1、前言
对旋式轴流风机因其结构紧凑,压头高、流量大且具有良好的反风性能的特点被广泛应用于矿山安全通风与隧道通风工程中,这种风机由于两转子间没有导叶而使得两级间的气动匹配与气流干涉成为内流分析优化的核心内容。本文结合BD6对旋风机的几何模型,采用CFD分析方法对该机的性能与两级间的气动匹配特点进行了分析,预测性能与实验性能进行了对比,给出了内部流动的流场分布,讨论分析设计工况下两级间匹配的内部流动结构,为该类风机的使用和优化改型提供依据。
2对旋风机的内流分析方法
对旋风机的内流模拟近十年来一直受到流体机械内流研究领域的重视,作者曾在文献通过对采用混合设计方法设计的一种板式叶片的对旋轴流风机通过采用SIMPLE算法编程实现求解雷诺时均N-S方程,给出了两级叶片流道内的速度分布,为设计的叶片提供了局部的流动依据。应用标准K-e紊流模型和SIMPLEC算法进行了定常三维紊流流场的数值模拟分析了对旋式轴流泵的内部流场特性及前后叶轮之间的流场干涉情况。李秋实等结合实验对对旋风机对旋叶轮级间流场进行了研究,成功应用CFD对对旋风机昀内流场进行了研究。近年来商用软件在叶轮机械上的成功应用,使得对旋风机的深入细致的内流分析更为容易。
2.1计算方法
采用三维雷诺平均守恒型定常Navier-Stokes方程和K—s标准两方程湍流模型对前、后两级叶轮构成的集合模型,采用SEGREGATED隐式计算方法,湍流动能、湍流耗散项、动量方程都采用二阶迎风格式离散;压力一速度耦合采用SJMPLE算法。
本模型计算研究中:当进出口的流量误差小于10
-5,同时各方向的速度参数和K、£等参量的计算误差都小于10 -时,认定当前数值计算已经收敛。
2.2计算模型与网格划分
计算中对对旋风机在进行数值模拟的计算区域包括从进入集流器到离开扩压器的所有内流流道空间,模拟使用的网格如图1所示。数值模拟中为控制网格质量,需将复杂的计算区域分割,各区域单独生成合适的网格节点。这里对整个流场按主要部件划分为四个计算区域,即: 1.集流器流道;2.第一级转子流道;3.第二级转子流道; 4.扩压器流道。其中区域1、4定义为静止区域;区域2、3为运动域。
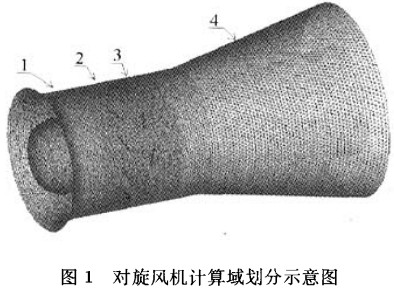
2.3边界及运动条件的确定
第一级转子和第二级转子区域为旋转区域,采用旋转坐标系,流体给定相应的旋转速度,其他区域为静止区域,采用静止坐标系。另外对旋风机的自身独特性,需要采用多参考系模型(MRF)。
定义转子所有叶片表面为旋转壁面,由于叶片随流体旋转运动,给定相对旋转速度为0,壳体表面、轮毂表面、整流罩表面均为静止壁面,旋转壁面和静止壁面均满足无滑移条件。
定义对旋风机的集流器进口截面作为整个计算域的进口,扩压器的出口截面定义为整个计算域的出口。进口边界条件给定为设计工况的质星进口,出口给定静压条件,为大气压。进出口湍流动能和湍流动能耗散率均依据经验公式计算确定。两级转子间的交界面使用interface面,上游的出口参数和下游叶片的进口参数在交界面上进行耦合计算。
3模型结果分析
3.1模型几何模型的特点
本模型分析中的对旋结构轴流风机模型选用文献中结构参数及气动性能数据较为齐全的OB-84-84B模型机。该风机的研制及实验工作是由前苏联中央流体动力学研究所与矿山机械和工程控制研究所共同进行的。这种通风机的特点是在设计它的工作轮叶片时考虑了沿半径的压力损失变化,该叶片的弦长值,翼型的安装角及其中线的曲率半径按照一定的规律变化,其特点是在给定压力和流量计算值的条件下得到较高的最大效率和扩压特性曲线的高效率范围。
该模型机主要设计与结构参数见表1。
表1模型机主要设计与结构参数
流量系数 |
0.225 |
压力系数 |
0.75 |
轮毂比 |
0.6 |
外径(mm) |
630 |
工作转速(r/min) |
2900/2900 |
基元翼型 |
NACA对称翼型 |
第一级叶片参数 |
12 |
第二级叶片参数 |
