某集团是70年代末我国三大全套引进新型干法水泥生产线之一的淮海水泥厂,由罗马尼亚提供带双列四级悬浮预热器SP型3 000 t/d回转窑,窑型Ø5.8 m×97 m。1985~1989年投料生产期间,由于设计、装备质量缺陷,回转窑运转率始终徘徊在30%以下,1990年在原国家建材局局长率领下,经专家组进行技术论证,认为必须对这条生产线进行技术改造才能达产达标。故我厂下定决心在1991年底停产3个月实施窑系统技术改造。整个技术改造设计共分三大部分,首先取消窑尾垂直烟道原设计的“一把火”装置,在单系列预热器上增加1台MFC型窑外分解炉,其次对篦式冷却机改造,第三部分就是对窑系统电气自动化控制系统进行全面彻底的改造。改造后窑的熟料生产能力为3 500 t/d,自动化控制系统的故障由改造前占总故障停机时间的40%下降到目前的几乎为零,大大提高了回转窑的运转率。为了与窑系统运转率相适应,从1993年起,工厂依靠内部技术力量,自己设计、施工、调试,陆续对全厂其它重点工序的自动化控制系统进行了彻底改造,使我厂从70年代的自动化控制装备技术水平一跃成为90年代技术装备水平。1999年在回转窑77.9%运转率情况下,熟料产量96万t,水泥产量130万t,电气自动化控制设备有效运转率达99%。目前回转窑已超过设计能力,具备单窑熟料产量100万t/a的能力。至1999年底我们已完成石灰石破碎、生料磨、回转窑、电收尘器、煤磨、水泥磨、4号包装机以PLC为基础的自动化系统改造,取得了较高的经济效益和改造经验,可为老厂技术改造提供参考,在此作一介绍。
1 自动化控制系统技术改造的设计思路
由于原设计提供的70年代自动化装备水平,生产过程控制全部采用相当于DDZ -Ⅲ型电动单元组合模拟仪表。进行过程数据的采集、转换、显示、调节、记录、报警,自动调节回路采用单参数模拟仪表控制,原理见图1。
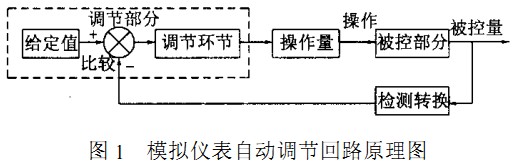
而机组设备的启停全部采用继电器逻辑联锁顺序控制各工序的运行。全厂自动化仪表有上千块(台),控制继电器几千只,从原料制备到水泥成品入库全部集中在一个中央控制室内操作、控制,其中95%的模拟仪表、继电器及其它电气元件为某家厂商生产,质量很不可靠,5%由美、英、德、法、日等第三国进口,给备件的提供也造成很大困难。整个自动化控制线路复杂,所有的仪表及电器元件有上万个继电器开关量点、模拟量控剖点及接线端点,全部集中在中央控制室内19个操作控制模拟盘内,22个继电器柜及现场大量的控制盘柜内,有一个控制点失灵则全线停车,检查几个甚至十几个小时才启动是常有的事,仪表和电气线路的维修工作量特别大,当时配有专职工程师在现场负责维修,直到1988年底最后两位专家撤走,仍未根本解决问题,严重影响了设备运转率和工厂的经济效益,而当时和淮海同期引进的宁国、冀东水泥厂因技术先进早已达产达标。科学技术水平落后就要被市节场淘汰,所以我厂自动化系统改造已是势在必行,针对上述设计及装备问题,我们内部经技术论证决定整体按以下设计思路实施自动化系统改造。
(1)参考原设计技术水平及思路,将全厂各工序分为三个层次的自动化控制水平,即窑、生料磨、水泥磨为一个层次,针对干法窑的工艺特点,模拟量中以热工参数温度、风量、速度、压力、料位等物理量为控制调节对象,加之大量的开关量,为保证产品质量和产量,配备的自动化程度技术水平最高,其次矿山、煤磨、包装等主要是开关量控制设备启停,第三个层次为辅助工序,如空压机站、水处理厂等,改用高质量的常规电器元件控制,全线控制回路保留原中控可转换控制方式,保留原机组联锁启停顺序关泵,优化选择原设计工艺过程检测参数点及重点控制参数自动调节回路,增加改造后窑尾MFC分解炉等热工参数检测控制点。
