2.1.3.3补充化学益生素
化学益生素可被动物肠内有益微生物作为营养物吸收利用,促进其生长繁殖,以此抑制有害细菌的生长。低聚糖有多种,如异麦芽低聚糖、大豆低聚糖、低聚果糖、半乳寡糖、乳果寡糖、低聚木糖、龙胆寡糖和甘露寡糖等。
2.1.3.4科学合理的加工和贮存
尽量降低益生菌产品的水分含量,对于厌氧活菌制剂应尽可能少接触氧气,可进行包被或采用胶囊化处理,产品尽量在低温下保存,有条件的可以冷藏保存,同时尽量减少存储时间。
2.2酶制剂
酶制剂的发现最早源于人们对发酵的关注,1897年用酵母细胞提取物把糖发酵成了酒精和二氧化碳,证明是细胞内容物在此过程中起到了关键的作用,称该物质为酶,随后将该物质以晶体结构提取出来,并最终证明这些酶的本质是蛋白质,自此,酶制剂理论不断被完善和丰富。
2.2.1酶制剂的实质和作用:
酶制剂发挥作用的实质是通过对特定底物的化学结构的专一性分解或合成,发挥高效的生物活性作用,提高生物反应的进行速度。饲料酶制剂重点是通过在饲料中添加相应的酶制剂,降解饲料中对应的底物,通过对底物的分解,或释放出供动物吸收利用的养分,或减轻该种底物的抗营养作用。综合各种资料,对酶制剂作用的描述可以概括为以下几点:
(1)分解饲料中非淀粉多糖,降低肠道粘度,提高饲料有效能值;
(2)促进饲料蛋白质、淀粉、脂肪和其它营养物质吸收率,降低料肉比或料蛋比;
(3)防止动物后肠道的过渡发酵,预防或改善肠道腹泻的发生,改善肠道微生态平衡,提高免疫力,促进动物健康;
(4)有利于开发非常规饲料资源,缓解饲料原料供需矛盾,降低饲料成本;
(5)调整肠道机能,减少粪便有机物的排泄,提高养分利用率,减少环境污染;
(6)提高动物产品品质,促进动物生长和生产性能的稳定。
2.2.2植酸酶的历史和现实反思
植酸酶作为酶制剂的一种,是目前在饲料中应用最广泛,用量最大的酶种。对饲用酶制剂应用历史的重新审视和回顾,对目前了解其它酶制剂的发展和应用,具有重要的参考价值。1995年以前,国内对植酸酶知之甚少,一直到2000年,对植酸酶在饲料中的使用仍处于怀疑和犹豫阶段,生产推广植酸酶的厂家在此阶段承担着介绍植酸酶功用的责任,2000—2003年期间,约有25%的厂家开始接受、选择并使用植酸酶。2004·2007年间,使用植酸酶的厂家增加到80%以上,植酸酶推广厂家开始增多,从最初选择使用具有品牌影响力的产品到尝试使用价格便宜的产品,市场价格竞争激烈,产品良莠不齐。2008~2010年,饲料厂家对植酸酶的使用已经相当普遍,随着市场竞争的白热化,产品已经处于微利状态,缺乏实力的植酸酶厂家逐渐被淘汰,市场得到规范,价格相对平稳。
