
生物质锅炉新闻动态
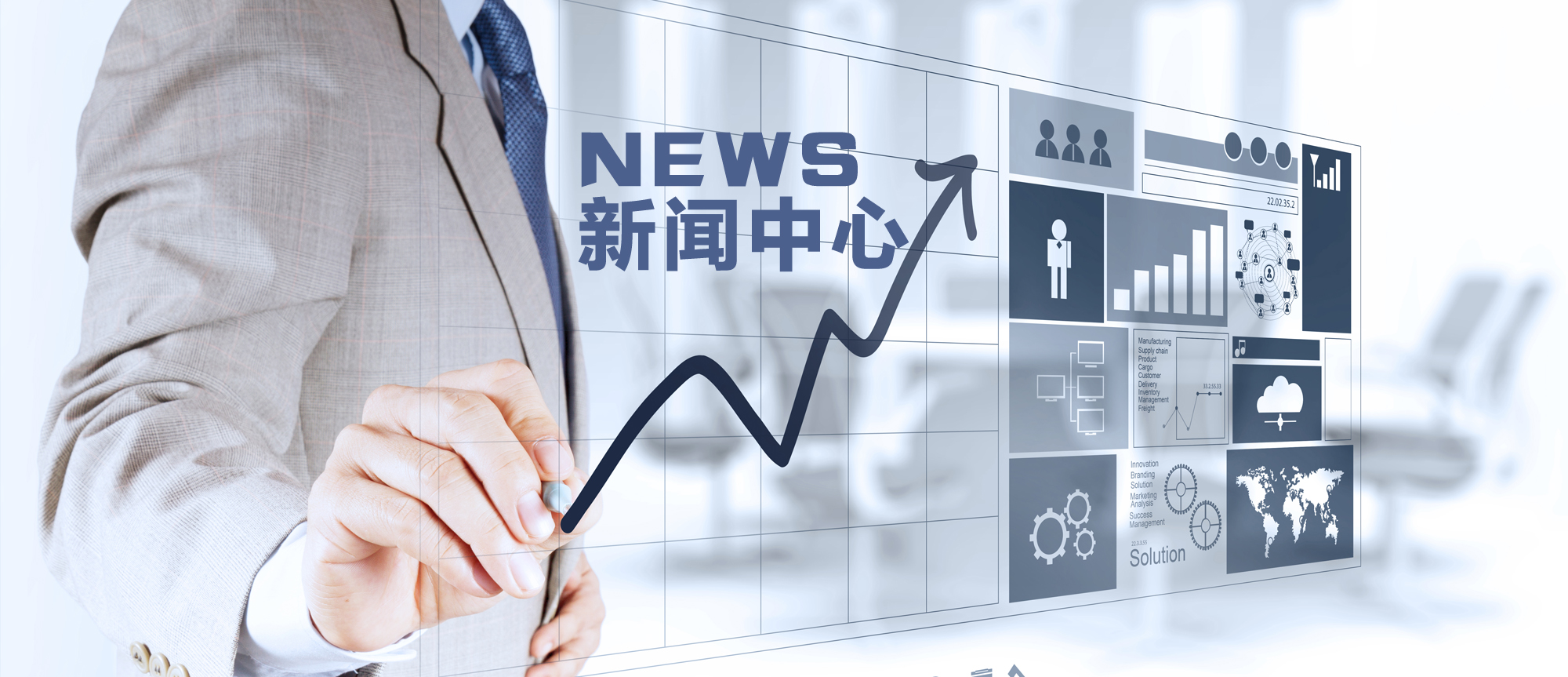
富通新能源 > 动态 > 生物质锅炉新闻动态 > > 详细
20t/h工业过热锅炉智能化自动控制系统
发布时间:2013-06-29 12:22 来源:未知
1、概述
工业锅炉是工业生产最重要的动力设备,锅炉生产的主要任务是:安全可靠、经济有效地把燃料的化学能转化为热能,生产出满足生产要求的蒸汽。工业锅炉是一种受压又直接受热的高压、高温特种设备,如果操作不合理、管理不善、处理不当,往往会引起事故;同时锅炉又是一种高能耗设备,因此确保锅炉安全运行至关重要,降低单耗也是锅炉经济运行的目标。随着锅炉不断向大型化发展,实现锅炉自动化是确保锅炉安全、稳定、经济运行的必不可少手段。
云南红塔蓝鹰纸业有限公司拥有两台容量为20t/h的工业锅炉,两台锅炉原已有检测仪表和控制设备,控制系统已运行10年(1988年投运),但困受当时电子技术限制,大部分仪表已不能正常工作,锅炉控制主要由工人进行。同时锅炉还存在一些需要急于解决的问题,主要表现在:(1)风量由风门调节,既浪费电能而效果很不理想,特别在停用蒸汽或少用蒸汽时,这种浪费尤为突出(有时浪费80%以上),风门关小,导致风门剧烈颤动和发出刺耳声音。(2)没有精确的检测仪表,人工操作困难,风量偏大热量浪费严重,风量偏小燃烧不充分,而煤质的经常变化,导致风量的不同需求。(3)由于锅炉容量大,需要严密监视,这必然增大工人的劳动强度;(d)因果用人工操作,汽包压力和汽包液位波动很大,对锅炉安全生产造成威胁。没有可靠仪表和测控手段,难以进行生产考核,难以实现优化控制。随着本公司对生产要求的不断提高,迫切需要用现代先进测控技术手段改造现有的锅炉作业过程,达到先进、可靠、实用、经济和便于操作和维护的目的,同时系统设计要便于以后扩展,富通新能源生产销售生物质锅炉,生物质锅炉主要燃烧木屑颗粒机压制的木屑生物质颗粒燃料。
2、主要测控参数及现场测控点
2.1主要测控参数
(1)炉膛温度的检测和控制。炉膛温度是工业锅炉生产运行的重要指标,通过对炉膛温度的检测,及时了解到炉膛中的燃烧情况,从而推断燃烧量、鼓风量和引用量的关系,并对有关量进行合理控制。
(2)蒸汽温度的检测和控制。蒸汽温度是生产工艺确定的重要参数(本锅炉要求为385℃一400℃),蒸汽过高会毁坏过热器水管,对负荷设备带来不利因素,过低会影响造纸效果。蒸汽温度可通过调节减温水控制。
(3)省煤器进、出口水温的检测。对省煤器进、出口水温的检测,是为了更好地了解省煤器的工作情况,防止省煤器管道结垢、发生堵塞现象或其它事故。
(4)省煤器进口和出口处烟气温度的检测。对省煤器进、出口处烟气温度进行检测,可监视省煤器是否正常工作,有无发生漏水和结垢现象,同时也能了解烟气通道是否畅通,以便充分利用低温烟气余热.降低排烟温度,提高锅炉热效率。
(5)空气预热器进、出口空气温度、出口烟气温度的检测。空气顶热器是利用锅炉尾部烟气热量加热锅炉膛燃烧所用空气的一种对流交换装置。检测空气预热器进、出口的空气温度,可随时了解空气预热器的预热效果和工作情况,根据预热空气温度的数值,可以推断空气预热是否有漏风、堵塞故障。空气预热器出口烟气温度的检测,能了解排烟温度是否达到规定标准,从而采取措施。
