0前言
某公司1 000 t/d预分解窑生产线,设计生产能力920t/d熟料(海拔1 223m),其回转窑规格为Φ 3.2 mx46m,预分解系统由TD分解炉和单系列五级旋风预热器组成,配套生料磨为Φ3.5mx10m中卸式烘干生料磨、冷却机为503H-606H-825H推动篦式冷却机。
本生产线于1992年10月破土动工,1995年8月点火带负荷试车。投产以来,长期徘徊在开开停停的不正常状态,熟料产量低。1995年,1996年和1997年的熟料产量分别为5800t,20900t和72267 t。至1998年底,熟料年产量也仅12.8万t,窑年平均运转率为49.1%,平均熟料产量仅为712.8 t/d。为改变这一状况,公司在狠抓基础工作、加强管理的同时,对生产线存在的问题进行了多次摸底、分析和论证。并从1999年初至2001年5月间,先后对该生产线进行了多次技术改造,取得了较好的效果。
1辅机设备改造
1999年初,公司决定首先解决设备故障多、运转率低的问题,并对影响窑正常生产、事故率较高的生料提升机、熟料输送机和窑尾密封等进行改造。
(1)熟料斗式输送机的改造。熟料斗式输送机因设备本身的质量问题(材质不过关和配件加工精度低),运行中经常发生脱轨、斗子挂坏、链轮齿块(镶嵌式链轮)掉、减速机高速轴断轴等事故;最严重时,班班有事故,导致窑开停频繁,生产十分被动。为此,我们更换了斗式输送机的链条、前后链轮,并将输送机的传动部位也作r改进,减速机断轴现象爵没有发生,使用效果十分理想。
(2)生料入窑称重仓提升机的改造。生料人窑称重仓提升机原采用链斗式提升机,因受当时制造水平和设备材质的限制,加之备品备件的质量较差,提升机经常出现故障,轻者U型环断裂,重者提升机落架,严重时班班停机处理。回转窑经常断料,严重影响窑内热工制度的稳定,对窑产质量造成很大的影响。为此利用原有壳体、斗子,仅增加钢丝胶带、牵引装置及配套部件,将其改造成胶带斗式提升机。
(3)窑尾密封板的改进。窑尾密封采用弹簧杠杆式密封。在试生产初期,因生产经验不足,在烟室弓形顶处耐火浇注料剥落后未能及时修补,固定磨擦板的法兰盘长时间暴露在高温气流下严重变形.造成密封板与磨擦板接触不好,磨损严重,故障频繁,时常发生整体垮落、掉密封板的事故。1998年因窑尾窑封故障停窑时间就高达528.5 h,成为窑运转率低的最主要因素。1999年5月在窑系统检修期间,对窑尾密封耐热钢法兰盘进行了更换并重新找正焊接,将磨擦板厚度由20 mm改为30 mm。在窑正常运行后,又采用在两磨擦件部位加废机油的方法,大大延长了密封板的使用寿命,提高了设备运转率,节约了生产成本。
1999年5月8日至5月14日期间,在圆满完成窑系统检修的同时,这三项改造工作也顺利完成,设备运转率明显提高,见表1。
2工艺设备的提产提质改造
辅机设备改造后,窑综合运转率大幅度提高,但窑产量、熟料质量并没有明显改观(见表1)。究其原因,主要是TD分解炉容积偏小、篦冷机冷却效果差和喂煤不稳,为此,对分解炉、喂煤系统和篦冷机进行了一系列改造。
2.1 分解炉改造
原TD分解炉容积偏小,炉内风速过快,造成煤粉及物料停留时间短,加之篦冷机冷却效果差,二、三次风温低,煤粉燃烧速度慢,造成煤粉燃尽率和人窑物料分解率偏低,增加了窑内热负荷,使窑速无法提高,影响熟料的产质量。同时,大量未燃尽的煤粉到C,筒内燃烧,经常出现C,出口与TD炉出口“温度倒挂”的现象,预热器结皮堵塞频繁。
