
生物质锅炉新闻动态
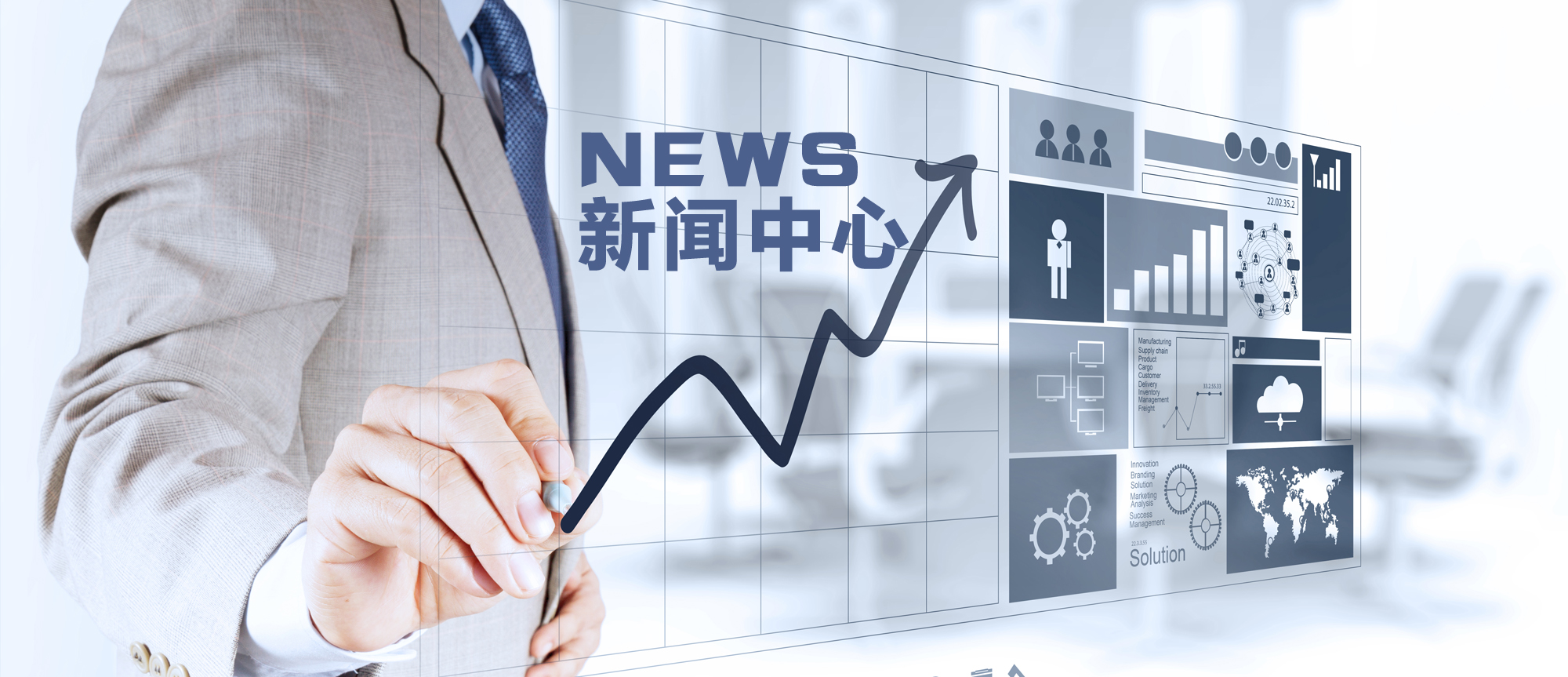
富通新能源 > 动态 > 生物质锅炉新闻动态 > > 详细
240t/h循环流化床锅炉运行及改造总结
发布时间:2013-09-08 08:42 来源:未知
0、前言
山东恒通化工股份有限公司热电厂11#、12#、13#、14#锅炉是240 t/h循环流化床锅炉。该炉系高温、高压、单锅筒、自然循环蒸汽锅炉,采用循环流化床燃烧方式、高温分离技术。其技术特点为:循环物料采用高温旋风分离器分离,分离器内工作温度与炉膛温度接近;燃烧室上部与前墙垂直布置有3片翼形水冷壁和6片Ⅱ级过热器;一、二次风采取分级供风方式,在炉前墙加入燃煤,实现炉内脱硫和控制NOx的生成量:采用“菌状风帽”式一次风布风装置;点火启动采用炉内物料流化循环,燃油加热升温并引燃燃煤的方式;循环物料控制采用J型阀。4台锅炉分别于2002年10月29日、2002年10月12日、2004年2月18日、2004年7月29日投入运行,其中11#、128锅炉为该型锅炉首次设计并最早投入运行的2台,由于在设计上存在着许多缺陷,因此在安装过程中,坚持一边施工一边更改的原则,设计变更达100多处。从2年多的运行情况来看,该型锅炉能够达到设计要求,能在30%~110%额定负荷下稳定运行。
1、锅炉本体与工艺流程
锅炉本体主要由4部分组成,即燃烧室、高温旋风分离器、返料装置和尾部对流烟道。燃烧室位于锅炉的前部,其断面呈矩形(长度×宽度为5.28 m×10.24 m),四周和顶棚布置有膜式水冷壁,底部为略有倾斜的水冷布风板,由于在燃烧室中磨损严重区域水冷壁上内衬耐火材料,造成水冷壁受热不足,因此在上部与前墙垂直布置有3片翼形水冷壁,另有6片II级过热器。燃烧室后有2个平行布置的旋风分离器,密封返料阀位于旋风分离器下部,与燃烧室和分离器相连接。燃烧室、旋风分离器和返料装置构成了固体物料循环回路。约占锅炉总量60%的热风经风室和布风板进入炉膛,对炉膛的床料流化,形成流化床燃烧。二次风从炉膛不同高度进入,实现分级燃烧。高温烟气从炉顶后墙两侧分别进入2个高温旋风分离器,其中绝大部分的颗粒被分离下来并作为循环灰,经2个气力控制的自平衡式型阀送回炉膛下部,形成循环床,富通新能源生产销售生物质锅炉,生物质锅炉主要燃烧颗粒机、木屑颗粒机压制的生物质颗粒燃料。
尾部对流烟道的锅炉后部,其内沿烟气流程依次布置III级过热器和I级过热器,下部烟道内依次布置有3组省煤器和一次风、二次风空气预热器。
2、运行及控制分析
2.1锅炉点火与启动
锅炉点火启动采用床料循环加热方式,冷床料(粒度<8 mm炉渣,可燃物<5%,床料厚度350—400mm,总量2m3/h)在流化床循环的条件下加热升温。加入床料启动2台“J”阀风机、引风机、一次风机、二次风机,按吹扫要求建立吹扫风量对锅炉进行吹扫,并将所有风机置于自动方式。
