
生物质锅炉新闻动态
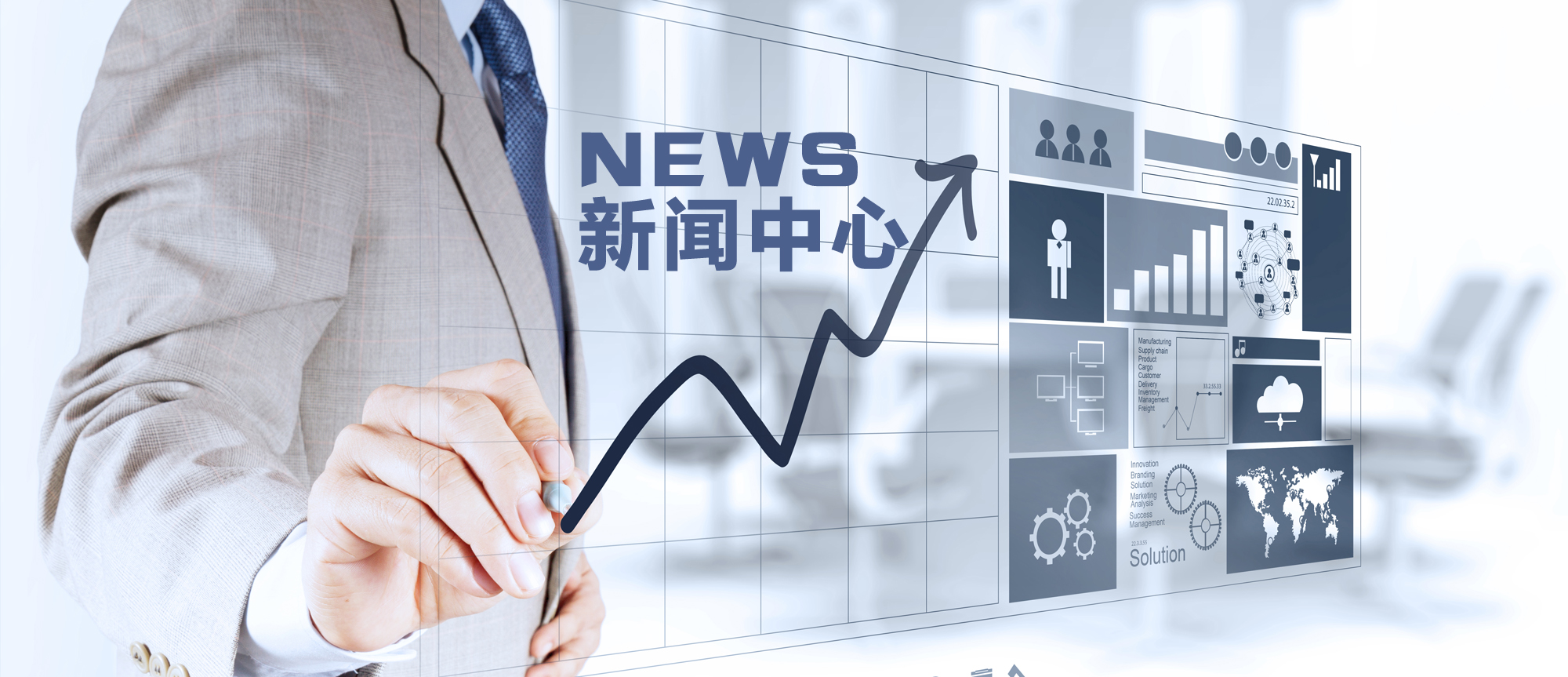
富通新能源 > 动态 > 生物质锅炉新闻动态 > > 详细
75t/h燃煤锅炉改烧高炉煤气的技术关键及工程实践
发布时间:2013-06-22 08:07 来源:未知
1、前 言
高炉煤气是冶金行业生产过程中的副产品,产量大,热值低,燃烧相对困难,且有一定的毒性,受其燃烧和化学特性的限制,要作为日常燃料输送和燃烧有相当的难度。据统计,高炉每消耗1t焦碳可产生3800—4000 m3高炉煤气,大型钢厂焦铁比约为0.36,年产200—300万t钢,高炉煤气产量高达(27~41)×108m3,除去高炉本身加热空气消耗约50%,剩余的高炉煤气达(14~21)×108m3。为节约能源、降低成本、减少环境污染,把高炉煤气作为锅炉燃料是一种适宜的选择。但由于锅炉大都属于燃煤锅炉,燃料的改变使燃烧工况发生很大的变化。为使其安全稳定运行,必须对锅炉结构进行相应的技术改造,以适应燃用高炉煤气的需要。
2、高炉煤气的燃烧特性
高炉煤气的可燃成分主要是co,容积含量约为30%,由于含有大量N2和C02(占63%~70%),故发热量较低,仅为3 762~4180 kj/m3,着火温度530~650 ℃,还含有大量惰性气体,故着火困难;燃烧温度不高,理论燃烧温度约为1200℃,比煤低很多,低热值特性高炉煤气火焰温度不高,锅炉炉膛温度水平降低。惰性气体阻碍可燃成分与空气的充分混合,减缓燃烧化学反应速度和火焰传播速度,从而使煤气燃烧难以完全,而且燃烧稳定性差,富通新能源生产销售生物质锅炉,生物质锅炉主要燃烧木屑颗粒机压制的生物质颗粒燃料。
3、高炉煤气与燃煤的燃烧特性差异
3.1炉内火焰辐射传热特性差异
高炉煤气燃烧后的烟气中以co2为主,约占90%,C02在红外光谱区的某些光带内具有一定的辐射和吸收能力,但辐射传热比燃煤时弱。
3.2烟气量的差异
由于高炉煤气热值低、惰性气体含量高,耍保证锅炉具有燃煤时的蒸发量,必然要送入大量的高炉煤气,从而导致炉内烟气量大大增加。
3.3热有效系数的差异
相对燃煤而盲燃气比较干净,受热面的积灰和污染比燃煤时减轻,故传热系数和热有效系数增加。根据热力计算标准,烟气进口温度大于400℃的对流受热面,热有效系数取0. 85,燃煤时一般取0.55—0.7。但应注意:当燃煤改燃气时如果受热面没有吹扫干净,则热有效系数只能按燃煤时取;高炉煤气含尘量大且细密,运行时间过长,热有效系数将小于0. 85,应考虑定时吹灰。
