1、前言
广西康密劳铁合金有限公司烧结厂24 m2烧结机由1979年建成投产,生产过程中烧结机台车落下的烧结矿需运输设备运输至热筛处理,最初的运输设备设计为橡胶皮带运输机,使用不到一年因满足不了输送的高温烧结矿要求,改造成为小格拉链运输机,一直使用至2006年6月。由于最初的设计局限(无铺底料装置),使得烧结机的生产正常化与小格拉链运输机的正常运行有着直接的关系,即小格拉链运输机生产时为不间断运行。在使用小格拉链运输机期间,故障频繁,设备故障停机率极高,影响烧结厂正常的生产,成为了烧结矿产量和技术指标难以提高的主要因素。
2、存在问题
原设备结构如图1所示,为模锻链刮板形式,其链节既传动动力又参加输送物料工作,主要由驱动装置、头轮装置、尾轮装置、链节装置、托辊装置等组成。由于该结构链节既传动动力又参加输送物料.而且拉链机回程(空载)段链条没有导轨,整台小格拉链机顶部无格网,头部下料溜槽坡度偏小,同时生产过程中大量烧结矿落在头轮装置部分,运行时烧结矿不断挤压人链轮和链节接合面,驱动装置设计为渐开线圆柱齿轮减速器、双套筒滚子链条传动、十字滑块联轴器形式,结构笨重能耗高选用功率大。由此生产以来小格拉链运输机,链节易偏移走位,脱出链轮槽,从而受力链节极易蹦断。链节上的销轴开口销十分易磨损而脱出产生事故,工人为维护生产的正常进行,不得不守在小格拉链运输机旁边,处理即将脱出的销轴和反复更换蹦断的链节:无导轨空载段链条呈现弯曲形状,严重时与周边磨擦产生大量的噪声;从烧结机台车落下的粘结在篦条上的大块物料无格网阻拦直砸到链条上,链条砸断现象时有发生;头部下料溜槽坡度的偏小致使头部下料困难.经常发生堵料现象。种种存在问题使得生产过程中小格拉链运输机不但故障频繁、噪音大、反复检修、劳动强度大、运行成本高,而且运行的不稳定使得烧结机的生产受到严重影响,作业率低生产产量难以提高,生产指标无法保证。
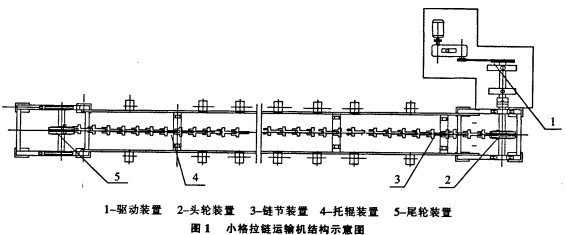
3、方案的选择
通过资料查寻和对其它行业使用厂家实地考察,能取代小格拉链运输机工作的输送设备有:滚轮链式刮板输送机、链斗输送机、鳞板输送机等,经过反复比较和分析,认为采用鳞板输送机取代小格拉链运输机比较适合我公司烧结厂生产实际。其驱动装置简单,能耗低,链节只传动动力而不参加输送物料,无噪声工作平稳,能输送高温物料,输送能力强。能彻底解决断链、脱链、跑偏、堵料等现象,提高设备作业率及烧结机生产稳定性,减轻工人劳动强度,实现不间断运行,确保烧结厂生产正常。
4、方案的可行性分析
由于小格拉链运输机的改造是在原设备的基础上进行的,新的结构与原小格拉链运输机完全不一样,相应安装位置及空间均有较大的变化,尤其机头部位空间,受原设备位置及厂房混凝土框架支柱的影响,同时机头环境温度非常高(有100~120℃)左右,时有烧透熔红状态烧结矿落下(落料温度有300~500℃左右).因此方案的制订相对复杂,既要为保证新设备的合理安装和正常运行,同时充分利用原有基础,又要使机头驱动装置防止高温幅射确保设备安全运行。安装高度受到其它设备相对空间限制不能过高过低,过低不能保证头部下料溜槽坡度下料不畅受堵,过高则需改变上部钢结构的位置结构安全受影响并且工程巨大,鳞板输送机设备总高只能与小格拉链运输机链轮中心高一致为900mm.安装总长不存在问题。通过方案的可行性分析和实际尺寸测量,对实施过程中存在的主要问题一一采取以下方法进行解决。改造后的设备结构如图2所示。

4.1 鳞板输送机驱动装置位置安装问题
鳞板输送机驱动装置安装位置设计与原设备安装一样为左装式,但实际安装时一厂房500 mmx500mm混凝土柱子正好落在驱动装置电机位置,由此往另一端加大驱动装置钢支架底座,保持电机上主动皮带轮与减速器上从动皮带轮中心距不变将电机移至另一端,加大后的支架底座偏离原设备基础过多一半悬空,现场利用160 mm槽钢与上部钢结构焊接吊装。
4.2 保证头部下料溜槽坡度下料顺畅不受堵问题
