
烘干搅拌输送新闻动态
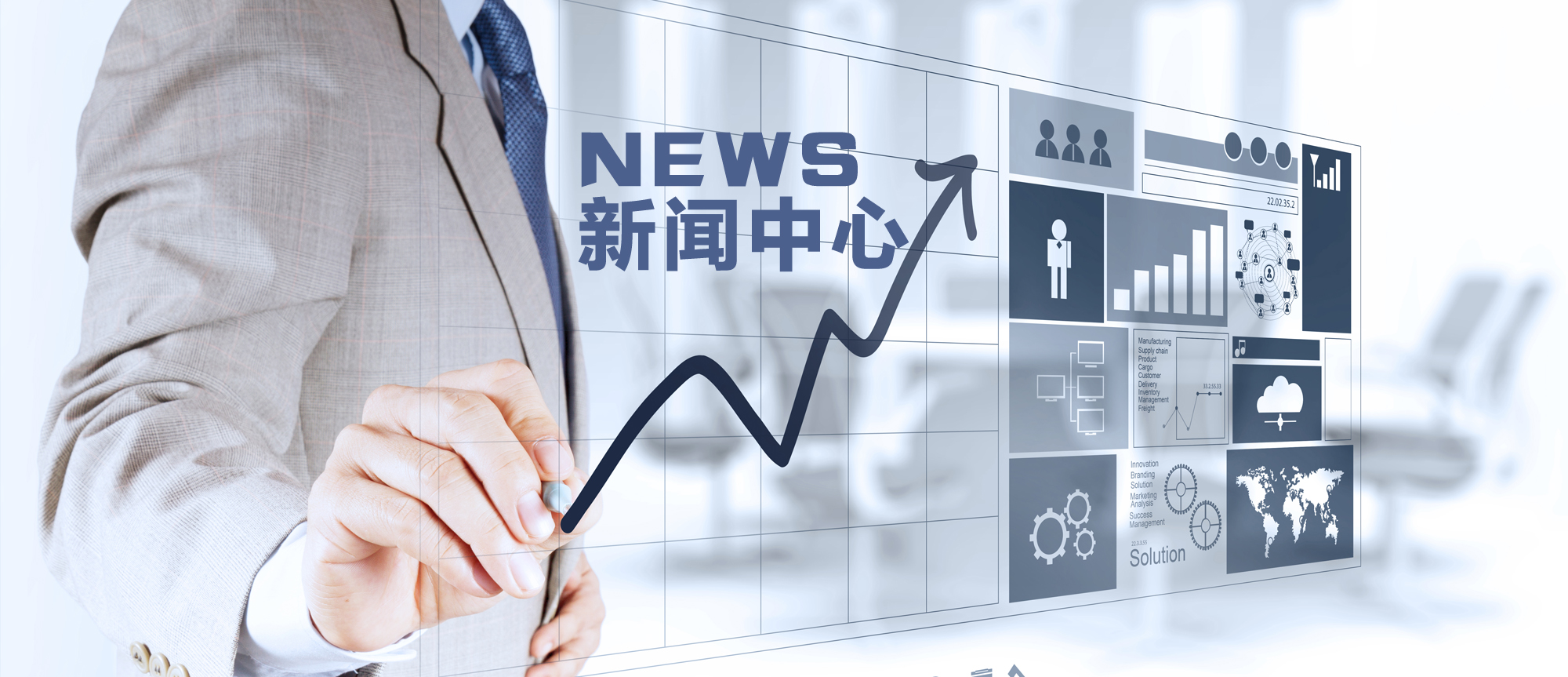
富通新能源 > 动态 > 烘干搅拌输送新闻动态 > > 详细
10000t/d生产线回转窑系统工艺故障及处理
发布时间:2012-11-19 18:12 来源:未知
10000t/d生产线采用DOPOL预热器和MSC在线式分解炉,回转窑规格为Ø6.4m/6.Omx90m,简体斜度为4%,燃烧器为POLYSIUS三风道燃烧器,篦冷机型号为HE101845R/1845R/1845R。现就该线窑系统出现的工艺故障及其处理作一总结。
1、燃烧器的故障及处理
1.1燃烧器外风通道堵塞
1.1.1 出现的问题
2011年4月中回转窑旬窑系统进行了一次大修,下旬开窑前燃烧器的定位为进窑300mm,头部中心在窑口中心位置,光点偏第四象限。系统开启后运行正常,投料量在700t/h,二次风温度在12000C左右,C3出口NO。浓度在600~700ppm,熟料质量较好。但是自4月30日起系统波动较大,窑运行不理想,主要表现在以下几个方面。
1)系统温度低,波动较大。C3出口NOx浓度低时在300~400ppm,高时在700~800ppm,平均在400ppm;二次风温低时在1 050~1100℃,高时在1200~1250℃,平均在1100℃。
2) fCa0多次超标,需大量减产调整工况。5月6日fCa0因调整不及时连续超标6次,造成2次一般工序质量事故,投料量频繁调整,最低时减到550t/h。
3)两列最下级Cl下料管温度相差15~20℃,特别是在窑前温度低时,煤粉燃烧速度慢,部分进入分解炉影响炉内煤粉的燃烧,由于窑带料侧受带起生料阻挡带入炉的煤粉少,所以带料侧的下料管温度相对偏低,导致两列Cl下料管温度出现偏差。
4)仪表显示头、尾煤比例明显倒置,窑头用煤在26~27t/h,窑尾用煤在18~19t/h。
5)窑皮长37m左右,20~30m处窑皮较厚,简体温度在240~300℃。
6)在清燃烧器头部积料时,C3出口NO,浓度会发生突变,出现突然上升或下降且不可控的现象。
1.1.2原因分析
针对上述问题进行了检查,根据煤粉仓仓重标定喂煤秤下料量,标定后发现窑尾喂煤秤的显示数据较实际值低12t/h,因此头煤的实际用煤比例为45%~47%,用量偏多但没有倒置。系统的调整以提高窑前温度和降低fCa0为目标,将燃烧器尾部抬高10mm,也就是头部下压约20mm,同时分3次向窑外抽出230mm,并调节三次风挡板,但是没有效果。由于在清燃烧器头部积料时C3出口NO。浓度会发生突变,怀疑燃烧器头部有问题。
5月13日16:00停窑,冷却1h后把燃烧嚣抽出,检查发现头部外风通道内有部分焊渣,导致外风通道堵塞。在检修时维修人员对燃烧器尾部外风管道进行了补焊,但没有及时处理焊渣,使其在运行中受高速风冲刷后脱落,堵塞在燃烧器头部外风管道内。受重力和一次风的共同影响,焊渣堵塞在了下方位置,使外风下部缺失,导致火焰形状发生变化,且大量煤粉沉积到熟料中,造成窑前温度偏低且熟料质量较差。在清理燃烧器头部时,受外力作用焊渣向下堆积,堵塞的面积就变小,对燃烧器的影响变小,窑,前温度也很快就会提高,但是这种外力的影响是不可控的,也可能会使堵塞面积变大,所以C3出口NOx浓度会在清燃烧器时发生突变。