(2)自动化设备的选型。由于我们是将70年代的装备,用仪表加继电器式的自动控制技术水平改为90年代高科技技术,经反复论证,决定采用较先进的集散型控制设备,当时DCS技术较好的ABB.MODICON.HONEYWELL.SIEMENS等公司产品均可选用。但由于窑系统1991年技改时已选用SIEMENS公司的PLC,因此为了今后全厂技术水平的统一、配件供应统一,方便今后全厂计算机联网,所以在其它工序自动化改造中全部选用SIEMENS公司上下位机、软件等成套技术,以提高可靠性、技术先进性。
(3)自动控制系统的装备配置。根据以上设想,为满足3 500 t/d生产线运转率,根据工厂的经济能力,决定采用低成本、以PLC为基础的自动化技术改造的原则,全厂工艺线分工序控制,自成系统,设就地操作站,各工序之间暂不联网,待时机成熟时再联网组成大型DCS系统。其中一窑两磨各自实施上下位机二级联网控制,煤磨、包装等工序采用PLC程序联锁自动控制设备启停,配以相应的操作台、模拟盘进行显示操作。各系统配备了编程器进行程序编制,检
测故障及软件开发。
(4)虽然自动化控制设备选型先进,但相应的控制信号转换电器元件也必须可靠,因此技术改造后各工序所有的
控制继电器及接触器选用国内合资生产的HH - 52P型继电器及3TF系列接触器,其质量非常可靠,很少发生故障。
现全厂已全部取消了原罗设计的中控及现场控制盘、仪表、继电器柜,所有的模拟量及开关量全部送入计算机及PLC
进行控制、显示、调节、记录、报警等,上下位机基本无故障运行,几乎没什么维护工作量,提高了技术人员技术水平及工作效率,把精力转入技术开发、研究、技术攻关等工作,也大大减少了维护力量,增加了工厂的经济效益。
(5)为满足技术发展的需要,改造中也考虑了全集团公司的计算机联网问题,在各工序改造设计中,上下位机均保留了可扩展、可联网接口,不但工艺生产线可联网,而且目前集团公司已建立的计算机信息管理中心、财务、销售、供应等计算机管理系统均可联网,利用目前先进的网络技术实现集团公司的计算机网络化管理,进一步提高管理水平。
2 自动化系统技术改造的设计特点及问题处理
在全厂各工序自动化改造中,其设计思想及设备配置各有特色,但基础则全部为SIEMENS公司产品,下面仅举窑、生料磨系统为例迸行说明。
2.1窑自动化系统的技术改造
窑系统因在1991年改造时,SIEMENS公司的产品还较单一,因此上位机采用2台COMPAQ386微机互为备用,下位机采用SIEMENS公司的PLC,软件为美国西雷公司的ON-SPEC,组成两级联网的NCDCS控制系统,通讯采用RS -232C,系统组成的优点是具有DCS的特点,但系统价格较低。系统原理见图2。
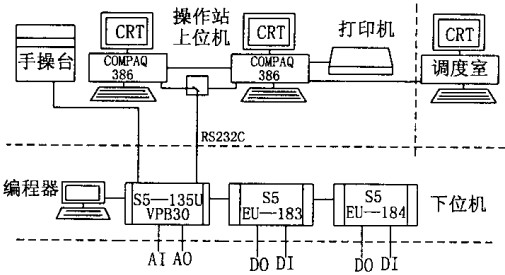
(1)该设计由于当时的技术水平及自动化装备产品有限,除二级联网控制外,又设计1套手动操作台作为上下位机备用,一旦故障,随时可用手动操作台操作,操作台配有相应机组转换按钮,风门操作,工艺过程模拟仪表等,可满足人工操作条件。
(2)罗方原设计12条PID自动调节回路,经优化选择改为10条,控制分解炉、篦式冷却机、预热器等的温度、风量、压力、速度的调节。
