中国石油某公司2007年进行炼油装置能量优化,原油加工能力从150万t/a上升至200万t/a,催化裂化加工能力从60万t/a提高到90万t/a,随着炼油装置加工量的提高,炼化瓦斯量也相应增加。过剩的炼化瓦斯直接经火炬排放,为了节省能源,将动力车间长期停运的一台35t/h煤粉炉改成瓦斯炉,将过剩的瓦斯引入燃烧,产生中压蒸汽,进汽轮机组发电。动力车间35t/a煤粉锅炉(型号:BG-35/39-M3)是北京锅炉厂1988年设计制造的,1990年投运,2001年重催CO余热锅炉投运后停运。
1、改造的原则及内容
1.1改造原则
本着锅炉主体结构和受热面结构改动尽可能小,尽能提高改造后的锅炉出力,改造后锅炉燃料全部为瓦斯。改造主要为炉本体、燃烧器、瓦斯净化及调压系统、引送风系统、送风系统、尾部烟道、控制系统等部分组成。
1.2炉本体改造
拆除锅炉的制粉系统、燃料油点火系统。燃气锅炉不同于燃煤锅炉,它需要使用燃烧器将燃料喷入锅炉炉膛,采用火室燃烧而无须使用炉排设施。由于燃气锅=炉燃烧后均不产生燃料灰渣,故无须排渣设施。为了防止炉膛漏风,提高锅炉效率,需封堵水力除渣槽,将锅炉底部冷灰斗用耐火浇注料修补封死。
富通新能源生产销售的生物质锅炉如下所示:
-
生物质颗粒燃料
生物质锅炉
-
适应物料:≤12mm生物质颗粒燃料
设备类型:家用生物质燃料锅炉
-
适应物料:生物质颗粒燃料
设备类型:生物质锅炉
1.3燃烧器的改造
改造选用是4台RT-1000型扩散式燃烧器,每台燃烧器的燃气量为300~1000m3/h,压力为0.01N0.05 MPa,主要由燃烧喷嘴、风门电动执行机构、点火器及火焰监控组成。RT-1000型扩散式燃烧器采用三道旋流叶片,群管多喷头的扩散燃烧方式,瓦斯气直接从多头多孔中喷入燃烧室,再与同进燃烧室的空气混合后进人炉膛燃烧。燃烧室的中部为旋流风,四周为直流风,其比例可调整,能有效地保证燃烧时火焰的形状、长度可调。为了避免炉膛死角存有少量瓦斯残气,在燃烧器上专门配有长明灯小火把。点火器装于燃烧器中的管中,抽装自如,便于检查。其风门电动执行机构,摒弃了带凸轮连杆的伺服机构配备的一体化电动执行器,可确保风门调节灵活、可靠。
燃烧器采用四角布置,在炉膛内做切向圆燃烧。没有选择燃烧器一面墙布置方式,主要考虑原锅炉煤粉燃烧器为四角布置。如果采用一面墙布置方式,为将4个燃烧器布置进去,前墙水冷壁需做炜弯处理的工作量较多,前炉墙改动工作量也较大,且需将四角封堵。采用燃烧器四角布置,只需将每个角的八根水冷壁做煨弯处理即可,改动工作量较小。这样既保持了原有炉膛的受热面,又基本保持了炉体的原貌,对锅炉炉墙破坏最小。以炉膛中心∮260的理想圆为基准,对四角瓦斯气燃烧器的主火焰中心线作切向圆布置,其优点是:
(1)4个燃烧器火焰在炉内形成切向旋焰,利于瓦斯在炉内最大限度燃尽;
(2)保证了相邻火焰及对角火焰无干扰现象;
(3)可满足大负荷。
1.4锅炉引、送风系统的改造
由于锅炉炉膛为微正压燃烧,高温过热器后为微负压燃烧,因瓦斯波动锅炉负荷随之变动很大,鼓、引风机决定使用变频控制转数,这样不仅便于对锅炉的燃烧进行控制,而且可降低能耗。
1.5烟道系统改造
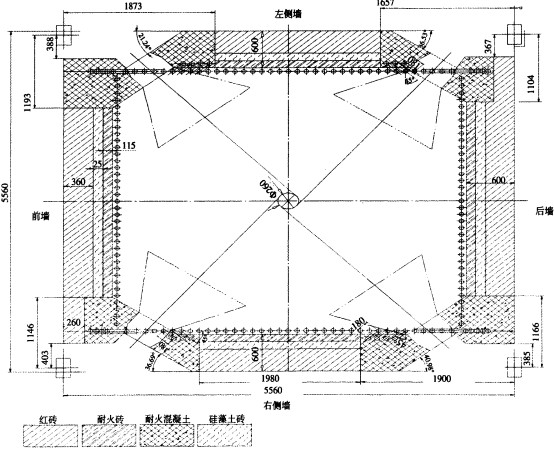