1999年7月30至9月5日,我们在窑尾塔架旁新增1台NMFC流态预燃炉与原TD分解炉串联,使分解炉的有效炉容由改造前的135m³扩大到改造后278 m
3。分解炉炉容的增加,加上NMFC流态化分解炉具有燃料的初燃烧区氧浓度高、物料及煤粉停留时间长、温度场均匀和可在低过剩空气系数下运行的工艺特点,从而提高了煤粉的燃尽率和入窑物料的分解率。改造后,熟料月平均28 d抗压强度提高5 MPa以上。w(f-Ca0)合格率达80%以上,产量提高5.0 t/h左右。但因操作经验不足,窑内结圈、结球、c5堵塞等工艺事故频繁发生。经过近1年的探索和实践,到2000年8月改造效果才明显表现出来,实现3d达标和月达产,为实现年度达产打下坚实的基础,见表2。
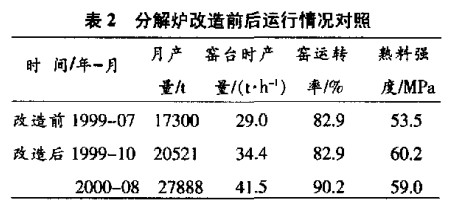
2.2喂煤系统的改造
原喂煤系统采用3台回转式压缩机送煤。回转式压缩机运行成本高、维护量大,且对维护、操作水平的要求高。由于维修、维护工作跟不.E,造成设备事故频繁。经常因滑片磨损严重,造成风量不足、送煤不稳,对熟料的产质量影响大。送煤螺旋泵叶片磨损不能及时更换,造成送煤不稳,严重时断煤,窑内无法正常煅烧,熟料质量极差,多次被迫停窑处理。
经反复论证、调研,公司先后将3台回转式压缩机更换为3台罗茨鼓风机;将输送窑头煤粉的L型螺旋泵更换为双端支承的M型富乐泵;将2台喂煤单管螺旋输送机的直流调速电机改为变频调速交流电机,传动形式由三角带传动改为减速机直联传动;将4台搅拌器的传动装置由减速机直联传动改为链传动;改造后喂煤系统的事故率降低,稳定性大大提高。
2-3篦冷机改造
随着窑产量的提高,篦冷机因锁风效果差、冷却风量不足,导致冷却效果很差且经常跑红料。由此引起篦板、破碎机锤头、下料口栅条磨损加快,篦板烧烂、漏红料的现象时有发生,导致篦冷机大粱变形、风室堵、卡断小拉链链条等设备事故增多;而篦冷机大梁变形义造成篦冷机传动负荷加大,多次发生电机脱焊事故。
为此,公司于2001年4月中旬采用第三代“TC”型充气梁技术对篦冷机进行改造。将第二代篦冷机的普通篦床改为由充气篦床、低漏料阻力篦床及普通篦床组成的组合式篦床,即高温区前5排篦板更换为固定的充气篦板配以管道供风,随后是4排高阻低漏料篦板和原来的普通篦板,仍由风室供风。将原来的4个风室改为3个风室(即将原一、二室合并,三、四室保持不变)+将原一、二室风机更换为3台高压离心风机,作为充气篦床及高阻低漏料篦板供风风机。为防止及处理高温区篦床部位堆“雪人”及大块熟料,在充气篦床前端设2台空气炮,篦冷机各风室锁风阀改为新型弧形锁风阀。改造后,二、三次风温分别从改造前的900℃和700℃提高
到1 100屯和850℃左右,窑平均产量提高I.2 t/h以上,熟料质量明显提高,熟料冷却效果大大改善,篦冷机设备故障率减少,单机运转率达96%以上,篦冷机前端堆“雪人”现象基本消除,见表3。
3改造效果
技术改造后,窑运转率、产量不断提高,熟料质量明显改善,并于2000年8月实现3d达标和月达产,2001年生产熟料305684 t,实现年度达产。2002年,再创历史佳绩,年生产熟料363621 t,为企业扭亏增盈,走出低谷打下坚实的基础。