3.3控制系统结构
5号炉LCS具有开放式的系统结构,能够适应现场恶劣环境,而且系统具备了双机热备的功能,保证了系统运行的可靠性。本系统的结构正是吸取了DCS在过程控制中的诸多优点,在使用简易,控制效果明显,并突出经济效益的目标下,设计出基予PLC的3层控制结构的控制系统。系统结构如图3所示:
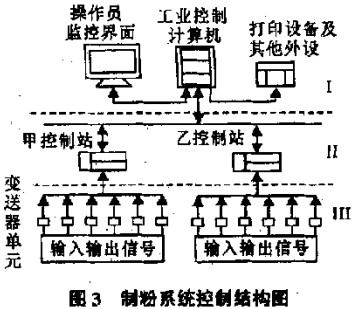
系统的3层结构分别是:
①工业控制计算机为服务器的操作员站I,服务器被安装在后台的控制柜中,前端连接显示器为操作员显示监控界面。服务器的主要功能是与第2层的控制器进行通信,一方面控制器将采集和处理后的信号量传送给服务器用作显示与控制计算,另一方面服务器向控制器发送控制参数与信号;同时,服务器还承担着记录数据的任务,服务器实现自寻优控制算法功能。
②执行控制功能与信号采集处理功能的执行器站Ⅱ。执行器站由2个PLC站组成,与操作员站I通信,同时与现场信号空进器连接。控制站专门执行控制功能:其输人为磨音信号、出人口压差、出口温度、球磨机电流、入口负噩和排粉机电流.输出信号则为控制给煤机电流变化的信号和控制风门变化的信号。
③最下面一层是现场信号层Ⅲ。该层由传感器采集系统所需各种信号.然后送人变送器,由变送器特这些信号转换成标准的4~20 mA的模拟信号供第2层使用。控制系统程序流程图如图4所示。
4改造后的调整试验及效果分析
4.1改造后的调整试验
改造后的调整、试验由电厂配合某公司调试人员进行。首先分步测试了系统各控制程序单独运行情况,主要有给煤控制程序、出口温度控制程序和人口负压控制程序,单独调试情况正常。
当磨煤机负荷实现定值控制后,影响磨煤出力的决定因素就在钢球量的调整上。根据预定的钢球装填办法:按直径40 mm,50 mm.60 mm以上3种规格的钢球,装载总量控制在16 t.钢球级配按3,4,3的比例进行称量装载。实际单台磨初装钢球量为14.5 t(其中直径40 mm左右钢球4.5 t,直径50mm左右钢球8t,直径60 mmn以上钢球2 t)。运行调试过程中,为提高磨煤出力先后分4次加入2.5 t直径60 mm以上钢球,此时总装球量为17t,对应的磨煤机运行电流为29 A左右。
乙磨煤粉细度(R90=31%(左右)高于甲磨煤粉细度(R90=25%左右),且乙磨煤粉均匀性n值偏小(0.7~0.8),分析原因可能是由于初装钢球时小球比例偏少,因此对原煤的碾磨作用不足,根据实际钢球的磨损情况,于11月25日向乙磨加了1t小球和1t大球,运行电流保持在29 A左右。根据实际化验结果,等磨运行电流下降到28 A左右时,叉向乙磨舔加小球1t,效果比较明显。最后煤粉细度均控制在R
90=2696左右(排粉机风门挡板开度为35%)。运行1 d后,逐步投入了出口温度控制程序和^口负压控制程序。6d以后,运行过程中出现出口温度瞬间高跳变,造成了热风门全关,冷风门全关现象,自动被迫解列。经过检查分析,最终判定由二次仪表变送的出口温度信号,在瞬间有跳变,造成控制程序认为温度超过80℃的保护动作值,制粉系统连锁保护动作。于是将出口温度控制程序的出口温度判定条件加入了限定条件:如果瞬间采集信号超过80℃,热风门自动输出保持前一输出值不变,如果2s后温度仍然保持80℃,连锁保护动作。后经30 d运行,此故障再没有出现过。
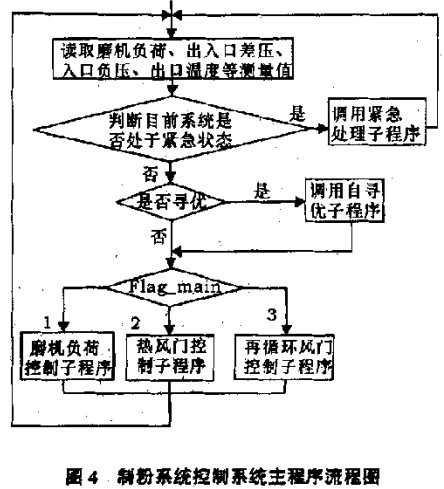
4.2改造后的效果分析
①项目实施后,经过优化调整,单台磨煤机内装钢球量在21t左右,2台磨较以往减少了2.5~3 t,但磨煤机制粉出力平均每小时提高了6t,与去年同期同负荷情况下相比,提高了制粉出力15%,加快了制粉速度,缩短了制粉系统的运行时间,平均每班缩短40min左右,磨煤机垒天停运时间平均延长了2.8 h。自动投入后,制粉系统能持续稳定运行,减少了人为干预控制.,均匀给煤,杜绝了满磨堵煤和空磨损耗,无形中增加了整个系统运行的安全性。调整后90 d的平均值与调整前90 d同期平均值对比见下表。
|
钢球量/t |
平均每天制粉时间/h |
平均每天停运时间/h |
平均制粉出力/t·h-1 |
减少运行时间/h |
甲磨 |
调整前 |
22.00~22.50 |
14.60 |
9.40 |
19.23 |
|
调整后 |
20.50~21.00 |
11.80 |
12.20 |
22.41 |
2.80 |
乙磨 |
调整前 |
22.00~22.50 |
14.60 |
9.40 |
19.46 |
|
调整后 |
20.50~21.00 |
