某院在某铜矿山选矿厂的工程设计中选用了两台西门子公司的MSI单托辊秤,配用了BW100积算仪,在现场调试合格并投入运行,在调试和多年的实际运行中遇到了许多具体问题,回顾一下这些问题的发生和解决过程,总觉得对皮带秤的应用来说挺有代表性的,也许很多用户会碰到类似的问题,所以将这些问题一一列出与大家共同讨论。
1、MSI单托辊秤
西门子妙声力公司的MSI单托辊秤架采用直接承重式结构,不带杠杆,没有支点,秤架比较轻巧.称量托辊组通过两个托辊架卡与动态梁连成一体,然后通过两个平行四边形称重传感器固定在静态梁上。
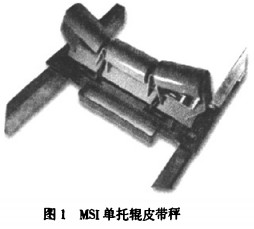
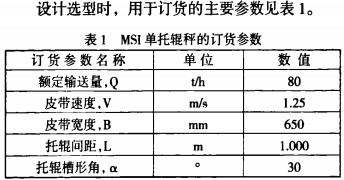
2、安装位置选择
工艺专业要求在球磨机给料皮带上安装皮带秤,给料皮带机前后滚筒的中心距为21.35m,断面为变倾角的凸弧形,先13。倾斜向上后水平,水平段仅4~5m,倾斜段离开裙板后直线段长度约为9m。最初是在图2所示位置3安装皮带秤,因这里是给料皮带机的水平段,但安装以后皮带秤的性能不稳定,零点及满值调试始终不能满足要求。查找原因后,确认是皮带秤安装位置选择不当,因为位置3虽然是水平段,但距弧线段太近(仅1~2m),距头部滚筒也很近(只有3m),而且与纠偏托辊4仅相隔l组托辊,因而造成性能不稳定。查阅随产品说明书所附西门子公司皮带秤应用规程,发现有以下四点未满足要求:
1)规程要求秤架安装在靠近尾部滚筒1的区域,这里是整条皮带输送机皮带张力最小且皮带张力变化最小的地方,而实际秤架安装在靠近头部滚筒区域,这里是整条皮带输送机皮带张力最大且皮带张力变化最大的地方;
21这条皮带输送机有曲线段,如果秤架安装在凸形弧线段之后,规程要求距弧线段终点至少12m,而实际秤架安装在距弧线段终点只有Im的地方;
3)当秤架迫不得已安装在靠近头部滚筒区域时,对300托辊槽形角的称量托辊要求在秤架之后先安装2组30°托辊槽形角的托辊组,再安装l组200托辊槽形角的托辊组,同时尾部滚筒应抬高13mm,从而使秤架处皮带的形状更能适合300托辊槽形角,而实际未安装20。托辊槽形角的托辊组,也未抬高尾部滚筒;
4)规程要求纠偏托辊与秤架的距离至少9m,实际仅相距Im。
经反复考虑,将皮带安装位置改在皮带输送机的倾斜段(见图2位置2及图3).但从离开裙板到弧线段起点的直线段长度仅9m,而规程要求如果秤架安装在凸形弧线段之前,秤架至少离开弧线段起点6m,所以直线段非常紧张,但也基本达到要求。这里离尾部滚筒较近,是整条皮带输送机皮带张力最小且皮带张力变化最小的地方;秤架附近的纠偏托辊搬到离称量托辊尽量远的地方,虽然现在的秤架安装位置处于有13。倾角的倾斜段,但全面比较下来,安装位置2远远优于位置3。
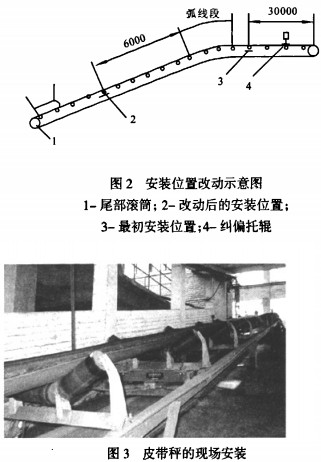
3、准直性校准
由于重新安装秤架,我们严格按西门子公司的使用说明书进行准直性校准(见图4),说明书要求对称重托辊及其前后各2组托辊(前后托辊分别称为进入托辊和退出托辊)进行校准。通过在3节槽形托辊上张紧3根高质量的弦线进行校准(见图中3节托辊上方的直线),校准误差应小于±0.8 mm,但它同时又强调称重托辊处不应出现负校准误差,即不能比相邻托辊低。准直性校准非常重要,在现场安装的条件下,想达到非常高的校准精确度的确很困难,但也应该尽可能多花点时间和精力做得更好。
4、托辊间距校准
在秤架准直性校准的同时,要完成托辊间距校准,即如图4所示的A1、A2、SI、R1、R2这5组托辊之间的4个托辊间距要按皮带输送机现有的1m托辊间距重新进行精确的调整,校准误差应小于1mm。
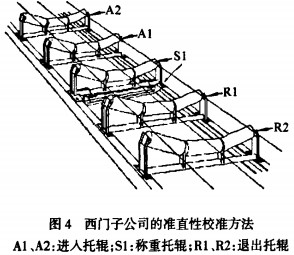
经过安装位置改动后的秤架,在完成准直性校准、托辊间距校准后进行了调零,从调零的效果来看,安装位置改动后的秤架的零点稳定性与以往相比大大改善,说明我们所作的上述工作是有成效的。
