0、引言
颚式破碎机发展至今已有140余年的历史,现已广泛运用于矿山、冶炼、建材、公路、铁路、水利等工程领域。国外从上世纪中后期便开始利用计算机仿真优化技术对颚式破碎机机构、腔型、产量及磨损等进行仿真优化分析,并研制开发出无塞点、低高度、重量轻、破碎产品粒型好、产量高的高性能新型颚式破碎机,大大提高了破碎机性能,缩短了产品开发周期,提高了产品竞争力。近年来我国虽然已有不少破碎机生产企业采用仿真技术进行新产品的开发和研制,但总体性能仍然与西方国家知名公司的产品有一定差距。
本文利用有限元分析软件ANSYS对BS105型颚式破碎机动颚支架进行数值模拟。通过对某公司生产的BS105型颚式破碎机动颚支架原结构设计及去掉面板开孔两种结构形式的强度、刚度计算分析,探讨动颚面板开孔与否对动颚整体强度和刚度的影响,同时根据计算结果进一步对原结构设计提出改进建议,为BS105型破碎机动颚结构设计提供参考。
1、动颚支架有限元计算
(1)计算所用材料参数。依据提供的材料数据及材料手册资料,本计算所用材料参数见表1。
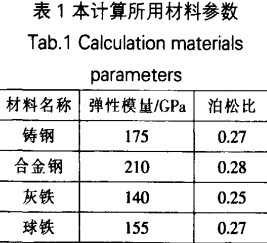
(2)有限元计算模型的建立。按照设计图纸尺寸在ANSYS环境建立几何模型,根据动鄂支架的对称性,为方便计算采用其一半结构作为计算模型。单元类型采用软件库提供的Sol-id187.模型网格如图l所示,原结构面板有孔模型(以下称模型1)单元总数100136个,面板无孔模型(以下称模型Ⅱ)单元总数101345个。
(3)载荷施加及约束条件。依据动鄂支架实际工作时受力特性及关联部件的有关性能,假定动鄂支架受力面仅为正向压力,其计算简图如图2所示。于是可按照
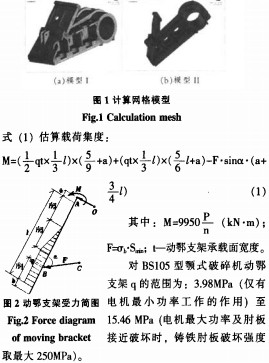
取最大250MPa)。
对称面对称边界条件,动鄂与轴承连接圆柱面及肘板与机架连接底座面固定,肘板与底座粘接。
2、计算结果
本文分别对两种模型(面板带孔模型和不带孔模型)计算两种工况下最小荷载3.98MPa-实际加载4MPa和最大荷载15.46MPa-实际加载16MPa),计算结果主要提取位移图和等效应力图如图3、4所示。
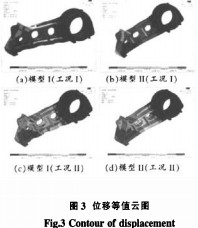
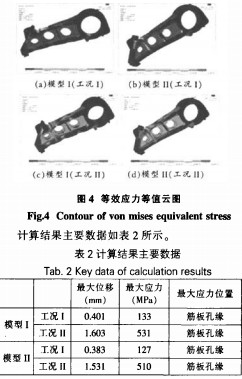
3、计算结果分析与讨论
从计算结果来看,支架变形不大,整体变形比较均匀,且基本没有扭曲变形。在较小荷载作用下支架最大等效应力约为130MPa.低于其屈服极限(230MPa),材料处于弹性范围内;在最大可能载荷(16MPa)作用下支架筋板邻近空洞边缘的大部分区域材料处于屈服状态,且局部应力已达到并超过其破坏强度(450MPa).而其它构件基本都在屈服极限以下,说明本结构在静态刚度强度上设计基本合理。两种工况等效应力云图都表现出最大应力发生在支架同一位置,筋板大部分区域,尤其是邻近孔缘局部应力普遍较高,在最大荷载作用下已超过材料的屈服极限,因此实际运行中应注意这些部位的状态,若条件允许应加强这些部位铸造缺陷的检测,避免产生裂纹源。通过开孔和不开孔模型比较可以看出,在刚度强度方面均基本相同,数值显示无孔板略有提高,约为4%。
4、建议
本文实现了BS105型
颚式破碎机动颚两种结构的数值模拟分析。根据计算结果分析,为提高破碎机整体性能及动颚使用寿命,现提出以下建议:
(1)从静态计算结果来看,在最大可能载荷作用下只有较小区域应力值偏大,因此本设计在强度、刚度方面还有较大优化设计空间,应进一步进行结构优化.尽可能减少总重。
(2)在应力局部较大区域,如筋板开孔边缘,适当加厚,避免孔洞边缘局部应力过大,以提高整体承载能力。
(3)通过对比分析得知动颚面板开孔与否对强度、刚度影响不大,建议开孔,以减小总重。
(4)加大几何突变部位(如凹槽顶与面板等部位)倒角半径,避免因应力集中产生超高应力,导致动颚过早断裂破坏。