1、风机的磨损机理
1.1风机磨损的原因
风机叶轮磨损,实际上是一种喷砂型的固体粒
子对靶材表面的冲蚀。固体粒子冲击到靶材表面
上,一般都会造成靶材的冲蚀破坏。靶材的耐磨性
或耐冲蚀性反比于一定工作环境下单位重量的磨
粒冲击材料表面造成的靶材重量或体积损失。
风机叶片的磨损形式通常分为侵蚀磨损、化学磨损、疲劳磨损和磨粒磨损等。风机工作时,含尘气流中尘粒与气体分两相流动,气体从风机入口向出口流动时偏转900,由于尘粒具有动量,质量较大的尘粒进人流道后加速向叶片工作面与后盘的交界处、叶片工作面流动,也有少量的尘粒向叶片非工作面流动。粉尘粒子进入叶轮后与壁面相互作用,在离心流道的进口区域和整个轴向流道内,基本上是在气流的夹带及自身惯性的综合作用下以非零攻角碰撞壁面,然后又反弹进入流道内,这样引起的壁面材料的磨损是典型的冲蚀磨损;而在离心流道的出口区域内,尘粒在流道内运动了较长一段距离,大部分和壁面发生过多次碰撞,基本上沿着压力表面滑动或滚动,并对壁面有着一定的压力作用,这样造成背面材料的磨损属于擦伤式磨粒磨损,尘粒在压力面附近区域的集中更加剧了磨粒磨损的危害程度。叶片磨损主要由固粒对叶片的冲蚀磨损和固粒在叶片表面运动的擦伤式磨粒磨损组成,前者主要发生在叶片前部,后者则主要发生在叶片尾部。磨损的具体情况视叶轮材料的物理性能和机械性能、尘粒的硬度、形状、流速、入射角而定。
1.2磨损率与寿命
对于金属材料的摩擦,叶片的磨损率定义为单位时间界面被磨蚀的平均厚度,可用式(1)表示。
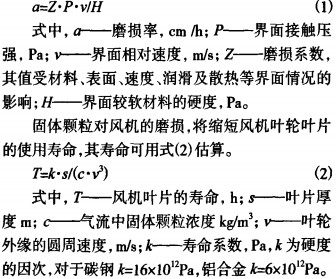
2、影响风机磨损的因素
影响离心风机磨损的因素很多,有风机本身的因素,也有系统的因素。
(1)气体中尘粒的硬度
尘粒对金属的磨损是由尘粒对金属的撞击和擦伤两种作用构成的,但其先决条件是尘粒被压入金属,使之形成一个塑性的凹坑,在大量尘粒的连续作用下,这些凹坑将逐渐形成一个塑性变形的薄层。当尘粒的作用负荷超过塑性变形层的极限强度时,这一表层即被破坏而掉落,造成磨损。当尘粒的硬度较高并超过风机流道部件的硬度时,就会打击或磨损其所接触的流道壁面,如同锉刀在工件上锉削一样。尘粒硬度越高,风机中的流道壁面就被磨损得越快。
尘粒硬度对叶轮的磨损影响可用粉尘硬度Ha与叶片材料硬度hm的比值描述,HJH越大,叶轮的磨性率越大。HJHm≤0.64时表现为软料磨损,叶轮的磨损率较低;HJHm> 0.64时表现为硬磨料磨损,叶轮的磨损率较大。
(2)叶轮的材质
叶轮耐磨性能与其材料的硬度关系很大,一般而言,叶轮材料的硬度越高,则抗冲击能力越强,耐磨性能越好。但叶轮的耐磨性不仅取决于材料硬度,而且还与材料成分有关。经过热处理后的各种不同成分的钢,虽然硬度相同,却有不同的耐磨性。如40钢和16Mn热处理后硬度相近,但16Mn比40钢耐磨性强得多。由此可见,提高材料的耐磨性,既要提高材料硬度,也要选用合适的材料。
(3)气体的含尘浓度和速度
叶轮的磨损量F与气体含尘浓度和速度的关系可用式(3)表示。
F=cvn (3)
式中,F-叶轮的磨损量,m;r—气体含尘浓度,kg/m3;v—气体的速度,m/s; n-速度指数,一般取n=2.0~3.0。
叶轮的磨损量与气体的含尘浓度成正比,粉尘浓度越大,单位时间内固体颗粒撞击叶轮叶片壁面次数和频率越高,叶轮叶片磨蚀越严重;叶轮的磨损量与气体运动速度的n次方成正比,速度越大,尘粒的离心力和动能越大,对叶轮的冲击越大,磨损越严重。
