某厂2台熟料B600倾斜链斗式输送机是用来提升由原回转篦式冷却机(Bl.6×21. 465m)出来的熟料至联合储库,因为篦冷机后面没有熟料破碎机,所以经常有大块进入输送机内。该输送机一直存在链斗易脱轨、下部轴承易损坏的问题,起初认为主要是大块多、红料多造成的。1994年10月对1号立波尔窑系统进行了技术改造后,安装了LBT24135推动篦式冷却机及熟料破碎机,但输送机的故障依旧,严重影响了回转窑的运转率。经认真分析后认为引起事故的主要原因是输送机下部结构不合理所致,1997年12月我们对2台熟料链斗输送机进行了改造,效果较好。
1、改进前下部结构存在的问题
改进前的下部密封、张紧装置的结构见图1。
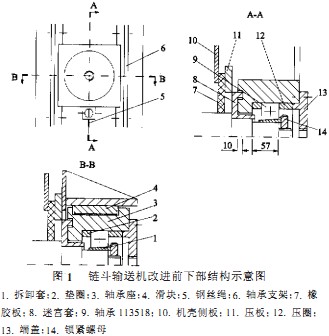
轴承座的密封是通过活套在尾轴上的迷宫套与轴承座的迷宫槽形成迷宫式密封。由于输送的是温度较高的熟料,使用一段时间后,下部机壳变形,两侧轴承支架的中心距拉大,使得轴承不能按要求装到设计位置,但又不可能在生产中更换机壳以调整轴承支架间的中心距。这样,造成迷宫套与轴承座分离形不成迷宫,失去了密封效果,轴承进灰损坏。底部机壳的密封是通过紧固在轴承支架上的压板顶住橡胶板,直接摩擦形成接触式密封,防止熟料从下部轮组自由调整孔漏出,但橡胶板的耐温程度有限,不多久就烧坏变形,再加上机壳侧板严重变形,几乎起不到密封效果。工人为了少漏料,往往用钢板将下部轮组上下自由调整的长条形滑行孔封焊死。这样一来,由重锤通过钢丝绳拉住轴承座来调整输送链斗松紧的轴承座在滑块上的滑行空间受到严重限制,致使尾轴与封焊的钢板对磨。在实际使用中,每次检修均要检查并补焊尾轴。并且滑块与轴承座的四方槽是面接触,左右易别死调整不灵。加上调整的长条孔被封焊死,根本没有自由调整的空间,经常导致链斗脱轨,每年因链斗脱轨停窑抢修的次数不少于15次,严重困扰着正常的的生产管理。
2、改进措施
针对上述问题,我们作了以下改进,见图2。

1)将机壳侧板的钢板厚度由12mm增加至16mm,为了改进密封装置,还将机壳侧板之间的距离从1170mm增至1248mm。
2)去除压板和橡胶板,增设a=16的挡料板,迷宫套材质由灰铸铁改为铸钢,迷宫深度由lOmm增加至15mm,挡料板和迷宫套焊接在一起,活套在尾轴上,紧贴机壳侧板形成接触式密封。
3)将轴承座与滑块接触的四方槽改为半径36mm的圆弧形槽,轴承座材质为区别于迷宫套,由铸钢改为灰铸铁,并增加排油孔使轴承座内多余的油脂从此孔排至滑道,起润滑作用,减少滑行阻力。
4)将原四方形滑道(800×100×25)改为半圆形滑道(800×中60×35),使轴承座与滑块的面接触变为线接触,减少了接触面,提高了调整的灵活性。在滑块上增设加油孔,端盖装上油杯,加油至滑块,减少滑行阻力。
5)在迷宫套上加装PG115×140×14的骨架油封,增强了密封效果,防止轴承进灰。
6)将垫圈改为油圈,使轴承座内多余的润滑油脂从油圈孔和排油孔排至滑轨上,减少滑行阻力,调整灵活。
7)将尾轴的轴径长度由57mm加长至75mm,增加1个20mm厚的调整垫圈,厚度还可根据实际安装情况而改变,以补偿尾轴增加的长度。改变了因机壳、钢架受热、挤压等变形往外拱造成拆卸套装不到原设计位置,而使M80 x2的锁紧螺母压不到拆卸套的现象,这样,有了可调整余地,延长了机壳、钢架的更换周期。
8)由于尾轴轴径长度加长,遂将原平面端盖改为内凹面的端盖,并将原中间加油孔改在外侧圆周上,使加油阻力减少,方便设备维护。
3、改进后效果
改进后,机壳、轴承的密封效果明显改善,漏料明显减少,只有少量的粉料冒出,轴承的使用寿命由原来的几个月延长至3~4年。轴承座调整灵活,在现场可观察到上下微微的自由滑动,因下部链轮组调整不灵的链斗脱轨事故的次数大大减少。
三门峡富通新能源销售破碎机、皮带输送机、颗粒机、秸秆压块机等机械设备。