关键词:生物质;循环流化床;节能减排
0、引言
随着节能减排工作的广泛开展,使用农作物秸秆、稻壳等生物质能源作为主要燃料的供热设备日益增多。国家陆续出台了相应的激励政策,鼓励燃用相对清洁的可再生生物质能源。国家发改委2007年8月公布的《可再生能源中长期发展规划》中指出:全国农作物秸秆年产生量约6亿吨,除部分作为造纸原料和畜牧饲料外,大约3亿吨可作为燃料使用,折合约1.5亿吨标准煤。秸秆燃烧利用前景广阔。
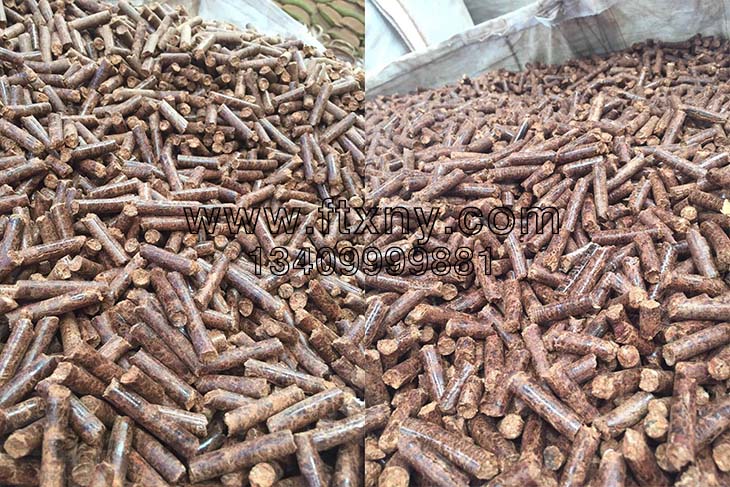
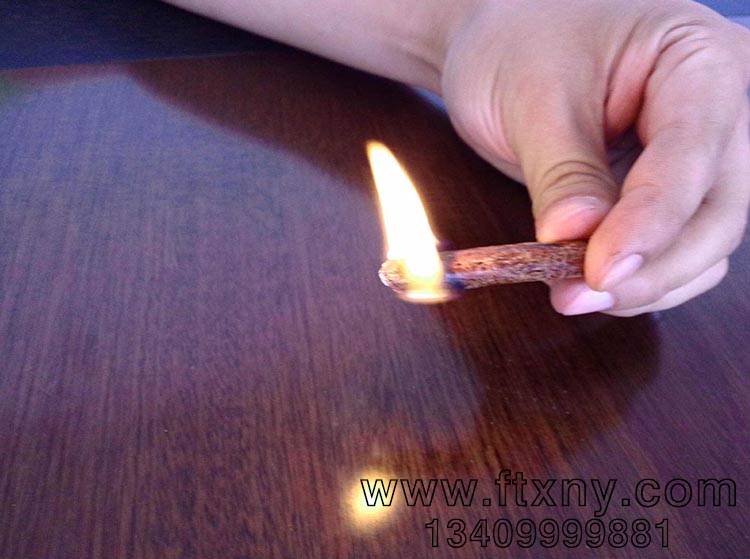
链条炉排是工业锅炉最常用的燃烧设备,园内已有相当丰富的制造和运行经验,这种燃烧设备对负荷变化和间歇运行的适应性强,符合小型锅炉房负荷多变的特点。但是链条炉排的着火条件不好和区段性燃烧,限制了它的煤种适应性和燃烧效率,当燃用难着火、难燃尽的燃料时,链条炉排上的燃烧工况就会恶化,造成炉渣含碳量高,炉渣含碳量高已成为制约层燃炉效率提高的瓶颈,一般层燃炉炉渣含碳量为20%~30%,甚至能达到30%以上。
本文提出一种新的构思,将层燃炉的炉渣和生物质燃料在同一循环流化床内燃烧。用层燃炉的炉渣帮助生物质燃料建立良好的循环,保证锅炉的正常运行,同时义使层燃炉的炉渣进一步燃烧,降低炉渣含碳量。
1、燃料特性
1.1生物质燃料特性
以北方地区常用的玉米秸秆成型燃料和稻壳为例,给出生物质燃料的特性,见表1。
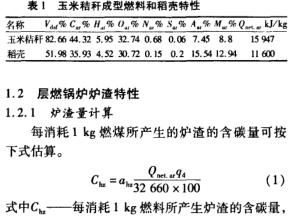
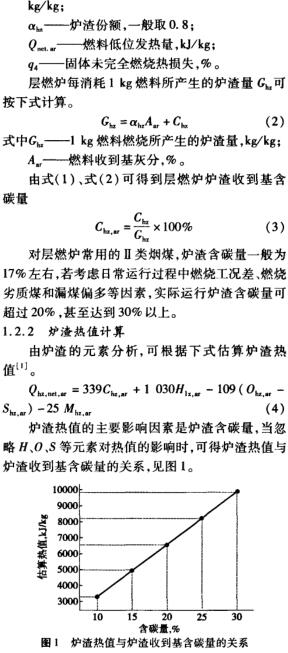
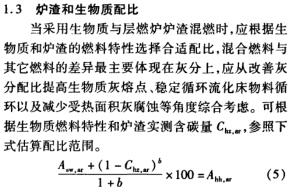
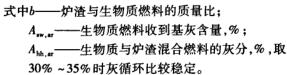
2、锅炉结构
锅炉主要由流化装置、炉膛水冷壁、高温旋风分离器、U型返料器、对流管束、省煤器等部件组成。锅炉采用双级配风,一次风从炉膛底部布风板风帽进入炉膛,二次风从卫燃带下部进入炉膛,一、二次风配比为1:1。炉膛下部卫燃带以及密相区覆盖有耐火防磨材料,密相区无受热面,稀相区除卫燃带外的四周布置光管水冷壁,经旋风分离器的烟气进入对流受热面,锅炉尾部竖井烟道布置铸铁省煤器。
3、设计需要考虑的特殊问题
3.1防止结渣
流化床可控制在800~850℃的较低温度范围高效燃烧,且炉膛内温度场分布较均匀,大大减少了熔渣生成量,从而避免生物质由于燃烧温度高而烧结。另外,层燃炉渣中有大量A1203、Mg0等高熔点物质,生物质与炉渣按一定配比混燃可以改善混合燃料中的Si、Al配比,可以在一定程度上提高生物质燃料灰熔点,有利于控制床内聚团、结渣。
3.2组织燃烧
