1、引言
烘炉技术并不是一种新型技术,其产生的年代可以追溯到重型炉墙的烘烤。随着锅炉技术的发展,煤粉炉普遍采用了轻型炉膛的结构,使烘炉技术开始变得鲜为人知。但随着近几年循环流化床锅炉的迅猛发展,为了克服循环流化床锅炉普遍存在的磨损问题,对炉墙中耐火耐磨浇注料、耐火保温浇注料、耐磨耐火砖以及耐火保温砖性能指标要求也越来越严格,烘炉技术又获得了广泛应用,并有了新的发展。为了降低锅炉炉墙中耐火耐磨浇注料等材料所含的水分,需要在正式点火前将浇注料的水分排除,实现烘炉的目的,为将来锅炉安全稳定运行打好基础,富通新能源生产销售生物质锅炉,生物质锅炉主要燃烧木屑颗粒机压制的生物质颗粒燃料。
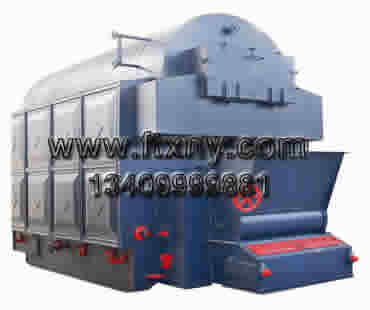
2、1#锅炉烘炉实践
2.1锅炉简介
唐山市某公司热电站一期工程共安装3台35t/h循环流化床锅炉,配置2台6MW抽汽凝汽式汽轮发电机组。该锅炉系太原锅炉集团有限公司设计制造的中温、中压、单锅筒、自然循环、Ⅱ型布置的燃煤、燃气混烧循环流化床锅炉。锅炉炉膛为全膜式水冷悬吊的封闭结构,采用高温旋风分离器作为分离元件,分离器位于炉膛出口和尾部竖井烟道之间,旋风筒为中部支撑结构。高温过热器布置在水平烟道内,低温过热器、省煤器和空气预热器布置于尾部竖井烟道中,过热蒸汽温度调节系统采用喷水减温。
1#循环流化床锅炉由北京电力建设安装公司安装完毕后,于2006年8月24日开始烘炉。9月12日进行煮炉,做完各种试验后,9月16日点炉投入试运。9月18日因锅炉结焦停炉处理,在此期间发现返料器处有浇注料脱落现象。
2.2问题分析
经调查分析后认为造成浇注料脱落主要有以下原因:
(1)烘炉前部分热工仪表没有投入运行,DCS系统没有完善;
(2)没有对旋风分离器处采取专门措施进行烘烤;
(3)施工单位在烘炉过程中没有严格按筑炉材料厂家提供的升温曲线进行升温。
针对此问题,对2#、3#循环流化床锅炉的烘炉工艺和方法进行改进。
3、烘炉工艺及改进方法
耐磨耐火材料施工配方及对烘炉过程的要求一般都由材料供应厂商决定,并提供烘炉曲线图,但厂家不考虑具体的烘炉手段。而常规的烘炉方法经常无法满足材料厂商所给定的烘炉指标甚至造成材料损坏,这样就形成了烘炉的技术空缺。随着流化床锅炉的大型化,提高耐磨耐火材料性能及其经济安全性,使得烘炉技术的研究显得尤为重要。
3.1烘炉及系统应具备的条件
在烘炉前应完善以下工作:
(1)锅炉本体的安装,炉墙及保温工作已结束,炉墙漏风试验合格;
(2)锅炉衬里工作全部结束,打开各处人孔门,自然干燥100~200h以上;
(3)炉膛、烟风道、旋风分离器、空气预热器及除尘器内部检查完毕,杂物清理干净;
(4)锅炉膨胀指示器安装齐全,指针调整至零位;
(5)锅筒内部装置安装结束,锅简水位计水位标志清晰、正确,照明良好;
(6)向锅炉上软化水或化学除盐水至正常水位,水温50~60℃并将水位计冲洗干净;
(7)锅炉启动前调整主蒸汽排汽和放水,主蒸汽排汽打开:
(8)锅炉所有电动门、风门挡板、调节门等调整完毕,开关方向正确,开启准确,动作灵活,具备投运条件。一、二次风机及引风机调试完毕,具备投运条件;
(9)烘炉前应做好试块放人锅炉各部位,待烘炉结束后进行含水率分析;
(10)DCS烟温测量系统校准并具备投运条件;
(11)烘炉前,省煤器外护板不要密封焊,返料系统旋风分离器处适当位置割排气孔。开孔位置:沿高度方向及环形方向每米割∮30mm的排气孔,便于水蒸气排放,烘炉结束后再进行密封焊接。