11#锅炉冷态点火启动时间约10 h,间歇投煤时床温为470℃。锅炉压火时间较长(>2 h),床温低于投煤温度。在锅炉温态启动时需投运油燃烧器。
锅炉压火后1—2h内热态启动,热态启动床温高于投煤温度,可直接投煤。热态启动时要严格控制风量大于临界流化风量,若风量过大会导致床温降低,压火前适当保持较高床压运行以保证炉膛较大的蓄热量。
由于有大量的高温床料存于炉内,压火后要保持一段时间过热器排汽、冷却过热器泄压。停运给水泵前,将水加至汽包较高水位。到燃烧器投运为止,床温平均下降速率约为35℃/h,由于床内有较多的耐火材料要求床温的变化率控制在< 80℃/h。在较低的负荷下稳定运行30 min,有利于保护分离器及其它部位浇注料。
2.2锅炉热效率
临沂市能源监测中心对11#、12#锅炉进行测试,测试结果如表1所示。
由表1可知,锅炉热效率可以达到86. 6%、88.6%。飞灰未燃烬碳含量低于设计值8%,分析室在4月6日和28日分别对飞灰进行测试,结果分别为8. 80%和10.04%,这与运行工况和燃料粒度等因素有关。
2.3 辅机运行情况
辅机运行情况见表2。
从表2可以看出,各辅机都留有较大余量,形成“大马拉小车的现象,造成用电量较高,不利于节能。
2.4控制参数
该锅炉具有较好的控制性能,运行期间最低稳定负荷为80 t/h,在30%—110%额定负荷之间瞬时负荷变化率和连续负荷变化率可达到设计值。运行中几个主要控制参数情况如下。
(1)料层差压:设计控制参数为7.0~9.5kPa,实际运行中控制在8.0 kPa,料差的控制通过改变水冷滚筒式冷渣机变频电机的转速实现。我厂滚筒式冷渣机的使用效果良好,关键在于两个方面,一方面严格控制入炉煤的粒度,防止大颗粒堵塞冷渣机,另一方面操作人员对冷渣机结构及运行保护理解全面。
(2)炉膛差压:设计控制参数为<1.5 kPa,实际控制在1.0 kPa,炉膛差压的调控通过放灰来实现。投运初期需人工放灰,现经过技改工程加装冷灰机,可以在微机上实现自控。
(3)氧含量:设计控制参数为3%~5%,实际运行中为6%。这就增大了排烟损失,需进一步加强操作控制,把过量空气系数控制在1.15~1. 25(50%负荷以下可以取1.6~1.8高值)。安装时,过热器后2个测点仪器一为国产产品,插入深度1.5 m,另一为进口产品,插入深度较浅,导致测量结果偏高,二者平均值为6%。若将测点按规定安装,可以控制在<5%的指标内。
3、存在问题、采用新技术及建议
11#、12#锅炉在安装及试运行期间发现诸多设计上问题。由于是第一次设计制造,许多问题由设计人员、安装人员及厂方在现场协商变更,变更达100多处,现仅列出对锅炉比较重要的几项供分析参考。
2002年7-9月试运行期间,发现炉膛由于水冷壁刚性梁设计不合理致使水冷壁刚性差,出现间歇性腹吸式振动。根据煤粉炉设计和使用经验,刚性梁问题最大不应超过96倍水冷壁外径,但对于流化床锅炉则不同,厂家设计间距(从下至上)分别为1.8 m、2.0 m、2.8 m、3.0 m,2.4m、2.4 m、2.5 m。经过三方协商,对刚性梁问题进行调整,标高19.2 m、22.0 m、25.0 m之间3道改为5道,并加装止晃装置后运行正常。