(6)汽包压力检测和控制。汽包压力是锅炉生产正常运行的主要参数之一,它既反映蒸汽量与燃料发热最的平衡关系,又是指导锅炉安全生产的重要依据。汽包压力过高和过低都不利于安全生产,汽包压力必须控制在工艺要求范围内。汽包压力控制可根据实际情况,通过控制蒸汽流量、、燃料量、送引风量加以控制。
(7)炉膛负压检测和控制。炉膛正常运行时,炉膛压力应保持在15 - 25Pa的负值范围内。负压过大,漏风严重,总风量增加,烟气热量增大,同时增加风机电耗。负压偏低,易造成炉膛向外喷火,不利丁安全生产。炉膛负压可通过引风机、鼓风机的风量合理配比控制。
(8)鼓、引风压的检测和控制。保持燃料量和送风量的合理比值关系,是保证燃料充分燃烧的基本条件。鼓、引风风量可通过鼓、引风风压间接检测,同时通过变频器来控制鼓、引风风机转速而控制。
(9)汽包液位及锅炉进水流量检测和控制。汽包液位是工业锅炉安全运行最关键的参数,关系到汽水分离速度和生产蒸汽质量。汽包液位太高,不利于汽水分离,同时威胁到过热器安全;汽包液位太低,容易造成“干锅”,也会威胁到对流管的安全。汽包液位必须控制在安全范周内。锅炉进水流量需要在线检测,以便实现汽包液位的稳定控制。
(10)除氧器液位、进水流量检测和控制。除氧器液位需要在线检测和控制,以确保有足够的水量供锅炉生产需要。除氧器液佗太低,不利于安全生产;太高也不利于除氧和易于造成溢出事故。除氧器进水流量需要在线检测,以便很好地控制除氧器液化。除氧器同样存在“假液位”现象,检测进水流量,可以实现前馈控制,从而实现除氧器液位的稳定控制;
(11)除氧器蒸汽压力监测和控制。除氧器蒸汽压力是确保除氧效果的重要参数。蒸汽压力增加时,氧气在水中的溶解度降低,但并非越高越好,应参考除氧器的水温度来进行蒸汽压力控制。
(12)除氧器温度检测和控制。除氧器温度是关系到除氧效果很重要的参数,温度一般控制在104℃。除氧器的水通过蒸汽来加热,其温度主要通过控制蒸汽量而控制。
(13)炉排速度控制。因现有条件制约,锅炉给煤量主要通过调节炉排速度来控制。速度快时煤量增大,速度慢时煤量减小。炉排速度不能太快,否则将会造成煤燃烧不充分。可采用滑差电机控制炉排转速来控制煤量,煤量是控制锅炉负荷量最根本的参数量。
(14)主蒸汽流量的检测。对作为工业锅炉终产品的蒸汽进行检测,以便于液位三冲量控制和生产考核。采用涡街流量计检测蒸汽体积流量,并结合温度、压力,可计算出蒸汽质量流量。
(15)炉排前拱、后拱温度的检测。对炉排前拱、后拱温度的检测和显示,可分析煤层的燃烧情况,以及燃烧中心的位置,以便根据情况进行调整。
2.2现场测控点
根据控制系统洲控内容和任务,本着先进、经济、实用、耐用的设计指导思想,对控制系统测控点作了精心选择。由于氧化锆探头需要频繁更换,且价格昂贵,控制系统没有采用氧化锆仪表进行氧份检测,但增加相应的控制方法。控制系统测控点如图1所示:
3、控制系统的结构
