某发电有限责任公司5号炉系上海动力集团生产的一次中间再热自然循环锅炉,电负荷为125 MW时,蒸发量为410t/h。至2004年12月10日,5号机组运行约5万小时,锅炉末级再热器管发生泄漏失效,左数第25片屏内圈厂家制造焊口断裂,第24、25、26、27片屏U型弯上方1600 mm处部分直管段10处泄漏,另有18处管壁减薄,断裂焊缝距下弯头700 mm左右,距上定位板70 mm左右。对失效现场进行了查勘,并取样进行了化学元素分析、机械性能试验、金相分析及断口扫描电镜观察,对失效原因进行了分析。
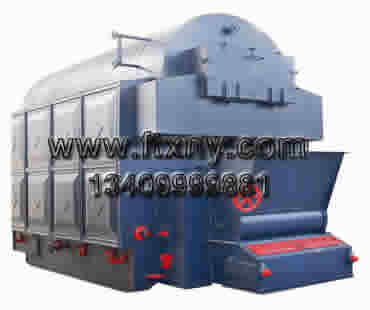
1、试样与方法
1.1试样
取开裂泄漏附近处的管段作为试样,进行拉伸试验,金相试验及断口扫描电镜分析。
1.2实验方法
在DLY-30型液压万能材料试验机上进行拉伸实验,试样尺寸为300mmx20mm。
金相组织由LEC0500大型金相分析仪观察。
显微硬度用MH-6显微硬度计测量。载荷为200 g,保载时间为15 s。
断口形貌由KYKY2800扫描电镜观察。
2、试验内容及结果
2.1宏观检查结果
泄漏处末级再热器管设计材质为钢102(12Cr2MoWVTiB),规格为∮63x75 mm与∮63x45 mm对接接头,属同外径不同壁厚对接接头,为保证对口厚度一致,对壁厚较大的一侧进行了内镗孔,镗至∮63x4.5 mm。断口沿焊缝热影响区裂开,断面十分整齐。泄漏处管子及弯头宏观无明显变形,内外壁氧化不严重,无明显氧化皮,管径无明显胀粗,管壁无明显减薄。
厚壁(∮63x7.5)侧有一由于机械加工造成的退刀槽,由内向坡口处以450方向呈螺旋线延伸,最深处在坡口边缘,长约30mm,最深处约0.5 mm。
断口上明显可见整圈焊缝不均匀,退刀槽处外壁的焊缝有明显的宽度变化,而焊缝内表面有较大的焊瘤,较其他部位高出约2 mm。断口上明显可见多处未熔合。
2.2化学元素分析
在开裂泄漏的焊缝附近管段取样,进行化学元素分析。试验结果如表l所示。
由表1可见,试样的化学元素成分除Si的含量稍低外,其余符合GB5130-95《高压锅炉用无缝钢管》标准的要求。
2.3机械性能检验结果
取开裂泄漏附近处的管段作为试样,进行拉伸试验,测定材质的强度和延伸率,具体数据如表2、表3所示。
由表2、表3数据可见,母材的抗拉强度符合GB5130-95《高压锅炉用无缝钢管》标准要求。
2.4金相分析结果
2.4.1试样
在泄漏管上共取4处试样进行金相分析。试样1为离泄漏位置250mm处∮63x4.5 mm侧管段横截面试样,试样2为离泄漏位置200 mm处∮63x7.5 mm侧管段横截面试样,试样3为泄漏焊口∮63x4.5 mm侧纵截面试样,试样4为∮63x7.5 mm侧管段退刀槽处纵截面试样。
分析结果认为,试样1~4的金相组织均为回火贝氏体,组织正常,见图1~4。
2.5显微硬度测量
取末级再热器管试样,测量显微硬度值,位置为金相分析的试样1、试样2等两处。显微硬度值见表4。
由表4数据可知,管材显微硬度符合标准要求。
2.6.断口扫描电镜分析
取泄漏末级再热器断裂管的断口进行电镜扫描分析,可见裂纹起源于退刀处未熔合,从内壁起裂,向外壁扩展。断口上可见沿穿晶型二次裂纹,为沿晶脆性断口,见图5~8。
3试验结果分析
3:1宏观检查结果
(1)断裂是在垂直于最大拉应力方向发生的,断口表面无宏观的塑性变形,为脆性断口。
(2)末级再热器管开裂于退刀槽处的未熔合处,从宏观检查可知开裂位置焊接质量不良,存在未熔合等缺陷。
(3)化学元素分析、机械性能试验结果表明管材化学成分、抗拉强度符合GB5130标准要求。
(4)金相分析结果表明,金相组织为回火贝氏体,属于钢102原材料典型正常组织,显微硬度值符合要求,原材料母材、焊缝及热影响区组织正常。
3.2断口的扫描电镜观察结果
(1)开裂末级再热器管裂纹起源于退刀槽处未熔合,正是处于应力集中处,并且存在焊接未熔合缺陷。
(2)末级再热器管断口上可见二次沿晶裂纹,属典型脆性断口。
以上分析结果表明:末级再热器管开裂泄漏是由于焊接质量不良,存在未熔合焊接缺陷,成为裂纹源,加上退刀槽处应力集中,在此处萌生裂纹,裂纹沿未熔合区扩展,加之焊缝热影响区力学性能相对薄弱,最终裂纹沿热影响区发展,导致断裂而泄漏。