350
颗粒机(环模直径为350 mm,孔径2.5 mm)专用于生产颗粒乳猪料。
2004年新机使用后,环模内固定压辊的支承轴频繁出现断轴故障,平均20d换轴一次,最短2d一次,每次1~2根。设备生产厂家人员分析故障原因后认为:频繁发生断轴是由于颗粒料含乳清粉成分偏大所引起。
断轴问题不仅影响颗料饲料正常生产,还增大制粒生产成本。为解决频繁断轴故障,2年多来,厂家先后采用增大支承轴轴径(从+=18 mm增大至22 mm),更换压辊轴套等多种改进措施,使断轴频率稍有降低,但故障一直没有得到根本解决。
三门峡富通新能源生产销售饲料颗粒机、颗粒机、
秸秆压块机等生物质燃料成型机械设备。
为找到消除断轴办法,2007年我们对故障原因进行分析,依据分析结果,加工2支有弹性的支承轴并安装上机试用,结果表明:在制粒工艺参数相同情况下,弹性支承轴寿命超过210 d(至2008年6月21止),尚未发生断轴现象,很好地解决了断轴问题,且产量不下降。
同时我们了解到同行的制粒机也存在类似的问题。为给同型号制粒机用户提供一个参考,现将解决支承轴断裂方法介绍如下。1支承轴的作用与环模、压辊的结构关系(见图1a、图1b)
从图1a、图1b可见,制粒装置的环模内有2个压辊(含匝辊轴).2根支承轴和一块前板;支承轴的一端分别以螺纹紧固在座板上,另一端分别穿接前板中间2个孔位对前板起支撑作用,前板对2个压辊的悬臂端起固定作用(压辊悬臂轴端有摆动的角度y1,所以需由前板固定)。2个压辊与环模有装配间隙B1、B2。当环模转动时,两个压辊随环模转动,当粉料被喂入环模和压辊形成的挤压区即被逐步挤压,并从环模孔挤出形成颗粒料。
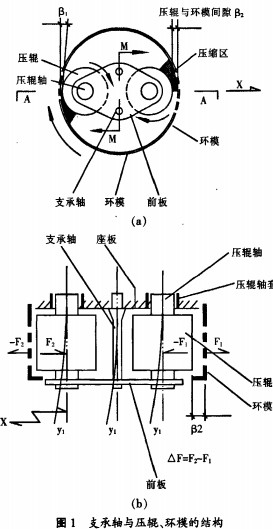
2断轴原因分析
我们分析,挤压粉料过程压辊是有振动的,而振动结果引起支承轴断裂。造成压辊振动的原因是2个压辊受到往复变化挤压力而引起的。从图la中可见,当粉料被压辊挤压出环模过程中,粉料对压辊同样产生很大的挤压力:由于喂人到两个压辊间隙粉料量瞬间不能绝对相等,因此间隙B.、B:所形成的挤压力(x轴向)分别对2个压辊产生方向相反、大小不等的推力F2和-Fi,由于F-Fi≠O,所以动态推力差AF=F2-FI随之产生;若AF足够大且在往复变化的条件下,2个压辊(与前板)便发生X轴方向振动。
压辊振动还与环模转速有关,环模每转动一定角度都可能使AF方向和大小发生变化,如按环模转速=360 r/min分析,压辊振动频率应远大于6 Hz。
由于压辊和前板(见图la)产生X轴方向振动,而起支撑前板作用的支承轴体强度不足以抑制振动的发生,所以其悬臂端也随前板一起振动:振动使轴体产生反复弯折作用,而轴体揉性又不够,一段时间后,材料产生应力疲劳,继而引起断轴,这是支承轴断裂的主要原因(见图2)。
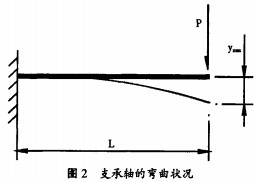
除X方向的振动外,如果考虑到挤压粉料时环模会有微小的弹性变形和径向跳动,前板(因压辊挤压粉料而产生的扭转矩M),压辊轴与衬套间隙磨损增大等因素影响,压辊与前板振幅会更大,支承轴受力状况更为复杂,更容易发生断轴情况。
3解决断轴方法
断轴的发生证明支承轴是处于振动受力状态的,而解决断轴简易方法是改变支承轴的结构以适应振动的要求。据此分析我们重新设计支承轴并满足以下要求:
①支承轴的尺寸符合原轴装配要求:
②支承轴固定后能承受前板产生的扭转矩M;
③支承轴的截面积S≥原轴Sl,保证支承轴的强度要求:
④考虑支承轴自振频率远大于6 Hz;
⑤保证轴端的最大振幅处于材料的弹性极限范围内。在环模的约束下,支承轴悬臂端振动的幅度B是有限的(B≤1.5mm),设计支承轴端点挠度yn≥B。。按轴悬臂梁挠度公式(参见<机械工程设计手册》)计算:
Y
max=PL
3/3EI≥1.5mm
式中:p一轴端载荷(N);
L一杆长(mm);
E一材料弹性模数(MPa);
I—截面轴惯性矩( mm
4)。
按上要求,我公司所加工的弹性支承轴在使用中达到了预期效果并验证上述分析和计算是正确的。图3所示是外形图,图3中弹性段具体结构是以多薄片组合而成。
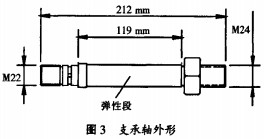
通过改变支承轴结构解决断轴难题,我们的体会是,有上述类似现象的350制粒机用户,如将原有支承轴改为弹性轴后,轴体寿命可延长5倍以上,甚至可消除断轴现象;这对降低制粒成本和稳定生产均有明显效果。