根据控制系统的设计指导思想,以及锅炉控制的实际需要,关键设备采用进口产品,其它则采用国产精品,尽可能降低成本,使性能价格比达到最大;因原有控制系统主机和现场仪表已损坏或严重老化,控制系统主机和现场仪表需要全部更换。现在两台锅炉轮流使用,即一用一备,为节省投资,两台锅炉共用一组变频器,在选定锅炉时进行信号切换和变频器输出切换即可。除变频器外,两台锅炉各没有独立的控制系统。系统硬件配置如图2所示(1#、2#锅炉配置相同,仅以一个控制系统为例),具体说明如下:
(1)采用三菱PLC作下位乇机,研化多媒体工业计算机作上位主机,构成集散控制系统,上位机负责系统管理,下位机负责系统控制。本系统的特点为:①分散控制,集中管理;②可靠性高、系统扩展方便;③支持PCI和ISA两种总线;④在Win-dows平台上运行,支持多媒体功能;⑤下位机可脱离上位机独立工作;⑥具有动画、语音等多媒体功能,人机界面更加友好,控制系统更加充满生气。⑦模块可任意组合,数据采集迅速,模拟信号为4
20mA,DI信号为24V DC,DO信号为220V AC。
(2)采用日本富士变频器控制风机、水泵的转速,本变频器具有性能可靠、价格适中、功能丰富、适应性强等特点;电动调节阀选用国产精品,一体化配置,安装简单,维护方便。
(3)采用日本横河公司的压力、差压变送器检测有关压力;同时通过差压变送器检测液面上、下两点的压力差,并结合不同温度下水的比重,算出液位。压力、差压变送器可通过手持电脑终端进行量程调整和校准。
(4)根据不同温度和条件需要,选用国产热电偶、热电阻,检测有关测点温度。1000—1700℃测点采用铂铑10 -铂热电偶,为使高温下不致套管软化和避免高温腐蚀,采用耐腐蚀、耐高温的刚玉套管;1000—500℃之间采用镍铬一镍硅热电偶(氧化铝套管),500℃以下采用热电阻(不锈钢套管)。
(5)选用H本横河公司高温型旋涡流量计检测蒸气流量,奉流量计耐温可高达400℃。因锅炉给水压力和温度较高(约105cc),选用普通型旋涡流量汁检测锅炉给水量。流量计可通过手持电脑终端进行量程调整和校准。
(6)选用国产一体化电动凋节阀控制水量,本调节阀既可由控制器、手操器控制,也可进行现场手动调节。
(7)为了防止强烈的电磁干扰,采用光电隔离调理模块.对炉排滑差电机的控制信号进行隔离,同时此模块可将4 - 20mA的PLC输出信号调理至0~ 10V,满足滑差电机对控制信号的要求。
4、上位组态软件及其开发
随着生产过程对工业自动化的要求越来越高,以及大量控制设备和过程监控装置之间的通讯的需要,“监控和数据采集系统”越来越受到用户的重视,从而导致自动化组态软件的在自动化系统中的大量使用。使用组态软件,可以提高自动化管理系统的性能,大大缩短开发周期,提高自动化系统开发效率。
4.1组态软件简介
采用北京亚控公司开发的Kingview组态软件作为控制系统的上位组态软件,进行控制系统上位软件的二次开发。Kingview组态软件主要由以下功能部分组成:
工程管理器:工程管理器主要用于工程的管理,如新建工程、搜索工程、工程的备份、工程的恢复、变量的导人导出、定义工程的属性等。
工程浏览器:工程浏览器是Kingview组态软件的核心部分和管理开发系统,它将画面制作系统中已设计的图形画面、命令语言、设备驱动程序管理、配方管理、数据报告等工程资源进行集中管理,并在一个窗口中进行树形结构排列,这种功能与Windows98操作系统中的资源管理器的功能相似。