(4)尘粒的入射角
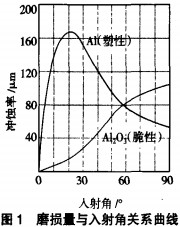
粉尘粒子的入射角是影响磨损量的一个重要参数,磨损量随入射角的变化规律如图1。对于脆性材料,尘粒入射角越大则磨损量越大,入射角为90°时磨损率达到峰值,主要是疲劳脱落;对于塑性材料,入射角为150~250时磨损量最大,主要是切削磨损。因此,确定入射角时要避开两峰值对应的入射角,选择最佳入射角,以期达到减少磨损的目的。
(5)尘粒的粒径与形状
尘粒的冲击能量E与其粒径d的立方成正比,即,尘粒的直径越大,冲击能量越大,粒子的能量增加容易击穿被磨材料的表面,使叶轮的磨损速率增加。但当粒度在50~lOOμm以上时,磨损量就不再以正比例关系增加了,而趋于一定值。
尘粒在风机流道中具有压入钢板的能力,其能力不仅取决于它的硬度,还与尘粒的几何形状和大小有关。具有棱锥或其它刃尖凸出表面形状的物体往往能在本身形状不被破坏的情况下,较表面圆滑的尘粒更容易压入硬度比它软的物体。
(6)叶片的形状
叶轮叶片形状对磨损的程度有着重要的影响。一般单直型叶片通风机,比机翼型叶片通风机耐磨,后向式叶片通风机,比前向式叶片通风机耐磨。高效机翼型叶片通风机由于其压力系数较低,叶片直径大,圆周速度高,磨损程度也大。因此,通过设计改变叶片型式和叶片角度,可以减少或避免叶轮叶片的磨损。
(7)吸附现象旧
粉尘中因含“湿”或分子吸附以及颗粒的摩擦或碰撞引起的静电吸引,使粒径较小的尘粒粘附于流道壁面上。气固两相流风机中,微粒的粘附大多出现在叶轮的出口处或突出处,它的出现会改变流道,恶化风机性能,腐蚀叶轮叶片。
3、风机的防磨措施
3.1提高除尘系统的效果
烟气中的粉尘颗粒是导致风机磨损的根源,提高除尘设备效率,降低粉尘浓度,是防止风机磨损最有效的方法。对于产尘设备和产尘点,必须设置高效率的除尘系统,决不能采取只设通风机而不设置净化设备的排尘方式。在除尘系统中,一般应将通风机安装在除尘设备之后运行,以保证风机在净化后的气流中工作,消除磨损条件。在条件允许的情况下,应尽量采用效率高的除尘设备,提高气体的净化程度。对于除尘设备,还要根据其结构特点,定期进行维护和检修,确保其正常的工作条件。
3.2控制合理的运行工况点
风机运行工况的变化,对叶轮内气固两相流动具有较大影响。当流量偏离风机的设计流量时,风机内颗粒的运动轨迹将发生变化,粉尘粒子对盘盖和叶片的碰撞位置前后移动,磨损量相应地发生改变。总的来说,当实际流量向小流量偏移时,有利于减少叶轮的磨损;偏离设计工况较多时,风机的磨损状况将恶化。因此,必须优化和合理控制风机的运行工况。对某个特定条件风机,一般最小流量等于设计流量的80%时,对减少叶轮的磨损较有利。
3.3选择耐磨风机
不同类型的风机耐磨程度不同,一般大而低速的风机抗磨性好,单板或空心翼形叶片的离心风机总比轴流风机耐磨性好。与轴流风机相比.离心风机通常可提供4-5倍的抗磨性。目前我国已生产制造出几种型号的耐磨风机,如C4-73型,适用于抽排含尘气体,M7-29型,适用于粉粒物质的输送。耐磨风机的蜗壳部分用钢板焊接,内衬有护板,以便磨损后更换。叶轮全部采用碳素弹簧焊接,叶片系前向型。在粉尘气流中工作的风机,应优先选择具有一定耐磨特性的风机。
3.4降低风机转速
从前面的分析知道,风机的磨损受其转速的影响较大,转速越高,磨损越严重。在满足了系统流量、压力要求的前提下,选择低比转数的风机,可降低风机转速以减轻磨损。
3.5提高叶片的耐磨性