2003年停炉检查时发现,两旋风分离器中心筒变形严重。原设计中心筒外圈只有底部1道环形拉板,中心筒外圈中部缺少环形固定拉板(起限制变形的作用),因此在长期的高温条件下,中心筒中间部分变形严重。为了减小中心筒变形量,在中心筒外圆中部加1道环形拉板,可大大减小高温条件下中心筒的变形量,从而保证了旋风分离器的分离效率。
炉膛卫燃带浇注料过渡区水冷壁管磨损严重,到目前为止还没有根本解决方法。本型循环流化床( CFB)锅炉炉膛卫燃带高度为5m,虽然锅炉厂采用美国纽克拉电站循环流化床锅炉的外弯让管设计方案,防磨效果并不理想。这类磨损的机理主要有以下2个方面:一是过渡区域内由于沿壁面下流的固体物料与炉内向上运动的固体物料运动方向相反,因而在局部产生涡旋流;另一个原因是沿炉膛壁面下流的固体物料在交界区域产生流动方向的改变,因而对水冷壁管产生冲刷。卫燃带与水冷壁过渡区域内水冷壁管的磨损并不是在炉膛四周均匀发生的,而是与炉膛内物料总体流动形式有关。磨损主要发生在后墙和左右侧墙,尤其是后墙更为严重,前墙磨损较轻。我厂在11#、12#CFB锅炉炉膛水冷壁浇注料过渡区采用铬镍硬质合金火焰喷涂,效果不好,使用一段时间后,检查发现在喷涂区与基材过渡区涂层结合不好,涂层容易脱落形成台阶。经过焊补处理后,在过渡区焊销钉,增打可塑料防磨圈梁,在防磨圈梁上的一定高度范围内实施超音速电弧冷喷涂进行防磨,可大大减轻磨损,延长该区域水冷壁管的使用寿命。
炉膛卫燃带浇注料过渡区4个角水冷壁管磨损爆管现象严重。原因可能是角落区域内沿壁面向下流动的固体物料受到相邻2个面的共同作用,物料浓度比较高,同时流动状况也受到破坏,因此磨损要比其它几个面严重,目前也没有根本解决方法。我厂最早投运的11#、12# 240 t/h CFB锅炉角落区域曾发生过多次水冷壁爆管现象。在运行中,尽量不要长时间超负荷运行;在停炉检修过程中,要认真检查,对检查出的问题要妥善处理,必要时在四角一定高度内增打可塑料防护,在实施超音速电弧喷涂时,四角水冷壁管喷涂高度比其它区域要高一些。
炉膛出口之间水冷壁管磨损严重。运行一段时间后,停炉检查时发现,该区域水冷壁管在迎烟气流动方向45。~ 90。范围内磨损严重,最薄处壁厚为3.8 mm(水冷壁管规格为:∮60 mm×5mm)。主要原因是大量含尘烟气在临近炉膛出口处体积变小,流速增加,流动方向发生变化,目前也没有根本解决方法。在该区域也要采用超音速电弧喷涂进行防护,减轻水冷壁管的磨损,延长水冷壁管的使用寿命。
炉膛顶部翼形水冷壁和屏式过热器(Ⅱ级过热器)变形严重,与前墙让管处水冷壁管磨损严重。最早投运的11#、12# 240 t/h锅炉曾发生过屏式过热器和翼形水冷壁泄漏爆管事故。在停炉检查过程中,认真检查,检查出的缺陷及时处理。
