煤矿带式输送机中常用的机械摩擦式制动器仅适用于水平或上运带式输送机,它不宜在下运带式输送机中作为一级制动方式使用。盘式制动器是一种制动力沿闸端面作用的制动器,它与块式制动器相比,具有惯量小、动作迅速及散热性能好等优点,主要应用于采区上山(下运)带式输送机,是为解决当前煤矿下运带式输送机制动时存在的滚料、飞车、打滑、冒火花等问题而研制的,也是目前下运带式输送机急需解决的关键技术难题。经过近几年的研究、试验和应用,已达到了预期的目标和要求,满足了煤矿下运带式输送机对制动器的技术条件和要求。本文对自冷盘式制动器的关键技术问题及解决方法作主要介绍。
1、盘式制动器的技术关键
(1)下运输送机的制动问题
带式输送机制动时,制动器所吸收的能量为整个输送机及物料的动能和克服输送机及物料的阻力矩所做的功。在向上运输、水平运输及向下运输的电动机工况下,阻力矩是帮助输送机制动的,故即使不设制动器,电机断电后,输送机也将自动减速与停车;在向下运输的发电机工况,阻力矩成为输送机及物料的动力矩,制动器所吸收的能量比上述几种工况时大得多,而且制动时间越长此能量越大,其机械能转化为热能,使制动器温度升高。如仅使用块闸式制动器,制动轮表面热量集中,制动时间短,热量不能及时散出,温度急剧升高,超温和闸瓦磨损互为因果,导致冒火花、飞车等事故。因而,目前使用的块闸式制动器仅能适用于水平或上运输送机,对下运输送机只能作为二级制动或备用制动用。对此,国内曾专题研究了下运输送机的制动系统(如液力、液压等制动方式),但它们都是作为初级制动,起吸收大部分制动能量、使速度降低的作用,最后仍然靠机械制动器刹停。由于这种制动系统复杂、造价高,使推广应用范围受到一定限制。本文重点以一级制动代替二级制动的要求,在达到同样制动性能的前提下,实现安全、可靠地制动,它涉及到基础材料的研究及制造工艺的水平。到目前为止,国内还没有适宜高速制动的摩擦副材料及其经验数据资料。因而,研究对制动及闸衬的材料、摩擦副对偶性能及其稳定等问题是解决下运输送机盘式制动器的技术关键之一。
此外,下运输送机上物料的下滑分力与制动时产生的惯性力方向相同,两者叠加易造成滚料现象,故要求制动器能平稳地制动,即制动减速度应限制应在~定的范围内,同时要求制动器的制动力矩随输送机负载大小的不同而自动调节;且当采区发生停电事故此情况下,制动器也必须能自动投入紧急制动,并保证制动的平稳性和安全性。
(2)制动盘的散热问题
制动器在制过程中,把机械能转变为热能,制动盘吸收其中95%以上的热量,引起制动盘急剧升温,摩擦系数降低,制动闸衬磨损增加,并可能导致制动盘疲劳破坏,如目前使用的块闸式制动器经常发生制动轮超温、冒炎花、打滑、飞车等事故。如何提高制动盘的散热性能来解决上述温升引起的一系列问题也是所研究的关键技术问题。
(3)无火花闸衬及其磨损问题
煤矿井下的制动设备应具有可靠的防爆性能,严禁制动器在制动过程中出现火花现象。由于目前普遍使用的制动器系列产品因制动轮(或制动盘)超温、闸衬易冒火花等问题得不到解决而不宜用作下运输送机的制动,以防其在制动过程中产生高温、火花而引起井下瓦斯爆炸。盘式制动是通过闸衬与制动盘的摩擦产生制动力矩的,由于闸衬的磨损会使额定制动力矩降低而影响制动的可靠性,因此,必须提高闸衬的耐磨性,在确保制动盘的温升不超过允许温度的条件下,解决制动闸衬材料的无火花问题,并保证其良好的耐磨性能。
2、主要研究内容及结果
(1)主要研究内容
1)制动及其调节系统
防爆型自冷盘式制动器,采用夹钳式双面对称闸瓦液压控制方式,制动力矩大、结构紧凑、动作灵活,并能同时与输送机滚筒或减速器配套使用。它与块闸式制动器相比,具有散热性能好、无热衰退现象、转动惯量小、动作迅速及零件通用性大等优点;与现有的液力制动系统相对比,它用一级制动代替了二级制动,大大简化了制动系统,从而使制造成本大为减小。