4、燃煤改烧高炉煤气的技术关键
4.1燃烧器选择及其布置
选择烟气卷吸性能好、能强化着火初期燃烧、稳燃性好的燃烧器,如预燃室开缝钝体燃烧器。众所周知,钝体具有很好的卷吸稳燃性能,同时,该燃烧器又因钝体中间开缝流人空气给燃烧初期补充了大量的氧气而强化了着火初期的燃烧,因此,着火点离燃烧器喷口很近。甚至在燃烧器内已大部分完成燃烧。开缝钝体燃烧器的这一着火燃烧性能刚好适应了低热值煤气的燃烧要求。
由于高炉煤气炉内辐射能力差,为增加水冷壁的吸热量,可考虑采用压低火焰中心、增大切圆的办法,以增大气流充满度,延长可燃物在炉内的停留时间,强化烟气对水冷壁管的直接冲涮,增加水冷壁的对流吸热量。
4.2凝渣管改造
为增加炉内的吸热量,降低炉膛出口的烟气温度,可考虑通过增加凝渣管排数的方式来增加辐射受热面积,采用这种方法同时还可带来强化对流传热的好处。计算表明75t/h燃煤锅炉凝渣管每增加1排可增加受热面积约13m2。该锅炉凝渣管的纵横向节距较宽,为这一改造提供了可能。
4.3省煤器改造
为降低排烟温度,提高锅炉效率,必须增加锅炉尾部受热面,尾部受热面中以高温省煤器传热温差最大,因此增加高温省煤器的面积效果最佳。
4.5尾部烟道系统改造
由于高炉煤气发热量低、惰性气体含量高,因此燃用高炉煤气时,锅炉的烟气量及阻力都将增加,为此,一般须考虑扩大尾部烟道流通面积降低流动阻力及增加引风机引风能力。
5、燃煤锅炉改烧高炉煤气的工程实践
5.1锅炉简介及改造要求
某钢铁公司热电厂WG275/39-6锅炉设计燃料为煤粉与煤气混合燃料,钢球磨煤机中间储仓式热风送粉系统,直流燃烧器四角切圆燃烧。改造前因煤气供应量很少,实际运行时以烧煤粉为主。
应厂方要求,改造时按全烧煤气(混合煤气/高炉煤气-1/13.8)进行设计,煤气的燃料特性如表1所示,并要求当煤气不足时能实现煤粉与煤气混烧,以保证出力要求。全烧煤气时锅炉的主要技术指标为:过热汽流量≥65 t/h、锅炉热效率≥80%、排烟温度≤180'C、过热汽温不超温、引风机出力满足出力要求。
5.2改造方案
5.2.1燃烧器改造