由于瓦斯量冬季和夏季区别较大,锅炉负荷会随之发生很大的变化,瓦斯气中还含有H2S,锅炉尾部可能会产生低温结露腐蚀,所以必须确保排烟温度要高于140℃。最后一组省煤器,在改造时烟道做旁路连接,将低温空气预热器摘除,以应对负荷变化造成的腐蚀。热电偶采集点布置在高温空气预热器前后,根据温度的不同采取不同的短路措施。旁路控制装置采用电动执行器。在低负荷时(20t/h)打开旁路,用烟道门的开度来控制尾部的烟气温度。烟道及风机机组系统,烟道两组可相互间切换也可同时并开。由于瓦斯气燃烧后,烟气较为洁净,为减少烟道阻力,将原水膜除尘器予以短路。
1.6燃气的脱液、过滤及减压
因为瓦斯气中含有液体及杂质,必须经过脱液和过滤才能送人减压器,否则会影响减压器的使用。脱液采用旋风分离脱液罐,脱液指标为≤10g/3。瓦斯气脱液后经过滤器,进入减压器。因瓦斯气管网压力波动较大考虑到燃烧的安全性,确保安全平稳的气源进入燃烧装置,故设置二级调压。瓦斯管网进气压力0.4~0.6 MPa,经一级调压系统调压后稳定在0.15MPa。在每个燃烧器前,增设一组二级调压器,将瓦斯气出口压力降至0.05~0.09MPa,过滤及减压装置在配备时采用一备一用方式。
1.7锅炉控制系统改造
燃气锅炉不同于燃煤锅炉,喷入炉内的燃气如果与空气的体积比达到爆炸极限就会爆炸,因此燃气锅炉均需采用自动化的燃烧与控制系统。
本次改造选用的是西门子PLC系统,实现锅炉吹扫、置换、瓦斯系统漏检、点火、燃烧整个过程全自动控制。西门子PLC系统对锅炉蒸汽压力、蒸汽温度、给水压力、瓦斯气压、烟道温度等主要参数实施自动跟踪与控制,对火焰监视、气阀开启等实施自动跟踪与控制,对锅炉全系统实施自动吹扫、自动点火、熄火保护、负荷调节全过程自动化。确保运行时先投引风机后投鼓风机、锅炉在超压时切断燃料、低水位或超高水位切断燃料、每个燃烧器熄火时切断此燃烧器的气源。确保在全部燃烧器熄火时先切断鼓风机后切断引风机,并留信号给汽轮机,在超高水位、低水位、超压、超温、每个燃烧器熄火时报警。
阀组系统、检漏装置、智能型电动调节阀、火检仪均由PLC系统控制。阀组系统主要由测试烧嘴、放散阀、阻燃瓦斯切断阀、点火瓦斯气切断阀等组成。测试烧嘴和放散阀是互为配合的两个装置,如果测试烧嘴测得瓦斯火焰正常,燃烧良好,说明该瓦斯气是在安全使用的范围内,如果测试烧嘴火焰异常.并伴有爆破声说明瓦斯气含氧量超标,如果将其送人燃烧气燃烧就有可能发生意外,这时就需要打开放散阀,放出不符合使用要求的瓦斯气,放到一定程度时,继续测试,直至合格。程序控制器检漏仪配合对2个气动切断阀间进行检漏。智能型电动调节阀可根据负荷情况与燃烧系统中的电动风门相匹配,通过改变调节阀片角度来增减瓦斯气量。
通过紫外线火焰监控设备和快速切断阀构成熄火保护系统。在火焰监控上,选用的是可用于感应火焰强弱的国产火检仪,但在安装位置的确定上遇到了其他炉型上从未遇到的难题,因为燃烧器四角布置,同时燃烧时这就要求火检仪只能检测自己的火焰,必须避开相邻及对角火焰对它的干扰,因燃烧器安装相当紧凑,火检仪既不能水平安装(否则看到炉膛及对角火焰),更不能垂直于本燃烧室(炉墙很厚且破坏炉内水冷壁管),且紫外线探测仪只对根部火焰感应最强,经过反复摸索与实践,75°角度探视燃烧室内火焰可达到理想效果。
锅炉通过安在过热器后的氧化镐探头测得锅炉内的氧含量,根据氧含量调整空燃比,自动调整进风量。
2、改造效果
经过一年多的运行观察,锅炉改造后运行平稳,完全可适应瓦斯组份、热值、压力、气量的波动,产生的中压蒸汽并入发电机组,年发电500万度以上,年可节约电费200万元以上。将瓦斯废气引入锅炉燃烧,变废为宝,不但能源得到了充分利用,大大降低直排火炬造成的环境污染,且具有很好的经济效益和社会效益。