尾部竖井烟道内布置的Ⅲ级过热器、I级过热器、省煤器和空气预热器磨损较轻,运行2年后,几乎没有磨损现象。这主要有3个方面的原因:一是旋风分离器分离效率高,大量的物料被分离下来,返回炉膛多次循环燃烧,流经尾部受热面的烟气含尘浓度较低;二是流经尾部受热面烟气流速较低;三是声波吹灰器运行效果较好,能及时清除尾部受热面积灰,避免局部烟气流速过高而加快该区域受热面的磨损速率。
风帽磨损现象严重。本型锅炉采用1872个“菌状”风帽,与水冷布风板采用螺纹连接,风帽磨损区域主要靠近后墙回料口附近。其原因主要是由于较高颗粒浓度的循环物料以较大的、平行于布风板的速度分量冲刷风帽;另一种情况是风帽小孔的扩大,改变了布风特性,固体物料漏到风室,减小了风室的有效容积,大风室起不到稳压均流作用,从而造成流化质量下降.甚至堵塞送风通道。且布风板螺纹容易变形,停炉检修时不容易更换风帽,可将螺纹连接改为直接插装电焊固定。
锅炉冷渣机冷渣通道容易堵塞和泄漏,进渣嘴容易泄漏,锅炉煤质变差和入炉煤粒度得不到保证时,冷渣机不能满足锅炉排渣量。短节的长度过长,不能满足锅炉水冷壁管热状态下向下膨胀的需要;冷渣器进渣管磨损严重,经常发生泄漏;冷渣通道容易被大颗粒堵塞,且不易清理;距冷渣通道进口约5 cm范围内,经常发生泄漏;进渣口落红渣时,托轮轴承容易被烧坏;在进渣端设置6根回水管,给检修和疏通渣管堵塞带来不便。为了满足锅炉热态下向下膨胀的需要,将短节长度由150 mm改为50 mm;冷渣器进料管是双层壳体结构,最内层是进渣通道,是夹层是冷却水通道,是带有一定速度的高温炉渣最先经过的部件,工作环境最为恶劣,并且该部件并不随冷渣器转动,磨损特别严重,很容易被磨漏。根据多年的经验,决定在此处焊上销钉,打上1层可塑料防护层,可有效地起到防磨作用,从而大大减小冷渣器进料管的维修工作量;为了提高冷渣器的耐磨性能和运行可靠性,生产厂家作了如下改进:冷渣通道的板材厚度由3 mm改为4 mm;板材材质由20#改为16Mn;为了增加滚筒转动时的稳定性、防止热渣下落时烧坏托轮轴承,将托轮由前端改为滚筒下部;为了检修方便,将进渣端的回水管改为出渣端回水管。通过厂家的进一步改进设计,该型滚筒式冷渣器的性能得到进一步提高。针对冷渣器高温区冷渣通道氧化和磨损特别严重的实际情况,建议厂家在设计时考虑在高温区增加防磨护瓦,可进一步提高冷渣通道的抗氧化和抗磨损能力。
正压浓相气力输灰系统仓泵进料阀、出料阀、底部流化盘磨损严重。仓泵出料阀密封面容易磨损且价格较高,维修费用较高,进料阀在泵体内,检修极不方便。对仓泵出料阀要加强运行管理与检修维护,在阀体底部加设吹扫头,提高出料阀的使用寿命,降低维修费用;为了检修方便,在仓泵进口管道增加1只进料阀,原泵体内的进料阀不再使用。