为提高燃烧效率及增加水冷壁的对流吸热量,对其总体布置及结构设计作了以下调整:a.考虑到煤气量不足时仍要求锅炉能满出力运行,设计时仍保留了2个煤粉喷口、1个二次风喷口及顶部的三次风喷口,其结构及布置与改造前相同;b.燃烧器采用预燃室开缝钝体燃烧器为压低火焰中心,增大气流充满度,延长可燃物在炉内的停留时间,高炉煤气喷嘴出口轴线在水平方向偏转25。,垂直方向向下偏转25口,混合煤气喷嘴在水平方向偏转15。,向下偏转15。;c.煤气燃烧器采用了大切圆布置,如图1所示,高炉煤气燃烧器的假想切圆直径为∮=4 047 mm,混合煤气燃烧器的假想切圆直径=2 087 mm。大切圆布置可大大强化烟气对水冷壁管的直接冲涮,增加水冷壁的对流吸热量。
5.2.2对流受热面改造
根据原受热面布置及剩余空间的情况,经多次校核热力计算,确定增加高温省煤器和凝渣管的面积,具体方案为:a.在原有高温省煤器的上方再增加1级省煤器。管子纵向新增16排,新增加的省煤器管其纵、横向节距,其布置方式与原有高温级省煤器完全相同.b.新增3排凝渣管,即按烟气流向,将原第2,3,4排凝渣管每排管相间改成2排管,然后每根管采用串并联结构在凝渣管下部一分为二,在近炉顶管处汇合并与原来的凝渣管穿墙管相接而送入汽包。改造后的高温省煤器与凝渣管的面积分别增加80%和142.5%,增大了凝渣管对炉内高温烟气的曝光率,使凝渣管束能吸收更多的炉内辐射热量。另外,烟气的横向流通面积由24m2减小到13m2,烟气流动速度增加将近1倍,强化了气流对凝渣管束的冲涮作用,这将大大强化对流传热,从而有利于降低烟气温度和维持蒸发吸热量与蒸汽过热吸热量间的合理匹配。
5.3尾部烟道系统改造
由于锅炉改造后绝大部分时间燃用煤气,只有当煤气中断或严重不足时补入部分煤粉燃烧以满足出力要求。因此锅炉运行时大部分时间不需要除尘,但烟气流量很大。阻力计算表明,全烧煤气时引风机不能满足锅炉满出力运行要求。为保证在不更换引风机的前提下的锅炉满出力运行,对引风系统进行了图2所示的降阻改造——增设烟气旁路。当全烧煤气时切换除尘器进口烟气挡板使烟气经旁路直接进入引风机;当有煤粉投入时切换烟气旁路挡板使烟气经过水膜除尘器除尘后进入引风机,这样,将有煤粉燃烧时的除尘运行要求与全煤气燃烧时引风机的大容量低阻力要求有机地统一起来。
5.4改造效果
改造后对锅炉进行了整体测试,实验数据见表2所示。改造后还进行了煤、气混烧实验,实验表明,煤、气混燃烧时锅炉具有很强的超负荷能力,最大蒸汽流量可达88 t/h,此时排烟温度只有150℃左右,过热汽温正常,但未燃碳损失偏大。
6、结 论
煤改气工程的实践及试验测试表明,该煤改气关键技术与实际改造吻合得较好,说明该技术能够成功运用于燃煤改燃高炉煤气的改造,可供类似锅炉改造工程参考。