
生物质锅炉新闻动态
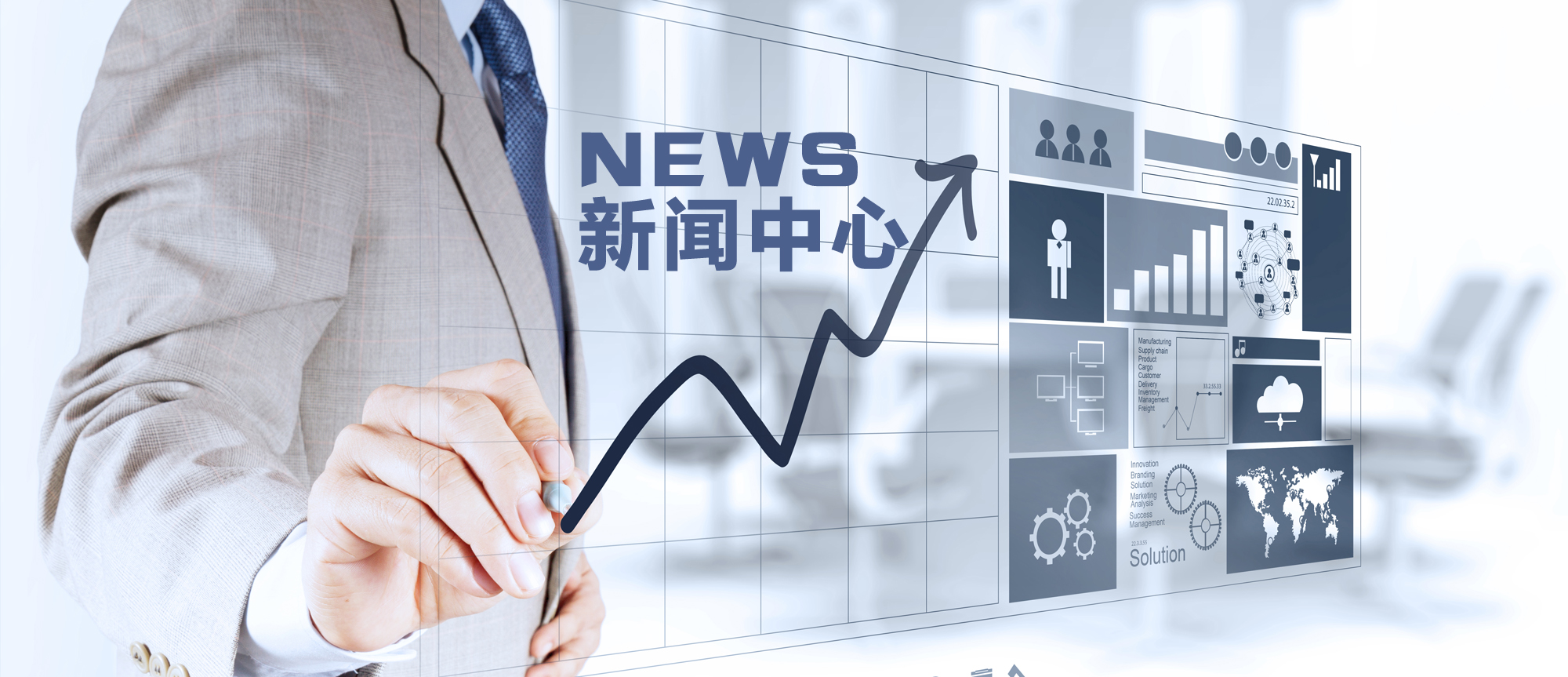
富通新能源 > 动态 > 生物质锅炉新闻动态 > > 详细
75t/h循环流化床锅炉调试运行总结
发布时间:2013-08-25 08:14 来源:未知
0、前言
山东肥城化肥厂自备热电联产工程设计规模为:2台75 t/h循环流化床锅炉达到12 MW发电量。首期工程为1台75 t/h循环流化床锅炉(5.3MPa、485℃)配1台12 MW抽凝式汽轮发电机组。抽气压力为1.27 MPa、温度329℃,减温后供化肥生产用。锅炉系统于2003年4月份投运,至今稳定运行,现对该锅炉系统的调试运行做一些总结和探讨。
1、工艺流程
(1)汽水系统工艺流程见图1。除盐水站来除盐水经旋膜除氧器除氧后(104℃),经高压锅炉给水泵加压至6.8 MPa(经高加一机组运行时)。然后经流量计、给水操作台后一路送至混合集箱,另一路送至面式减温器再返回混合集箱,共同进入省煤器。在省煤器内被加热至220℃左右后,送至汽包内,再经2根直径325 mm的降水管和底部的散水管进入膜式水冷壁,形成饱和蒸汽由水冷壁上集箱送入汽包,经汽水分离后进入过热系统(包墙管、吊挂管、高温过热器及低温过热器)形成5.3 MPa、485℃的过热蒸汽进入汇汽集箱。最后由主蒸汽管道运送至汽轮机或减温减压器,富通新能源销售生物质锅炉,生物质锅炉主要燃烧木屑颗粒机压制的木屑生物质颗粒燃料。
(2)烟气系统工艺流程见图2。烟气由炉膛出来( 900℃)进入旋风分离器(2台)分离出可燃物料后,经过冷凝管( 876℃)再回到锅炉的平烟道,与高温过热器内蒸汽换热降至670℃。再进入尾部竖井烟道与低温过热器、包墙管、吊挂管、省煤器内的汽水介质换热降至238℃。再经二级分离返料器除灰后进入空气预热器预热进入锅炉的空气。最后降至138℃左右,再经静电除尘器除尘、除灰后经引风机送入烟囱排人大气。
(3)灰渣系统工艺流程见图3。燃煤由3台螺旋给煤机送入落煤管进入炉膛燃烧室,锅炉前置了2台∮3000(内径)的高温旋风分离器,下方设了2台返料装置,分离下的物料返回炉内燃烧,也可放灰;在竖井烟道最下方设二级分离返料,分离下的灰送入炉膛,也可排灰。锅炉灰渣的比例为7:3,燃烬的渣由锅炉排渣管排至冷渣机,冷却后排出。烟气中的灰尘经静电除尘器除尘再由下部经加湿机加湿后排出系统。