大风室积灰、漏灰现象严重。目前有一种中间加装套管的新型大孔径风帽,可以大大减轻风帽之间的磨损和大大减少风室漏渣现象,但是对现有锅炉改造较困难,这需要锅炉厂重新更改水冷布风板的设计。所以目前可以加厚风帽,以延长风帽的使用寿命。关于风室漏渣问题,只有要求操作人员及时将大风室积灰放掉,管理人员加强监管力度。锅炉每次检修时,都要认真查找风室漏灰点,并要加以消除。2004年11月128锅炉计划停炉检修时,检查人员发现由于风室漏灰,水冷布风板下集箱局部区域被冲刷磨损现象。
蓬煤、堵煤现象比较严重。入炉掺兑燃料中含有一定量造气炉渣和除尘灰(它是由化肥造气转来的)。特别是在阴雨天,入炉煤又细又湿,煤仓蓬煤、落煤管堵煤现象更加严重,严重影响着锅炉机组的正常运行,还增加了操作人员的劳动强度。在煤斗内壁镶贴高分子聚氯乙烯板,实际使用效果并不理想,聚氯乙烯板多次发生脱落,给正常生产带来很大麻烦;采用疏松机技术,煤斗蓬煤后,自动疏通,使用效果较好。入炉煤细小颗粒较多,水分较大,尤其在掺烧造气除尘灰后,在落煤管弯头处和炉膛给煤口处粘附,越积越多,最终导致落煤管堵塞,发生堵煤现象。可采用增设播煤风系统,在落煤管弯头处加吹扫风,及时将煤吹进炉膛;运行中加强对落煤管的监视,发现有煤粘附落煤管壁,要及时清除;同时加强入炉煤的管理,混合料各成分和粒径搭配均匀,尽量减少入炉煤的水分。
根据国内厂家流化床锅炉浇注及砌筑的实际情况,我厂对浇注料及砌筑项目给予了高度重视,安排专人负责此项工程,经过对国内410 t/h、220 t/h、130 t/h、75 t/h、35 t/h 5种炉型浇注料及砌筑工程施工和使用情况的考察,对厂家的图纸作了大幅修改,主要有以下几个方面:
(1)所有浇注料部位用料提高一个档次。
(2)旋风分离器采用内江410 t/h锅炉设计。
(3)尾部烟道炉墙纵向膨胀由原设计1道40 mm改为2道各20 mm。
(4)返料器回料高度改为450 mm。
(5)省煤器防磨梁增打浇注料。
(6)燃烧室、水冷套等处安装时的变形由浇注料存度增减来弥补。
4台240 t/h锅炉自投运至今,浇注料及砌筑完好,没有发现损坏处。主要经验有3个方面:一方面要选择有资质、有实力、有施工经验的单位;二是对用料检验把好关;三是加强施工监管。
部分受热面设计不合理,不能满足锅炉正常运行要求。11#、12# 240 t/h CFB锅炉排烟温度设计为140℃,实际运行中160℃左右,空气预热面积偏小,建议重新核算。2004年10月各炉在较低负荷(每台锅炉约带170~180 t/h负荷)运行,在减温水全部关闭的情况下,过热蒸汽温度仅达到500℃左右,严重影响了热电厂的热效率,建议锅炉厂家对各种负荷下的受热面重新进行校核计算。
针对各风机余量较大,造成用电量较高的实际情况,结合成熟的节能技术的推广应用,建议各风机与驱动电机采用液力偶合器连接,不但降低各风机的耗电量,而且可大大降低风机的启动力矩和启动电流。
4、结语
(1)4台240 t/h循环流化床锅炉运行稳定,蒸汽参数、锅炉出力、变负荷能力等均达到设计值。
(2)分离器分离效果较好,尾部烟道防磨措施得当,尾部受热面磨损轻。
(3)锅炉热效率达不到保证值。