1、前言
炭素原料的煅烧是炭素制品生产工艺中第一次将原料进行高温热处理的工序,而原料煅烧质量的好坏直接影响到最终产品的质量。因此在炭素工艺设计中,正确地选择煅烧设备是十分重要。
在煅烧设备的应用方面,虽然已有比较先进的回转床煅烧设备,但是,由于投资较大,在国内炭素厂还没有得到普遍的应用,只有石油六厂利用其煅烧针状焦。目前国内的煅烧设备主要有回转窑和罐式炉,罐式炉虽然煅烧质量好,但是占地大,一次性投资大,劳动条件差,不易实现自动化,耗费较多的人力资源。国外石油焦煅烧普遍使用大型回转窑作为煅烧石油焦的设备。国内自1958年开始使用中1.4×24m回转窑做煅烧设备以来,至今已经发展到全国有数十台大、中、小型的炭素煅烧回转窑。
根据国内外的生产实践,回转窑和罐式炉相比,虽然具有对原料的适应性强,设计制造简单,投资省,建设周期短,自动化程度高,产量大,劳动条件好、节省人员等优点,但还存在着碳质烧损大、能耗高、煅烧质量稍差、设备运转率低等缺点。目前国内的延迟石油焦,含有较高的水分(一般在8%~10%)和挥发分(通常在12%~14%),同时焦粉含量也较大。
针对国内石油焦的特点,为了在回转窑煅烧石油焦过程中减少碳质烧损,降低能耗,提高煅烧质量,对回转窑进行如下改进。
(1)扩大窑尾预热段的直径,降低烟气的流速,减少烟气带走的粉尘量,减少碳质烧损,加强预热段的预热效果,提高煅烧质量。
(2)合理确定三次风的位置、风量,即能使挥发分充分燃烧,增加预热效果,又不使烟气温度降低,提高煅烧质量。
(3)采用U型燃烧室,增加燃烧室的长度,使粉尘在燃烧室内充分燃烧。
2、以中2.2×45m回转窑为例进行讨论
2.1设计改进型的回转窑
回转窑进料端直径扩大,Ø2.2×45m回转窑(Ø内1. 74×25m/Ø内1.80×20m)(见图1)改为Ø2.2×25m/中2. 42×20m(Ø内1.74×25m/Ø内1. 94 x20m)(见图2)回转窑。将窑尾梢形改为直筒型;窑尾法兰直径由<Ø1000mm改为Ø1200mm。
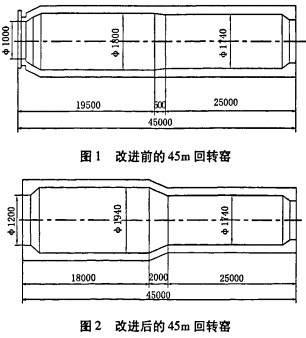
改进前后的两台45m回转窑的主要参数及有关的数据见表1。
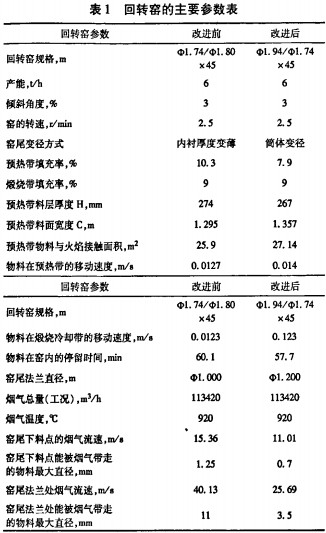
从表1看出窑尾变径后产生如下变化:
(1)窑的预热带、加热带(变径部分)的物料填充率由10. 3%降至7.9%。
(2)料层厚度减薄。
(3)物料在预热带的移动速度略有增加。
(4)物料在窑内的停留时间减少2分钟多。
(5)预热带物料与烟气的直接接触的表面积稍有增加。
(6)窑尾加料点的气流速度降低,能被烟气带走的物料的颗粒直径减小。
(7)窑尾法兰处的烟气流速降低。
这些变化,对提高煅烧焦的实收率,起到了积极的作用。具体论述如下:
①改进前的回转窑预热带的填充率为10. 3%,适用于含水率<3%,挥发分<8%的石油焦,能够煅烧出质量合格的石油焦,作为阳极生产的原料。
目前国内石油焦含水、挥发分较高,用改进前的窑煅烧,煅烧质量略有下降(真比重较低),改进后,填充率降到7.9%,同时料层厚度略有减薄,改善了物料间的传热条件,物料与烟气的接触面积亦有增加,这些都改善了物料在变径段的烘干、预热、加热条件,提高了窑尾的预热能力。物料进窑后温度上升有所加快,挥发分的逸出速度加快,同时在恰当的位置增加三次风,将有利于挥发分的燃烧,注意加入的三次风的量,已不使窑内烟气温度降低为宜。这将有利于石油焦的烘干、预热效果,提高煅烧质量。