(3)窑头喂煤及窑尾分解炉喂煤,生料入窑喂料秤系统因当时信号转换接口元件无成熟产品,未进入上下位机,在操作站用人工操作,但砍掉了原设计中两个脑袋控制的问题,即窑头控制室控制煤粉入窑,而中控室无法控制,操作产生矛盾,改造后则全在中控室控制,取消了窑头看火工。
(4)在生产调度室设1台远程终端286计算机显示窖系统运转工况,但只监视不参丁.控制。该系统在运行中也遇到一些问题,经工厂技术人员的不断完善及改动,使原设计更加可靠,其主要问题有:
①抗干扰能力低。1992年上半年,上下位机在运行中会突然全线停机,再全线重新起动,有时1d多达3~4次,无法正常运行,后我们自己将原设计的下位机架又重新进行了配置,增加了系统单独接地极,并对上下位机的程度进行了整理优化选择,解决了这一问题。
②由于当时选用的软件功能不太成熟,上位机由于干扰或程序问题经常死机,且上下位机通讯速度很慢,现场采集的信号进上位机有时滞后15 s,而且变频器对模拟量T扰很大,给操作带来困难。目前该问题仍存在,有待配置新的SIEMENS上位机后就可解决。
③由于下位机输出至现场控制信号为24 V,当现场发生短路等干扰时,会造成PLC模块烧毁,一年损失近5万元资金,后将现场控制信号改为220 V,下位机仍为24 V,增加了继电器隔离后解决了该问题。
2.2生料磨自动化系统的技术改造
生料磨及水泥磨自动控制系统在1993年后的改造中,也是摒弃了原设计的所有自动化装备,应用了SIEMENS公司更先进的DCS系统产品,上位主机采用VPB30,下位机为S5 - 135U棋拟量开关量模块,软件为COROS,没计中吸取窑系统的优点,应用上下位机二级联网系统,使之设计更加完善。利用总线通讯,速度很快,上位机进行工况监控,包括实时数据的采集、处理,设2台CRT彩显进行动态数据、工艺流程显示,2台键盘互为备用和操作,机组启停、设备及流程选择,实时趋线显示,PID控制及显示,数值给定,报警及打印均可通过键盘操作完成,系统原理见图3。
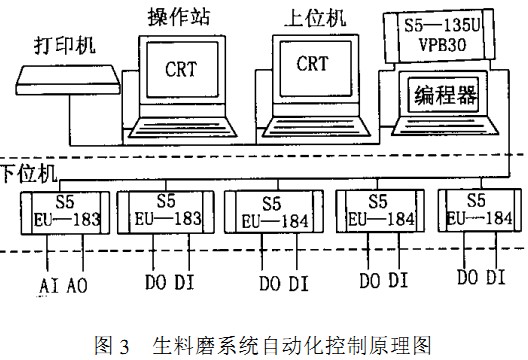
3检测及计量设备的技术改造
3.1检测仪表的技术改造
由于是全套引进技术,原现场检测仪表均为罗方产品,由于上面所谈质量原因,我们本着立足国内的原则,将其全部国产化,主要是一次检测元件热电偶、热电阻、压力开关、温度开关、数字显示仪表、电动执行器等,全部选用上海或天津仪表厂的产品,采用西安仪表厂的444型的温度变送器和1151型压力变送器。但料位检测元件一直无合适的产品,重锤式、螺旋式、射线式、声波式等,在使用中因受物料冲击、粉尘下扰等很难正常使用。现场一次检测元件虽不会造成停机等问题,但若质量不好也给显示、操作造成误导,因此必须使其稳、准、灵。原使用的窑头比色高温计为西门子ARDOCOL型产品,技改中已使用工业电视看火,石灰石破碎、生料磨、窑喂料均配置了彩色电视监视系统。
窑简体温度检测原采用ARDOPYR型辐射高温计,因显示不直观,技改中已选用澳大利亚蓝圈公司的T - Scanner型窑简体温度扫描仪,采用计算机控制,其优点是可直观地观测窑简体温度、窑皮分布、耐火砖厚薄、窑速、轮带滑移量、历史数据储存、温度曲线分析等多种功能,使窑的运行状况一目了然,就减少耐火砖检修一项每年可创效益上百万元,因此大型干法窑配备这种检测仪还是值得。
