显著下降,建议该锅炉的高炉煤气掺烧量控制在10 000~ 20 000m3/h之间,如果有剩余的高炉煤气,考虑其他锅炉的掺烧。这样,既可以保证锅炉的稳定高效燃烧以及高炉煤气的合理使用,也可以创造更好的经济效益。
6、项目经济效益核算
该项目总投资574万元,其中设备费198万元,仪表、自控系统102万元,施工(包括主材等)254万元,其他20万元。
创造效益:
直接经济效益
每年减少高炉煤气放散:
5.4x24x365 x90%=7 884万m3/a
按发热量折合动力煤:
1.8 x7 884=14 191 t/a
1.8为煤气折合动力宽系数。
降低锅炉灰渣含碳量10%(由原来的30%下降到20%)节煤:4.5x30%×33%×24×365×90%=3512t/a
4.5为锅炉小时用煤量,30%为原煤含灰量.33%为灰渣含碳量下降百分比,90%为锅炉运行率。
创总效益:
(14 191+3 512)×104.8=185.5万元/a
(2)间接经济效益
锅炉改造后燃烧稳定,适应煤种和负荷能力强,满足生产蒸汽的需要,解决了煤资源相对不足的问题。高炉煤气使用量达到5万m3/h(掺烧比例为60%),飞灰含碳量在掺烧比例30%以下时低于20%,便于实现灰渣的综合利用,有一定的环保效益。同时减少动力煤消耗量,相对提高了喷煤能力,为高炉创造了一定的间接效益。
7、结论
(1)随着高炉煤气的掺烧量增加,混合燃料的低位发热量、理论燃烧温度都下降,导致煤粉的不完全燃烧,飞灰可燃物含量上升,锅炉效率下降;另外,烟气量增大,烟气在炉膛内的流速增加,煤粉在炉内的停留时间缩短,也造成煤粉的不完全燃烧,锅炉的燃烧效率下降。
(2)正确选择和布置燃烧器对形成良好的空气动力场至关重要。
(3)综合考虑各种影响炉内燃烧的因素,我们认为高炉煤气的最佳掺烧量为10 000~ 20000m3/h之间,既可以保证锅炉的稳定高效燃烧以及高炉煤气的合理使用,也可以创造更好的经济效益。