5、校验
第一步校验是采用随设备带来的砝码,砝码共两个,每个重8kg。根据实测的皮带输送机实际皮带速度为1.27m/s,则根据公式可计算出在满量程时由于输送物料重量加在称重传感器上的力P:
P =QL/3.6V =80×1/3.6×1.27=17,50kg
式中,O、L、V,的含义和数值见表l,但皮带速度y为实测值。
由此可知,随设备带来的砝码重量是较为接近P值的。
但仅仅只用砝码校验还不能令人信服,所以我们又设法进行物料试验。但是在皮带输送机的前后都没有找到合适的加载点或卸载点,所以想进行真正的物料试验还有相当的难度。最后采用了两种替代方法进行物料试验:砂袋试验和刮皮带试验。
砂袋试验方法是将实际输送的铜矿石(中碎后的小块度矿石)装入编织袋里,预先精确称重。每袋按10kg重量装入矿石.由于皮带速度不算太快,可以采用不停皮带输送机的方式进行试验。用人工从皮带秤前方把砂袋依次放在皮带上(注意不应使皮带秤超量程),通过皮带秤后用人工取下砂袋,以所加砂袋的总数×lOkg作为标准重量值进行计算。最初的几次使用的砂袋数较少,例如10袋(总重100kg),试验几次后,通过满值系数调整,可使每次校验误差大体在1~2kg时,再将每次使用的砂袋数增加到20袋或30袋,当连续几次砂袋试验的误差均在1%范围内时,应该说基本达到使用要求了。这种校验方法较为简单,在皮带秤瞬时输送量不大时可以使用。
由于我们的物料量检测对象是选矿球磨机的给矿量,该参数用于给矿量的定量调节回路,所以皮带秤的瞬时输送量是比较稳定的,通常波动量不超过1%~2%,因此比较适合采用刮皮带试验方法。这种方法在皮带秤的瞬时输送量比较稳定时,大致按每2s左右读一次瞬时流量值的方法读取IO组数据(1人读数据,1人记录).然后通知停皮带输送机,在皮带输送机上量取Im长度,并将这个长度上的物料取到容器内进行称重。如果条件允许,可同时取多段(例如2—3段)Im长度上的物料进行称重。然后根据10组瞬时流量值数据的平均值与多段Im长度上的物料的实际称重数据的平均值进行误差计算。这种试验方法简单,工作量小,试验结果基本可靠。但他需要短时间停皮带输送机,中断物料输送过程,可能对生产有影响。
我们通常在允许较长时间停止向球磨机给料时进行砂袋试验,在只允许非常短暂时间停止向球磨机给料时(例如2_4分钟)进行刮皮带试验。
6、皮带秤量程修改
随着工艺操作过程的改进,球磨机的处理能力不断提高,因此要求对皮带秤的量程进行修改,为此我们首先进行了称重传感器量程的计算和测试。由于MSI单托辊秤架采用直接承重式结构,称重传感器不仅要承受输送物料的重量,还要承受秤架的皮重。
而秤架的皮重可以通过托辊组重量、称量段(相当于托辊间距Im)长度上的皮带重量及参与称重的托辊架卡、动态梁等部分的重量相加后得到。但这些数据查找及实际测量较麻烦,我们采用的办法是测量皮带输送机空载时称重传感器的输出mV值,然后反推出秤架的皮重。
这台秤所配称重传感器为2个C4-TBSP-100型,额定量程100磅,约等于45kg,总容量为90kg,在该秤二次仪表(BWIOO)参数表中的P940、P941可以直接查到左、右两个称重传感器的输出mV值。该值约为8~9mV,根据供桥电压为10VDC,称重传感器的灵敏度为2mV/V,可以计算出皮带秤因称量托辊组、皮带、动态梁、托辊架卡等加在称重传感器上的皮重值大致在称重传感器量程的40~45%之间。
前面已经计算出在满量程80t/h时,由于输送物料重量加在称重传感器上的力P为17.50kg.这大体相当于称重传感器量程的20%。
按100%称重传感器量程考虑,减去称重传感器上承受的输送物料的重量和秤架的皮重,还有35%以上的余量,对于输送物料重量加在称重传感器上的力来说的相对余量达到200%,即皮带输送机的输送量再增大一倍至两倍(即160—240t/h量程)也不会使称重传感器过载。