11.80 |
12.20 |
22.52 |
2.80 |
②调整运行后,煤粉细度平均比调整前提高约30%(R
90=26,R
200=8),煤粉均匀性指标咒值约为0.8,飞灰可燃物指标在6%以内,经过一段时间的运行后,锅炉燃烧状况良好,各项污染物指标均正常。调整后90 d的平均值与调整前90 d同期平均值对比结果见下表:
|
R200 |
R90 |
0.8≤n≤1.2(均匀性) |
飞灰可燃物/% |
甲磨 |
调整前 |
2.60 |
16.80 |
0.89 |
1.68 |
调整后 |
7.60 |
25.65 |
0.81 |
3.65 |
乙磨 |
调整前 |
2.80 |
16.90 |
0.87 |
1.87 |
调整后 |
8.10 |
26.47 |
0.79 |
3.79 |
n=2.884·lg(2-lgR
200)/(2-lgR
90)
n值是代表锅炉钢球配比、煤粉细度均匀性的重要指标.0.8≤n≤1.2比较合适。
③改造后,因为飞灰含碳量由原来的2%~4%提高到现在的4%一6%,原煤的浪费量有所增大,由飞灰含碳量倒推出多消耗的原煤量M的计算公式见式(1)。由公式(1)计算出的改造前后多消耗的原煤量比较表见下表。
|
Ay/% |
Chy/% |
B/Kg·h-1 |
Qyd/Kj·kg-1 |
全年浪费原煤量/t |
全年多消费原煤量/t |
2005年 |
21.88 |
2.50 |
21 |
22.054 |
87.06 |
|
2006年 |
21.88 |
5.50 |
21 |
22.054 |
191.46 |
104.40 |
M=(KA
Y×0.8C
hyB)/(100-C
hy)Q
yd
式中 A
Y煤的应用基灰分含量,%;
C
hy为飞灰台碳量,%;
B为每小时燃煤量,kg/h;
Q
dy煤的低位发热量,kJ/Kg;
K为碳的发热量,取K=32 886,kj/kg。
5改造后的效益分析
制粉系统经过一段时间的优化运行,其经济效益也明显体现出来。
①煤机内钢球总量减少2.5~3 t.磨煤机制粉出力平均每小时提高了6t,减少了制粉时间,既节约了钢球费用9 000元,又节约了制粉电量。
节约钢球的效益=(原钢球装载总量一现在钢球装载总量)×钢材市场价格-2.5x3 600元/t=9 000(元)
②制粉单耗也明显降低,往年同期制粉单耗平均为27, 51 kW/t,而现在制粉单耗平均只有21. 89kW/t,同比下降了约20%。以年均满负荷计算,每年仅制粉电量就可节约72×104 Kw/h,折合成出口电量(按0.27元/kW/h)计算,每年可节约资金21.8万元。锅炉年最大负荷平均运行小时数按6 000 h/a计算,满负荷每小时耗煤24 t。
年节电效益=(改造前年同期平均制粉单耗一改造后平均制粉单耗)×每小时耗煤量×锅炉年均运行小时数×上网电价= (27. 51 - 21. 89)x 24×6 000x0.27=218 505.6(元)
③改造后锅炉的飞灰含碳量由原来的2%~4%提高到现在的4%~6%.原煤的浪费量较2005年增大了104 t,多消耗原煤的费用为14 560元。多消耗的原煤费用;多消耗的原煤量×煤碳的市场价格- (191.46--87. 06)×140=14 560(元)
将一年中各项费用统计如下表:
节省钢球费 |
节省点亮费 |
多消耗原煤费用 |
总计节约费用 |
9000.0 |
218505.6 |
-14560.0 |
212945.6 |
通过费用对比,制粉系统改造后总的经济效益依然突出,利大于弊。
④制粉自动控制系统在设计阶段,就对制粉系统可能出现的事故状况提出了要求,因此对事故报警和保护比较完善,不仅保留了原设计图中的连锁保护,而且还针对可能出现的异常情况,进行一定范围的智能调整和保护,使运行人员能及时判l明情况;进行相应处理和调整,在一定程度上减少了人为干预。
⑤煤粉细度经过调整后,由R
90=2096提高到了R
90=2696,粉仓温度较以前也有了明显的降低,平均降低了2.5℃,对安全生产运行是非常重要的。
6结束语
由于采用先进的程序控制技术,对制粉系统各测点的数据进行采集和自动处理,对球磨机负荷实施自动控制、自动监测、自动报警和自动保护,使制粉系统始终工作在最佳工况。这样既提高了机组的自动化水平,降低了工人的劳动强度又保证了设备的稳定运行和经济运行;提高了制粉系统的安全性,减少了事故的发生率,最终实现制粉系统的安全高效、节能降耗。
三门峡富通新能源销售球磨机、雷蒙磨、雷蒙磨配件、雷蒙磨粉机等。