10 |
算选用的对旋轴流通风机结构简图,其中1为集流器,2为扩压器,R1为第一级工作轮,R2为第二级工作轮。其中电机与工作轮直联,前后两级工作轮的旋转方向相反。
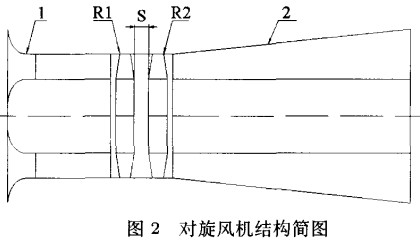
3.2整体及一、二级叶片网格划分
用GAMBIT形成了1、2级叶轮的非结构化网格,其中对叶片的叶尖、叶根部位进行了局部加密,整个计算区域划分网格数量为150万左右.其中一、二级叶片区域划分的数量分别为48万和55万。
3.3性能预测及与试验结果的对比
为详细对比CFD预测性能与实验气动性能结果,采用上述方法计算了给定转速凡= 2900 rlmin时的8个不同流量工况,计算预测结果与文献[1]中给出的气动性能略图结果对比,图3给出了CFD预测与试验结果的对比。结果显示,在流量系数小于0.22的小流量区,实验与预测结果相差在8%左右,而在流量系数大于0.22后,压力特性实验与计算预测精度符合较好,误差在2%范围内,而在效率的预测时,流量系数大于0.25后效率与实验误差逐步增大。大。显然在小流量工况下预测计算时采用紊流模型受到了限制,而在大流量范围内能够较好地预测整机的压力特性。
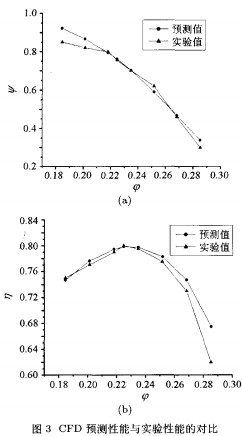
3.4设计点工况的内流特征与分析
在转速为n=2940r/min时,设计点的流量6.5m
3/S,压力为4500 Pa,该工况下子午面上的流速等值线分布见图4。图5给出第一、二级叶轮中部及两叶轮中间无叶通道中部的径向面上的流速等值分布结果,显示为局部通道径向面上的结果,平均周向回转面上的速度云图、等值线及速度矢量图分布见图6。
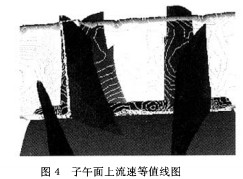
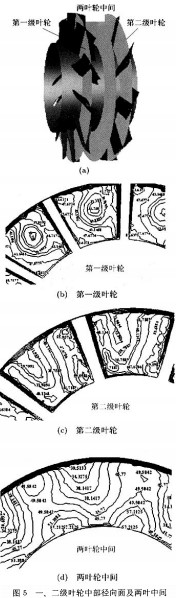
在设计工况下,图4子午面其流速等值线显示由于所取的截面穿过第一级叶轮,而该截面又穿过第二级叶片间通道,因此只能局部反映第二级通道流动流速在子午面上分布,第一级位置反映了在叶片周围的速度变化在子午面上分布;图5径向面分布显示,一、二级叶片通道中部的速度大小分布结构差异较大。第一级中部径向面不同位置速度的大小不同,在中部流动速度较低,而轮毂、叶顶位置上速度增加;而在第二级中部径向位置,通道上下流速分布较好,在叶片边界部位速度变化明显,而在中部流动结构显示,由于一、二级叶片所处的相对位置不同,使得局部图上显示部分区域上从叶顶到叶根速度下降,而相邻部分的速度则相反。这种分布沿周向基本对称分布,显示两级叶轮间速度上下传送的特征。图6平均周向面上的流速矢量及等值线分布看出,第一级的进口速度分布均匀,显示具有良好的进气条件,一级叶片通道内的流动速度分布基本均匀,而在出口形成一定的尾迹,影响到两叶片间的流动速度分布,使二级进口速度分布不均,在二级通道两侧的流动速度分布具有明显的不稳特征。
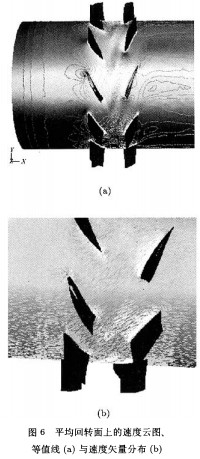
4结 论
(1)本文结合对旋式轴流风机的特点,对所选模型的结构进行了全流道的CFD模拟分析计算,给出了计算分析方法,预测计算的性能与实验得到的性能吻合,选用的模型方法对于高效率区的预测精度相当高,在大流星区,效率预测与实验结果误差在8.8%内,验证了本文处理方法的可靠性,能够为同类风机的优化改型提供帮助。
(2)对设计工况点进行了两级流道内内流结构的分析,详细给出了两级叶轮周向面、径向面以及子午面上的流速等值分布特征,给出了初步的分析。结果显示,设计点上外部性能良好,但其两级叶轮间的流速分布仍存在很大差异,流速分布显示一级尾迹对二级进口影响较大。
(3)利用成熟的CFD软件进行全流道对旋式轴流风机的内流分析比过去传统的数值模拟方法进行内流的分析具有计算速度高,后处理直观清晰,能够有效地缩短研究周期,得到内流的更多有效信息,有助提高对该形式风机内流机理的认识。