Kingview画面开发系统:Kingview组态软件画面开发系统是应用程序的集成开发环境。工程人员在这个环境中完成界面的设计、动画连接的定义等。画面开发系统具有先进完善的图形生成功能;数据库中有多种数据类型,能合理地抽象控制对象的特性,对数据的报警、趋势曲线、过程记录、安全防范等重要功能有简单的操作办法。利用Kingview丰富的图库,用户可以夫人减少设计界面的时间,从整体上提高工控软件的质量。
画面运行系统TOUCHVEW: TOUCHVEW是Kingiew组态软件的实时运行环境,用于显示画面开发系统中建立的动画图形画面,并负责数据库与I/O服务程序(数据采集组件)的数据交换。它通过实时数据库管理从一组工业控制对象采集到的各种数据,并把数据的变化用动画的方式形象地表示出来,同时完成报警、历史记录、趋势曲线等监视功能,并可生成历史数据文件。
信息窗口:“组态王信息窗口”是一个独立的Windows应用程序,用来记录、显示Kingview开发和运行系统在运行时的状态信息。信息窗口中显示的信息可以作为一个文件存于指定的目录中或是用打印机打印出来,供用户查阅。当工程浏览器、TouchVew、I/O设备等启动时,一般会自动启动信息窗口。
Kingview5.1组态软件支持的硬件设备,已经由原来的数十种到现在的300多种,功能也日益丰富和强人。功能特点如下:
(1)全新中文Explorer界面,使用更加方便、更加灵活;
(2)真正32位程序,多任务、多线程,运行于Win98/NT平台,更加稳定、更加可靠;
(3)采用OLE自动化技术,将组态王和驱动程序整合到一起,采样速度快,可靠性高,保证不丢失任何重要数据;
(4)新增立体管道、透明点位图、多种动画控件,生成画面更加逼真、美观;
(5)增强的多媒体功能,支持语音报警,视频输出;
(6)支特AetiveX控件,增加温控曲线、x-Y轴曲线,列表框等几十种功能控件;
(7)集成近二百种驱动程序,支持国内外流行的31种PLC(Siemens、Modicon、OMRON、三菱等),11种智能仪表(欧陆、岛电、理化、神王、字光等),6大类智能模块(牛顿7000、ADAM4000等),约150种板卡(中泰、研华、威达华控、研祥、磐仪等),还有多种变频器,支持的驱动程序种之多,居各类组态软件之首;
(8)驱动程序自动配置向导,引导您连接各种硬件没备;
(9)配方管理、美观的实时报表和历史报表:
(10)内容丰富的在线帮助系统,引导迅速掌握组态王5.1;
(11)直接支持TCP/IP及串口互连网,分布式历史数据库.掏造企业级信息共享更容易;
(12>操作员Ll令保护,操作过程记录,安全级达999级;
(131强人的双机热备功能使您的系统更加可靠;
(14)新增ODBC接口,支持SQL Server,可与任何标准的数据库进行数据交换;
(15)新增OPC接口,可与任何拥有该接口的系统进行通讯。
4.2组态软件开发
Kingview组态软件进行控制系统软件开发的主要步骤为:
①创建控制项目工程,进行下位机AIS PLC和FX2N PLC的创建和组态。包括设备地址、通倍方式、通信口等的组态;