原下料点在链轮下部,下料漏斗物流溜槽倾角为400.采用鳞板输送机下料点在链轮上部,但鳞板输送机设备总高与小格拉链运输机链轮中心高一致为900 mm,相对T料点只比原提高了250 mm,下料漏斗物流溜槽倾角增大为470,不能满足实际下料角度需要(因烧结粉矿有一定粘性,经验要求物流溜槽倾角按煤粉及粘土设计,需大于600)。将鳞板输送机整体向热筛方向(即下料口方向)移动450 mm,给料漏斗角度增大为620,头部下料溜槽坡度小下、料不顺畅、受堵问题得以解决。
43鳞板输送机驱动装置防高温问题
机头部位高温的环境温度使得原小格拉链运输机机头轴承极易损坏,鳞板输送机安装后距离热源更加靠近,同时传动装置为皮带轮传动,皮带更不耐高温,反复对比了几种方案,最终采用将烧结机下料口正对鳞板输送机机头部位进行岩棉玻璃纤维板加镀锌铁皮隔热措施,岩棉板厚度为100 mm,解决了鳞板输送机驱动装置温度高问题。
4.4防止大块物料砸坏鳞板问题
直接采用18#钢轨在整台鳞板输送机接料流槽全长上焊接格网,防止大块物料砸坏鳞板机,使落下大块物料先砸到钢轨击碎后再落人鳞板输送机鳞板上。在头部落料处加强格网密度,更有效地防护好鳞板输送机机头部分。
4.5鳞板输送机工作过程机头下部积料问题
由于鳞板输送机的结构特点,在输送粉状物料过程中当鳞板运行至下段时不可避免的出现将少量粉料带下设备底部,运行时间一长在机头将积累较多粉料,对现场卫生及设备维护十分不利,同时加大了工人劳动强度。通过现场分析直接在机头下方底处凿开水泥混凝土地板一个1400 mmx1200 mm落料口,再增设一人接料钢斗用Dg300钢管引入水封拉链机中,由引入水封拉链机将粉料运送到工艺系统中,此问题即可迎刃而解。
5、改造后的设备特点
改造后的鳞板输送机选用广西百色矿山机械厂生产的BLT650x28.85型鳞板输送机,该设备由头轮装置、鳞板装置、尾轮张紧装置、机架、轨道和驱动装置组成,具有运行阻力小、鳞板装置刚性好、承受冲击能力强、结构简单紧凑等特点。鳞板输送机是板式输送机的一种,在矿山、冶金、化工行业中广泛应用,非常适合我公司烧结机生产时台车落下的烧结矿(粉料+大块粘结烧结矿)的输送工作,在设备订购前期不断与生产厂家进行技术交流,扬长避短,取精去粕,充分保留鳞板输送机的输送特点,相应作些整改以完全满足生产实际需要。譬如原标准机型只适宜输送$400℃的高温物料,而实际烧结矿有近500℃,因此将鳞板厚度由6 mm加至8 mm.以满足实际输送的物料温度和设备强度。轨道方面将标准机型的8槽钢改为18+钢轨,满足实际设备长期运行的需要。
鳞板装置每组鳞板两端有滚轮各一个,为滚动轴承型式,使磨擦力大为减少并使噪声减弱,相应所需动力小。为使结构简单,驱动装置部分减速器为行星摆线针轮减速器,电机采用电磁调速电机,可实现无级调速,结构简单,起动性能好,功率仅为2.2kW,而原小格拉链运输机功率为7.5 kW,能耗大为降低。采用皮带轮传动能在设备运行受异物卡死时自动打滑防止电机烧坏,尾轮张紧装置采用简单通用的螺旋调整装置,方便实用。
输送机改造前参数对比见表1:
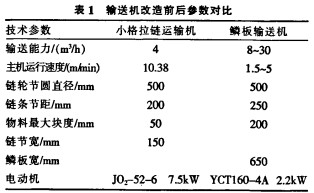
6、改造效果
2006年6月将小格拉链运输机改造为鳞板输送机,6月25日投入使用。经过两个多月的生产实践证明,改造取得了圆满成功,鳞板输送机完全能取代小格拉链运输机工作,并达到了良好的效果。
工作平稳,输送能力强,能彻底解决断链、脱链、跑偏,堵料等现象,原小格拉链运输机运行一天至少停机维修4~5次,甚至一天有10次以上之多,由于小格拉链运输机的设备故障停机率每月均达l0%o以上,现改造后提高了设备作业率,由此烧结机运行不再因其不稳定而受影响,烧结厂设备故障停机率大为减少,无因鳞板输送机故障产生的设备故障停机率,实现了不间断运行,确保烧结厂生产正常。
无噪声,工作环境改善,无故障检修次数基本无,无堵料,工人劳动强度大大减轻。
成本降低,电机能耗低,鳞板运行无故障,检修次数少,运行费用低,维修及维护简单。
7、结语
将小格拉链运输机改造成为鳞板输送机是十分成功的。通过此次改造,消除了设备故障点,采用新的输送设备彻底解决了存在的问题,提高了设备作业率,减少了设备故障停机率,改善了工作环境,减轻了劳动强度,确保了烧结厂的生产正常稳定,从而保证了高炉生产所需烧结矿用量,小格拉链运输机的改造达到了我们的预期目的。
三门峡富通新能源销售输送机、皮带输送机、刮板式输送机、斗式提升机等输送设备。