纵观植酸酶在饲料中应用历史,我们可以得到以下启示:1酶制剂在饲料中的应用,以植酸酶作为典型代表来分析,在理论和实践中是切实可行的,酶制剂能够在动物肠道中发挥生物活性作用;2酶制剂作为一种生物制品,在饲料中应用的性价比不是固定不变的,会随着时间的推移持续发生变化,这是由于菌种选育,生物工程技术和发酵工艺技术在持续提高,国内市场最初销售的是500单位酶活的植酸酶产品,是因为当时发酵表达活力很低,后来随着技术的提高,生产销售的植酸酶活性也持续提高.相应的价格不断降低。因此性价比提高后,在饲料中添加的量也持续增加,得到了良好的投入产出比。3厂家对出现新型的饲料添加剂,特别是生物制剂要高度敏感,及时掌握,通过小规模试验和大规模试用,科学地进行分析评估。对植酸酶的接受越早,越能从中早受益,早使用植酸酶的厂家,就可有效降低成本,提高产品竞争力,扩大市场占有率。使用植酸酶早和晚的时间差,可使饲料厂家在市场上的竞争态势发生逆转。
三门峡富通新能源生产销售的饲料
颗粒机是养殖户们很好的选择。
饲料颗粒机以及生产的饲料颗粒如下图所示:
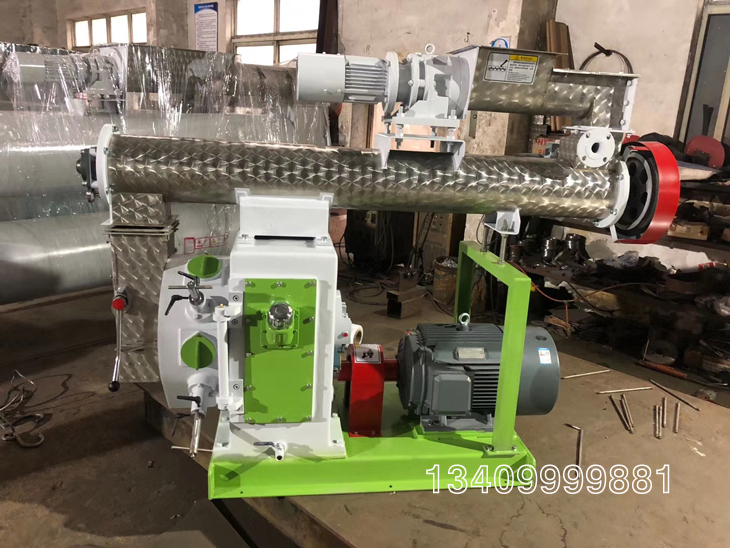
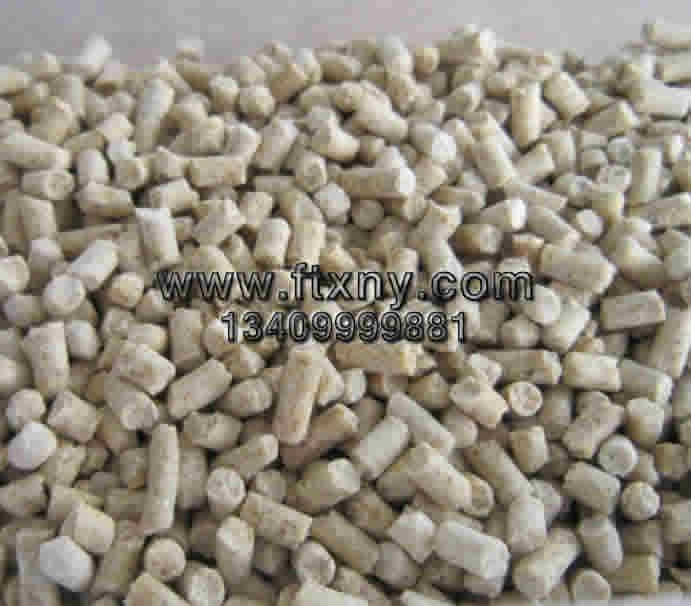
2.2.3酶制剂生产的历史和现状
国外研究酶制剂历史较早,应用也相对普遍,国内在动物营养上的研究较晚。80年代末90年代初,国内的科研单位开始关注酶制剂的研究,在饲料工业的推广应用则更短,但经过近几年的迅速发展,国内酶制剂厂家由原来简单模仿到自主开展研发,进行科技攻关,已在多种菌种上拥有了专利。上世纪90年代,国内饲料酶制剂企业基本没有自己的发酵工厂,均以国内外采购各种原酶进行复配,同时缺乏饲用酶制剂的国家标准,没有科学统一的衡量指标,产品良莠不齐,市场秩序混乱。近10年来,随着酶制剂理论研究的深入,酶制剂企业实力的增强,建立了多家饲用酶制剂发酵基地,大规模自主开展酶制剂特别是非淀粉多糖酶的生产发酵。
2.2.4酶制剂发酵方式和方法
主要分为液体发酵和固体发酵,近几年由于液体发酵具有自动化程度高,发酵工艺可控性强,发酵规模大,产品质量稳定等优势,逐渐取代了固体发酵,成为酶制剂生产最常用的方式。在具体发酵方法上,又分为单菌种单酶发酵、单菌种多酶发酵和多菌种多酶发酵等方法。
单菌种单酶发酵是发酵体系中用一种菌株,通过发酵培养生产一种酶制剂,这是目前液体酶发酵中最常用的方法。多菌种多酶发酵是通过在一个发酵罐内同时接种上几种不同菌种,每个菌种可产生不同的酶,经过发酵培养后,就可以同时产生多种酶制剂。这种发酵方法难度在于不同菌种的培养条件需要接近,要求不同菌种处于同一发酵技术条件下均可正常增殖表达,一般需要是同大类微生物才可以采用这种方式发酵。
单菌种多酶发酵是发酵体系中用单一菌种发酵培养,产生多种酶制剂的技术方法。该方法需要通过生物工程的手段,将不同来源的产酶基因克隆到一种微生物载体上在发酵培养过程中生产表达出几种酶。如果采用自然筛选的菌种进行单菌种多酶发酵,则生产出来的多种酶的活性和比例往往不符合饲料配方要求,导致使用效果不如基因工程菌种生产的多酶产品。