(1)叶片表面进行防护处理
对叶片表面进行渗碳、渗硼、涂刷防磨涂料、喷焊耐磨合金等工艺处理,使金属表面形成硬而耐磨的保护层,可提高叶片的抗磨性。常用的是叶片表面渗碳处理,使金属表面形成硬而耐磨的碳化铁层,并保持钢材芯部的韧性。由于钢材在组织状态呈奥氏体时,吸收碳的能力最强,所以在渗碳过程中,必须把叶片加热到能使内部组织转变为奥氏体所需要的温度。但温度不宜过高,否则,易引起晶粒变大和表面层含碳过高而出现脆性,致使叶片容易产生裂纹。一般渗碳温度应控制在900℃左右。渗碳层越深,防磨效果越好,但脆性越大,叶片易断裂。实际渗碳时,渗碳层的厚度和部位,要根据叶片厚度和磨损情况以及渗碳工艺决定。
(2)叶片表面设防磨块
由于粉尘粒子在磨损部位的基本运动方式是沿着叶片的表面滑动或滚动,并对表面有一定的压力作用,在叶片工作面上沿轴向加装突出横条,可阻挡这种运动,改变粉尘粒子的运动方向,从而使粉尘粒子跳离叶片表面,如同气流在叶片工作面上形成一空气垫对其起保护作用,可以延长风机使用寿命1~2倍。在叶片工作面上加装错列的突起小块,也能起到防磨作用。风机叶片加焊防磨小块后,应对风机叶轮作静平衡和动平衡校正,以保证叶轮运转平稳。对于小型风机,可不作动平衡校正,仅作静平衡校正。
(3)叶片表面加防磨衬板
在叶片的易磨损区加防磨衬板或堆焊耐磨层,同样可防止叶片磨损。一般可在叶片工作面、非工作面、叶片头易磨损区加16Mn低合金衬板。工作面由于磨损严重,还可在衬板上堆焊耐磨层来提高其耐磨性能。如在叶片工作面的防磨衬板上可堆焊条状耐磨层,在叶片头的一定区域内堆焊3~5mm厚的耐磨层;非工作面磨损很小,仅加衬板即可。防磨衬板需要预制成与叶片形状一致,以免组装时产生焊接应力。在堆焊耐磨层之前,要对衬板进行除锈、预热处理.焊条要烘干,以防止耐磨层产生裂纹、气孔等缺陷。
(4)叶片表面粘接耐磨陶瓷
陶瓷材料具有高耐磨、高耐腐蚀、低密度、低摩擦系数、高硬度的优点。在冲角较小时,陶瓷和金属、橡胶相比磨损最小。在叶片表面粘接陶瓷材料,即在叶片易磨损部位粘接厚度1.5 mm陶瓷片,对提高叶片抗磨损能力非常有效。由于陶瓷片厚度小,对叶轮质量增加很小,不影响叶轮设计强度和风机启动时的惯性矩。值得注意的是,陶瓷材料与钢材料的膨胀差大,叶片的工作温度不能太高;必须保证粘接的复合强度,防止耐磨陶瓷在运行中的脱落;要保证叶片表面平整,没有喷涂层。
(5)设置耐磨刃口
风机叶片的头部一般磨损较为严重,提高叶片头部抗磨性能非常关键。采用由复合硼化铁组成的烧结硬质合金耐磨叶片前缘是一项有效措施。为了使风机具有良好的空气动力性能,前缘刃口的外形应制造精确,耐磨刃口可以用扩散结合电子束焊接技术制造。
3.6改进风机的结构
(1)合理选用进风口
从气一固两相流运动规律出发,分析粒子的运动及磨损机理,从气动角度改变风机中粒子的运动轨迹,是一种从设计方面改善风机磨损的方法。合理选用风机进风口就是改善风机的进气条件和含尘气流运动方式,降低风机磨损。实践证明,当采用普通圆柱形进风口时,风机磨损严重,且不均匀;当改装喇叭型进风口以后,叶片进口磨损变轻,且磨损均匀。
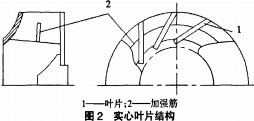
(2)变中空叶片为实心叶片
这种方法主要针对的是机翼型叶片。由于机翼型叶片是中空的,所以当叶片磨穿后会有尘粒进入,破坏风机的平衡,使风机寿命进一步缩短。为了避免这一现象,可将空心叶片做成等厚度实心直板叶片。但当叶片进出口宽度太大时,改成直板叶片后其强度和刚度会有所下降,会产生变形,此时可在位于前盘与后盘中部两个相邻叶片之间增设加强筋板(如图2)。为增加叶片的抗磨性能,在叶片进出口部位可再堆焊耐磨焊条FeO5。