1.1.3采取的措施及效果
对燃烧器外风道内的焊渣进行清理,清理出的焊渣并排摆放有25cm长。清理后把燃烧器推人窑内300mm,头部位置没有进行调整。21:20开主电动机投料。窑前温度明显提高,C3出口NOx浓度在500~600ppm,在清理燃烧器积料时未再发生突变现象。
为避免再次出现类似事故,公司制定了一套完整的燃烧器维修操作规程,详细规定维修步骤和注意事项。要求燃烧器管道拆除后要对管道密封,防止杂物进入管道,焊接时要从内部到外部进行焊接,完成后要对焊渣进行淆理,避免堵塞管道。
1.2未及时调整燃烧器位置
5月14日开始,篦冷机固定端头部频繁出现大块熟料不易走掉现象,熟料发黏易形成黏散料,二次风温较低,在1120℃左右。15日将燃烧器向窑内推进100mm后效果不明显,将C1下料管温度降至875℃以下,一段篦压降至6.0~6.3kPa,调整后可以勉强维持固定端不结大块。但是由于窑前温度偏低,再加上篦冷机一段料层较薄,二次风温一直偏低,在1100~1150C,C3出口NO,浓度也在500~600ppm。在此期间,投料量可以稳定在680t/h左右,窑皮长33m左右,厚窑皮在20~25m处。
研究后认为原因可能是以下几个:
1)分解炉两个喷煤点喷煤不均衡,造成两列Cl下料管人窑生料的分解率相差较大,低分解率的生料入窑后还要在窑内继续分解,加重了窑内的热负荷,使窑前温度得不到有效提高。
2)三次风挡板损坏脱落,造成三次风风量增大,窑内通风不足,煤粉在窑内不完全燃烧,导致窑前温
度偏低,且有煤粉掺入熟料,造成熟料发黏。
3)燃烧器的位置过于偏料,造成大量煤粉掺入熟料中不完全燃烧,通过熟料带入篦冷机形成二次燃烧,使熟料发黏不易走掉,再加上冷却带变短熟料来不及冷却也会使熟料发黏。
检查后发现三次风挡板全部完好,排除三次风挡板损坏脱落的影响。两列Cl下料管物料的人窑分解率偏差较大,一列在92%~93%,一列在96%~97%,多次调整用煤比例后,两列下料管温度可以基本持平,生料的分解率也基本都在94%~95%。窑前温度得到一定提高,二次风温度在1150℃左右,C3出口NOx浓度在500ppm左右。上次燃烧器外风道堵塞时,曾将燃烧器头部下压20mm,恢复正常生产后,没有将其位置恢复,导致燃烧器头部过于偏料。19日将燃烧器头部上抬20mm后,窑况明显变好,二次风温度稳定在1180—1220C,C3出口NQ浓度在500—700ppm,投料量在700t/h左右,窑皮长度在28—30m,15—20m处窑皮稍微有点发厚但整体较为理想。篦冷机运行状况明显得到改善,基本没有熟料发黏现象,偶尔有大块窑皮脱落在固定端,现场处理即可解决。
燃烧器维修后要按照设计位置恢复,在运行中要根据具体的工况进行调整,以加强熟料煅烧,避免耐火材料烧损和保证系统稳定运行。
2篦冷机漏红料的处理
2.1 出现的问题