2.2.5 酶制剂的作用发挥和影响因素
2.2.5.1酶制剂的作用发挥
根据目前国标或行标中规定不同酶制剂的酶活概念,就能简单的分析出该种酶的分解底物的作用大小。例如淀粉酶:1克酶粉,在一定条件下,l小时液化l克可溶性淀粉(转变成糊精,麦芽糖和葡萄糖),即为1个酶活力单位。如果采用的淀粉酶活为1000单位/克时,则在合适的消化条件下100克该产品可以将100公斤可溶性淀粉消化。蛋白酶:在一定条件下,1分钟水解产生1微克酪氨酸为一个酶活力单位。如果蛋白酶为10000酶活单位/克,则在合适的消化条件下,Iq0克蛋白酶消化l小时可以产生60克的酪氨酸,以酪氨酸占蛋白质的1/20计算,则能分解1.2公斤的蛋白质。纤维素酶:在~定条件下,每分钟降解释放1μmol还原糖所需要的酶量为一个酶活力单位U。采用活性为1000单位的纤维素酶,则100克产品消化l小时可以分解出6摩尔即1. 08公斤的葡萄糖。木聚糖酶:在一定条件下,1分钟内从燕麦木聚糖中产生了lμmol木糖所需的酶量,为一个酶活力单位。100克10000酶活单位的产品可在合适的消化条件下,消化1小时可以产生60摩尔即9公斤的木糖,按酶解率10%计算,则可分解了90公斤的木聚糖。通过对概念的分析,可以简单推测在饲料中加入100克不同种类的酶制剂,对饲料性能的巨大提升作用,当然由于肠道中的实际内环境和各种酶概念中要求的条件存在很大的差异,肠道内的环境不可能像体外实验操作那样发挥最佳的降解底物的功能,所以刚才列出的数据可作为对酶制剂作用评价的参考,实际作用的发挥会因肠道内各种因素的影响而有较大变化。
2.2.5.2影响酶制剂使用效果的因素
影响酶制剂使用效果的因素分为产品自身因素和过程影响因素。产品自身因素包括耐温性、分解底物的能力、酶颗粒大小;过程影响因素包括矿物元素、胃酸和胆汁酸、其它酸化剂、水分等。不同基因来源的菌种,所生产的酶对温度的耐受性不同,相同基因来源的基因,可能因在不同载体系统中表达后的糖基化不同,对温度的耐受性也存在差异,目前通过选育和修饰手段生产出的酶制剂,特别是非淀粉多糖酶已经能够耐受普通制粒高温。同种酶可能因为基因来源不同,对不同谷物底物的分解能力不同,即使这两种酶的酶活完全相同,这是因为根据目前的酶活概念,尚无法从各个角度对酶制剂进行全面科学的概括和评价。所以,对酶制剂可能产生的效果评价,要在参考酶活高低的基础上,通过对其它性能进行对比,才能更加科学合理。酶制剂要发挥对底物的降解作用,必须要同底物分子充分接触契合,所以在相同酶活条件下,酶制剂的颗粒越小,在饲料中的有效颗粒数就会越多,和底物的结合机会就会越大,就越能发挥生物活性作用。但当酶制剂的颗粒数越小时,酶分子的活性也就会受到饲料中过程影响因素对酶分子活性的作用,使酶活下降甚至丧失。