盘式制动装置主要有制动器(包括制动器底座、制动盘、制动闸等部件)、油压站及微机控制器等组成,如图1所示。该制动器与微机控制器有机地结合,构成了自动调节制动系统。其基本工作原理为:当制动器制动时,控制器通过转速传感器输入的转速信号,经控制内部电路放大整形后,送人微处理器,经运算比较后自动调节电液比例阀,以控制输送机的制动减速度在0.1~0. 3Hi]S2范围内,从而平稳地将输送机从制动初始转速制动至零,并能自动补偿制动闸的闸村磨损,以确保制动的安全、可靠性。
2)制动盘散热性能的研究
a.制动盘的散热及其理论
制动盘的散热是通过辐射、传导和对流方式将热量大量散发,其中主要的为对流散热。当制动盘回转时,气流纵向流过通风道表面,从而产生强迫对流散热。影响对流散热的主要因素是气流的流速,制动盘的材料及通风道的设计等。增大冷却空气在制动盘表面的速度,减小流动边界层或层流底层的厚度,是提高制动盘散系数的主要方法。
制动盘的热负荷能力是其散热性能和蓄热能力的综合指标,合理选择制动盘的材料可提高其散热和蓄热能力。如材料的导热系数高、可降低制动盘摩擦表面的最高温度;比热容和密度大,则蓄热能力高。因此,应选用热强度高、与对偶(即闸衬)的摩擦、磨损性能好、线膨胀系数小、比热容和密度大、导热性好的材料研制制动盘。
制动盘内开设通风道是提高其散热性能的有效方法。气流在通风道内的运动状态影响制动盘的散热性能。经实验证明:散热良好的通风道应该是通风道内气体相对速度高、气体附面层薄。因此,把通风道设计成加速状态有利于散热。
b.制动盘的研制与试验结果
通过理论研究和模拟试验,先后设计、制造了多种不同材料和不同结构型式的制动盘,并对其进行了试验和测试。其中硅青铜制动盘是采用了国内较少使用的硅青铜材料,它是铜一镍
硅锰系列的可热处理强化合金,具有较高的强度、硬度和良好的热稳定性及耐磨性,且与对偶材料高速摩擦不易发生火花;在结构设计上,借鉴离心风机的设计理论,在制动盘内开设曲线通风道,并使冷却空气在通风道内呈加速紊流状态,以有利于散热,考虑到制造的方便,曲线通风道采用圆弧形叶片,叶片总数为24。此外,为防止制动盘表面的瞬时热量集中,发生过热现象,在制动盘表面内圈增设了散热叶片,确保制动盘表面的最高温度≤150℃,经台架试验、检测:硅青铜、曲线型叶片制动盘在相对速度较高的条件下,散热能力强,制动盘表面与对偶连续制动时无超温、火花现象,允许最高转速达到1000r/min。而直线型钢结构制动盘与硅青铜制动盘相比,则结构简单、制造方便实用、价格低廉,并符合起重运输机械用盘式制动器制动盘的基本参数、技术要求和检验规则等。经试验室台架试验和测定,制动盘的强度、热稳定性和摩擦、磨损性能等均达到设计要求,但制动盘在高转速制动时,制动盘表面与闸村之间有火花现象。因此,直线型钢结构制动盘在煤矿井下使用时通常以制动盘转速小于700 r/min为宜,而与通用制动闸衬对偶,其相对磨擦中心的线速度一般不宜超过7.5m/s,宜安装在减速器的低速轴上使用。
3)无火花闸衬的研制
制动闸衬的火花问题与对偶材料的摩擦性能及摩擦线速度密切相关。在试验国内刹车片制动牲能的同时,协同材料保护研究所共同研制了十多种不同材料成份的闸衬试验样品,并先后在台架上作了样机试验,以检验闸衬的技术参数是否达到要求。通过试验比较,研制成功了以酚醛树脂为基体,附加多种添加剂(如润滑剂、阻燃剂等)配制的无火花闸衬。根据研究和试验证实:因限于国内目前的材料及工艺水平,当闸衬中心相对制动盘表面的摩擦线速度≥30m/s时,闸衬火花问题仍难于解决。因此,本制动器产品系列在防爆场合下使用,仍适宜输送机的低速级制动。
综上所述,采用自冷盘式制动器解决下运带式输送机的制动问题是切实可行的。