实际生产过程中,量程已经分几次从80t/h加大到10t/h、120t/h、150t/h,而称重传感器一直没有更换。
量程改动非常简单,仅仅需要在该秤二次仪表的参数表中调出POIl(设计流量)并按要求输入新的量程值即可。
由以上计算过程可以了解到,直接承重式结构秤架使用称重传感器的余量(如本例的35%)比较大,而且相对于输送物料重量加在称重传感器上的力来说的相对余量更大(如本例的200%),所以在大多数情况下,当皮带秤的输送量需要增大时,直接承重式结构秤架使用的称重传感器通常不必更换,这也应该是他的一个优点吧。
7、测速传感器更换
原设计选用MD-256测速传感器,他是转动轴直连式,每转动一周发出256个脉冲,当皮带电动机或皮带滚筒的转动轴轴端预留有延伸轴时,能方便地与测速传感器的轴连接。但实际生产现场皮带滚筒的转动轴轴端壳体上没有预留安装孔,也没有延伸轴,需要在皮带滚筒的轴端壳体上开孔并连接一段延伸轴才能安装测速传感器,非常麻烦且安装不牢固,安好之后测速传感器晃动大,所测皮带速度值波动较大(约±0.05m/s)。使用一段时间后,因为安装处正好位于上层楼板开孔的下方,清洗水滴到测速传感器上致使其损坏。因返回检修时间长达三个月以上,就在现场用国产测速传感器替代,安装形式也改为在下皮带上方安装的滚轮式。因为都是三线制连接,工作电源都是10~12VDC,所以替代过程很简单,只是显示的速度值不符。我们只要在该秤二次仪表的参数表中调出P018(速度常数调整),输入原有速度显示值即可。这项修正工作也可以在参数表中调出P015(速度常数),输入新旧速度显示值的相关修正系数即可。在下皮带上方安装的滚轮式测速传感器稳定性较好,所测皮带速度值波动小(约±0.02m/s),使用效果还优于原设计的MD-256测速传感器。
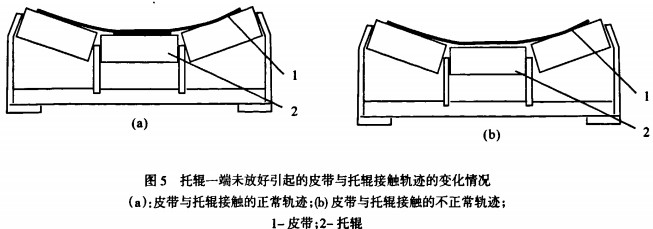
8、次故障的查找
皮带秤投入运行后,秤的使用基本正常,但有一次工艺专业更换皮带,现场技术人员重新进行了一次调校。但再次投入运行后,零点、满值一直不稳定,而原因一直找不到。当我们来到现场时,怀疑是准直性没有调好,而现场人员讲他们也是按以前进行准直性校准方法作的,应该没有问题。当我们在现场仔细观察后,发现如图5 (a)所示的称量托辊组前后的托辊组与皮带接触的轨迹和如图5(b)所示的称量托辊组与皮带接触的轨迹不一致。前者的轨迹是正常的,皮带与托辊组的中间托辊有一半以上的宽度接触了,与左右两个托辊也在托辊中部开始均匀接触;但后者托辊组的中间托辊几乎不和皮带接触,左边托辊与皮带接触还可以,但右边托辊与皮带几乎是全接触,而且从三节槽形托辊的断面形状来看,右边托辊的左端明显高出来约20mm,用手摸一下就找到了问题产生的原因,原来是这个托辊左端的中心轴未能放入托辊支腿的凹槽内。停一下皮带输送机,用力将这个托辊的左端按到托辊支腿的凹槽内,使托辊组整个断面的形状从图5 (b)改变成图5(a)。在随后再次进行的皮带秤零点、满值的测试中,秤的性能又恢复到原来的稳定状态,这次故障处理过程也从反面证实了准直性校准的必要性和重要性。
9、累计脉冲信号远传
由于该铜矿山选矿厂工程的控制系统选用了西门子公司SIMATIC S7-400 PLC.皮带秤二次仪表除了将物料瞬时流量信号送到PIJC进行球磨机定量给料调节外,还将物料累计脉冲信号送到PLC进行累积显示和报表打印。开始的时候我们在二次仪表选择lOkgt脉冲送PLC的开关量输入模块进行脉冲累加,但很快发现在PLC上显示的累积值少于皮带秤二次仪表的累积显示值,显然是因为累计脉冲信号频率过快,PLC接收信号时出现了丢脉冲的现象,将10kg,脉冲改为1000kg/脉冲后,因累计脉冲的间隔时间大大延长,就再也没有出现丢脉冲的问题。
三门峡富通新能源销售皮带输送机、斗式提升机、刮板式输送机、颗粒机等机械设备。