2011年7月20日,因为限电进行了为期8天的检修,7月28日开窑时,燃烧器入窑400mm,头部在中心位置,光点偏第四象限,三次风挡板开度在50%。系统运行初期,由于电气原因发生了几次止料,再次开窑后,窑电沆较高,平均在810A左右,正常时在760A左右,C3出口CO含量一直偏高,在0.02%一0.03%,最高时达0.05%,正常应在0.005%—0.01%。虽然窑运行比较稳定,熟料产质量也在正常范围内,但是篦冷机运行不好,灰斗内漏红料现象严重,特别是细料侧,从一段到三段几乎所有灰斗都漏红料。拉链机上的熟料细颗粒量偏多,熟料结粒不均匀。
2.2原因分析
检修中发现,分解炉燃烧器的旋流片磨损严重,怀疑是分解炉内风煤料混合不充分导致煤粉不完全燃烧,产生CO。因此加大系统通风,预热器出口压力由原来的-4.9kPa提高到-5.2kPa,但CO含量还是偏高,且系统温度出现大幅波动,漏红料现象更加严重,据此判断,CO应为窑内煤粉不完全燃烧而产生的。
运行初期的几次止料过程中,操作员没有及时调整好燃烧器的内外风,正常情况下外风压力应在5kPa左右,内风压力在13kPa左右,实际外风压力偏高,在9kPa左右,导致在止料保温期间,煤粉大量沉积在过渡带,使此处窑皮成长过快,形成煤粉圈。煤粉圈的存在,减少了窑内的通风面积,使窑内通风量减少,风煤没有充分混合,煤粉末完全燃烧落人熟料内,使火焰温度降低,熟料结粒小且不均匀。
窑内通风量的减少,增加了三次风风量,使零压面后移,窑头存在逼火现象,篦冷机的冷却用风量减少。由于熟料结粒差,篦冷机通风差,细颗粒熟料在没有冷却的情况下通过篦缝漏入灰斗,导致漏红料。
2.3 采取的措施及效果
8月14日把三次风挡板开度由原来的50%调整为40%,增大窑内通风。调整后窑电流降到770~780A,系统CO含量降到正常值,窑头排风机转速由440~450r/min增大到460~480r/min,窑皮长度由43m减少到35m,后部的厚窑皮也逐渐变薄,煤粉圈逐步脱落。从拉链机上观察,熟料结粒均匀,细颗粒变少,漏红料现象得到明显改善,只有个别灰斗还有少量红料。
3窑系统周期性波动的调整
3.1传统的调整方法
万吨生产线对窑内煅烧的要求较高,多方面因素的影响都会使系统发生波动,如果处理不当或处理不及时,不仅会影响熟料的煅烧质量,还会增加预热器结皮,影响其安全运行,严重时还会损坏窑内耐火材料。传统的调整方法是根据分解炉的温度来调整分解炉用煤量,根据篦下压力来调整篦速。但这些中控参数存在一定的滞后性,所以传统方法不能短时间内消除系统波动,如果调整不当反而会增加系统波动。
因为系统波动时篦冷机篦压波动较大,传统的调整是,篦压高提高篦速,篦压低降低篦速。但是在系统出现大的波动时,该做法只会增加系统的波动。系统波动的原因多数是窑前温度偏低,熟料结粒不好,透气性变差,流动性增强。如果篦速提高过快,很容易使篦冷机料层迅速变薄,篦压下降,这时再迅速降低篦速,料层又会迅速增厚,篦压又快速上升。如此反复会使篦冷机的波动持续增大,二次风和三次风温度会跟随篦压的变化而变化,最低时二次风温度在1050℃左右,三次风在600℃左右,而最高时,二次风温度在1250℃左右,三次风在850℃,且很长时间不能稳定。
通过长时间的观察和分析,本人总结出了一套可以在短时间内消除系统波动的炉、窑、篦冷机综合调整法。
3.2综合调整方法
3.2.1 调整窑内煅烧状况
