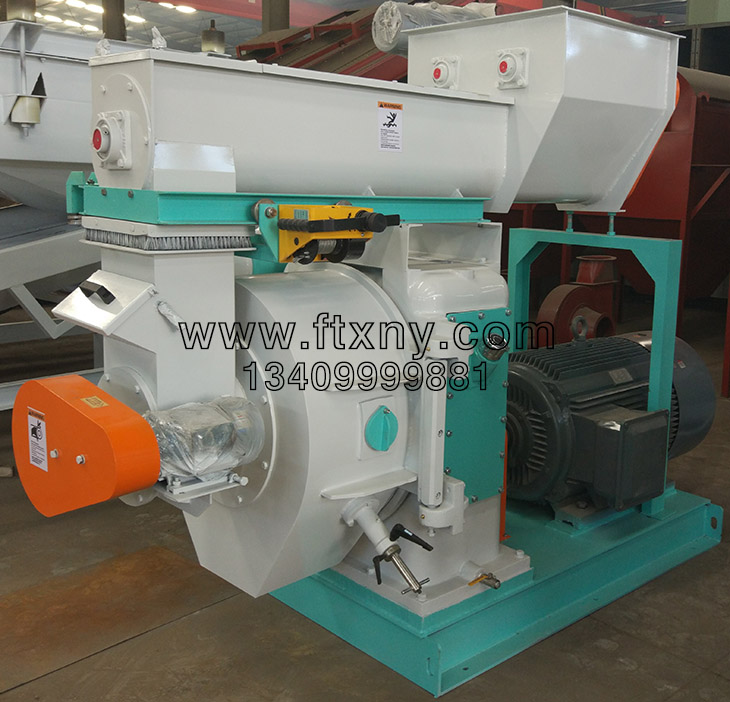
秸秆是我国主要的农作物,每年的产量在6亿吨以上,其中有超过12.7%的剩余秸秆就地焚烧或闲置,造成了环境污染和能源的浪费。如果把这些秸秆作为能源加以开发与利用,可以带来可观的经济效益和社会效益。秸秆转化的主要方式有直接燃烧或制成致密燃料(颗粒、块状)、气化燃料(秸秆燃气、沼气)和液化燃料(燃料乙醇和生物原油)等。
由于秸秆致密燃料的原料利用率可达90%以上,热值约为15.49~17.586 MJ/kg,不同秸秆热值稍有不同:玉米秆15. 49 MJ/kg,稻秆12. 56 MJ/kg,麦秆14. 65 MJ/kg,大豆秆15. 90 MJ/kg,薯类14. 23 MJ/kg,油料15. 49 MJ/kg,棉花秆15. 90 MJ/kg'4]。秸秆致密燃料中S和灰分等的含量仅为中质烟煤的1/10左右。秸秆致密燃料中C02的排放和吸收形成自然界碳循环,可实现C02零排放,是减排C02最有效途径,是防止全球环境恶化的一种科学选择,秸秆致密燃料燃烧技术参数为密度800~1100 kg/m3,热值15.49~17.58MJ/kg,灰分6%~20%,水分≤12%,C02 0,N0214mg/m3,S0246mg/m3,烟尘≤127mg/m3。
国家发展和改革委员会关于“‘十二五’生物质致密成型燃料发展规划”中提出,到2020年,使秸秆致密燃料成为普遍使用的一种优质燃料,每年消耗致密燃料5000万吨,代替3 000万吨煤。每年如果消费5 000万吨致密燃料,可实现减排C021~1.5亿吨,减排SO2 80—100万吨,因此,开发秸秆致密燃料具有十分重要的环境效益和经济效益。
2、秸秆燃料成型机工作原理
秸秆致密燃料是在一定温度和压力作用下,将各类分散的、没有一定形状的秸秆经过收集、干燥、粉碎等预处理后,利用致密成型设备挤压成规则的、密度较大的棒状、块状或颗粒状成型燃料。
根据成型机工作原理把致密成型设备分为:活塞冲压式成型机(pistonpress)、螺旋挤压式成型机(extruderpress)、卷扭式成型机(twistpress)和模压成型机(matrixpress)。其中模压成型机生产成本较低,产能高,物料适应性强,现在被广泛应用。模压成型机的核心部件是压辊和压模。压辊可以绕转轴转动,压模上有模孔,物料在压辊的作用下被压入模孔内,挤出,用切刀切成秸秆致密燃料。根据压模结构的不同,模压成型机可分为环模成型机和平模成型机。本文着重讨论平模成型机的工作原理及平模模孔仿真研究。
平模成型机由电动机、传动装置、传动轴、平模、压辊、喂料器、进料口、切刀、出料口等部分组成。平模成型机的平模上有多个压辊,压辊随轴做圆周运动,并与平模间有相对运动。电动机带动平模,以机械圆周运动为基础,使得压辊和平模之间有较高的摩擦温度。旋转的平模通过与物料的摩擦作用带动压辊旋转。在平模和压辊的强烈挤压下,物料逐渐被压实,均匀地分布于平模表面。物料在强烈的挤压过程中,克服孔壁摩擦阻力,从模孔中挤出,挤压过程如图1所示。平模成型机对原料的粉碎度要求较低,含水率8%一25%的物料都能被致密成型,且由于其结构简单、成本低廉、易于维修维护,适于广大农村地区小规模灵活使用。
3、平模模孔结构分析及仿真
