0、引言
自有人类以来,生物质能源一直是我们赖以生存的重要能源。17世纪末期大规模使用煤炭以前,生物质能就作为主要的能源:目前,全世界仍有25亿人口用生物质煮饭、取暖和照明.生物质能约占世界总能耗的14%,相当于12. 57亿t石油。尤其在发展中国家,生物质能仍然是主要的能源来源,约占总能耗的35%左右,相当于11.88亿t石油加。
中国生物质能十分丰富,尤其是秸秆,其产量达6亿多t,相当于3亿多t标准煤。然而,一直以来,由于利用装置非常落后,热效率很低,秸秆投有得到合理的利用,甚至有的秸秆被就地烧掉等等。不但浪费资源,污染大气,而且影响交通安全。据有关专家预测,生物质能极有可能成为未来持续能原系统的组成部分,而寻找新技术更加高效合理的利用生物质能也成为一个大热门。
生物质成型燃料(经过
颗粒机、
秸秆压块机加工而成)技术应时而生,而秸秆成型燃料也成为世界范围内解决生物质高效、洁净化利用的一个有效途径。利用秸秆替代矿物燃料,实现C02零排放,降低大气中的NOx、SOz含量,对保护生态环境、发展社会经济、实施能源可持续发展战略有着重大的现实意义。
但是,由于结渣等因素,生物质成型燃料燃烧技术得不到广泛推广与发展。结渣是由软化或熔融的灰粒冷却不充分遇到温度较低的水冷壁时生成的熔渣。结渣不仅会对燃烧设备的热性能造成影响,而且危及燃烧设备安全性。因此在燃烧设备设计时,若能准确判断燃料的结渣性能,则将会把炉膛尺寸、受热面布置以及吹灰系统的选择和布置这些问题解决得比较合理,这对确保机组的安全,经济运行也是至关重要的。所以探寻结渣的规律及影响因素也就显得非常必要。
然而.目前中国对秸秆成型燃料结渣的理论研究和应用研究很少,为此,笔者对设计出的双层炉排生物质成型燃料燃烧装置进行结渣特性及影响因素的试验与研究。
1、试验方法与使用仪器
1.1试验方法
根据GB/T15137 -1994工业锅炉节能监测方法与结碴率的测定方法,对燃烧设备进行试验。试验采用双层炉排燃烧方式:双层炉排的上炉门常开,作为投燃料与供应空气之用#中炉门用于调整下炉排上燃料的燃烧和清除灰渣,仅在点火及清渣时打开;下炉门用于排灰及供给少量空气,正常运行时微开,开度视下炉排上的燃烧情况而定。
1.2试验所用仪器与燃料
仪器:电子天平,KM9106综合燃烧分析仪,IRT-2000A手持式快速红外线测温仪,SWJ精密数字热电偶温度计,磅秤,米尺,秒表。
燃料:试验燃料为液压成型玉米秸秆,一般粒度为130 mm圆柱,密度为1.15 t/m3,含水率为14%,收到基挣发热量为15658 kj/kg。
2、试验的结果与分析
2.1结渣与妒膛内过量空气系数的关系
根据风门开启的从小到大可分为四种工况:工况1,风门最小,apy=1.6;工况2,风门较小,apy =2.2;工况3,风门较大,apy=3.2;工况4,风门最大,apy =4.4。通过试验,绘制出生物质成型燃料的结渣率与炉膛内过量空气系数关系如图1所示。
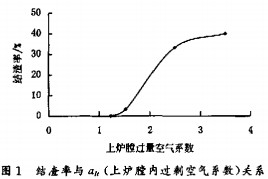
从图1中可以看出,结渣率随过量空气系数的增大,在atx=1.2~1.5时增加缓慢,在atx=1.5~2.9时急剧增加,在‰>3以后结渣率基本保持不变。考虑到燃烧装置运行在最佳情况下,即atx为1.5以下时,这
时结渣率较低,所以可以得出燃烧装置在此种燃烧情况
下为轻微结渣。
2.2结渣与炉膛温度的关系
通过试验,绘制出生物质成型燃料的结渣率与炉膛内炉膛温度关系如图2所示。
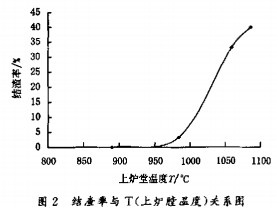
从图2中可以看出,结渣率随炉膛温度的增高而增大,在T=890~984 C时增加缓慢,在T- 984~1059℃时急剧增加,在T>1059 ℃以后结渣率逐渐增大。考虑到燃烧装置运行安全性,炉膛温度在984 ℃以下时,结渣率较低。
2.3燃料粒径与结渣的关系
在燃烧最佳工况下,对不同粒径燃料进行燃烧并进行结渣试验与观察,其结渣与燃料粒径的关系如图3所示。