窑尾废气分析仪原采用H&B公司Uras3G和Magnos5T红外线分析仪,经多年使用,除取样器需经常清理外,使用尚可,为检修方便后又购置一套南京分析仪器厂的HW - 500型分析仪互为备用。但在技改后窑的产量达3 500 t/d时,因窑尾预热器出口负压增大,分析仪使样气抽取能力不足,目前正寻找合适的取样泵更换。
3.2计量设备的改造
随着产量及效益的提高,计量设备对过程控制中产品质量的重要性及计量技术的更新发展也是非常重要的。原设计磨、窑及各工序的喂料、配料全部采用schenck公司计量称,有调速式定量给料称、失重式计量仓、冲击流量计,由予技术的发展及更新,备件无法供应,对秤进行了改造,且已准备将原MICRCONT控制器改为INTECONT控制器,秤体也需改造。同时增设许多新的计量装置。
在生料质量控制中,原罗方对生料率值及磨机负荷控制采用计算机、配料称、x-分析仪、电耳组成自动控制系统,后在1991年技改中也是因为设计及设备质量问题对该系统进行了改造,由国产的Inte1286上位机及STD工控机代替罗方设计的ECAROM - 800计算机,西安二六二厂生产的FJ2810G型X-萤光分析仪代替原PW - 1600分析仪,配有IPC610工控机计算、显示。其控制方法及思想与原设计差不多。系统组成见图4。
水泥窑负荷控制系统基本也采用了入磨喂料秤配回料流量计组成新料+回料=常数的磨负荷控制系统,配以相应的磨内喷水控制温度的自动控制回路组成水泥磨自动调节回路,喷水装置因喷头雾化效果不好等原因,后不再应用,如果喷头问题解决好的话,还是应该继续使用的,以期提高水泥质量及产量。
在窑头窑尾供煤粉计量装置的改造中,窑头喂煤系统采用改电气控制部分的办法,该系统由法国PILLARD公司提供,但失重式计量仓还是SCHENCK公司的产品,将原控制部分的模姒量插件板改为当时较先进的MICROCONT控制器。原窑尾“一把火”喂煤系统与窑头相似,后因增加了分解炉,但该装置喂煤量不够,又全部改为SCHENCK公司的冲板流量计配以F-K泵向分解炉喂煤,窑头窑尾这2套计量装置在使用中遇到的主要问题是受环境温度、煤粉湿度、流化气质量、正压、反串风、负压等影响,波动较大,使用中经常出现不稳定现象,给窑的操作带来一定影响和困难,目前我厂正在调研,准备再次改造,采用科里奥利或菲斯特计量秤代替。在熟料出窑的计量设备中,1988年增设了核子秤计量熟料产量,但在使用中因受熟料颗粒度、料层厚度、粉尘大影响测量元件精度,干扰较大,计量效果不理想,现只作为产量参考计量,虽然中间又更换了一套核子秤及测量信号转换系统,仍不理想,这个问题有待研究。
为了适应市场,降低成本,加之工厂粘土资源渐匮乏,开发利用粉煤灰代替粘土及水泥掺加剂已是发展方向,而且可享受环保政策,1999年我厂采用粉煤灰配料,与生料一起入窑效果很好,熟料强度大幅上升,且开发生产了适合核发电站用的低碱水泥品种,为了提高计量精度,采用了科里奥利计量秤,精度和稳定性很理想,建议在技术改造中采用。而2台水泥磨粉煤灰糁加剂计量,据其精度要求只要能满足生产质量和产量即可,由本厂设计配套,采用转子秤配双管绞刀喂料的方案,成本较低又实用,其余在全厂各1序配备的电子计量秤,只作为计量及产量考核成本用途。
由于电子计量没备技术更新很快,因此企业在技术改造中必须采用新技术,如我厂原70、80年代的Schenck公司电子秤产品早已停止生产,控制部分已经采用INTECONT新一代产品,原产品连备件也买不到,因此必须不断技术更新,才能加快企业的发展,特别是计量技术已牵涉到大型水泥企业的经济效益问题,应非常重视。
三门峡富通新能源销售颗粒机、球磨机、破碎机、雷蒙磨等设备。