3.2烘炉改进方法
对于循环流化床锅炉而言,炉膛卫燃带、风室、旋风分离器、返料腿及返料器等各部位的浇注料为关键烘炉部位。尤其是旋风分离器处,如果采用烘炉的方法不当会出现浇注料脱落现象,为锅炉日后运行埋下隐患。为保证旋风分离器处的烘烤质量,烘炉可采用如下方法。
3.2.1常规方法
(1)开始使用木柴烘炉时,烧柴日期约为6~7天,以后采用烟煤烘炉;
(2)采用木柴烘炉时,一般采用自然通风,以引风机进口调整,挡板调节维持炉膛负压,后期采用烟煤烘炉时,可启动引风机;
(3)为了保证旋风分离器处的温度,在烘炉结束后煮炉期间,用控制返料温度的方法,旋风分离器必须达到缓慢上升,最好温升为80~90℃/h,当返料温度达到350~400℃时运行1h后,压火降温,过3h后再升温,这样循环2~3次。杜绝升温太快,导致浇注料爆裂。
烘炉后期,温升应平衡,水分在7%以下为烘炉结束,可开始煮炉,煮炉结束时含水率不大于
2.5%,分析合格后,锅炉降压,烘炉结束。
3.2.2改进方法
(1)前两个步骤与常规方法相同;
(2)在返料器内堆放木柴生火进行烘烤;或在烘炉前将炉膛出口处用耐火砖(留部分出口)堵住,在烘炉过程中使部分烟气直接从返料口处经旋风分离器排出,使旋风分离器达到烘烤要求,当各部位的试块含水率达到要求后,烘炉结束。
3.3烘炉过程注意事项
(1)烘炉时,火焰应在燃烧室中部,勿使火焰偏斜或迫近炉墙;
(2)烘炉时,操作人员要严格按照筑炉材料厂家提供的烘炉升温曲线的要求,控制升温速度,不得出现温度过高或过低的现象;
(3)操作人员应每隔1h记录一次炉膛温度、旋风分离器进出口烟温、过热器出口烟温,并注意经常检查锅炉的膨胀情况,检查分离器外壁所开排气孔的排气情况。烘炉升温速率以炉膛出口的烟温为准,其他各点的温度仅作为参考;
(4)烘炉时,要监视水位保持锅炉的正常水位;
(5)烘炉时注意检查炉墙情况,不得有裂纹、凸凹等缺陷。
4、2#、3#锅炉烘炉技术关键
根据1#锅炉烘炉中出现的问题,在2#、3#锅炉烘炉中按以下技术要点进行。
(1)严格按照烘炉曲线控制烘炉质量,烘炉前期宜慢不宜快,严格控制烘炉升温速率和保证恒温时间。烘炉升温曲线如图1所示。
(2)加强烘炉监控手段,对启动燃烧器、回料阀、水平烟道等关键部位应根据实际情况适当增加温度测点,确保烘炉效果。对耐火材料的水分化验应及时充分,并根据化验结果调整烘炉工作。
(3)及时根据燃烧情况调整风量,保证配风合理,炉内温度稳定可控。
实践证明,在采取以上措施的情况下,于2006年11月20日对2#、3#炉开始先后烘炉。从烘炉后的检查结果显示,锅炉炉内耐磨耐火材料在整个烘炉过程和机组试运过程中没有发生1#锅炉出现的脱落、开裂、坍塌现象,证明烘炉效果良好,耐磨耐火材料经烘炉后其耐磨性、强度、耐火度、抗震性等指标达到了材料的技术要求,保证了耐磨耐火材料的使用寿命。
5、结论
循环流化床锅炉主体结构复杂,内衬材料施工面积大,且品种较多,如烘炉不当,锅炉运行中会因耐磨耐火等材料水分蒸发、膨胀等物理特性,而造成炉墙结构损坏和破裂,增加漏风量,影响锅炉运行的经济性,并会降低锅炉出力,缩短锅炉的使用寿命。因此,新锅炉投运前必须进行炉墙烘烤,并且要保证其烘烤程度。
实践证明2#、3#炉自2007年1月投运以来,炉墙保持完好,不但节约了大量的耐火材料并降低了维修维护费用,同时为锅炉长周期连续安全运行创造了有利条件。