从图3中可以看出双层炉排燃烧情况下,随着燃料粒径的增大,结渣率均增大。这是因为随着粒径的增大,燃料燃烧中心温度需提高,灰渣温度达到灰熔点,因而易发生结渣。
2.4燃料层厚度与结渣的关系
在燃烧最佳工况下,对燃料粒径为130 mm不同厚度燃料层进行燃烧试验,得出结渣率与燃料层厚度的关系如图4所示。
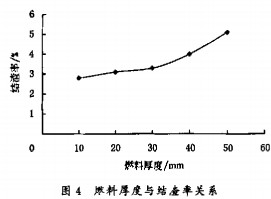
从图4可看出,随着燃料层厚度的增大,结渣率增大。这是因为随着燃料层厚度的增大,燃烧层内氧化层与还原层的厚度增大,燃烧中心温度增高,灰易达到灰熔点,结渣率增大。
2.5操作水平对结渣的影响
操作水平影响炉内温度水平和灰粒所处气氛环境。炉内温度水平是由调整和控制炉内燃烧工况来实现的。若燃烧调整和控制不当,使炉内温度水平升高,易引起炉膛火焰中心区域受热面或过热面结渣。运行时,在保证充分燃烧和负荷要求的情况下,通过调整和控制燃烧风量、燃料量来降低炉内温度,防止或减轻结渣。
燃烧装置通常应在atr=1.5左右运行。若atr过大或过小,则炉膛内烟气中含有的CO量增多,火焰中心的灰粒处于还原性气氛中,三价铁还原成二价铁,会引起灰粒的熔融特性降低,加大炉内结渣的倾向。运行时,应调整风速、风量,改善燃烧质量,将炉内烟气中还原性气氛降低,使结碴降低到最低水平。
3、结渣成因
3.1 结渣的形成过程
层燃锅炉的结詹过程包括三个步骤:1)胜料燃烧过程中,随着炉温的升高,局部达到了灰的软化温度,这时灰粒就会软化,灰中的钠、钙、钾以及少量硫酸盐就会形成一个粘性表面;2)随着炉膛内温度的进一步升高,氧化层和还原层内盘度超过了灰的软化温度,特别是在还原层内,燃料中的三价铁还原成二价铁,致使燃料的灰熔点降低,灰粒在还原层大都软化并相互吸附,形成一个个大的共熔体,3)大的共熔体下落过程中碰到水冷壁就会很快冷却,形成固体,而黏附在水冷壁上结渣。
3.2结渣的原因
结渣的原因有诸多影响因素,它们共同作用便造成了结渣现象,从而影响着燃烧设备的安全运行。这些影响因素分别是:
1)燃料燃烧过程中,燃料层的温度高于灰的软化温度是造成结渣的一个重要原因。在灰的变形温度t,下,灰粒一般不会结渣,但达到软化温度时,熔融的灰渣形成的共熔体玲却不充分便粘在水冷壁上造成结渣。
2)壁管表面粗糙是造成结渣的另一个重要原因。这是因为壁管表面粗糙,易粘结灰分,使其达到枯化温度,从而使燃烧室温度和管壁温度都因传热受阻而升高,这时局部燃料的还原层温度达到灰熔点,从而呈熔融或软化状态,相邻的高温熔体就粘结在一起,从而造成结渣。
3)燃烧过程中空气量不足,燃料层中的三价铁还原成二价铁,而铁以Fe存在时的熔点比以Fe抖的形式
存在时低,从而使燃料的灰熔点大大降低,造成结渣。
4)燃料与空气混合不充分,即使供给足够的空气量,也会造成局部空气量不足,在空气少的区域就会出现还原性气氛,面使燃料的灰熔点降低,造成结渣。
5)风速不合理,造成炉内火焰向一边偏斜,造成局部温度过高,使部分燃料层的温度升高达到灰熔点,冷却不及时造成结渣。
6)燃烧装置超负荷运行,炉温过高,使燃料层的温度升高,达到燃料的灰熔点,而造成结渣。
7)炉膛层燃炉内的燃料直径、燃料层厚度大等都会使层燃中心的局部温度过高,达到燃料的灰熔点而造成结渣。
4、结论
1)根据试验得出生物质成型燃料燃烧装置使用双层炉排燃烧在最佳工况下结渣率为3%左右,具有轻微结渣性;
2)燃料燃烧过程中,氧化层温度最高,但氧化层铁以Fe3+形式存在,Fe3+的共熔体灰熔点高达1500C以上,不易形成结渣。而在温度相对较低的还原层,铁则以Fe升形式存在,Fe2+的共熔体熔点低,在还原层的熔融灰渣碰到水冷壁后就形成渣层,渣块粒径最大达到300mm,最大厚度达到120 mm左右。因此,生物质成型燃料的结渣大部分在还原层。
3)生物质成型燃料在双层炉排燃烧设备中的结渣率随着温度增高、过量空气系数的增大、成型燃料粒径增大、燃料层厚度的增加而会有不同程度增加。
4)分析了生物质成型燃料结渣过程及影响结渣因素,为生物质成型燃料合理燃烧控制、实现安全及经济燃烧提供科学依据。
三门峡富通新能源生产销售颗粒机、饲料颗粒机、秸秆压块机等生物质燃料饲料成型机械设备。