系统的波动一般是系统温度偏低,熟料在窑内欠烧引起的,但是系统温度过高也会引起系统的波动。系统波动较大时,窑电流、二次风温度和三次风温度都在波动,不适合作为判断调整的依据,而系统的氮氧化物浓度、篦板温度、出篦冷机废气温度及破碎机电流这些参数受到的影响较小,通过综合的分析可以判断出系统温度的高低。如果氮氧化物浓度较高,篦板温度较低,废气温度较低,破碎机电流较高,说明是系统温度偏高引起的波动,要通过减少窑头用煤量,提高窑速来及时降低窑内温度。如果氮氧化合物浓度偏低,篦板温度高,废气温度高,破碎机电流低说明是系统温度低引起的波动,要通过增加窑头用煤量,或者适当减少喂料量,降低窑速来改善窑内煅烧状况。
如果熟料的率值发生了大的变化,特别是LSF或SM偏高,这时熟料煅烧就比较困难,首先要通知化验室进行调整,再结合系统工况适当减产。
煤质发生变化时,特别是煤灰分升高,挥发分降低,发热量降低时一方面要增加窑系统用量煤和系统通风,另一方面要调整煤磨的选粉机转速和系统用风,以提高煤粉细度,促进煤粉燃烧。
3.2.2 稳定分解炉温度
稳定分解炉的温度需要根据篦压的变化提前加减煤。篦压增高,篦速提高时,要提前减少分解炉用煤量;反之篦压降低,篦速降低时,就要提前增加分解炉用煤量。这是因为篦压增高则出窑熟料增加,带出热量也会增加,二次风温度会提高,为了稳定篦冷机料层而提高的篦速会把熟料快速推向三次风取风区,三次风温庋也会提高,导致分解炉温度上升,反之亦然。
调整时要注意以下几点:
1)加减煤的幅度要小,本着少量多次的原则来调整。如果一次加煤过多,会引起不完全燃烧产生CO,温度反而会降低。
2)要密切关注系统CO含量。若发现CO含量较高,就不能继续加煤,而要提高系统用风或者适当减少喂料量。
3)要关注喂煤及喂料的稳定性。如果存在波动要立即通知现场巡检进行处埋。
分解炉的出口温度要控制在8800C左右,Cl下料管温度控制在(872+5)℃,生料分解率控制在94%~95%。
3.2.3 稳定篦冷机操作
篦速调整的幅度要小,且要提前调整,一般情况下分解炉温度出现大幅变化的时候,过5~6min篦冷机就会相应的体现出来,因此在分解炉温度下降后3min提高篦冷机篦速,提前把篦板上的料层降下来,因为再过2min出窑的熟料量会大量增加,反之分解炉温度开始上升时也要提前降低篦速。通过提前调整料层克服出窑熟料量的变化,稳定篦冷机的料层。分解炉温度变化较大的调整过程中,在篦压下降速度减慢的时候就要提高篦速,不要等到上升了再提高;等篦压不上升的时候就要降低篦速。通过小幅度、勤调整,篦压很快可以调整平稳。
3.2.4小结
遇到具体的工况时要具体对待,首先要准确地判断系统温度的高低,找出系统温度变化的原因,作出相应调整。然后再运用上述调整方法操作,在调整的过程中一定要前后兼顾,本着少量多次的原则进行调整,切忌大起大落。通过多次实践检验,这种方法在处理大的系统波动时效果非常明显。用以前的操作方法调整,系统会波动很长时间,一般在5~6h,最长的一次波动了两个班,而用这种方法调整,一般经过1~2h的调整就会恢复正常,大大降低了系统波动引起的危害。
三门峡富通新能源销售回转窑、烘干机、干燥机、滚筒烘干机等。