由表1可知秸秆类生物质燃料普遍的特点是挥发分很高,一般情况下植物秸秆、木材干燥无灰基挥发分(Vdaf)可达70%~80%,所以生物质秸秆燃料比较容易着火,一般情况下在250~350℃温度下挥发分就大量析出并开始剧烈燃烧,此时若空气供应量不足或不能与空气充分混合,将会增大不完全燃烧损失,并且缺氧条件下容易产生大量不易燃尽并且分离器很难有效分离的炭黑,造成锅炉冒黑烟的现象。所以应适当加高密相区直段,使分别进入流化床的炉渣和秸秆成型颗粒充分混合,并提高二次风速,保证二次风穿透力,强化烟气扰动。
混合燃料燃烧过程中容易产生大量CO,而实验证明当烟气温度较低(≤700℃时)即便CO与空气充分混合也很难充分燃尽,为保证大量挥发分和焦炭在有限的炉膛高度范围内充分燃尽,避免在高温旋风分离器、返料器出现再燃,造成灰循环回路局部结焦,炉膛稀相区空截面风速可控制在3~4 m/s.
左右的较低范围内,延长碳粒在炉膛停留时间,并减轻分离器负荷。所以燃JH{生物质、炉渣混合燃料的循环流化宜选取较低的炉膛截面热负荷(1.5~2MW/m2)。
3.3分离器效率的选择
生物质燃料析出挥发分同时产生的同定碳由于灰烬包裹、空气渗透困难、炉膛温度较低等因素的影响,燃烧速度比较缓慢,而且混合燃料中的层燃炉渣大部分是燃烧缓慢的焦炭,为提高燃烧效率,并减少对流受热面的积灰,因此应达到一定的灰循环倍率,使焦炭充分燃尽。
当混合燃料折算灰分为30%时,一般分离器效率达到98%以上(灰循环倍率可达20以上)即可获得较高的燃烧效率,分离器效率对灰循环倍率的影响趋势如图3所示。
为了保证流化床在较低温度下稳定运行,并减少低温床料入炉份额,也要求分离器有较高的分离效率。一般情况下临界分离粒径越小,分离效率越高,目前高温旋风分离器在工业锅炉应用时其临界分离粒径一般为70~80um,设计时可以通过提高分离器入口烟气速度(20~25m/s)、减小分离器喉管直径等多种方法进一步提高分离效果,把包裹灰壳未燃尽的碳、含有碱金属的灰粒捕集下来,降低尾部受热面的积灰和腐蚀。
3.4防止积灰、腐蚀
生物质炉渣化学成分,灰粒特性等方面均与燃煤炉渣不同。由于生物质燃料灰分中K、Na等碱性金属含量大大高于燃煤灰分碱金属的含量,在锅炉对流管束烟气温度高于500℃区域容易形成高温粘结灰。层燃方式的生物质锅炉面临的对流受热面积灰、腐蚀等问题不易解决。而燃生物质流化床由于床温较低,升华碱金属的量比层燃方式少,采用与燃煤炉渣混烧的方式还可以改变生物质灰分配比,减少粘结灰的形成,并且高温旋风分离器可以将一部分升华碱金属随灰粒捕集下来以炉渣形式排出。另外,通过控制炉膛出口烟温在850qC左右、采用适当拉大管束横向节距、结合冲刷方式合理设计的受热面结构,并选择10 m/s左右较高的烟气速度等措施,流化床燃烧生物质比层燃方式更容易有效减轻高温粘结灰的形成。
