1、故障情况
破碎机型号为1250×1250反击式破碎机,转子体为整体铸钢结构,材质为ZC35B。2001年9月,3#破碎机在运转过程中,转子体悬臂突然断裂(经查:悬臂断裂处40%截面前期有隐性断裂层),脱落的悬臂和板锤直接劈断二级转子体一组悬臂,致使两只转子体严重受损,已经完全报废。若更换两只新转子(包括相应的主轴、轴承等),配件费用将高达30万元,并且短期内配件无法供应,为此,我厂作了大胆尝试,决定利用一周时间现场焊接修复。
转子体受损情况如图1所示。
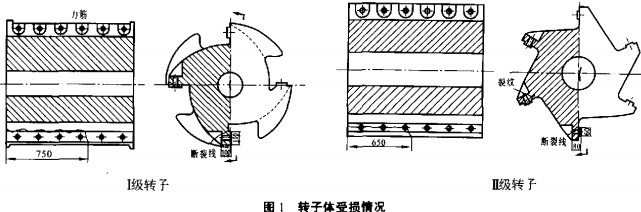
一级转子体一组悬臂齐根断裂,长度为750mm左右,二级转子体齐孔断裂,长度约650mm,并且另一组悬臂根部出现深度裂缝,裂纹长450mm,深40mm。
2、修复方案及措施
我厂做出的修复方案为:根据悬臂形状,选择若干块厚度12mm的钢板,每块竖直重叠焊接在转子体上,最后形成悬臂。
一级转子体具体修复过程如下:
(1)将转子体断裂面用气刨修平,用角磨机打磨平整,气刨刨过的碳化层要打磨干净,断裂处的力筋要尽量保留残根。
(2)制作750×140mm,厚度12mm的钢板五块,两侧及下端开坡口约1公分,再用一块厚度40mm的钢板刨成“凸”形,前凸部位作为板锤支座,前凸部位刨床加工后宽度为100
-0.12-0.30:,把六块钢板叠放整齐,预先钻好45的螺栓孔,并特制M44.5的夹紧螺栓四只进行夹紧和定位,以防止钢板在焊接时,受应力作用,产生倾斜。
(3)将钢板逐一竖直焊接到转子体相应位置,采用细焊条、小电流、多层焊接法。第一块钢板从内侧力筋处开始焊接,焊接时+采用J507低氢碱性焊条,施焊均匀,每焊完半根焊条,用手锤敲击焊缝及四周,消除应力,并将药渣清除干净后,再焊第二遍,直至坡口内填满为止。然后再叠加下一块钢板焊接,下一块钢板要紧贴头一块钢板,并用特制的M44.5螺栓进行定位并紧固好,钢板上端的接缝处先点焊几处,防止钢板错位和钢板问形成缝隙。重复这一操作,直至焊好全部钢板。
(4)所有钢板焊接后,在上端钢板接缝处,用气刨刨出约l公分的坡口后焊接,从而使所有钢板焊接成整体,形成悬臂。
(5)在断裂的力筋处,按形状平放厚度40mm的钢板三块,用A302不锈钢焊条周边焊接。因不锈钢焊条与铸钢母材熔敷较好,焊层稳定,抗拉强度大。每焊完一块后,再平整的放置下一块钢板同样焊接,力筋处也用不锈钢焊条。修复情况如图2所示。
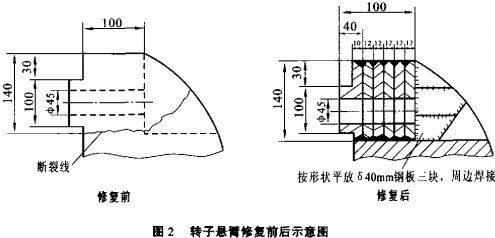
(6)由于转体体修复一侧,偏重13公斤,为求平衡在其对应的一侧焊接一块同样重的钢板。
二级转子体的修复方法相似,不同之处是:气刨刨平断裂面时,刨至悬臂螺栓孔的一半,根据悬臂形状,用六块650×60mm厚度同为12mm的钢板叠加焊在一块,焊接后悬臂上螺栓孔处形成半个孔,再用气刨吹成的∮38螺栓孔。另一处裂缝处理:用气刨顺裂纹挖成450×65×40mm的凹槽,打磨平整后,逐一平放厚度20mm的钢板两块,用不锈钢焊条周边焊接。
我厂3#破碎机自2001年9月修复后,数月后只是在力筋处发现轻微裂纹,及时进行了焊修处理,现运行状态良好。此次修复,在现场施工,不需要对破碎机进行大的解体和拆装作业,在短时间内完成,缓解了生产压力,仅用焊条约35kg,维修材料费不足千元,避免了两只转子体的报废,取得了较好的经济效益。