环模
制粒机广泛地应用于饲料工业、新能源技术和制药等领域,而环模和压辊是其关键部件。制粒过程中物料是在环模和压辊的强制挤压作用下通过小孔成形的,因此环模和压辊的工作性能直接影响物料的成形率、颗粒质量。国内生产的环模使用寿命短已是个不争的事实,环模的力学性能是影响环模使用寿命的重要因素,对环模进行力学分析具有重要意义。
1、成形过程分析
环模和压辊是
颗粒机的心脏部件。工作时,环模由电机带动旋转,由于环模与物料之间的摩擦力和物料与压辊之间的摩擦力使得压辊自转。环模和压辊的旋转使物料被强制挤压,最后物料成条柱状从环模孔挤出,再由装在环模外面的固定切刀切成一定长度的颗粒,如图1所示。
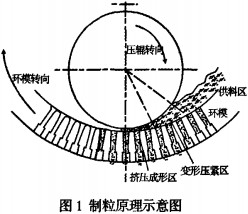
环模制粒机的颗粒成形过程,是建立在粉粒体间存在间隙的基础上的。粉料在温度、摩擦力和挤压力等综合因素的作用下,使粉粒体的空隙缩小,形成具有一定密度和强度的颗粒。根据粉料在挤压过程中不同的状态,将粉料分为3个区,即供料区、变形压紧区和挤压成形区,如图1所示。(1)供料区:物料基本不受机械外力的影响,但它受离心力的影响(环模旋转),使粉料紧贴在环模的内圈上。(2)变形压紧区:随着模、辊的旋转,物料进入压紧区,受到模辊的挤压作用,粉料之间产生相对位移。随着挤压力的逐渐增大,粉粒体间空隙逐步减小,物料产生不可逆的变形。(3)挤压成形区:在挤压区内,模辊间隙较小,挤压力急剧增大,粉粒体之间接触表面积增大,产生较好的粘接,并被压人模孔。
2、挤压过程力学模型
显然物料在三个区域所受的外力不同,进而环模沿周向所受的作用力也不相同,下面分别对位于三个区域的环模内表面受力情况加以分析。
2.1供料区
物料基本不受机械外力的影响,因此近似认为供料区环模不受力。
2.2挤压成形区
位于挤压成形区的环模内表面受力情况与模孔入口处受力基本相同,其模孔受力模型,如图2所示。式中:P -预紧压强(N/mmz);v-物料泊松比;r—模孔半径
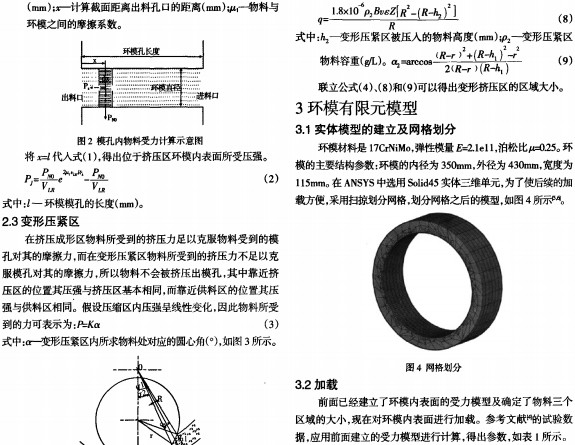
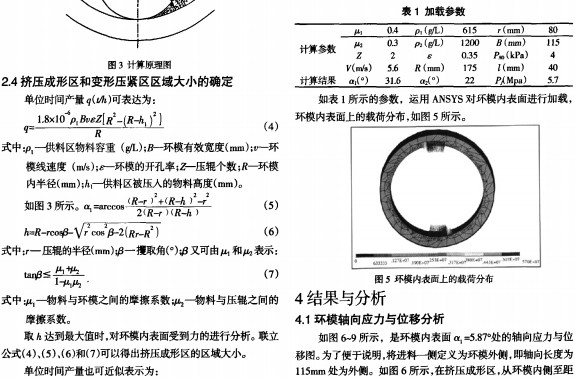
环模内侧19.167mm处,环模内表面所受到的力较大,最大为20.8Mpa。从距环模内侧19.167mm处至环模外侧,环模内表面所受到的力较小,最小值为6.8Mpa。如图8所示,在变形压紧区,从环模内侧至距环模内侧19,167mm处,环模内表面所受到的力较大,最大为20,4Mpa。从距环模内侧19.167mm处至环模外侧,环模内表面所受到的力较小,最小值为8.2Mpa。如图6、图8所示,无论在挤压成形区还是变形压紧区,环模所受到的应力从里侧到外侧逐渐减小。如图7、图9所示,无论是在挤压成形区还是在变形压紧区,环模内表面位移变化均呈线性变化趋势,环模外侧的位移变化比较大,由受力分析可知,环模内表面外侧受到的挤压力较小,这将造成环模里侧的磨损较大,环模外侧的磨损较小。
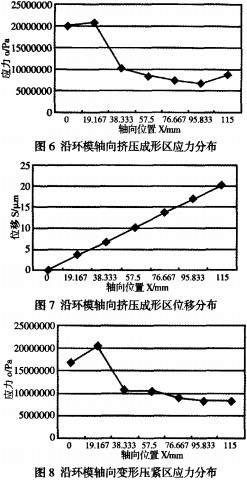
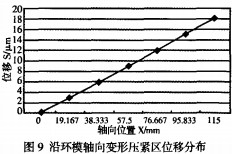
环模实际磨损照片,如图10所示,环模与压辊的磨损沿轴线方向呈现不规则磨损,压辊与环模的磨损均是两头磨损较严重,中间磨损较少。
有限元分析结果与实际磨损情况的对比,证实了载荷在环模轴向方向不是均匀分布的,环模外侧物料较多,造成环模外侧磨损较大。
如图6、图8所示,从环模轴向38.3mm处开始,环模应力比较稳定,不会造成环模外侧磨损比环模中部磨损大,这说明r物料沿轴向的均匀分布有利于改善环模的磨损情况。
4.2环模周向应力与位移分析
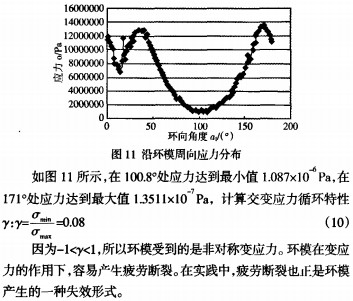
如图11所示,是环模内表面距环模内侧38.3mm处应力,其横坐标的周向角度是以环模的圆心角来计的,00所在的位置是环模与压辊距离最近处,然后依次经过挤压成形区、变形压缩区和送料区。由于环模所受到的力沿圆周方向是对称的,因此做曲线时取了环模的一半来研究。
因为-1<y<1,所以环模受到的是非对称变应力。环模在变应力的作用下,容易产生疲劳断裂。在实践中,疲劳断裂也正是环模产生的一种失效形式。
5、结论
对环模内表面进行了受力模型的建立,应用ANSYS,对环模进行了有限元分析,分析表明:(1)物料在环模内表面沿轴向是非均匀分布的,物料在外侧分布较多。(2)环模内侧磨损较严重的主要原因是环模是悬臂梁结构;环模外侧磨损较严重的主要原因是物料在环模的外侧较多;物料层沿环模轴向均匀分布有利于改善环模的磨损情况。(3)疲劳断裂是环模的一种失效形式。
富通新能源生产销售
木屑颗粒机、秸秆压块机等生物质成型机械设备,同时我们还有大量的生物质颗粒燃料。