2、运行情况
75 t/h循环流化床锅炉有关运行数据(2003年6月20日)见表1。
3、调试运行中存在问题的探讨和建议
3.1 磨损
循环流化床锅炉技术在较短时间内能够在国内外得到迅速发展和广泛应用,虽然具备燃料适应性广、有利于环境保护、负荷调节性能好、燃烧强度大、传热能力强及灰渣综合利用好等诸多优点,但其仍存在磨损问题。循环流化床锅炉的燃料粒径较大(0—13 mm),并且炉膛内物料浓度是常规煤粉炉的十至几十倍。循环倍率K:21,为中倍率循环流化床锅炉。虽然采取了许多防磨损措施,但实际运行中循环流化床锅炉受热面和分离器的磨损速度仍比常规锅炉大得多。
锅炉原设计的防磨损措施有:(1)旋风分离器、返料装置、燃烧室采用高强度耐磨浇筑料,凝渣管上有高强度耐磨可塑料;(2)高、低温过热器第一排管子弯头处加设lCr18Ni9Ti的防磨罩。
在运行期间停炉检修时发现存在以下问题:
(1)分离器内的浇筑料有明显裂纹,其原因是冬季开车烘炉不彻底,主要是耐磨浇筑料本身性能特点造成的。为保护炉墙每次开车启动时间一定控制在6h以上。
(2)凝渣管、高温过热器管子有磨损现象,磨损部位在防磨浇筑料和防磨罩终边处,此处烟气易形成涡流而加剧冲刷。为此采取了凝渣管上的高强度耐磨可塑料由1200包敷改为3600全部敷盖,高温过热器前排防磨罩由1200型改为1800型。
(3)水冷风室顶部的中温保温浇筑料有明显磨损。经分析认为运行中有细灰物料落入风室,并且运行中在风的吹动下对保温浇筑料进行了冲刷。为此建议在风室内的保温浇筑料外再浇筑一层耐磨料,并且在风室下方设计2个快开式排灰门,及时将炉膛落入风室的物料排出,从而保证风室内风量和供风均匀性及安全性。
(4)布风板上风帽存在磨损现象,除锅炉本身设计性能外,主要为风帽布置密度大,物料冲刷严重。现在有些锅炉厂正在探讨改进该技术,并在保证风量、风压及物料流化均匀的条件下减少风帽个数,加大间距,并采取钟罩方式,减少磨损和落入风室的物料,从而提高运行寿命。
减轻磨损、延长运行时间,最关键的是严格操作,控制负荷在设计能力内,以保证所设计的低烟气流速,从而减轻物料对受热面等易损部位的磨损,达到长周期安全运行的目的。
