目前,我国水泥产量位居世界第一,水泥设备制造业也得到飞速发展,其中回转窑是水泥厂的心脏,是最重要的关键设备。解放前我国只能向国外购买,解放后-我国开始自行设计制造,在20世纪50年代末,我国设计了Ø2.5mx78m回转窑,满足了180t/d湿法水泥熟料生产线要求:20世纪60年代,我国设计了Ø3.5mx145m湿法长窑和Ø4mx54m、Ø4mx60m半干法窑;20世纪70年代,我国开发了1650t/d的咖5/5.5mx185m湿法长窑;20世纪80年代,我国开发了2 000t/d的44mx60m带分解炉的旋风预热器窑;20世纪90年代,水泥生产技术快速发展,特别是大型新型干法烧成系统,6 000t/d以下规模水泥熟料生产的关键设备都已经完成国产化。21世纪初,由于中国设备价格较低且供货周期较短,在国际工程市场上受到越来越多的业主的认可,国内工程及装备企业进入国际市场已经越来越成为一种必然。2004年成都院启动10 000t/d水泥熟料煅烧回转窑的开发,以求尽快提高国内万吨级水泥装备水平。
在开发该设备之前,成都院已经成功的开发了1000~5 000t/d水泥熟料煅烧回转窑,得到了业主的一致认可。本项目以成都院开发的100t/d~5000t/d规模回转窑为基础,在规格上适当加大,并对局部结构进行优化,从而开发出具有自主知识产权的高可靠性和经济性的水泥煅烧回转窑。
1、技术开发要点
1.1设计回转窑的原始数据
根据项目的额定产量及工艺技术性能要求,确定回转窑的规格Ø6.2mx98m,接着确定计算窑的所有部件的耐火转、窑皮和物料负荷重量。
1.2筒体排版及轮带的定位结构形式
筒体部分在设计计算基础上综合考虑各档跨距,通过分析和计算简体的载荷及其分布、筒体弯距和应
力、简体变形,合理地对简体选材、壁厚、排版等进行优化见图1。

简体轮带活套在垫板上.垫板浮放在简体上,由大、小挡块对垫板进行周向及轴向定位,同时对轮带进行轴向定位,轮带垫板可方便的更换见图2。
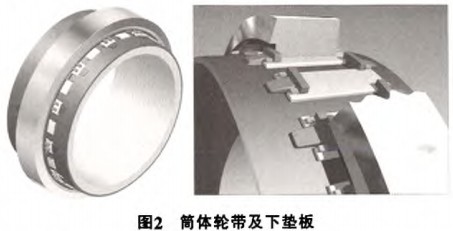
1.3支承装置的结构及冷却方式
回转窑窑体是以3%~4.5%的斜度支承在托轮支承装置上,支承装置有滑动轴承和滚动轴承两种。该设备支承装置采用自调心滑动轴承,并采用油勺提油润滑,轴承内设有冷却水通道。为适应高温环境,同时采用强制油玲却循环系统见图3。
1.4挡轮装置
当窑回转时,窑筒体在自重作用下向低端下滑,因此必须设置挡轮装置来限制窑筒体轴向位移。挡轮装置按其工作原理分信号、吃力和液压挡轮。该设备的下滑力是利用第1、2档的挡轮装置解决见图4。
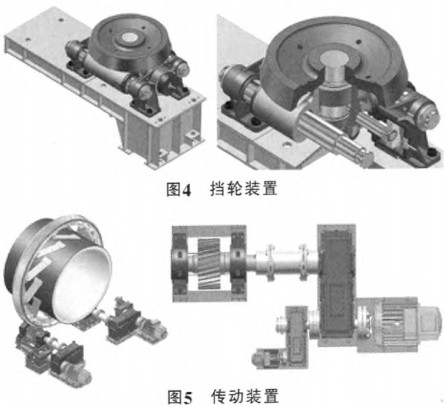
1.5传动装置
随着窑体的加大,传动功率亦越来越大。由于大功率、大减速比的设计制造困难多,因此采用双传动型式,主电机采用变频电机,主减速机配套强制润滑的稀油站,大小齿轮的润滑采用油脂喷射系统自动控制和调节见图5。
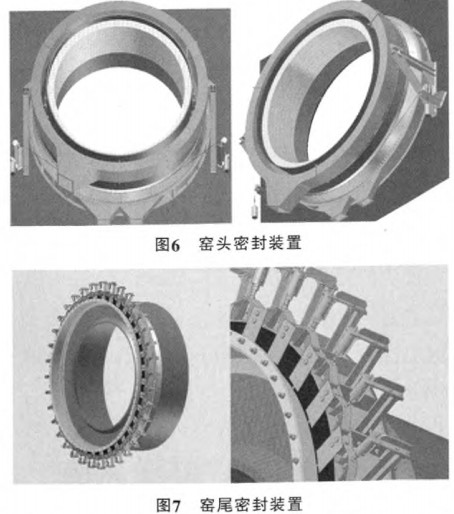
1.6窑头窑尾密封结构
窑头密封装置采用弹簧片和迷宫组合式密封结构。风机通过喇叭口吹人适量的冷空气冷却窑头护板。相互搭接的耐热弹簧钢片适度压紧于风冷套的筒体上见图6。
窑尾密封采用径向弹簧压紧式石墨块密封装置。安装在预热器上的固定套筒的外圆面作为与石墨块的接触密封面。石墨块在轴向和周向上受到限制,在径向上通过弹簧力始终与套筒外圆面紧密接触,并自动径向补偿运行中的损耗见图7。
1.7窑头罩
采用小窑头罩结构,三次风不从窑头罩抽风,弧形壳体的刚性强,罩壳侧设有点火孔,对拉移动式窑门,窑门上设有摄像孔、观察孔、清灰门见图8。
1.8重要铸件的材料、热处理
重要铸件结构设计、材料选择、制造工艺和热处理等合理、经济,从国产化方面考虑国内现有的加工能力。
2、技术开发成果及应用
经过近半年时间的开发、设计、优化,2005年成都院的设计成果开始在中国的制造厂生产。2006年初,中国第一台10 000t/d水泥熟料煅烧回转窑从上海港出发运往阿联酋ucc项目。经过安装、调试、考核、使用等实践证明成都院开发10 000t/d水泥熟料煅烧回转窑是成功的,助推了我国水泥业的发展。
从已建阿联酋ucc项目10 000t/d工程的使用效果来看,该项目2006年12月28日点火,并于2007年4月23日至4月26日顺利完成72小时考核,均日产量10 277t。从考核期间中央控制室的DCS运行参数显示,额定产量下,窑主传动转速约3.1r/min,电机电流约870A,为额定电流的60%;窑支承轴承的温度最高为54℃,低于报警温度16℃。从调试至今,经过了长时间的考验,回转窑运行良好,得到业主及咨询公司的一致认可和肯定。
10000t/d水泥熟料煅烧回转窑的开发是成都院应对国外技术封锁而设计的开发项目,也是成都院自身技术发展的必然,依托ucc项目,成都院不但成功的完成了最大规模的回转窑项目的开发,也为成都院的海外市场的开拓打开了新局面,并奠定了坚实的基础。
三门峡富通新能源销售回转窑、颗粒机、烘干机、滚筒烘干机等机械设备。