(3)选用较窄的叶片
叶片的磨损率与其自身的安装角和气流的流入角有密切的关系。对于硬度较低的塑性材料,磨损量最大发生在撞击角150—300之间,其影响程度又与叶片形状有关。当叶片的压力面是圆弧形时,通常存在与尘粒构成最不利的撞击角部位,使这部位的切削能力加强,形成磨损最严重的地方。而对于较窄的直板叶片离心风机,只要合理设计叶片安装角,磨损则相对较轻。
(4)采用前置防磨叶栅或增加导向叶片
风机的磨损部位之所以很不均匀,其原因是气流中固体粒子分布不均匀,浓度大的地方磨损严重,浓度小的地方磨损轻。采用前置防磨叶栅或增加导向叶片都是从气体动力学的角度出发,控制粒子运动使其均匀分布,从而降低磨损的方法。当叶轮安装了前置防磨叶栅后,叶轮运转时前置叶栅随之转动,产生一股可驱散粒子束的气流,强制使其轨道半径减少,阻止粒子向后盘及叶根处运动,使固体粒子沿叶轮进口边比较均匀的分布,从而将粒子的集中磨损转化为均匀磨损,提高叶轮耐磨性,延长风机使用寿命。
4、风机的抗磨改造实践
某砖瓦企业一旋风除尘器配套一离心引风机,型号为№6-12。使用中发现叶轮叶片后盘部位磨损严重.平均1个月左右修理或更换一件叶轮,维护费用高,影响工艺生产。为了提高叶轮的抗磨性,决定对叶轮进行改造。本着减少投资的原则,改造中利用了原风机机壳、电机、轴及传动装置,并保持风机的流量、风压、转数等参数不变,仅改进叶轮结构及配套集流器。具体如下:
(1)叶轮改为锯齿形中盘直板叶片型叶轮(如图3)。这种叶轮的特点是叶片工作面出口处没有中盘,而使整个中盘呈锯齿形。烟气从左右前盘入口进入叶轮后,烟气中尘粒不与中盘相撞,而是随左右侧气流汇合后共同到达出口。左右侧气流汇合后使部分尘粒还未来得及到达叶轮工作面就已经飞出了叶轮,避免大量尘粒与中盘相撞而集中磨损。尽管有一部分尘粒由于与对侧的气流及尘粒相撞而消耗了能量,在离心力的作用下到达叶片对叶轮产生磨损,但是数量大为减少。因磨损面积由原来中盘根部扩展到大部分的叶片工作面,所以单位面积的磨损量减少了,且对叶片均匀磨损。
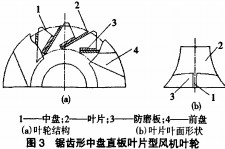
(2)改变气流中尘粒的入射角。叶片出口安装角从原30。提高到55。,使气体尘粒的入射角尽量避开叶片磨损最严重的200~300角,提高叶轮的寿命。
(3)增加叶片防磨衬板。在叶片上焊接6Mn材料的村板,增强叶片的抗磨损性能。
新叶轮使用一个修理周期(半年)以后,叶片中盘根部仅有轻微的磨损,且磨损均匀,经局部补焊校验平衡后仍可继续使用。可见,锯齿形叶轮的改造应用,较好地解决了叶轮磨损不均匀的现象,同时也大幅度地减轻了叶轮的磨损。
5、结束语
砖瓦工业风机大多数为气一同两相流风机。气一固两相流风机磨损的原因很多,有风机本身的原因,如风机结构形式、材质等;也有除尘系统状态原因,如粉尘性质、浓度等。风机的防磨损措施,大体可分为两大类:被动防磨和主动防磨。被动防磨是选取适当的耐磨材料或对被磨材料进行适当的耐磨处理。虽然被动防磨方法在防磨方面起到了一定的作用,但却不从根本上消除和缓解磨损的发生。主动防磨也称为气动防磨,主要是从气一固两相流的动力学特征人手,对流体机械本身进行抗磨损等的优化设计,对流动参数进行控制与优化配置。气动防磨才是解决带粒流磨损问题的根本。