(2)自冷盘式制动器主要特点
1)散热性能好,防爆易解决
制动盘经合理的通风道设计,可将制动功转化的热量迅速带走,防止制动盘表面温升过高。同时,无火花闸衬的研制成功,有效地解决了机械磨擦制动器的防爆问题。
2)制动平稳
制动控制器通过转速传感器和电液比例阀对盘式制动器进行自动调节,可保证制动力矩随负载大小而相应变化,使制动减速度控制在规定的范围内。
3)采区事故停电时,由液压站蓄能器自动投入制动,同样保证制动的平稳性。
4)整个系统结构紧凑,操作方便,易于功能扩展和自动化控制。
3、工业性应用及推广前景
通过研究和试验,KPZ防爆型自冷盘式制动器适用于下运带式输送机在倾角-3°~28°运行,该系列设计产品经国家采煤机械质检中心检验,各项技术指标均达到预期的设计要求。目前该盘式制动装置已投入批量生产,其中常用型号为KP2650,KP2850、KPZ1000、KP21200等,额定制动力矩为2500~16000N-m,并在许多矿井投入工业性使用和运行(典型实例如表1所示)。
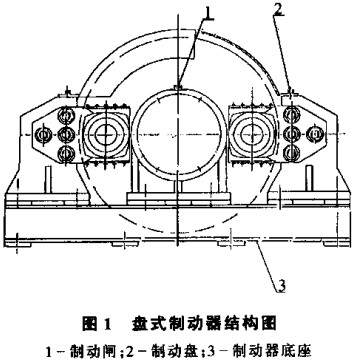
目前某公司在煤矿采掘、辅助运输、输配电、通风、排水、洗选加工以及装车,化验等各个环节已经广泛地应用了自动化控制技术,并取得了良好的经济效益和社会效益。自2000年以来,先后在大柳塔矿井、活鸡兔矿井、榆家梁矿井及补连塔矿井等进行了自动化改造。根据现代集成制造以及管控一体化的思想,以三层网络为基础,结合自动化、信息、计算机、网络、通讯的新理论和技术,采用世界先进的自动化产品、网络产品和工业控制软件、数据库软件,将公司煤矿生产、管理的各个环节,统一在一个网络平台上。在生产规模、系统结构、网络通讯、自动化覆盖范围等方面达到了世界先进水平。用高新技术达到了减员增效、提高矿井生产能力,增加经济效益的目的。
以大柳塔为例,2000年底实现矿井综合自动化以后,全矿人员由原来的365人进一步减少到300人,全员工效提高了22%,达到120t/人.工。大柳塔矿与活鸡兔矿合并,经自动化综合改造后,年生产能力今年将达到1900万t,定员却只有480人,刨世界记录。
(2)企业资产管理系统的探索与实施
在组织对国内外相关企业进行调研、分析和论证基础上实施了企业资产管理(EAM)系统。该系统具有设备有偿使用管理、设备维修管理、设备跟踪管理、动态调整配件安全库存、利库功能、自动比价、采购计划自动生成及合同跟踪等主要功能。将设备的购置、跟踪、维修、处置的全过程以及物资的计划、采购、仓储等主要业务用信息技术整合到一起,形成了神东煤炭公司机电管理工作的统一信息技术平台,满足了公司机电管理当前的业务的需求,完备了机电管理业务功能,实现了企业财富的便捷应用和共享,实现了神东设备资产管理与国际规范的接轨,使神东机电管理整体水平实现跨越式提升。
目前,已经有16个单位(9矿、5中心、1厂)的机电工作全部在EAM系统中执行,共涉及44个业务流程700多个流程结点,共管理设备资产10536台价值46亿元、配件物资20000多种价值7亿元,底层数据270多万条,数据信息1438万个。通过以工单制为核心的设备全过程管理,实现机电管理规范化、流程化;提高设备维修水平,缩短大修周期,降低维修成本;减少设备停机时间,延长设备运行寿命,提高资产使用效率。这些均为神东矿区生产的可持续发展提供可靠的机电保障,对煤炭行业、对国家的煤炭行业技术装备的进步起到不可估量的作用。
总之,在世界先进采煤技术装备的使用和科学化管理方面走过的路子,为我国煤炭企业不断应用机电一体化装备做出了新的有益的尝试。它的成功证明了建设现代化矿井,科技是根本,装备是基础,素质是前提,管理是关键。将继续探讨新路子,为我国煤炭企业的发展谱写更新的篇章。