平模是平模成型机中的关键部件,是最容易损坏的部件,需要经常更换平模,增加了成型的成本,工作中的平模如图2所示。平模上模孔众多,降低了平模抵抗变形的能力,特别是在工作过程中,孔与孔之间的薄壁承受着使秸秆成型所必须的压力。虽然在布孔上考虑了平衡的布局,但模孔仍在局部范围内会发生变形,采用Pro/Mechanica对平模工作过程中受载后位移、应力进行分析仿真,可以为优化模孔设计提供理论基础。
3.1建模
首先要进行建模分析。要使秸秆物料能挤压成型,挤压过程中模孔内壁上承受着一定的压力。所以选取平模中的一个模孔及周围的6个模孔作为研究区域,即B区域为建模的单元,压力在这个区域内会起到一定的平衡作用,如图3所示。
使用Pro/Engineer软件,设定秸秆在模孔内满足等压强原理,所建模型在孔轴向所受压强相同,因此取厚度1 mm模孔进行建模,如图4所示,将建立的模型导入Pro/Mechanica中,模型材料选择454钢,材料属性设定为:弹性模量E=2.1×1011Pa,泊松比肛=0.269,材料密度p=7 800 kg/m3,张力强度Ub=1080 MPa,屈服强度σ=930 MPa,热膨胀系数σ=11.3×1-6℃。
3.2施加载荷及结果分析
假定模孔受力均匀且平衡,在A区域与B区域交界的面施加约束,B区域内环面施加载荷。模型约束加载后得到位移云图如图5所示,由图5可以看出,受载下模孔内壁部分位移最大,进一步导人位移曲线,模孔内壁位移变形呈现小范围连续变动规律,最大位移值为5.42×10-4mm。
根据模型加载后的应力云图得出受载下模孔内壁部分应力最大,进一步导入应力曲线,根据应为曲线,模孔内壁应力呈现小范围连续变动规律,最大应力值为5.51N/mm2。
通过仿真说明,模孔内壁受载下位移及应力是一个小范围连续变动的阈值,且不同载荷下的位移、最大应力呈一元线性回归。
3.3 不同载荷下模孔的最大应力分析
在成型的过程中,模孔受到的压力并不是完全相同,根据成型压力曲线,当压力高于40 MPa,才能得到较好的秸秆成型燃料。因此对压力为45~70MPa区间进行研究,通过仿真得到最大应力拟合曲线。对拟合曲线进行一元线性回归分析:
y(t)=a+b·x(t)+u(t)式中:y(t)-最大应力,N/mrr12;x(t) -压力,MPa;n,b-回归参量;t-时间序数;u(t)-包括了除x(t)以外的影响y(t)变化的若干微小因素,u(t)是随机部分,变化是不可控的。利用MATLAB对最大应力拟合后,得到:
y(t)=0.5+3.9x(t)+n(f)
参考中华人民共和国机械行业标准JB/T 5161.1- 1999《颗粒饲料压制机型式与基本参数》,结合仿真结果与理论分析确定平模的主要参数。确定平模外径D= 500 mm,平模内径D.=140 mm,则攫取层厚度h=9mm。
4、结论
成型过程模孔容易发生变形和磨损,需要经常更换平模,这样增加了成型燃料的生产成本。为了降低生产成本,优化模孔设计,提高模孔的强度,对模孔壁的受载情况进行仿真研究。根据秸秆燃料平模成型机成型原理,对平模进行建模,采用Pro/Mechanica对工作过程中模孔的受载进行位移、应力仿真分析。
结果表明,模孔受载下内壁位移及应力值呈现小范围连续变动,不同载荷下的位移、最大应力分别随载荷呈一元线性回归。参考中华人民共和国机械行业标准JB/T5161.1-1999,确定平模的主要参数:平模外径D=500 mm,平模内径1D=140 mm,攫取层厚度h=9 mm,本文的研究旨在为平模成型机的设计和制造提供理论依据。
(转载请注明:富通新能源颗粒机www.ftxny.com)