生物质燃料干燥程度较好的情况下,可不用布置空气预热器,为节省对流受热面钢耗而布置省煤器。只要设计时合理选择排烟温度,避免尾部受热面结露形成硫酸液,一般不会出现堵灰、腐蚀。生物质燃料中S的含量较少,循环流化床燃烧方式可实现燃烧过程中高效脱硫,并且一部分S与碱金属生成化合物被飞灰捕集,可以减少尾部受热面的低温腐蚀。
生物质燃料巾普遍含有一定量的Cl,容易在金属管壁温度较高的部位造成严重的高温腐蚀,经验证明在受热面管壁温度低于400℃时高温腐蚀并不明显。而C1燃烧过程巾生成的HCl容易沉积在低温受热面,所以即便选择较高的排烟温度,也有可能出现尾部受热面腐蚀的情况,为此选用耐腐蚀的铸铁省煤器。
3.5燃料粒径
本锅炉适合燃用成型生物质燃料或稻壳等粒径
比较均匀的生物质燃料。由于成型生物质燃料挥发分很高,并且含一定水分,其在炉膛燃烧时,水分、挥发分的大量析出会使秸秆成型颗粒不断爆裂,所以成型颗粒的粒径要求可放宽到0~25 mm左右,由螺旋给煤机送人流化床燃烧。灰渣的粒度应控制在10mm以下。采用层燃炉渣生物质分级人炉方式,由不同的给煤机送人流化床,炉渣燃料给料口靠近布风板,生物质在炉渣给料口和二次风之间送人。
4、节能环保效果预测
以7MW热水锅炉为例进行比较。如SHL7.0 -1.0/95/70 -AⅡ热水锅炉,设计燃烧效率84% (q4为15%,q3为1%),满负荷运行4 000小时消耗Ⅱ类烟煤8 552吨(按600元/吨)。由式l、式2估算,最少可产生3 933吨含碳量20%的炉渣,并向环境排放约12 261吨C02温室气体。如果使用SHX7.o-1.0/95/70 -T循环流化床热水锅炉,玉米秸秆成型燃料与层燃炉渣(含碳量20%)混合燃料的配比为5:3,由式4估算混合燃料折算热值可达到12 510kVkg,设计燃烧效率95%(q4为4%,q3为1%),满负荷运行4 000小时消耗玉米秸秆成型燃料6 561吨(按350元/吨),燃烧层燃炉渣3 937吨(按100元/吨),向环境排放约2 740吨C02温室气体。对比计算表明,燃用生物质与炉渣混合燃料可比普通层燃炉节省购置燃料资金40%以上,另外可以减少温室气体C02排放约9 500吨以上,节能减排效益可观。
5、结论
(1)燃用生物质的循环流化床设计运行时尽量采用较低床温,并合理设计炉膛结构,选用多级送风,采用较低的炉膛截面热负荷,进而控制燃烧温度,均匀分布温度场防止结渣,并使燃料充分燃尽。
(2)采用与层燃煤炉炉渣混烧方式不但可以稳定灰循环,而且可以提高灰熔点,改善灰分配比,减轻碱金属对较高烟温区受热面的高温粘结积灰,并减少能源浪费。
(3)设计时适当提高旋风分离器的分离效率,合理布置管束,减轻对流受热面积灰、腐蚀。
(4)从燃料收集存放、以及运行过程中结渣、积灰、腐蚀等方面综合考虑,燃烧生物质燃料锅炉采用低倍率小型循环流化床,与层燃煤炉炉渣混烧整体经济效益较好,减少温室气体排放优势明显。
转载请注明:富通新能源木屑颗粒机www.ftxny.com