3.2 -级返料的回料阀
锅炉物料循环系统的回料阀采用的是U型非机械阀。靠回料气力输送物料,运行中靠改变通气量来调节回料量。阀底都布置一定数量的风帽,实际为1个小流化床(见图4)。
现在隔板两侧共用1个风室。这就在调节上存在一个矛盾:为增大返料量,应加大输送风量Q,但同时Q增大又阻碍了从立管中流下的物料流量。如增加立管中流下的物料量,减少风量Q,又造成返料量减少,易造成返料堵塞,影响运行。为此需将料阀的风室一分为二,各自调节(见图5)。Qi、Q2调节均有1个最佳值,运行时一旦调节好,回料正常稳定,负荷没有大的变化,一般不需调节。
3.3锅炉给水泵
2台电动泵(1开1备)型号为DG85 - 80×9次高压锅炉给水泵,配用电机6 kV、315 kW。在锅炉负荷低时,泵出口再循环阀需打开,就造成了动力消耗浪费,为此建议设置高压变频器。为进一步节能可采用1台电动泵加1台汽轮泵的配置。在系统开车初期采用电动给水泵给水,汽轮泵备用。在机组投入运行后采用汽轮水泵供水,电动泵备用。汽轮水泵原理:一般热电厂除氧器加热利用汽轮机组的二抽汽为厂用蒸汽(1. 27MPa),通过减压阀减压后(0.2 MPa)送入除氧塔内,这就造成了能量的浪费。汽轮水泵就是利用该压差设置1台背压式汽轮机来带动水泵,以发电机组抽汽为气源,经背压后的蒸汽去除氧器,此技术设备,既稳定又节能。以1台75 t/h炉为例,1台汽轮泵投资80万元左右,1台电动泵315kW,如用汽轮泵代替电动泵,1年节约电费为:315kW×24 h×330×0.5元/kWh:125万元,因此该技术是很有应用价值的,值得小型电厂推广应用。
3.4关于燃料颗粒特性对锅炉运行的影响
粗颗粒较多时对锅炉运行的影响:(1)会沉积于燃烧室下部燃烧,易造成密相区燃烧份额过大,炉床超温结焦;(2)床层加厚风阻增大,如果采取经常排渣措施,会造成带出热量多、锅炉效率下降,如加大风压,则电耗会加大;(3)风压加大,大颗粒在炉内流速增大,加剧了炉内下部受热面的磨损。为此一定要稳定控制好原料中的各种粒度物料的比例,摸索合理的炉膛温度流化状态下的合理风量,从而保证设计工况性能。同时也通过调整燃煤粒度,方可调整锅炉燃烧温度和汽压。
富通新能源不但销售生物质锅炉,同时我们还销售木屑颗粒机压制的生物质颗粒燃料。