②创建变量数据库。这是上位软件的核心之一,数据变量必须正确,才能实现要求的功能。数据变量按来源分,可分为内部变量和外部变量;按性质来分,可分为:离散变量、整型变量、实型变量和字符串变量。根据实际情况进行组态;
③监控画面的开发。控制系统的所有数据、运行过程等需要通过画面反映出来,本部分的开发一方面反映开发人员的水准,另u-方面,包括图形、数据显示或设定、控件操作、趋势图等的开发;
④命令语言编程。为了实现各种需要的功能,单依软件控件的功能远远不够,需要对操作项逐个进行编程。Kingview组态软件的命令语言与C语言格式相似。
⑤报表开发。Kingview组态软件支持与EXCEL的连接,可通过EXCEL进行复杂报表的编写。
5、结论
(1)采用PLC与工业计算机组成的集散式控制系统,实现了分散控制、集中管理,控制系统性能可靠,功能丰富。
(2)采用二线制检测仪表,减少了布线量和线路故障,提高了系统抗干扰能力,检测数据精确。采用智能电脑终端,仪表调试更加方便。
(3)采用变频调速技术及相应合理的控制方法,节能可观。经3年的生产考核表明,节能42.8%.节煤5.6%。排烟、排渣连续这标。
(4)系统设计充分考虑可能出现的情况,同时具有相应的手段,使系统更加可靠安全。采用高性能电动调节阀和相应的改进技术,稳定性好,无泄漏,调节灵活。
(5)对传统的PID控制算法作了改进,增加了判断和处理程序,具有智能化,可避免控制回路在非正常情况下的误动作,增加了控制回路的可靠性、灵活性和稳定性。
(6)汽包液位采用二冲量串级控制技术,克服了“假液位”难于控制的难题,液位控制及时、稳定性好;与其它三冲量串级控制不同的是,回路PID控制器都为独立型增量控制,各控制回路输出信号可进行算术运算,并对计算结果作限定。
(7)炉膛负压采用智能PID串级控制技术,当鼓风量改变时,引风量也自动作相应的调节,始终保持炉膛负压稳定。调节迅速、控制品质好。
(8)除氧箱液位采用前馈PID串级控制算法,解决丁“假液位”难于控制的难题,对“假液位”f:扰不敏感,稳定性好。除氧箱压力、温度控制,采用模糊控制与智能PID串接的控制技术,除氧箱,E力和温度互为控制目标,也取得了很好的的控制效果。
(9)采用光电隔离和信号调理技术,避免炉排控制器对Pl,C的强烈干扰+实现了PLC对炉排速度的控制:
(10)以汽包压力为控制目标、炉膛温度为控制参考,通过模糊控制器对鼓风和给煤控制回路的管理,实现送风和给煤的合理自动控制,实现锅炉作业的全自动控制。达到了节能降耗的目的。
(11)在具有硬件操作面板以供备用的同时,提供了“软控件”的操作面板,使调节更加简单方便和精确。
(12)丰富的功能,精美的画面、方便的操作,使操作人员能方便及时地了解锅炉运行工况,对锅炉的生产管理方便及时。提供实时趋势,能方便地了解各参数目前和过去的变化情况,为生产管理提供强有力的手段。
(13)具有实时在线调试功能,为系统调试和参数修改提供方便。
(14)具有多媒体功能,提供语音报警。提供实时报警和历史报警窗口,和提供对历史数据的检索功能。系统启动简单、显示直观、操作简单、维护方便。
(16)充分利用PLC的特点,采用线性补偿、温度与压力修正技术,使检测数据更加精确。