②由于预热带的扩大,使物料在该段的移动速度加快1.3 mm/s,从而使物料在整个窑内的停留时间缩短2分钟之多,可以说对煅烧质量影响微不足道,反而由于提高了物料在预热带移动速度,加快了在窑内的相对位移,为煅烧高挥发分延迟石油焦时防止窑尾结圈创造了条件。关于这类问题早已被国内36m回转窑的生产实践证明。贵铝一期、青铜峡铝厂一期分别采用了Ø内1.6×36m及Ø内1.6/Ø内1.9×36回转窑,当这两台窑都煅烧100%延迟石油焦时,青铜峡铝厂的变径回转窑从未发生过窑尾结圈的现象,而不变径的窑却需要经常进行烧结圈操作,45m不变径的窑也常出现窑尾结圈的现象。这些都说明回转窑变径是非常必要的。
③进料端扩大、窑尾法兰直径加大,能提高煅烧的实收率。
由于进料端的直径加大,使窑尾加料管处的烟气流速15. 36m/s降低到11. 01m/s,使下料管处在下料时能被烟气带走的粉料粒度由1. 25 mm降到0. 7mm。而我们目前加料管的安装方式又为带走这些小粒焦粉提供了条件。
目前加料管的习惯安装位置是根据窑尾料层厚度H.在适当抬高A,便是加料管底面实际安装高度,而且是加料管装在窑断面纵向中心位置上(即图3中I的位置),而窑内的物料断面却是在沿窑的转动方向与水平成一个该物料静安息角的位置,所以加料管内的物料流出料管落入窑内时,要下落一个(H+A)的高度,在此下落过程中不同直径的焦块、粒、粉都要经过一段悬空的过程,这时,如果烟气的流速达到某种粒度料的1. 38倍,能被烟气的气流带走,当烟气行至窑尾法兰收口处时,由于断面面积减小而烟气的流速增大,就能很快将夹带的物料,(包括滚到法兰口上较大块的料)带进燃烧室,由于窑尾及沉降室密封不严漏风(内部呈负压),一些细焦粉连同在窑内没有完全燃烧的挥发分在沉降室(或燃烧室)内继续燃烧,这样固然可以提高烟气的温度,增加余热锅炉的产气量,但必须要多烧掉一部分石油焦,即增加了碳质烧损,又降低了实收率,所以,窑尾直径扩大,降低了烟气流速,合理地安装下料管(如图3中Ⅱ的位置)对降低碳质烧损,提高煅烧实收率是有益的。
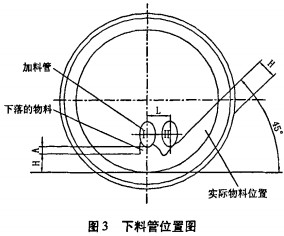
将窑尾的梢形改为直筒型,即可增大窑尾法兰的直径,降低烟气流速,又能加大下料点的料面与窑尾法兰口的高度差,防止物料直接反入沉降室(或燃烧室)。
从图3的安装尺寸便可以看出在改进前窑尾处的结构及安装尺寸的不合理。因而造成一些物料从窑尾法兰滚入燃烧室(实测发现燃烧室内有较多20—30mm,甚至40一50mm的焦块),根据国内长期使用的经验,改进后会收到很好的效果。
2.2合理确定三次风的位置
三次风的位置应设在不加三次风时,回转窑内烟尘最浓密处,此处挥发分挥发的最剧烈,三次风应采用变频控制,根据投料量的多少,确定风量的多少,引入的三次风风量过大,反而造成引入处的温度下降的很多,对煅烧起了反作用,如果不加三次风在排出挥发分温度范围内,窑内焦炭床的升温速度明显降低,影响焦炭的煅烧质量。因此适量地加入三次风,可以使挥发分燃烧,提高焦炭的加热速度,改善煅烧焦炭的质量。
2.3燃烧室的改进
改进前的燃烧室为平底落地式的燃烧室,设计的意图是将烟气带入燃烧室的细焦粒、粉在补充一定的空气条件下完全烧掉,实际设计的燃烧条件不够,只补充了空气,而燃烧时间不够,较粗的焦粒、粉在短暂的悬浮过程中被完全烧掉,这些没有烧掉的焦炭在燃烧室内沉积,形成表面一层能接触空气,中间和底部料无空气助燃,无法继续燃烧,原设计并不成功。
改进后的燃烧室,采用U型,长度比改进前增加4倍以上,保证含粉尘的烟气在燃烧室内处于不稳定的状态,充分与空气混合,提供足够的氧气,同时加长燃烧室,保证了燃烧时间,使炭粉在燃烧室内充分燃烧,窑尾直径扩大,降低了烟气带走的焦粒的直径,还起到了降低燃烧室长度的作用。
3、结论
将Ø2.2 x 45m回转窑改为Ø1.74/Ø内1. 94×45m回转窑的结构形式,调整三次风,将筒形燃烧室改为U型燃烧室,能够改善回转窑的煅烧石油焦的质量,还能够在降低碳质烧损、提高实收率等方面有所提高。对以后的回转窑的设计提供借鉴。
三门峡富通新新能源销售回转窑、烘干机、干燥机、气流式烘干机、滚筒烘干机等烘干干燥机械设备。